The Winning Formula To Beat Aftermarket Delays

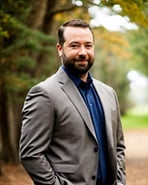
Q AW: What parts does Republic Airways use AK Structures for?
A JB: We use them for nacelle inlet repairs and exchanges. After COVID, due to parking our aircraft, we noticed a lot of erosion on the lipskins of the inlets. By 2023, we were back to almost full flight capacity, but at the same time, we were seeing big jumps in lead times and prices for OEM replacements. Therefore, taking advantage of AK's PMA part and DER repair solutions was a natural step.
Q AW: What is Republic's main priority when selecting a maintenance provider?
A JB: The top one is cost-effectiveness. We want them to be price-competitive and transparent with their pricing details. We also value reducing pricing through alternatives like PMA parts and DER repairs – anything that helps us be cost-efficient. Quality is also essential: do we have any returns? Is what they repair top-notch, or must we send it out again? We value our partnership with AK Structures as they continue to hold true to their values, integrity, and quality of work.
A DH: That's true: Our repair station has an FAA Diamond Award for Excellence for training. Besides the DER process, to save money for our repair customers, we focus on ensuring our labor rates are fair. Plus, we go through a rigorous program for initial and recurrent training to ensure we're not wasting any labor hours the customer is paying us for.
Q AW: How has Republic's adoption of PMA and DER developed in recent years?
A JB: We've experienced significant increases in OEM parts prices and turnaround times, so we've used many more PMA parts. Our purchasing team is very good at finding PMAs, and then we pass that up to engineering, who have become more lenient about what we can do PMA-wise or with owner-operated parts. Most of the PMA parts we approve last longer, if not the same amount of time as regular OEM parts.
Q AW: And how does AK Structures support Republic with these alternatives?
A DH: We started working with Republic in 2020, during the pandemic. Then it was about the two companies growing together and us understanding what Republic needed for its fleet: what parts were available to support these products, what weren't, what repairs could we do versus what we needed to buy from the OEM. Then we took all that information, and we were able to reverse engineer those parts with which they were having supply-chain issues. We're a complete manufacturing facility and a Part 145 repair station, so we have the equipment to manufacture all the heat-treating and forming equipment to make composite and other parts in-house.
Q AW: How important is repair time for Republic Airways?
A JB: Turnaround time is [TAT] hugely important. We count on our suppliers to deliver the TATs they promise. Many turn times have increased since the pandemic, but AK Structures has reversed that tide, dropping their repair TATs for our inlets from 46 days when we started working with them a few years ago to 20 days now. We have a DER with them right now for straps and doublers, and it's been working great: it saves us time, money, and hair-pulling because we're not dealing with the OEM.
A DH: To give you an idea of what Jenny means, I have an order with the OEM for a complete set of lipskin doublers for European customers who didn't want a DER repair – they wanted all OEM parts. And I've had that on order for four months now, and the OEM doesn't know when they're going to fulfill it. They haven't given me a date, so getting OEM parts is almost an infinite timeline. AK Structures has 50 of those doublers in our inventory, so if an inlet hits our shop tomorrow, we could start taking it apart and installing those parts right away. This means we can support as many of these inlet repairs as Republic or any other operator – can give us.
Q AW: What benefits does Republic get from parts exchange programs?
A JB: We value partnership and innovation from our maintenance providers, which means working with us on our Aero Exchange program. So, instead of fixing the unit we send in if they have a spare unit, they can paint it the color of the airline we need it for and ship it out. AK Structures is quick with its inlet exchanges, so we don't like relying too much on a single maintenance provider. For inlets, we lean on them more because they are faster. Recently, they sent us an American Airlines-painted inlet in three days, which is a huge saving for us compared to a potential repair turn time of 65 days.
Q AW: And what goes into supporting such a large fleet as Republic's, which operates hundreds of aircraft across multiple airline brands?
A DH: We try to keep one of each livery that Republic flies in inventory and ready for exchange. Republic flies for Delta, American, and United so we aim to keep one of each so that when Jenny needs one quickly, we can provide that service for her. To get those units available, we'll either invest in inventory ourselves to support Republic and other regional airlines or partner with somebody else with more inventory.