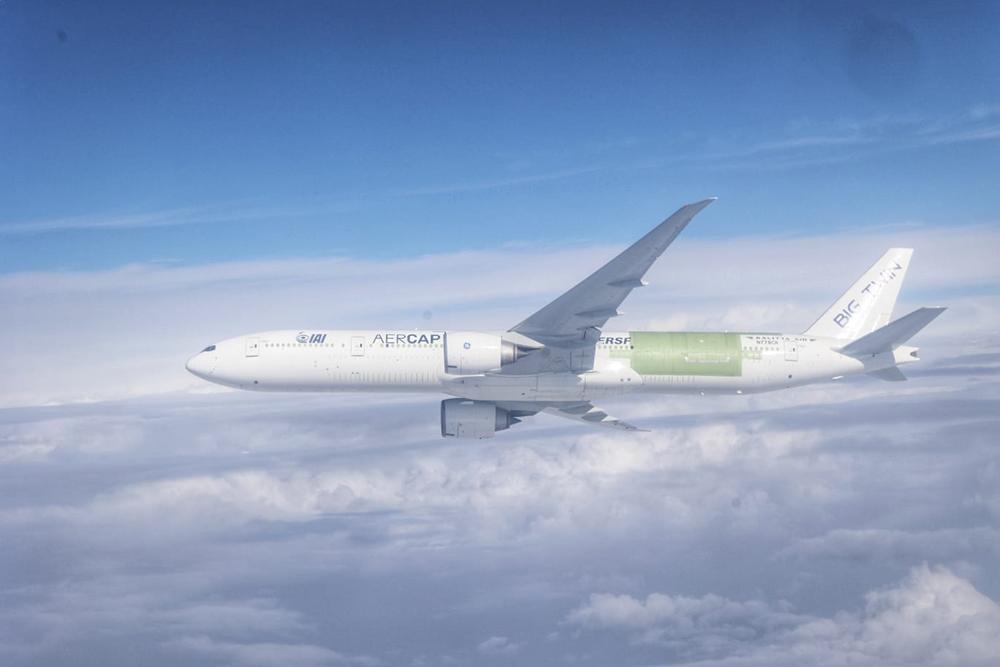
Airbus predicts shippers will need 560 widebody freighters of more than 80-ton capacity from 202-41. Boeing expects demand for 515 widebody freighters over the same period. Much of this demand will be satisfied by new-make cargo aircraft, but one veteran and two new ventures are moving steadily toward converting Boeing 777s to meet the requirements for heavy cargo aircraft.
The partnership of Israel Aerospace Industries (IAI) and AerCap flew the first test flight of its 777-300ERSF in late March. IAI originally hoped to have the ‘Big Twin’ in service in 2022, but COVID-19 slowed down the project, according to Yaacov Berkovitz, vice president and general manager of conversions and upgrades at IAI.
IAI first had to adjust its work processes to COVID-19 restrictions and it was then hit by supply chain problems. However, it says the first test went very well, and now it is continuing with ground tests and will perform further flight tests as it works with regulators.
IAI has been working with both the Civil Aviation Authority of Israel (CAAI) and the FAA on certification of the 777-300ERSF. “Under the U.S.-Israel Bilateral Aviation Safety Agreement, the FAA and CAAI reciprocally approve design changes on products for which the U.S. or Israel is the state of design,” explains an FAA spokesperson.
“We are aiming to have our STC by the end of the third quarter of 2023, and are on track for that,” Berkovitz says.
The 777-300ERSF will have a maximum payload of 220,000 lb. The conversion will have a rear main cargo door, as do new-make Boeing 777 freighters. A rear door “is efficient to load and easy to work around,” Berkovitz says.
Berkovitz says the 777-300ERSF will be far more fuel- and maintenance-efficient than the 747 and MD-11 freighters it replaces and, even including feedstock costs, it will cost less than new 777 freighters. Yet even after conversion, the Big Twin will be able to fly “at least 20 years.”
Comparing IAI’s product with other 777 conversions, Berkovitz cites the company’s four decades of experience in cargo conversions. And, as a government-owned company almost as old as Israel itself, he says IAI can guarantee future customer service. “We will be around forever,” he says.
These kinds of advantages have already elicited more than 60 firm orders from companies such as AerCap, Emirates Cargo, Challenge Group, EVA Air and CargoJet.
Customers do not want to wait in lengthy conversion queues, so in addition to its own facilities at Ben Gurion Airport, IAI has arranged production partnerships with Etihad Engineering in Abu Dhabi and Sharp Technics K at Incheon International Airport. “We aim to add more lines as fast as we can,” Berkovitz says. IAI’s goal is for each line to do 2-3 conversions per year.
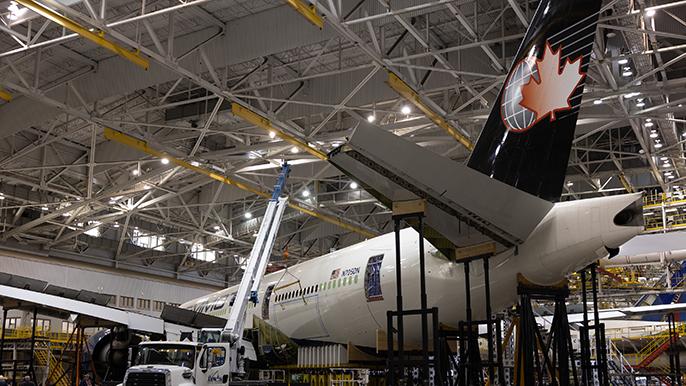
Mammoth Freighters has obtained FAA’s agreement to its project-specific certification plan and it is working with the agency’s West Certification Branch on certification of its converted 777-200LRMF and 777-300ERMF, according to Brian McCarthy, vice president of marketing and sales. Transport Canada and the European Union Aviation Safety Agency will also be involved with Mammoth’s customers, so the company plans on continuous dialogue with these agencies.
This venture began in 2020 when Fortress Investment Group, Mammoth’s financial backer, acquired 10 Delta Air Lines 777-200s that were grounded during the pandemic and were not expected to return to service.
“Engineering is progressing well on both the -200LR and -300ER,” McCarthy says. “Drawing releases continue with satisfactory momentum,” he adds, noting that Mammoth is now moving focus toward parts installation.
Like IAI, Mammoth has faced supply chain challenges, but it has sourced the majority of materials in the U.S. to better control delays.
Mammoth is now building freighter conversion’s door and door surround. It will install the first large structure in early June. The company has more than 100 of its own engineers, plus another 60 at component suppliers working on the project.
Like IAI, Mammoth is installing a rear cargo door. This requires complex engineering, but McCarthy insists it is the right approach. Front door loading can risk tipping the aircraft, he argues. Furthermore, for efficient operations, he says major cargo carriers want common configurations, and new-make 777 freighters from Boeing will have rear doors.
Mammoth is currently working on the first two -200s and one -300. The -200 has maximum payload of 233,000 lb. and the -300 has maximum payload of 220,000 lb.
McCarthy says Mammoth is aiming for it first test flight of a -200 in January 2024 and certification by the end of 2024’s second quarter. The -300 should be certified by the end of 2024.
Mammoth already has 35 firm orders, six for -300s and 29 for -200s. Customers include Canada’s Cargojet, Avia Solutions Group and DHL Express.
Mammoth plans to perform modification work on at least five lines at American Airlines’ old MRO facility in Dallas-Fort Worth, which features six widebody hangar bays. In addition, it will use two lines at STS Aviation Group’s Manchester, UK facility.
McCarthy expects a bow wave of 777 conversions in the next several years as 747 and MD-11 freighters are retired. Then, 6-7 years from now, he expects Mammoth will shift to emphasizing heavy checks on 777 freighters, while still doing some conversions.
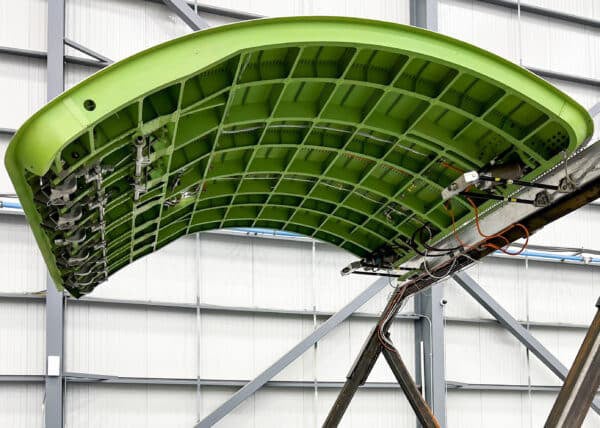
Kansas Modification Center and NIAR WERX at Wichita State University received FAA acceptance of their project-specific certification plan for 777-300 conversions on May 18. KMC President Jim Gibbs says it took several revisions and back-and-forth discussions to get FAA agreement to the 500-page document. “The first FAA response had 400 comments, we revised it, and then FAA responded with 77 comments,” he says.
Gibbs says having FAA agreement on the certification path will make a “huge difference” going forward, making the certification effort more of a working partnership executing to an agreed plan.
KMC’s next steps are to go into production with its first converted 777. Its approach is to open up the aircraft for the shortest period of time for each modification change. Gibbs says this lowers risks and requires less inventory and floor space than taking the skin off the entire aircraft.
KMC now has more than 200 staff working on the conversion, including 150 engineers, 75 support staff and about 15 mechanics.
Next will come qualification testing of subsystem components. KMC is building sub-assemblies now, and will then jack and shore the aircraft and install the new cargo structures. “Then, we put it back on wheels and go fly it,” Gibbs explains. He expects the first test flight late in the second quarter or early third quarter of 2024, then an FAA STC late in the third quarter or early fourth quarter of the same year.
Gibbs says KMC’s approach to supply chain issues has been to engineer solutions that do not require scarce materials, rather than pay exorbitant prices to hasten deliveries.
KMC’s 777-300ERCF can carry 205,000 lb. Unlike the IAI and Mammoth projects, KMC’s 777-300ERCF will have a forward cargo door. Gibbs says extensive analysis indicates this forward door does not increase tipping risk, and a tipping alert system will further mitigate any risk. He also argues that major freight companies have successfully operated freighters with forward cargo doors, including MD-11s, 767s, Airbus A300s and other types.
Gibbs says KMC’s conversion will be the only 777 freighter approved by the U.S. Air Force Air Mobility Command for its civil reserve air fleet. This approval can earn airlines monthly rental payments.
Market willing, KMC will start with four 777 conversions per year, eventually ramping up to 12. It is also using the 777 program to build infrastructure for what it hopes to be a much broader business, beyond 777s and freighters. “We want to develop STCs and convert aircraft to different missions,” Gibbs explains.