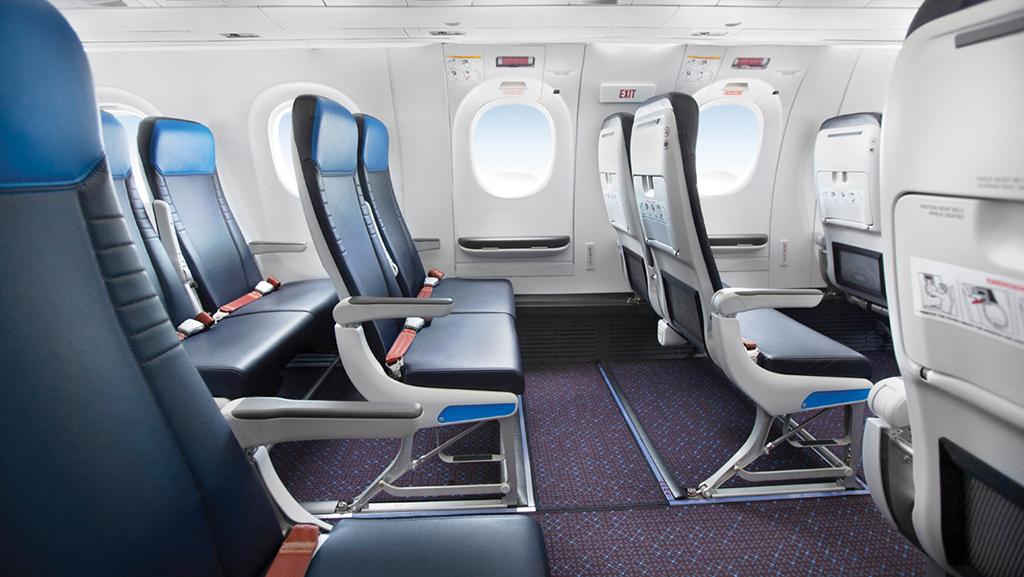
When airlines plan cabin updates, carpeting is typically among the replacement items, given its tendency to wear out. But today, concerns about carpeting go beyond choice of colors and patterns.
Sustainability, weight and durability now figure prominently in the purchase decision. Those factors have generated significant new trends, among them the transition from wool to nylon pile over the past decade, and a high level of recycled content.
“Wool used to be the main commercial aviation carpeting material,” says Topher Harrison, sales account manager at Airworthy, a Hudson, Wisconsin-based fabricator of custom-finished carpets. “Now, probably 80% of all airlines use nylon carpets,” he says.
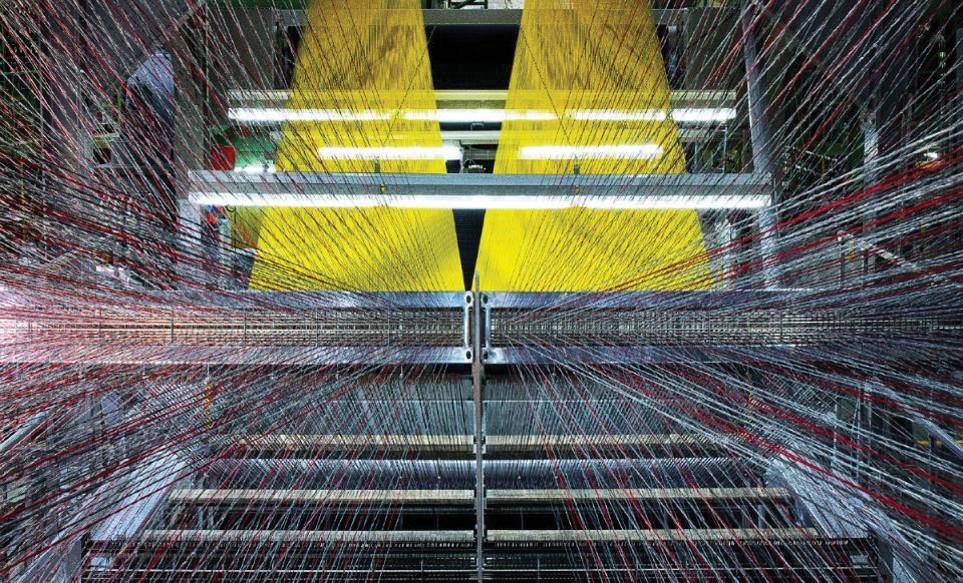
Nylon has advantages such as a life cycle about twice that of 100% wool carpeting. “As a natural fiber, however, wool is more fire-resistant, although nylon still meets U.S. FAR 25.853 fire regulations,” he says. “Wool will not completely leave the commercial airline market, but its popularity will be more likely in the private flying world.”
One case in point: JetBlue Airways has been moving away from the wool blend carpeting included by Airbus with delivery of the carrier’s initial A320 fleet in 1999-2000, according to Jan Karl Lorenzen, the airline’s senior aircraft interiors engineer for technical operations. “Wool would contract with steam cleaning and getting wet. Being a natural fiber, it tends to absorb dirt better, making it more difficult to get out,” he says. JetBlue now uses nylon carpets.
Due to its fire-inhibiting qualities, wool will continue to be a basic component of aviation carpeting, says Fabian Hellweg, global key account manager-aviation for carpet manufacturer Tarkett in the Netherlands. However, synthetic material such as nylon is added for increased durability.
Hellweg concedes that there is a growing preference for nylon carpets, especially in the North and South American airline markets, due to its durability. Change-outs of cabin--aisle wool carpeting generally occur every 6-12 months, while nylon is good for as much as 18 months. The underseat carpeting for both wool and nylon is usually replaced at every C check, or about every 18-24 months.
“While nylon is more durable, more resistant to dirt and stains and easier to clean, it doesn’t have the look or feel of wool,” Hellweg says. “Also, wool is more fire-resistant, which is why when you get into nylon carpeting, more fire retardant has to be used in the carpet’s backing.”
No matter the material of choice, carpet manufacturers are giving sustainability a high priority, given the considerable degree of recycled material that goes into their products today. For example, Tarkett created new carpets for KLM using repurposed fibers from the airline’s discarded flight attendant uniforms. The uniforms went to a third-party contractor for shredding. The fibers were then turned into yarn at a Tarkett-owned factory. “To my knowledge, no other aviation carpeting OEM is doing this,” Hellweg says.

Aad Visser, cabin engineer at KLM E&M, confirms that using recycled flight attendant uniforms for carpeting was introduced in 2013 as part of a cabin midlife upgrade program for the Boeing 747-400. That was extended in 2015 to the Boeing 777 fleet and then to the Airbus A330-200s. “Now we are installing the carpet made from the flight attendant uniforms on our 16 737NGs as part of their cabin midlife upgrade,” Visser explains. “Our 787 fleet was delivered with this carpeting.”
The uniforms worn by KLM cabin staff, Visser adds, are made of wool, which continues to be the airline’s choice for carpets. “With nylon, not all of our criteria for designs and colors can be met,” he says.
Airworthy’s suppliers have “made huge leaps forward” in using recycled material over the past five years, Harrison says. “A supplier, in a recent conversation, mentioned that over 60% of their carpets are made from recycled material and that almost 95% of the pile of the carpet is recycled into new carpet,” he remarks.
The source of that material, says Harrison, is mainly residential/commercial carpets, fishing nets and, for the backing, laminated glass from car windshields. Interestingly, worn aviation carpeting is difficult to recycle, given its typical pile height of just 0.25 in., which leaves less usable material when stripped from the backing, he says. In contrast, residential carpeting pile is about 1 in. high.
Bernd Zumbe, aircraft carpet sales director for ANKER, reports that the Duren, Germany-based manufacturer was the first aviation carpet manufacturer to bring to market a nylon carpet made from recycled content. Introduced in 2011 and made with Econyl fiber, the carpeting was initially used by Virgin America (since merged into Alaska Airlines) in 2014. “That was followed by American Airlines, with the carpet currently installed on 70% of its fleet,” he says.
ANKER, says Zumbe, is the world’s leading aircraft carpet manufacturer for using recycled content—with a global customer base of more than 40 airlines. At the end of 2020, the company confirmed it would be able to upcycle approximately 80% of its nylon carpets into newly manufactured products.
“Together with Eurowings, we started a pilot project on this development,” he notes. “Specifically, the Econyl yarn, used for the pile material, can be 100% recycled, with the polyester construction yarns also 100% recyclable.” The latex backing can be what Zumbe termed “partially recycled.” Meanwhile, last year ANKER announced a new latex backing with high content from recycled windshields and building glass.
Airlines continue to seek more ways to reduce waste. In 2019, for example, KLM started using a hook-and-fly method to attach or secure carpeting in place, as opposed to using double-sided tape, which is disposed of after a single use. With the hook and fly method, as KLM’s Visser explains, the carpet is affixed to a thin Velcro strip installed on the cabin floor. The Velcro itself can remain in place for several years before needing replacement. This enables the carrier to replace small areas of damaged or worn carpeting as needed.
“Under the seats, the carpeting is installed in the form of tiles or segments with a maximum length of 80 cm [31 in.],” Visser notes. “Each tile can be checked at every opportunity and replaced if necessary. Without the hook-and-fly system, 100% of the carpet would have to be replaced—about every 24 months.”
According to JetBlue’s Lorenzen, the carrier is using several approaches to stretch the time between carpet installations and removals. One is similar to KLM’s.
“Our carpet segments are about 100 in. long. Although it makes for a lot of pieces, they are easier to replace by one person, just one piece at a time,” Lorenzen says.
He adds that the airline is also looking to improve color fastness, especially now that some carriers are using ultraviolet light as an anti-microbial measure. Ultraviolet light, he points out, tends to fade colors.
In terms of other features, a new surging (carpet-edging) design, which eliminates the traditional loop-through construction method, is making the surging more resistant to damage from passenger impact and rolling food/beverage carts. The carpeting was included by Airbus on the A220-300s, which are just entering JetBlue’s fleet.
“When the edging begins to fray, you really can’t repair it,” so it must be replaced, Lorenzen says.