This article is published in Aviation Week & Space Technology and is free to read until Apr 18, 2025. If you want to read more articles from this publication, please click the link to subscribe.
Cabin Composites Pose Challenges, Opportunities For Aftermarket
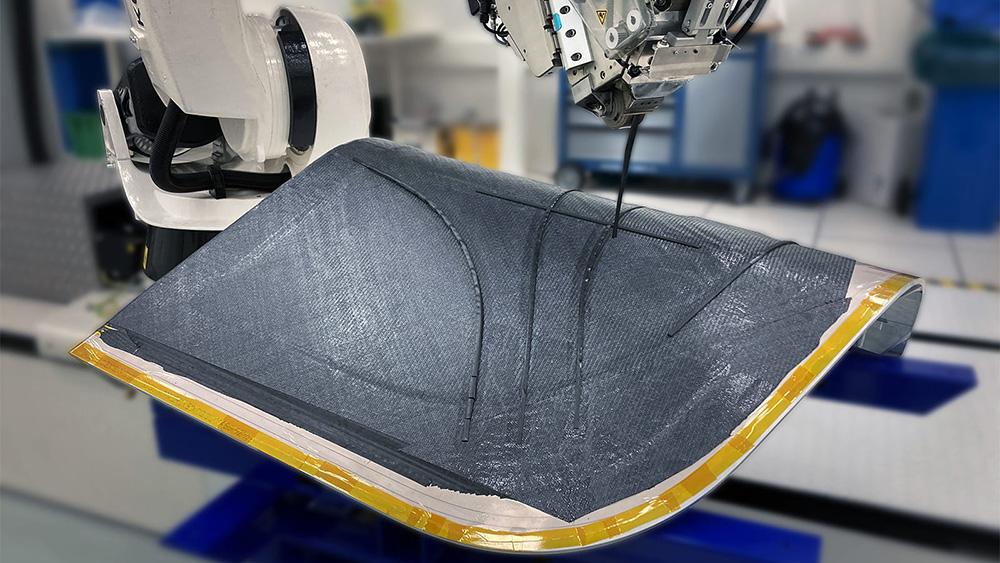
Recycling composite materials for reuse in aviation is tricky since the process reduces structural integrity.
The growth of composite materials within the aircraft cabin—usually carbon-fiber reinforced polymers—has seen a stratospheric rise over recent years, and as new cabins are developed for the forthcoming generation of aircraft, even more will be onboard. While these materials lay the technical foundations for the next generation of more sustainable aviation, they bring challenges and opportunities for MRO.
“Composites are everywhere,” explains Daniel Clucas, a member of the leadership board of the Green Cabin Alliance, an interiors sector group pushing for greater sustainability. “They are especially used in the aircraft internal linings: sidewall panels, bins and flooring under the carpet. They're extensively used in cabin products, too. The majority of flat galley, bulkhead and partitions are composites, and they're increasingly being used in seat shells.”
The core benefits over previous generations of materials—primarily standard thermoplastics and lightweight metal alloys—come from weight, durability and the right balance between rigidity and flexibility. In addition, in the cabin environment they can absorb noise.
They are, however, complex to manufacture, especially in the increasingly intricate 3D curves required for modern premium cabin seats. As the design, production and certification of these elements developed, some seat makers even eschewed composites for a time.
“While there has been a trend in business class seating away from composites due to complex manufacturing and quality requirements, their compelling weight-saving benefits remain an advantage, particularly as the latest generation of airframes is predominantly composite-based,” explains Alan McInnes, vice president for business development at seat maker Unum.
“The complex tessellation and curved designs of these suites have made composites an ideal material for their construction,” while further back in the aircraft, “in economy class, composites have been increasingly used in structural seat backs, contributing to significantly lighter seating over the years,” says McInnes.
Composites can also be more sustainable in the production process, especially when using Industry 4.0 technologies such as additive manufacturing and structural biomimicry.
“Sustainably speaking, composite materials can often be additively built, not only reducing the amount of waste during the manufacturing process but also improving product repeatability and improving yield,” explains David McConnell, associate director of research for advanced materials and process technology at Collins Aerospace. “This helps ensure we are able to optimize product performance, lifespan and reliability, making maintenance and repair situations more predictable. Composites also typically offer a high strength-to-weight ratio which has clear throughlines to reducing the overall carry weight onboard aircraft, resulting in less fuel burn and CO2 emissions.”
There are, however, challenges in the onboard environment. Composites react differently to damage than traditional aviation materials such as metal or thermoplastic. For instance, a crack might appear in damaged composite material where only a dent would be seen in other materials—so composites often require replacement or a larger repair compared with other materials. Specialized non-destructive testing techniques and new inspection equipment are also needed, and these require new training and certification for MRO technicians.
“Repairing composites is a vastly different process than repairing metals, which typically consists of welding, drilling and riveting techniques,” says McConnell. “Composite materials typically require specialized processes that involve patching with adhesives, resins and other fibrous materials before allowing adequate time for the repair to fully dry and cure.”
As a result—and also alongside a wider push toward modular design in aircraft cabins—on-wing MRO of composite elements is more likely to be a replacement or swap-out rather than a repair.
New minor repair techniques, however, are mitigating the complexity of repairs for normal nicks and scratches, explains McInnes. “Primary repairs typically involve paint touch-ups for minor damage, such as baggage and catering trolley dings on painted composite surfaces,” he says. “To address this, we have developed a design and repair scheme that enables these repairs to be carried out swiftly while the aircraft remains in service. As a result, MRO teams need the appropriate tools and skills to perform these predefined repairs efficiently.”
A key criticism of composites within the cabin is the complexity of processing them at end-of-life, since by their nature as a composite of multiple materials, the plastics and the reinforcement cannot easily be separated into those base materials.
“Recycling efforts often involve grinding down the mixture of materials into a powder that can then be combined with resin and molded into new parts, but lacking the structural integrity of their first iteration,” explains Clucas.
Closer collaboration between airlines, suppliers, manufacturers, MROs and recyclers will be critical to improving composites’ recyclability. This collaboration must address responsibility, ownership and finding secondary and tertiary uses within the industry.
Clucas characterizes the present situation as “an area of the industry that needs a lot of work,” despite stakeholders’ desire to collaborate.
“At the Green Cabin Alliance we are starting a working group with the Aircraft Fleet Recycling Association to look into exactly this problem, and [to] try to keep the materials in the aviation supply chain,” he says. “We use a lot of specialist materials, especially as they often have flame resistance added, which narrows their wider use, but makes them very valuable if they stay in the aviation industry supply chains.”
Until these issues are resolved, it is unlikely that cabin materials will see full circularity, but there remains a strong environmental and economic argument for their use on a weight-saving basis alone. Every gram that can be shaved off a seat that will be flown every day for a decade is multiplied exponentially by fuel cost and environmental emissions.