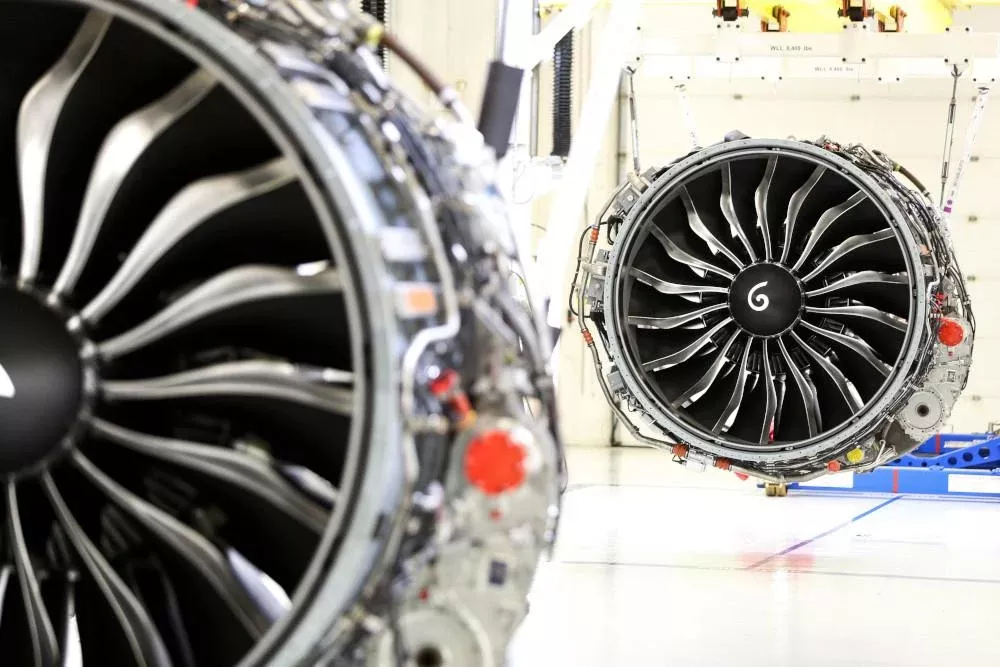
HONG KONG—A lack of developed repairs for new-generation engine types is leading to MRO repair providers reevaluating their parts sourcing strategies in a current environment of newer engines going into the shop earlier than anticipated.
With some shop visit lead times reportedly surpassing 200 days on some new-generation engine types because of supply chain constraints and specific issues like material shortages, MROs have had to adapt to the challenging environment.
Among these is StandardAero, which became part of CFM International’s Leap engine network in early 2023 for the Leap 1A and 1B variants. “New repairs for some new engine types are still in the development phase and there will be some years yet before we see more repairs coming up,” says Janice Ho, airline sales director, Asia-Pacific at StandardAero. “With any new parts we will work with the OEM to order the parts in advance once we know that the engine is coming into the shop.”
Ho says StandardAero briefs operators ahead of time before an engine comes into a shop. “We try to pre-provision the parts and order in advance to reduce the turn time or waiting time for new parts,” she says. “We also work with our component shops to repair the parts with shorter term times so that will help operators decrease the [turnaround time] required for engines in the shop.”
Lufthansa Technik (LHT) is also a partner on the Leap 1A and 1B engine platform. Regine Kuckuck, LHT's head of sales engine services, Asia Pacific, says that, like StandardAero, it also pre-stocks parts to have them available when an engine enters the facility. “But this can sometimes be a challenge since we of course have to manage the work scope, and once you've opened an engine, you never know how deep you have to go,” she says. “We try to be upfront to be sure about the work scope with perhaps a borescope inspection to cover any risk of work scope extensions and repairs.”
Kuckuck says LHT works with its OEM partners to identify which repair needs are in the operation. On the Leap program, Kuckuck says being a CFM branded license holder gives LHT the opportunity to develop its own repairs and give them to the OEM to be included in the engine repair manual. “With the experience of CFM programs, we can really contribute to developing repairs and work scoping in the right direction in order to keep turn times as low as possible.”
Paul Ashcroft, head of Asia Pacific at end-of-life services specialist AerFin, says OEMs typically push targeted work scopes to limit exposure to other parts of the engine during a shop visit. “The reality is a product is put into service and some of those repairs are in the background, ready for when you think the engine is going to come into the shop,” he says. “They’ve tried to advance some of those repairs forward now because the engines are coming into the shop far ahead of where they anticipated.”
While consensus suggests the industry hasn’t been ready for the level of engines coming into the shop earlier than expected, there is optimism for the future prospects of the Leap engine’s shop visit time frames. “The good thing is for the Leap engine we already see a second and third generation of new parts, and they have much better durability,” says Kuckuck. “Hopefully we are getting to the stage of [needing] repairs only every five years.”
Given the young age of both the Leap and geared turbofan engines and issues around asset availability, both programs are typically only leased for long-term periods. Short-term leases for new-generation engine types are expected to be some time off.
“Ultimately this will happen but it will take a lot of time, as asset availability is a natural challenge and lessors who have that asset will naturally want to tie in the longest possible term,” says Aerfin’s Ashcroft, who expects the time frame to be at least five years before short-term leases are options for newer engine types.
As a potential solution, LHT’s Kuckuck believes a scenario could occur where lessors send engines on long-term leases to MRO providers, who then in turn can lease engines out on a short-term basis to operators while covering shop visits.