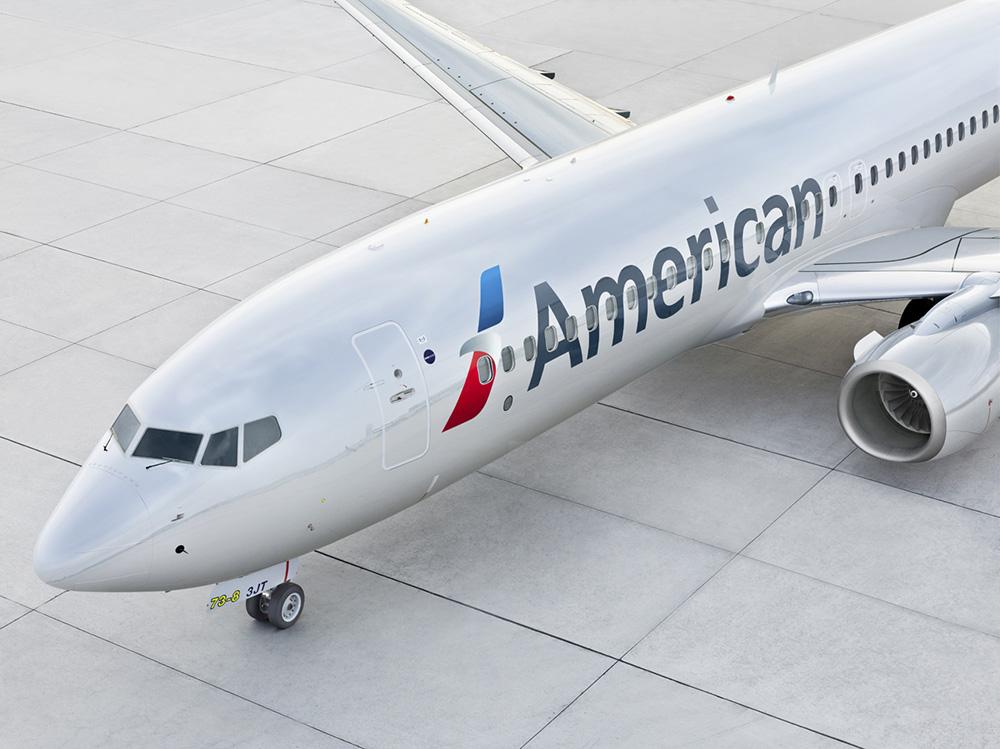
Carbon brake upgrades are gathering momentum again as airlines continue to rebuild flying schedules. Safran Landing Systems reports that customer American Airlines is in the process of reducing flight weight through enhanced braking solutions.
In December, American enlisted Safran’s services to provide lighter, more efficient carbon brakes for 300 of its Boeing 737NG fleet. Nicolas Potier, Safran’s executive vice president for wheels and brakes, reports that a task force has now been assembled for entry into service readiness, and to monitor the progress of the upgrade plan, which has been defined in close collaboration with the airline.
“American Airlines’ wheels and brakes repair shop in Tulsa, Oklahoma, has been supplied with all the necessary tooling and on-site training to ensure state-of-the-art maintenance practices on Safran products,” says Potier.
Potier says all the equipment to upgrade and support American’s fleet will be manufactured locally at Safran’s Walton, Kentucky facility, which will also perform the carbon heat sinks exchanges.
According to Potier, Safran has positioned an initial inventory of main assemblies and piece parts at American to provide support for the program’s launch, and additional material will be delivered to the carrier progressively as the aircraft are upgraded. “At the end of the day, the key challenge is mainly about logistics—making sure all resources such as material and labor are aligned at the right time and the right location for the upgrade program to be successful,” he says.
Potier highlights a few key trends currently driving airlines to upgrade to carbon brakes, such as a sharp rise in fuel prices that threatens airline recovery, but can be mitigated by lowering aircraft weight and, in turn, reducing fuel burn. More stringent environmental policies are also driving airlines toward more sustainable initiatives, notably the reduction of their carbon dioxide emissions. Airlines also want to reduce their maintenance costs and ensure high dispatch reliability through more reliable, longer-life components.
Several airlines and MROs have in-house capabilities to service carbon brakes. According to Safran, carbon brakes provide operators with a longer on-wing life—up to twice as much as steel brakes—thus reducing the number of maintenance events. In addition, Potier says carbon brake shop visits require less labor time than steel brakes, as carbon disks do not require specific maintenance operations, contrary to steel disks.
With carbon brakes supplanting steel brakes, Potier believes the existing MRO capacity is more than enough to support the associated services. “From a labor and logistical standpoint, the increased volume of carbon brakes in operation will have a positive impact on the cost of wheel and brake services for the operators,” he says.
Safran Landing Systems has developed a U.S.-based subsidiary, Wheels & Brake Services, to support its operators in the region. The business provides support to U.S.-based operators across its five strategically-located repair shops.