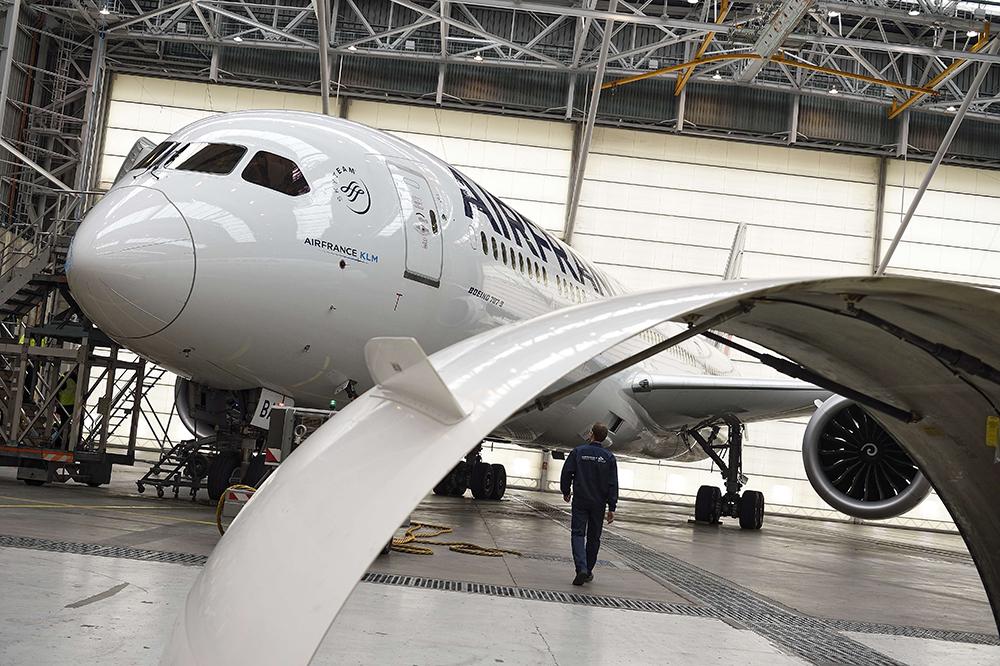
As the Boeing 787 matures, MROs are investing in added capabilities for more intensive checks, but also in aftermarket training to support its heavy reliance on electrical systems.
In Arizona, Ascent Aviation Services has added 787 services to its capabilities. However, Chief Commercial Officer Scott Butler feels 787 service providers in the U.S. are few and far between.
“The digital nature of controls and systems leads to a lot of specific tooling that requires significant investment for an MRO to add it to their capabilities,” Butler tells Aviation Week Network. Also, many of the airlines operating the 787 in North America have in-house capabilities, so the business case requires a large investment in a limited market, he says.
Delays and issues in the supply chain, especially for unique 787 parts, have been a recurring problem. Butler says controls by the OEM have led to practically no used serviceable material or parts manufacturer approval (PMA) parts in the market.
OEMs will often try to block PMA parts to protect their market, which Mike Cazaz, president at Werner Aero, fully acknowledges. “What I don’t understand is, why aren’t they [OEMs] coming up with solutions to the supply chain problems?” he adds. “I guess they feel that the customers have no place to go and will be forced to wait for the OEM.”
Since the 787 relies heavily on electrical systems to operate various aircraft functions, troubleshooting and fixing electrical issues often requires extensive training. AFI KLM E&M has its own internal European Union Aviation Safety Agency Part 66 training center, in consultation with Boeing.
“In general, troubleshooting and fixing electrical issues on a 787 is not that difficult,” says Jorgen Hoogendoorn, fleet chief for Boeing 787 at KLM Engineering & Maintenance. He refers to numerous “self-tests” on the aircraft that can flag any suspected parts, which then leads to suggestions for a component replacement.
“Sometimes, you will find a combination of multiple issues concurrently, which are tough to deal with,” Hoogendoorn says. However, he feels that such technical issues are often tackled with the support of Boeing, in-house technical expertise and sometimes assistance from other operators.
“Boeing is of great support, but in some cases, the issue is as new to them as it is to the operators,” he says.
Hoogendoorn also recommends that operators consider investing in soft time programs, but to exercise caution. “Consider the soft time options well, because ultimately you are paying double as an operator for the low performance of components, the lack of sufficient parts and the absence of reliability improvements by the OEM,” he says.
Even though capabilities are growing, there is still a lack of widespread expertise and facilities that can handle composite repairs, as on the 787s, causing delays and increased costs for operators. For example, damage to wings and flight controls requires different repair techniques compared to previous generation aircraft, so planning is fundamental for MROs and aftermarket service providers.
“We have a large composite back shop that has been integral in ensuring success for our 787 projects,” says Butler. “It’s been a learning curve for the different procedures, but we are able to overcome any hurdles thrown our way.”