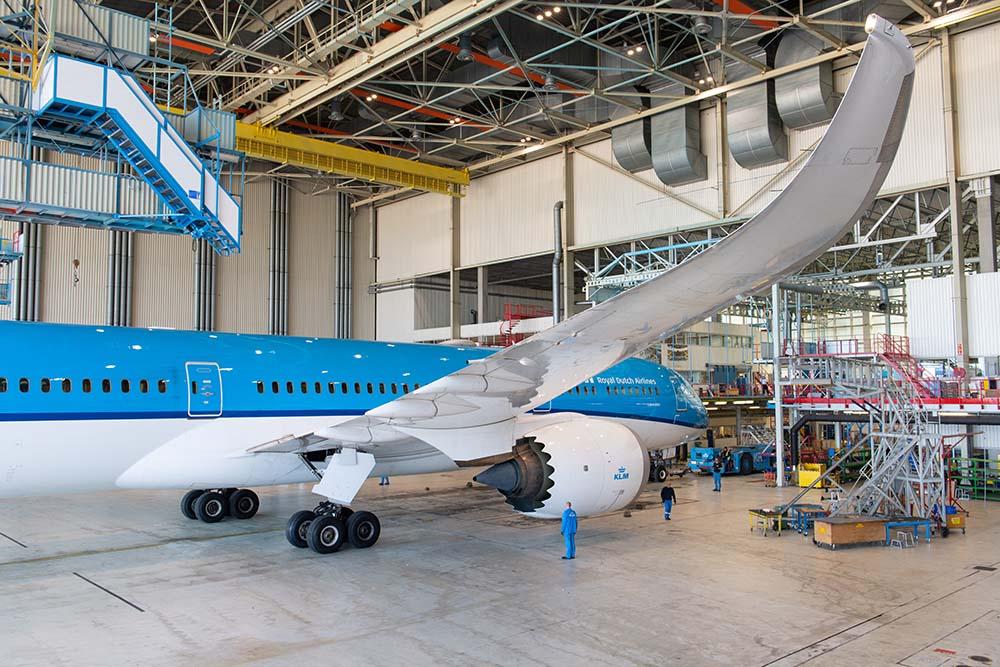
The Boeing 787’s unique parts have led to challenges in providing component support services.
Credit: AFI KLM E&M
The Boeing 787 has served as a cornerstone for airlines seeking to optimize operating costs and expand international routes. However, supply chain shortfalls are hiking up costs, so MROs must innovate and tighten partnerships to reduce uncertainties. After 13 years of in-service operations, the 787...
Supply Chains Pressure The Boeing 787 Aftermarket is part of our Aviation Week & Space Technology - Inside MRO and AWIN subscriptions.
Subscribe now to read this content, plus receive full coverage of what's next in technology from the experts trusted by the commercial aircraft MRO community.
Already a subscriber to AWST or an AWIN customer? Log in with your existing email and password.