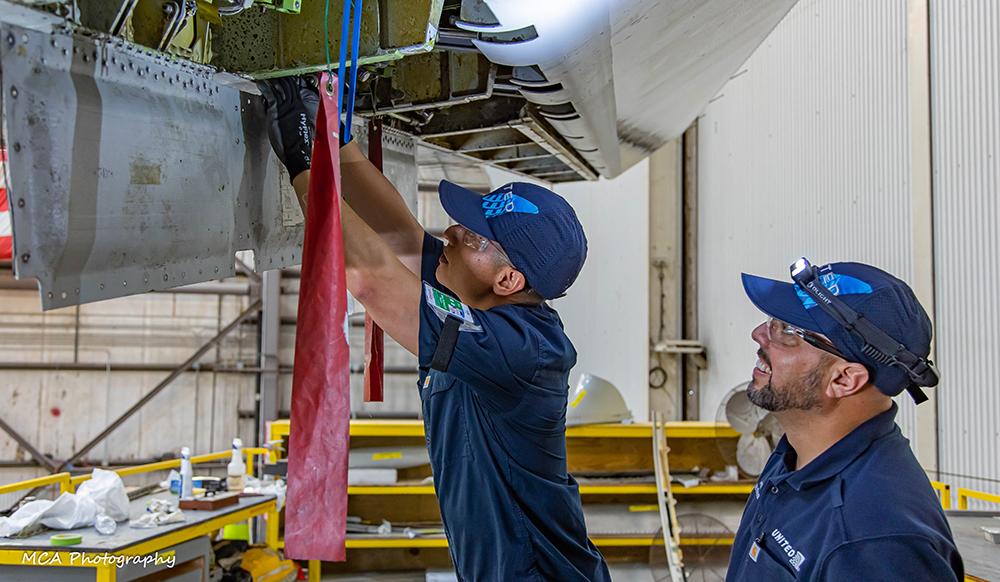
Calibrate Apprentice Daniel Maldonado and his trainer, Louis Bernard.
NORFOLK, Virginia—United Airlines, like other carriers in the U.S., is bracing for an impending wave of aviation maintenance technician retirements. This has necessitated major hiring pushes to replace retiring workers, leading to an industry-wide trend toward what Boeing has labeled “juniority across the workforce.” To bridge the gap, United is expanding investments in Tech Ops training, including growing its Calibrate apprenticeship program and opening a new Technical Operations Training Facility in Houston.
At the Aviation Technician Education Council Annual Conference here March 18, leaders from United’s Calibrate program shared data about why this training is a key workforce strategy and examples of its success thus far.
According to data shared at the conference by Jeremy Cooper, Calibrate senior manager, around 34% of United’s nearly 10,000 technicians have 30 yr. or more of experience at the airline and around 47% are “retirement ready.” Meanwhile, about 35% now have less than five years of experience at United. These numbers are particularly acute at bases such as San Francisco and Houston, which have 900 and 600 retirement eligible technicians, respectively.
United proactively launched Calibrate internally in 2022 to provide on-the-job training aimed at accelerating employees’ technical skills. The program has three tracks: aircraft maintenance technician (AMT), facilities maintenance technician and ground service equipment (GSE) technician. Since then, it has grown rapidly, expanding to nine U.S. cities and 126 apprentices by the end of last year. Cooper says Calibrate currently has around 16,000 applications despite “doing zero advertising.”
Calibrate was launched as a three-year program, but Cooper says United has been able to shorten the timeline to two years by partnering with Part 147 schools and leveraging technology. Apprentices within the AMT track receive airframe general training for the first 18 months before they are sent to Part 147 partner schools to receive powerplant training.
“[Apprentices are] actually building technician seniority while they’re in the apprenticeship program, so if they spend 24 months in the program, they will accrue 18 months of technician seniority,” says Calibrate Director Scott Ferris. “Seniority is big, especially when we’re hiring the numbers we are. It could mean the difference between a better station, shift or crew.”
Ferris adds that staff who sign on to be apprentice trainers get benefits as well, jumping to lead pay for their additional efforts.
While “the big elephant in the room” when United first developed the idea for Calibrate was what the return on investment was going to be, Cooper says, “We’re at the point now where the proof is starting to be in the pudding.” For instance, he says Calibrate’s first group of 15 AMT apprentices have all passed their airframe and general exams on the first try, “So we’re seeing it work.”
One way in which United is ensuring success is by partnering with software provider GoSprout to improve tracking and documentation of apprentices’ progress, including better aligning FAA Airman Certification Standards (ACS) with ATA codes.
“If a trainer gets a new apprentice for the night, they can look at the app and say, ‘I need to focus on Chapter 31,’ and then go hit it and make some more progress,” says Ferris. This has been helpful in ensuring that trainers do not simply unload busy work on apprentices that would not help them progress through necessary ACS skills.
United had 64 AMT track apprentices last year, and this year Cooper says the Calibrate team hopes to launch more cohorts and apprentices and have 55 graduates between all three tracks. Cooper and Ferris hope to roll the program out to more U.S. cities as well as to its first international city. However, Ferris notes that United is trying to balance hiring needs at certain stations with the added workload that apprentices would generate at those locations.
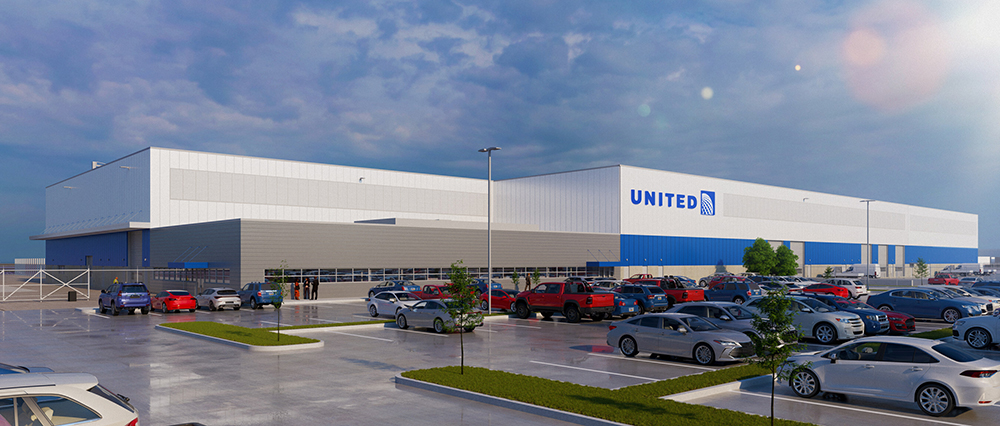
Beyond apprenticeship training, United is building a technical training hub in Houston. On March 25, the airline opened a new $16 million Tech Ops Training Center (TTC) and broke ground on a $177 million GSE maintenance facility at George Bush Intercontinental Airport.
The 91,000 ft.2 TTC includes sheet metal and composite training shops; desktop simulators that enable technicians to learn Boeing 737 and 787 troubleshooting; and scenario-based engine maintenance and inspection training, such as borescope and non-destructive testing engine inspections. United says the TTC will allow it to combine simulated and hands-on instruction in a shop environment to increase knowledge retention and enhance learning without taking aircraft out of service.
The 14,000 ft.2 GSE maintenance facility will train United’s GSE maintenance team of more than 130 to perform critical tasks such as charging batteries, fabricating metal and monitoring electronic controls on its more than 1,800 ground service vehicles. United plans for the facility to open in 2027.
On March 26, United also began a $315 million project to expand and modernize its maintenance facilities at Orlando International Airport. It is building a new 354,400 ft.2 maintenance campus that will house two hangars, a warehouse, shops, offices and work areas. The two hangars will be able to accommodate up to six narrowbodies or one widebody and three narrowbodies simultaneously.
United’s Orlando Tech Ops staff of more than 1,000 will continue to operate in its existing Orlando facilities while construction takes place. The new facility is expected to open by late 2027, at which point the original hangar, constructed in 1954, will be demolished.