Lavatory OEMs Incorporating Innovative Engineering And Design

Airliner lavatories are undergoing major engineering and design makeovers, largely accelerated by the COVID-19 pandemic.
“The pandemic impacted how we approach lavatory design,” says Jeffrey McKee, director of customer experience and design for interiors at Collins Aerospace. “From the start, the Collins advanced technology group and the business development teams approached the subject as an opportunity to understand how passenger and airline customers’ concerns and perceptions of using public spaces, such as a lavatory, have changed since the COVID-19 breakout. A considerable emphasis on minimizing physical touchpoints and maximizing hygiene was the message Collins received through its research engagements.”
McKee points out that the customer feedback essentially became the catalyst for Collins’ design and engineering teams to develop touchless solutions to support a hands-free interaction with lavatory amenities, along with active antimicrobial features such as Lilac-UV and surface coatings and a list of other passenger-enhancing features focused on hygiene.
“The pandemic has opened our designers’ eyes to see a world of new product ideas amidst a new normal in air travel and passenger safety,” McKee notes. “The lavatory is starting to expand the technology into the passenger cabin and crew space.”
In tandem with those trends, lavatories are incorporating lighter-weight materials, according to Teddy Gil, chief administrative officer of Sheffield Aerospace, a Texas-based engineering and design consulting firm. “Many of the traditional parts that were made from fiberglass layups have been converted to honeycomb composite paneling and injection molded parts to save weight,” he explains. “Thermo-formable designer plastic sheets are also being used to provide a more customized look while reducing previously labor intensive application. Another area seeing a high degree of use for customization is hydrodipping to obtain custom designs for countertops and paneling areas.”
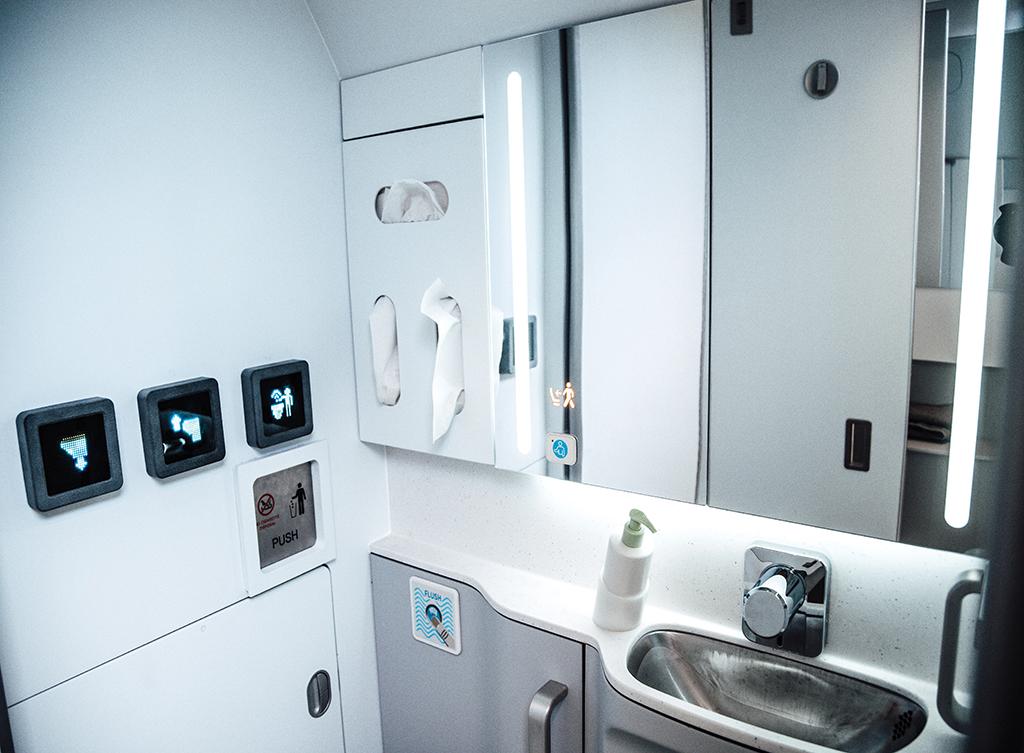
Gil agrees that there is renewed interest in touchless aircraft lavatory components such as faucets, toilet flush buttons and soap and lotion dispensers (in premium cabins) largely due to COVID-19. But he cautions that the key to successful application of touchless technology will depend primarily on its reliability, which he notes has not always worked as designed, along with the capability to combat continued COVID-19 variants that would prevent a return to pre-pandemic normalcy. He adds that while cost is a consideration, a more reliable product would mean increased demand, which will help drive down the overall cost. “Here, again, reliability will be key to its success,” he stresses.
Still, there is no question that touchless lavatory components are an inexorable trend. “We are experiencing an increasing request for touchless technologies,” says Guido van Geenen, vice president of corporate communications at Diehl Aviation in Germany. “We firmly believe that, in the near future, touchless and hygienic solutions will be assumed as a standard solution by passengers and will move quickly toward an industry standard, as it is in present-day public bathrooms.”
While touchless technology applications in airliner lavatories are moving ahead, they will be implemented on a phased basis, predicts Ali Dadvar, vice president of marketing and sales for Adams Rite Aerospace in Fullerton, California. “Faucets, toilet flush switches and buttons and waste flaps will lead the first phase, followed by a second phase to include soap dispensers and toilet seats,” he says. “For the third phase, the technology will extend to the lavatory door and the hand dryer [and]ultraviolet lights.”
For example, Dadvar reports that in June, Adams Rite Aerospace introduced its Touchfree Faucet for aircraft lavatories. The touchless component’s development, he notes, actually began in 2018-19, when the company “recognized a possible trend of the technology” from the industrial to the aviation market. “COVID boosted interest from the aviation market,” he says.
The Touchfree Faucet, which has a pending patent, uses infrared technology linked to electronic circuitry to release water upon detecting the user’s hand. Dadvar says it is lighter-weight, takes up less space and is more reliable than legacy products. It is now available for retrofit, under a service bulletin from Adams Rite, which holds the supplemental type certificate.
Since June, Adams Rite Aerospace’s Touchfree Faucet has been flying on a Boeing 737-8 in commercial service and, according to Dadvar, will be introduced throughout the fleet of that aircraft operator, which he declined to identify. He notes that the faucet can be retrofitted in both narrowbody and widebody aircraft. Interest in the faucet, he reports, has been indicated by airlines for retrofit as well as lavatory OEMs for line fit.
Dadvar adds that Adams Rite has four more touchless aircraft lavatory products in development. They include a waste flap, flush switch and soap dispenser slated for certification during the second quarter of 2023; certification of a touchless toilet seat is expected by the third or fourth quarter of 2023.
“Cleanliness in the lavatories has always been an expectation from passengers, but the recent health and hygiene requirements have reinforced that expectation and have given it a stronger voice,” says Julie Imbert, marketing director for Safran Cabin. “The gap between the [hygiene] solutions on the ground versus what can be offered in the air is also now challenged further, giving a push to innovations such as touchless features.”
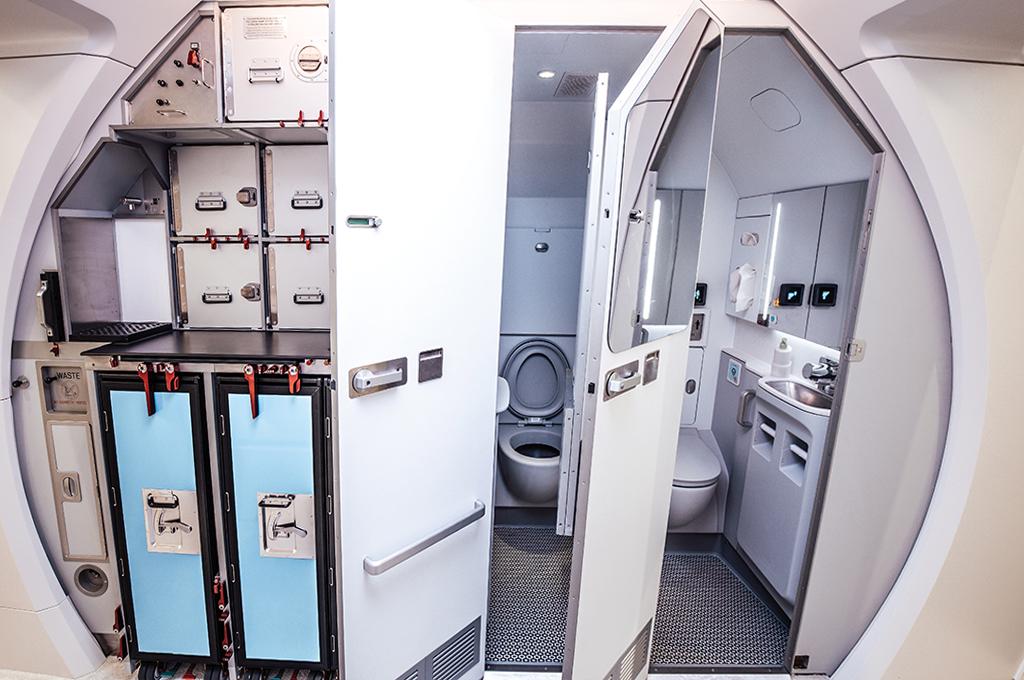
Currently flying on the Airbus A350 platform, Safran Cabin touchless systems are available for retrofit across all fleets, Imbert reports. Customers may select touchless faucets, waste flaps and flush switches.
While not directly linked to hygiene, sustainability is another important trend in lavatory design that has gained more visibility during COVID-19, Imbert notes.
“Sustainability is definitely something we are working on, but as the research is still running, we can’t share specific details yet,” she says. “Another important element we are looking at in the design of our lavatories is how we can leverage the synergies and experience of our various portfolios to make the lavatory environment more sustainable overall, addressing things such as water consumption, durability, weight, materials—as well as how the units are produced and handled at the end of their lives. The topic is vast and cannot be addressed simply, but we are working hard to make the right steps toward a more sustainable offer.”
Ultraviolet light (UV) applied as a disinfectant to lavatories is another topic of research at Safran Cabin, in concert with specialists in UV sanitation. According to Imbert, various applications of mature UV technology “have reached the investigative stage.” However, she cautions that UV is part of a spectrum of germ-fighting technologies that need to be applied in the right combination.
“Finding that combination is what we are doing with our customers through a series of workshops, looking at how it fits with their own cleaning routines as well as understanding the expectations of passengers,” she says. “The goal is to ensure those new technologies facilitate the processes without creating new challenges for the users during and after the flights.”
Asked about any developments focusing on lavatory maintenance, Imbert cites Safran Cabin’s Revolution toilet, which is currently in service. The design, she explains, has been simplified to reduce the amount of spares needed and to bring more commonality, without regard to the lavatory or aircraft on which the toilet is installed.
Sebastian Tivig, senior cabin integration manager at Diehl Aviation, reports that, along with sanitary considerations, its customers expect sustainability measures that reduce CO2 generation. One such approach is a grey water reuse system being developed by the company.
“This system will enable clean water used for hand-washing to be reused in toilet flushing,” Tivig says. “It allows airlines to save up to 210 kg [465 lb.] of fresh water for the lavatories on a long-haul flight.”
Diehl Aviation continues to develop designs for combined galley/lavatory designs. In addition to providing space for more cabin seating, Tivig reports that the approach is considered one of the best ways to provide a wheelchair-compatible lavatory. In fact, he notes that Diehl is seeing a renewed interest in highly integrated full-wheelchair-capable lavatories for single-aisle aircraft. He cites the OEM’s Skypax module, which provides roughly 2 in. of additional interior space and is 50-80 kg lighter than competing products on the market.
“Combined with a divider wall, this allows us to accommodate a full wheelchair—and a support person—inside the lavatory, with closed doors,” Tivig says. “It also allows for an additional seat row and reduces total aircraft empty weight. Another version, the Aft-Simplex, developed together with our partner HAECO Cabin Solutions, avoids the reinforcement of the aircraft floor.”
Tivig adds that although the focus of accessibility has been on people with limited mobility, a significant portion of the population has limitations that are not as easily identified and are generally overlooked.
“While there are people with limited range of motion or decreased arm strength, there are those who have vision or hearing limitations, color blindness, etc. We have some solutions for this in our touchless lavatory and have done research and testing. But right now, there is no market for this solution,” he explains.