Aircraft Seat Supply Chain Issues Raise Potential MRO Implications
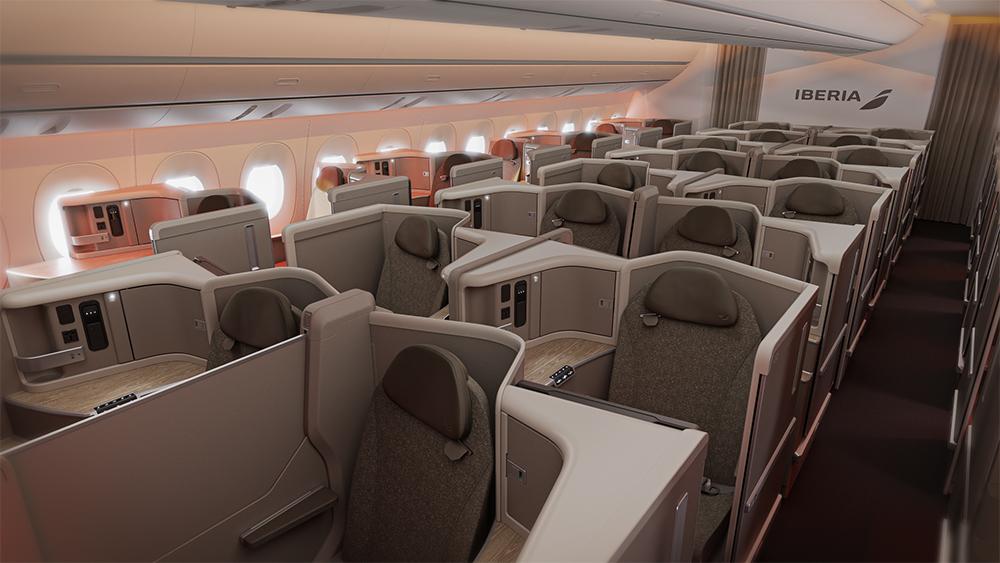
Iberia's latest Airbus A350 business class cabin was delayed, leading the airline to take delivery of aircraft with empty space up front.
Since its post-pandemic restart, commercial aviation has been plagued by ongoing supply chain issues, and some of the most visible consequences have impacted the cabin interiors industry—and, specifically, seats. Supply problems are combining, and in some cases multiplying, to add delays for interiors, aircraft delivery and wider operations. These issues all have broad and deep implications for MRO.
On the surface, the consequences can be very visible, including aircraft stuck on the ground outside final assembly lines awaiting seats or entire cabins missing from operating aircraft. For instance, Iberia took Airbus A350-900 aircraft without their delayed Recaro CL6720 (now renamed R7) fully flat staggered business class doored suites, installing instead a few economy class seats used only as handholds for crew passing through the business class area.
Similarly, Lufthansa’s latest Allegris A350-900s are being delivered without a first-class cabin following delays to the bespoke Collins Aerospace suites. Instead, on the front bulkhead of this space is a ‘computer spinning wheel’ motif with “Lufthansa Allegris First Class” and “Loading…” printed alongside and within. Here, too, a few scattered economy class rows provide handholds.
Aircraft in this situation require later MRO services to install the seats, which airlines will be keen to do as swiftly as possible once they have been produced and certified. Uncertainty about timings, especially around certification, will be an opportunity for MRO providers that have responsive capacity—both for these specific retrofits and for other work that is pushed out as a result.
A further problem is one of distribution. Premium seats are manufactured at a very limited number of specific factories, which are geographically distant from aircraft assembly lines. Seat manufacturers are used to shipping products to Toulouse for Airbus widebodies and Seattle or Charleston for Boeing widebodies. Shipping to MROs elsewhere may add delays because of distance, customs complications and inbound quality work. Compounding the problem are disruptions around the Red Sea shipping lanes and elsewhere. MROs will need to demonstrate understanding and capability here.
It is interesting that the aforementioned empty-cabin aircraft examples are A350s, primarily because Airbus is far out-delivering Boeing at the moment, particularly in widebodies. Lufthansa’s Allegris cabins were supposed to roll out on the Boeing 777X but were first installed on the A350.
Lufthansa has a multi-source supply chain for its Allegris business class: Stelia is to build the seats for the Airbus A350 and Boeing 747, Collins is building the seats for the A330 and 787, and Thompson is building the seats for the 777 and 777X. This means that not only did the seat debut on a different aircraft than originally planned but it was also built by a different seat manufacturer. This is likely a contributor to the clearly visible production quality issues within the cabin onboard the first two aircraft delivered, and MRO services will be required to remedy this.
Expertise will also come into play. Seat installation and integration are complex tasks, especially at this early stage of seat lifespans, when few lessons have already been learned. A new seating product is normally first installed on a factory-fresh aircraft on the airframer’s final assembly line, with MRO staff seeing it either as a follow-on retrofit program or during heavy check cabin replacements.
If an integration issue—such as power consumption bottlenecks or seat-sidewall interface problems—arises, the OEM’s entire wealth of expertise can be used to address it. If the problem is identified during a remote retrofit, or even at an airline’s home base far from the factory, resolving the issue can take more time and require additional resources.