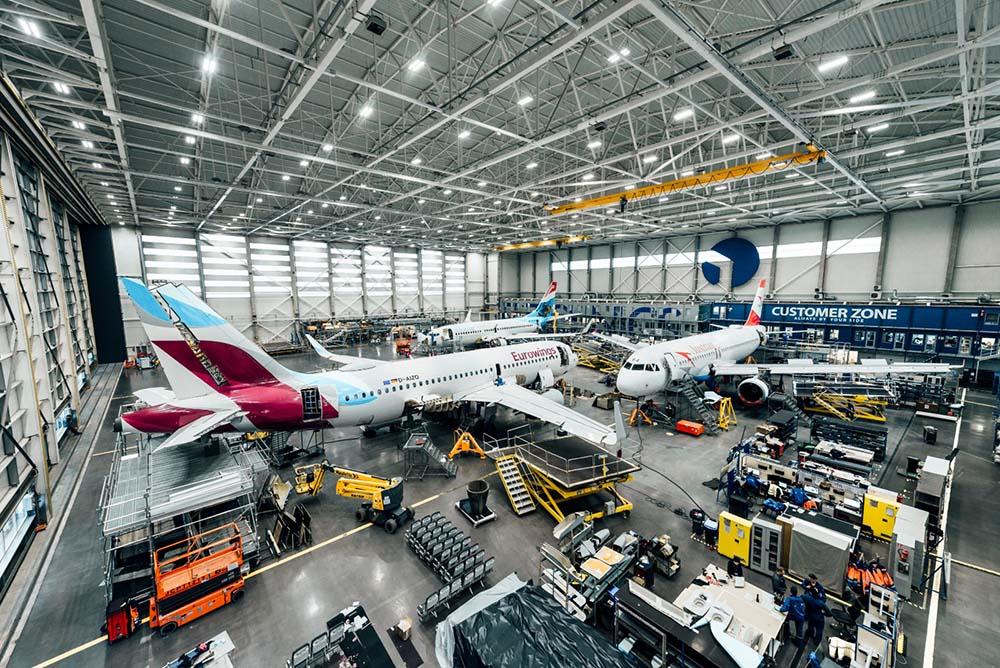
Experts at FL Technics are seeing far more Airbus A320 family aircraft coming in for maintenance work from European customers compared to similar sized aircraft such as Boeing 737NGs and MAXs. Not surprisingly, A320s still dominate the region outside of 737 operators such as Ryanair.
Juozas Lapeika, deputy CEO for production management at FL Technics, tells Aviation Week that while the company’s approach is to distribute maintenance lines as evenly as possible between 737s and A320s, the clear trend is leaning toward A320s. “However, we do expect a forthcoming influx of 737NG freighters for comprehensive nose-to-tail maintenance and the initial heavy maintenance repair post-cargo conversion,” he says.
In comparing the maintenance dynamics of both aircraft types, Lapeika says Boeing has applied a philosophy for “repair not replace” that grants MROs greater control. However, he points to persisting challenges, including a scarcity of raw materials, labor shortages affecting OEM query responses and complications arising from new provisions in the latest European Union (EU) sanctions package regarding the origin of raw materials.
Last month, the EU published its 12th package of sanctions against Russia, mainly focusing on imposing additional import and export bans on Russia. Reportedly, several billion Euros worth of Russian metals have been imported into the EU and, prior to the latest round of sanctions, the aerospace industry has heavily benefited from that.
“Unfortunately, OEMs' hesitance to furnish documentation further exacerbates these challenges, resulting in delays when parts encounter customs hurdles,” says Lapeika. He adds: “Despite these obstacles, our focus on long-term support for critical areas such as components, inspections, repairs and pooling remain pivotal.”
In terms of technology, Lapeika says the integration of sophisticated data software into operations has led to transformative changes in how FL Technics wants to deliver services, including nose-to-tail support. “This tech infusion enhances our project preparedness, facilitating streamlined processes for material procurement and the acquisition of specific tooling,” he says.
However, Lapeika says the real game-changer is its internally developed online project management system. “This becomes particularly crucial in project production, enabling us to effectively manage bottlenecks and promptly revise any maintenance programs with efficiency and precision,” he says.
Lapeika notes that maintenance requirements differ by customer, so FL Technics seeks to adapt to individual needs. “Larger fleet operators often seek extended nose-to-tail lines, for instance, securing prime slots, while smaller operators strategically choose optimal slots during the peak of the winter season,” he says.
Larger fleet agreements typically have more favorable conditions and Lapeika says multi-year contracts—with the inclusion of multiple lines at a single location—are commonly preferred by larger operators. “It's worth noting that each client has distinct procedures, requiring time for our teams to adapt,” he adds.