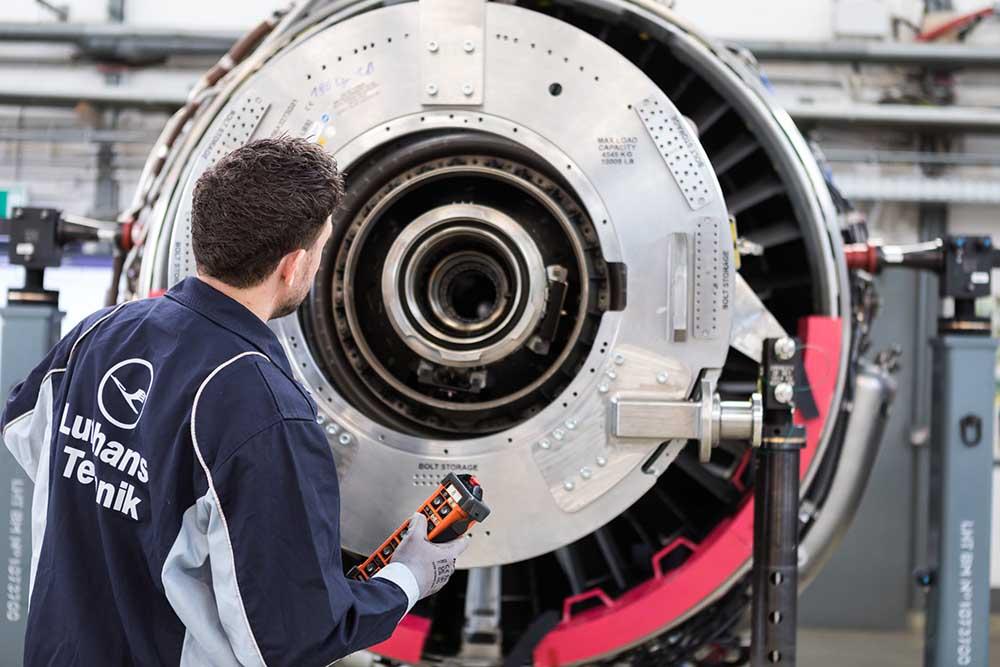
MROs constantly strive to achieve optimal engine performance in maintenance processes and, therefore, continuous monitoring of exhaust gas temperature—or EGT margin—remains an essential parameter in evaluating engine health.
StandardAero has seen a rebound in core performance restoration shop visits (PRSV) allowing operators to significantly recover EGT margins, without necessitating the cost of a full engine overhaul. It claims that by restoring close engine tolerances through the repair or replacement of aerofoils, stators and seals, a core PRSV can restore EGT margins to 70-80% of new-engine levels, thereby significantly extending time on wing while improving specific fuel consumption.
EGT margin deterioration is largely driven by hardware distress, and some of the typical culprits include issues like increased tip clearances, seal leakage, airfoil erosion and compressor fouling. As such, any maintenance activities which address these areas will help to recover and maintain EGT margins. Technical experts suggest the replacement of expired life limited parts (LLP) will provide the largest recovery in performance, but operators can also protect their margins through less substantial work scopes such as regular compressor washes, which help to keep the gas path clean by removing contaminants from the engine.
Dag Johnsen, the new chief operating officer at Aero Norway, says EGT margin recovery is important to estimate the engine’s potential performance life in service and is often used to determine the minimum LLP cycle life for that particular build. He believes an efficient engine is also far more economical to operate since the fuel consumption is reduced, and this also contributes to reducing emissions.
According to Hinnerk Behn, Lufthansa Technik’s head of propulsion system engineering services, the aim after a PRSV is to bring the EGT back to a level in which engine acceptance testing can demonstrate sufficient EGT margin, matching the engine’s expected life span. “This highlights the importance of maintaining engine performance during shop visits,” says Behn. “Planning a specific on-wing time or build life after the shop visit involves significant investment in part replacement and the performance margins must align with this lifespan to ensure cost efficiency.”
In a typical scenario, as Behn explains, the engine is disassembled for overhauling, focusing on the combustor and high-pressure turbine to address tip and seal clearances via parts repair or replacement. Additionally, and depending on their condition, the high-pressure compressor and stage 1 low pressure turbine nozzle might also undergo disassembly and restoration. “This process allows for the recovery of approximately 75% of the initial new engine production EGT margin,” says Behn.
Stay tuned for more about trends in performance restoration shop visits in the upcoming February issue of Inside MRO.