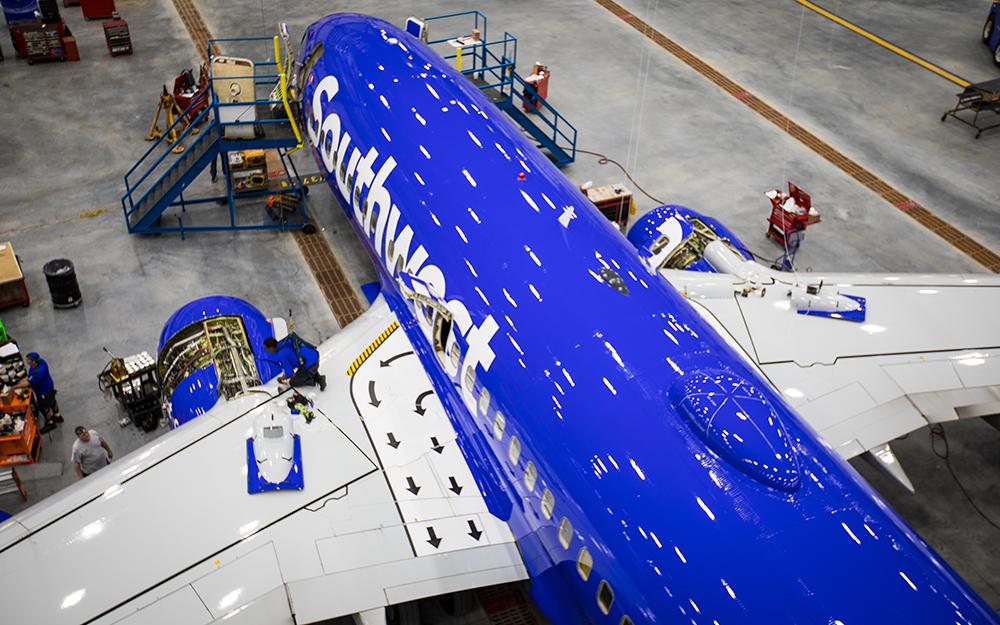
Southwest is wrapping up its large-scale transition from two older maintenance and engineering systems to IFS’s Maintenix software. It says the migration project, which began in 2015 and continued through the COVID-19 cash crunch, provided several major challenges due to its scale and complexity.
According to Landon Nitschke, senior vice president of tech ops at Southwest, this was “the largest single MRO system migration in the history of our industry.” CEO Robert Jordan it slightly differently: “We just finished the largest technical software project in airline history, which is a new technical operation system.”
But there is more to do, of course, including reaping all the benefits for which Maintenix was chosen.
Southwest had been managing maintenance on its Boeing 737-700s with Wizard, its own version of Sabre’s Maxi-Merlin software, and managing maintenance on its 737-800s and 737 MAXs with TRAX. According to Joe Marcella, Southwest’s senior director of technical operations planning, it chose Maintenix for three primary reasons.
First, to improve compliance with regulations. “Maintenix has very strong controls,” Marcella says. Secondly, to move toward real-time digital data entry, versus the airline’s largely paper-based MRO processes. And third, to build a foundation for Southwest’s evolution toward mobility for mechanics.
The airline had already been using PTC’s supply-chain solution, PLM, so this app needed to be integrated with Maintenix in the new MRO system.
Marcella shared with Aviation Week the major steps necessary for implementation of Maintenix: “First, we had to understand how it works and overlay that with our business processes to understand which would change,” he says. “There was lots of exploring and re-imagining of how we could operate.” The airline also had to identify features of Maintenix that would not work for Southwest, so IFS could adapt them.
Data migration was a “big piece,” Marcella says. This required a major effort because the airline planned to go live at the fleet level with hundreds of aircraft rather than bringing on aircraft in small numbers. “The entire ecosystem needs to be in place from the start, up front,” says Marcella.
These and other tasks were run in parallel, not in a sequence of steps.
Marcella did not provide any estimate of the man-hours or costs required, saying only that the implementation team was “a big number” and it fluctuated over time, tapping staff in Southwest’s technical operations and information technology units, plus staff at the third-party companies that assisted in implementation. “It was an extremely complex effort over five or six years and a huge resource commitment,” he says.
Prior to data migration, Southwest had to change the architecture of its MRO data from that used by TRAX and Wizard to the requirements of Maintenix. “Maintenix has a unique data structure, and that affects parts, schedules and rules,” says Marcella. “We had to revalidate the data, make sure it was correct, and then came the migration.”
In addition, Maintenix requires more data than did the previous systems, so the implementation team had to append this additional data.
The airline also had to change its business processes. “That was significant,” Marcella says. “It required huge change management messaging and training. And we are still on change management a year after we started to go live.” Training sessions were tailored for each work group.
One broad theme of change was the shift from paper to digital. “Before Maintenix we were almost all paper, except for some pockets with electronic sign offs,” Marcella explains. “Now we use e-signatures to the fullest extent.”
Front-line maintenance employees resisted these changes at first, but for what Marcella calls “the right motivations.” Everybody at Southwest seeks efficient operations, and the switch to electronic processes did require some extra time up front.
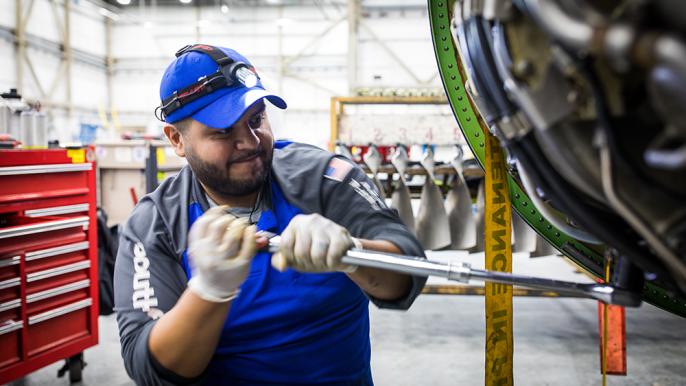
Credit: Southwest
Southwest’s new concept of operations is to move from high volumes of document entries to one-time digital entry before aircraft dispatch. This should improve accuracy, but it also brought changes to support workers. For example, authoring task cards would be very different. Still, the changes for support employees were not as tough as for front-line mechanics.
Marcella says Southwest consulted with other Maintenix users on implementation choices. Some airlines deployed the system in modules, but Southwest chose to deploy the entire new ecosystem all at once for each of its two fleets. “We did not hold back any large modules,” he says. The initial deployment thus included part, configuration control, electronic signature, work order, supply chain and warehouse functions.
Southwest also wanted a complete cutover to the new system at one time for each fleet to avoiding running several systems at once. “We already were using two systems; we did not want to extend that to three systems,” Marcella says. Management of 737-700s was switched to Maintenix in April 2021, although a few ancillary functions did stay on Wizard for several months. Then the -800s and MAXs were put on Maintenix in November 2021.
Marcella says COVID-19 did not have a direct impact on the transition project. “It was one of the few projects so far along, and management maintained support for it,” he says. Moreover, he adds, the project could not just have resumed instantly at full speed if paused, “so we proceeded through the pandemic.”
Nevertheless, Marcella acknowledges that the pandemic probably cost some efficiency in Maintenix implementation simply because some staff had to work remotely on the project.
Another big consideration in implementing Maintenix was Southwest’s route network, built up around focus cities rather than the hub-and-spoke model. Its aircraft typically rotate around its national network, and the carrier will swap planes among several stations when needed. “In planning maintenance, we have to be nimble,” Marcella stresses. “That creates an additional burden on Tech Ops.” Maintenix, previously implemented chiefly for hub-and-spoke carriers, had to be adapted to robustly support Southwest’s nimble maintenance work on a huge fleet flying point-to-point among focus cities.
So far, Southwest has achieved its principal goals of moving toward electronic records and improving compliance. It is now focusing on exploiting Maintenix to improve efficiency of operations. “Now that Maintenix is stable, we want to use it as efficiently as possible,” Marcella says. That will require some further changes in maintenance processes and some in the app itself.