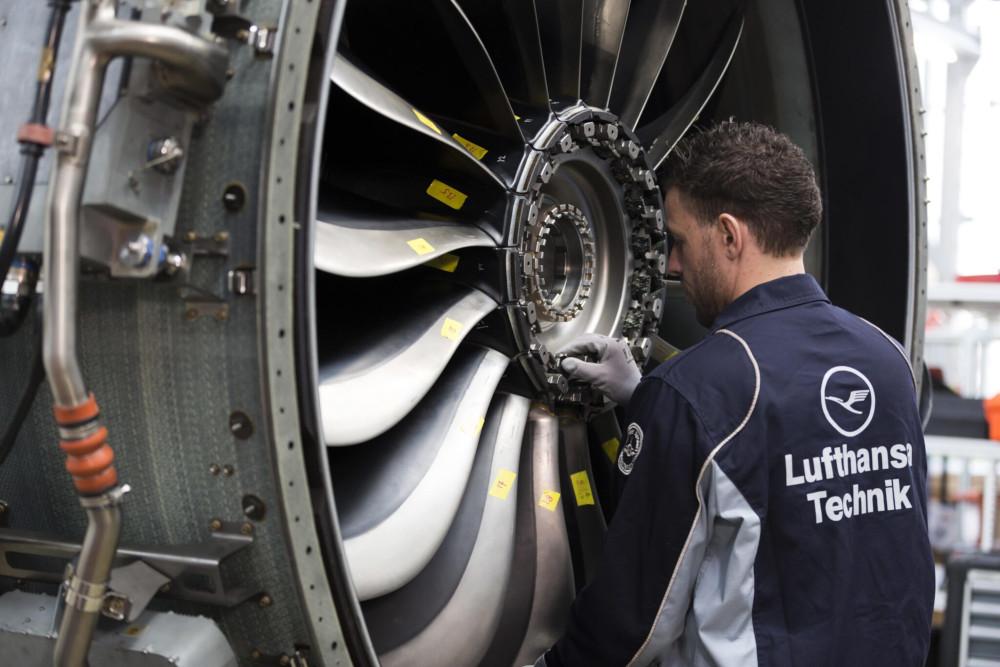
The combination of digitalization, automation and artificial intelligence can save time and improve accuracy in many MRO tasks, particularly non-destructive testing.
At Lufthansa Technik (LHT), for example, analog X-ray inspection used to require processing of film, whereas newer digital X-ray technologies significantly reduce the time between image acquisition and diagnosis, while also offering better resolution.
Another big advantage is the ability to archive images directly, digitally exchange them between the X-ray and production departments and have them evaluated globally through a platform designed for sharing X-ray images.
Several years ago, LHT enhanced the fault inspection process for welded engine cases by implementing its Digital X-ray Gantry system, which boasts 10 axes that can be operated either manually or automatically via a program.
It allows LHT to inspect large engine and other components with diameters of up to 3.8 m using X-ray technology.
A second digital X-ray gantry system is scheduled to be introduced later this year, which aims to further advance the technology by incorporating artificial intelligence-based image recognition algorithms for more automated fault detection.
“By pre-selecting images with potential flaws, this approach can help reduce human error in the inspection process. However, the final decision regarding repairs will always be made by a human,” says Karina van Heteren-Frese, NDT Responsible Level 3 for Lufthansa Technik, in an interview with Inside MRO.
Another non-destructive testing (NDT) advance at the company has been its Extremely Fast Fire Extinguisher Check and Test (EFFECT), an in-house developed NDT procedure for aircraft fire extinguishers’ pressure vessels without the need to purge and store hazardous halon extinguishing agent, cutting turnaround times and also reducing environmental risks.
Instead, EFFECT uses sensitive microphones to monitor sound waves generated by the pressure vessel as it is heated, displaying findings to the inspector in a 3D model on a monitor.
LHT has now inspected 2,500 pressure vessels this way, says van Heteren-Frese, adding: “Today, the majority of pressure vessels is inspected with this procedure, and we are in the process of expanding the solution to other parts inspections as well.”