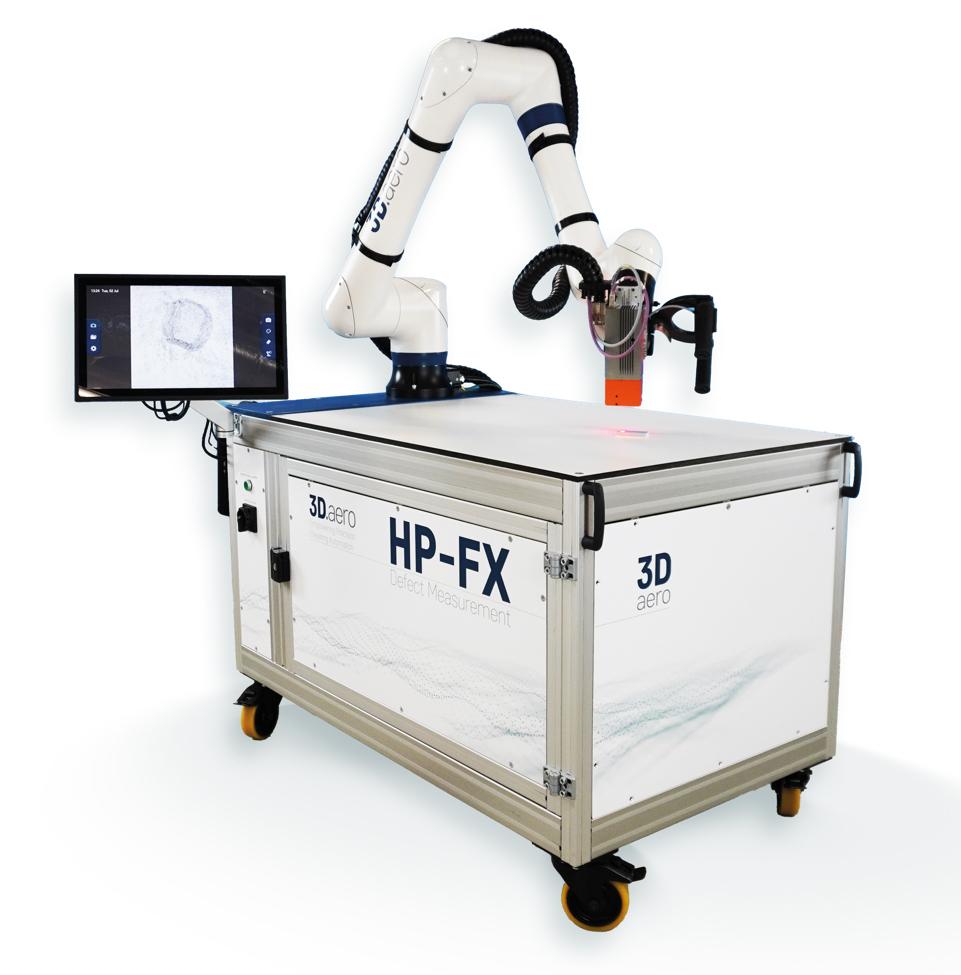
Credit: 3D.aero
1. Shop Floor Detection Company: 3D.aero Product: While MRO companies are enjoying a boom in demand, they are still struggling to replace the large numbers of skilled personnel that left the industry during the pandemic. This places a premium on technologies that are easy to use, such as 3Daero’s HP...
Aviation NDT Technologies Seek Inspection Improvements is part of our Aviation Week & Space Technology - Inside MRO and AWIN subscriptions.
Subscribe now to read this content, plus receive full coverage of what's next in technology from the experts trusted by the commercial aircraft MRO community.
Already a subscriber to AWST or an AWIN customer? Log in with your existing email and password.