This article is published in Aviation Week & Space Technology and is free to read until May 07, 2025. If you want to read more articles from this publication, please click the link to subscribe.

Delta wants to use the power of artificial intelligence to boost its predictive analytics, drone inspection and augmented reality initiatives.
Delta Air Lines and its Delta TechOps subsidiary have been busy the past few years, developing and testing a variety of maintenance-focused technologies such as predictive analytics, drone inspections and augmented reality smart glasses. This year, the airline is focused on scaling these technologies and leveraging the power of artificial intelligence (AI) to boost their efficacy.
On the predictive side, Delta TechOps is using lessons learned from its APEX program, which entails real-time data collection throughout an engine’s life cycle to optimize shop visits and predict material demand. The program won an Aviation Week Network Grand Laureate last year for its promising results, which Delta says include increasing predictive material demand accuracy to more than 90% and more than doubling the procurement horizon to 18 months. They provide suppliers with much further advance notice of the airline’s material needs.
According to Alice Belcher, director of predictive technology engineering at Delta, the airline is looking at how to “lift and shift” that knowledge to its line maintenance and component environments.
“[Engine] shops are very well contained . . . but when you talk about a line environment, you have all these stations that you want to bring parts to, so how do we bring that forecasting?” she tells Inside MRO. “What other variables do we need to get at, either through artificial intelligence or structured data, to be able to help our component area also be able to do that?”
Belcher says Delta is using two data platforms, Palantir Foundry and Airbus Skywise, to help answer these questions. The airline also has built its own large language model, Otto, to drive efficiencies. Based on Google’s BERT (bidirectional encoder representations from transformers) language model, she notes that Otto was “given a master class in tech ops language” using Delta’s relevant maintenance documentation, such as its component and aircraft maintenance manuals.
“We have a weird language in aviation and tech ops,” Belcher says. “If we were just trying to use a large language model out there and we said, ‘717 bleed valve inop’ [an example of a typical maintenance shop finding], it would think somebody was bleeding. It would tell us to call 911, and it would think 717 was a phone call.”
Delta is now looking at how Otto can scrape its large quantities of data from PDFs and handwritten documents to digest the information into the airline’s larger data structure so it can be tapped for insights. It also has embedded Otto into some other automation features, such as its “tech tips” and the ways in which the airline reviews blog pages and ATA insert codes.
Last fall, Delta deployed a Google-search-inspired tool called Otto Search technicians can use to ask questions and find MRO-related information. The tool has been programmed to provide the most likely answer to any given question, as well as a list of recent log pages in which that finding or question has come up. Delta also is looking at how to incorporate nonroutine findings into Otto Search.
“We’re getting feedback from the maintenance control center and our engineering teams to help [determine] what [about Otto] could be better. What other information do we want?” Belcher says. “We have a long list of documents we want to train Otto on, but we’ve also been starting to dabble in how we use that AI capability to look at pictures and diagrams. Those are very difficult.”
COOPERATIVE ECOSYSTEM
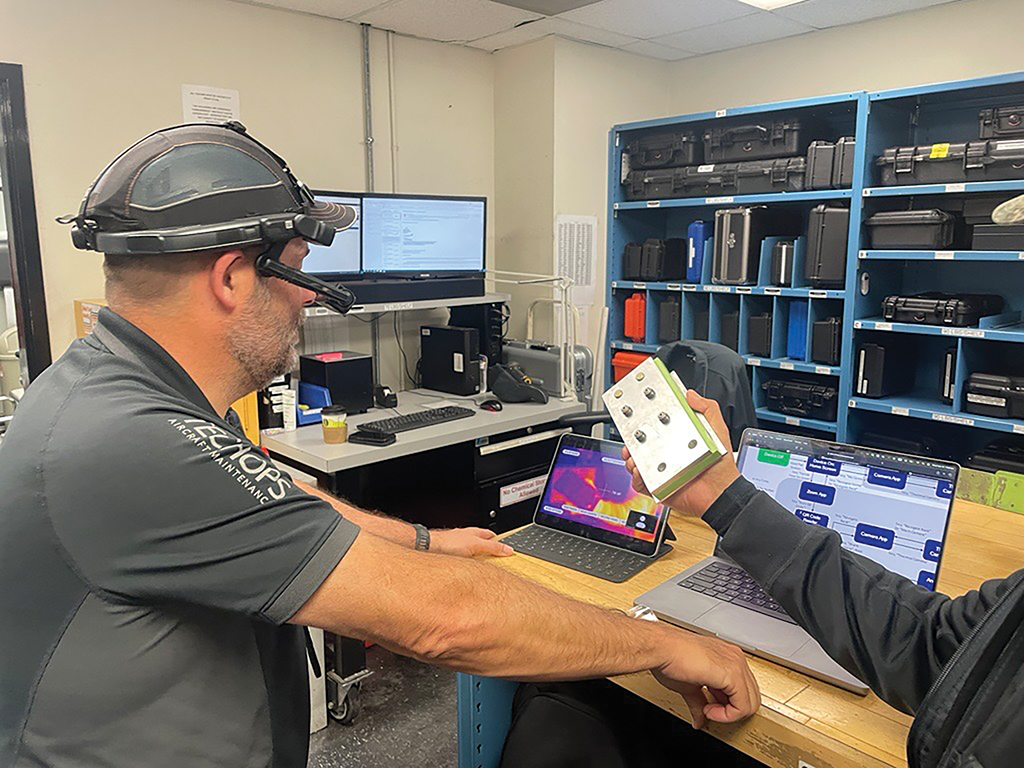
“We’re not trying to take the technician out of the picture,” Belcher explains. “We’re just trying to make it easier for them and our engineering teams to go find the information they need very quickly.”
Delta also is tapping user feedback about other technologies it is developing, such as drone-based inspections and augmented reality glasses. Both technologies have been used successfully at the airline’s Atlanta base, but now it wants to expand their use to other locations.
Belcher cautions that scaling and adoption are two of the most challenging aspects of technology deployment, so her team is working with user groups to devise the best strategies for the larger organization.
For example, in Florida, Delta sees considerable impact from lightning strikes—a scenario in which drone-based inspections have proven particularly useful. However, it may not make the most sense to put one of its drones there since it is not one of the airline’s major maintenance stations. “Do we put [a drone] there knowing it may sit for an entire year? Do we take them with our trip teams? Or do we start thinking about having a ‘go box’?” Belcher says.
“I think we’re at almost 1,000 airplanes now, so how do you scale [technology] into this huge organization? It doesn’t come from top down. It has to come from top and bottom and in the middle,” she points out.
In this spirit, Belcher’s team is working with an employee involvement group comprising technicians working across the business. “They know who to talk to, they bring ideas, and they help us get to the right people to get further definitions of requirements,” she says. “They give us suggestions about how to [deploy technology], and they help us with training and awareness programs, if we want that as well.”
User feedback is also an important part of the airline’s role in the Digital Alliance, a group of industry stakeholders—Airbus, Delta Air Lines, GE Digital and Liebherr—focused on expanding predictive maintenance and data-driven operational efficiencies. As the alliance’s airline stakeholder, Delta provides operational data and a customer perspective about what will and will not work when it comes to OEM-built digital products, Belcher says.
Liebherr joined the alliance last October, and Delta is now working with the aerospace equipment manufacturer on analytics, particularly around the Airbus A220, Belcher says. It is also working with GE on how to use full-flight data through the OEM’s digital systems.
“A lot of our predictive analytics have been built in the past on snapshot data, but because we have the capability to store that much data, we have tools now that can utilize full-flight data in very complex, multivariable, neural-net algorithms that don’t take 2 terabytes to code,” she says. “We can utilize some of those things to get better insights into how our engines and aircraft are performing, and that’s where we’re kind of also moving: How do we use some of these other tools so we can bring our own analytics as an airline?”
Belcher says the Digital Alliance is talking to other OEMs about joining to help contribute to the group’s predictive analytics developments.