COVID-19 Prompts Airlines To Reconsider Lavatory Features And Design
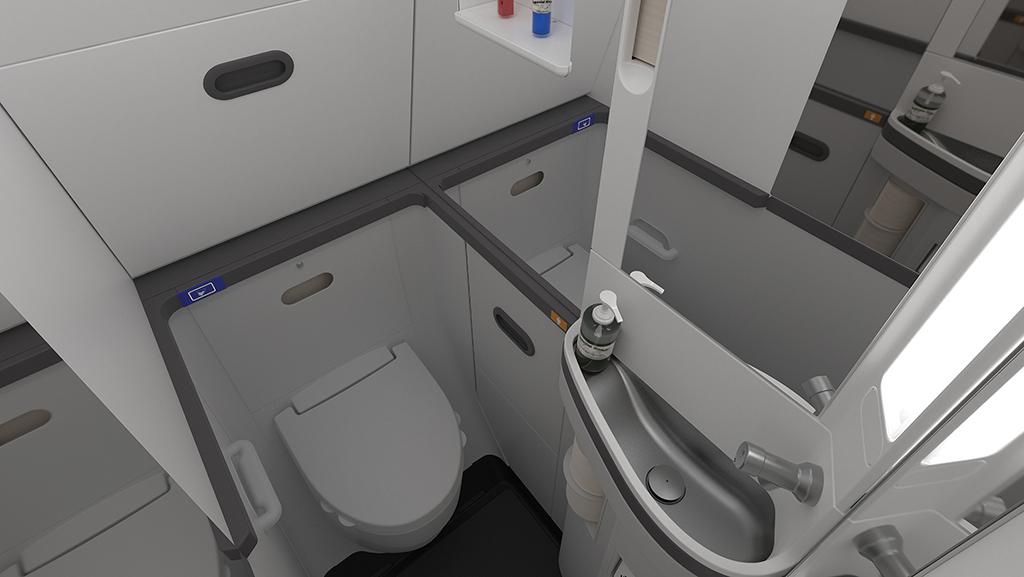
A revolution is taking place in airliner lavatory engineering and design as vendors focus on space savings, accessibility for passengers with limited mobility and, more recently, hygiene issues in the wake of the COVID-19 pandemic.
“There is a definite trend toward shrinking the lavatories to accommodate additional cabin seating, notably at the request of the low-cost carriers globally and U.S. carriers for their domestic fleets,” says Michael Planey, cofounder of HM Planey Consultants, based in Alexandria, Virginia. However, that will have to be balanced to accommodate passengers with reduced mobility (PRM), which is a focus of regulatory agencies and will be at the forefront in the future.
Planey stresses that there is a substantial need to improve the accessibility of lavatories, particularly on single-aisle aircraft, as evidenced by a Notice of Proposed Rulemaking (NPRM) published by the U.S. Transportation Department in January, calling for improvements.
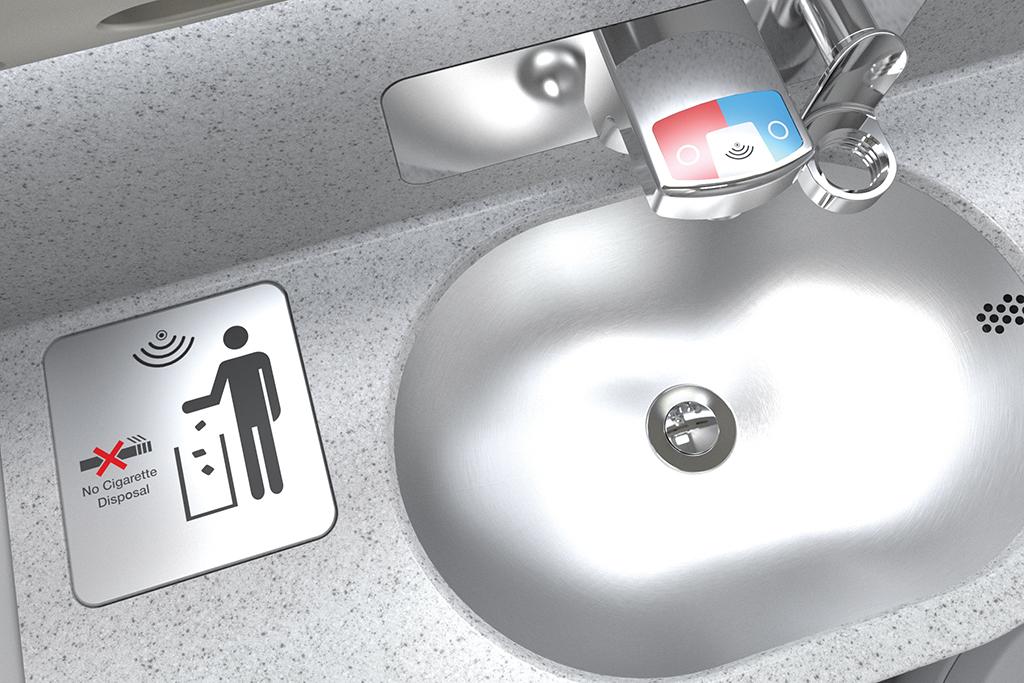
At the same time, there are concerns about maintaining a hygienically clean lavatory throughout the flight. This could be improved by new materials technology and touchless features, which are both major design trends in aircraft lavatories, says Jefferey McKee, Collins Aerospace director for passenger experience and industrial design.
“The materials used in the lavatory are being developed to reduce viruses and bacteria living on surfaces,” McKee explains. “In the design, we have to consider how to support those efforts—mainly through more thorough cleaning practices, easier access to exposed surfaces and minimal material breaks in hidden areas where viruses are likely to hide.”
Trevor Skelly, structures and integration general manager at Collins Aerospace, points out that the OEM is partnering with airlines and representatives of the flying public to incorporate those design technologies into solutions for both forward fit and retrofit. “The coronavirus pandemic has made this especially urgent, since the airlines want to restore public confidence in flying,” he says. “Expect to see more such solutions come out within the next two months, with applications to both narrowbody and widebody aircraft.”
At Diehl Aviation, lavatory designs will concentrate on touchless components, including the toilet seat and lid, waste flap, door lock, water faucets, liquid dispensers and flushing mechanism, according to Helge Sachs, the Laupheim, Germany-based company’s senior vice president of product innovation. “Industry efforts are focused on making lavatories more hygienic,” he says. “In the short-to-midterm, self-cleaning lavatories using UV-C light disinfection and fogging, as well as a smart mirror with instructions on how to use touchless functions will be available,” he says.
Sachs thinks there also will be more antimicrobial surface coatings and sensors enabling crews to monitor consumption levels for items such as paper towels and soap.
Diehl Aviation is developing a “smart lavatory,” which will incorporate all of the company’s enhanced hygienic features as well as embedded predictive health monitoring and management (PHM) capability, Sachs says. This has been promoted as part of Intelligent and Smart Cabin (i+sCabin), an international program defining standards for connected cabin features. Diehl Aviation is that program’s consortium leader.
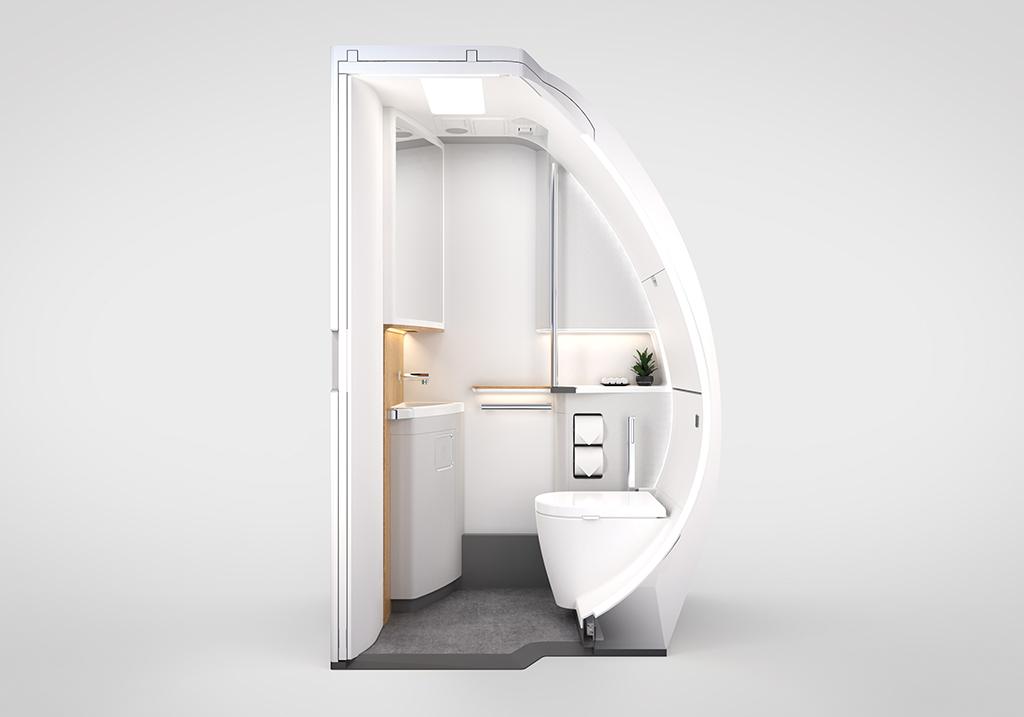
Boeing continues to evaluate its own prototype self-disinfecting lavatory, which was tested for the first time on its company-owned ecoDemonstrator Boeing 777-200ER in the fall of 2019. The lavatory uses ultraviolet light to eliminate at least 99.9% of germs after every passenger use, says Dan Freeman, director for payloads and customer engineering at Boeing Commercial Airplanes. Boeing also has tested ultraviolet light that sanitizes water flowing into the sink.
The prototype lavatory incorporates a hands-free faucet, soap dispenser, trash flap, toilet lid and seat and a hand dryer to reduce the waste of paper towels. “Further technology development and market interest will determine whether the self-disinfecting lavatory might be available on commercial airplanes in the future,” says Freeman.
Maintainability is Key
The COVID-19 pandemic has spawned a renewed focus on making hygiene much more visible and intuitive. “We have partnered with Safran Passenger Solutions to offer touchless activation of faucets, waste flaps, flush switches and toilet lids, which are available on our Airbus A350 lavatories,” says Nathan Kwok, vice president of marketing for Safran Cabin in Alkmaar, the Netherlands.
Safran Cabin is preparing a full suite of touchless products to upgrade existing lavatories. The products have been adapted from the proven technology incorporated in the A350 lavatory, with availability for twin- and single-aisle aircraft retrofit in 2021.
The supplier is also researching a variety of sanitization technologies such as ultraviolet light, antimicrobial surfaces and air ionization, Kwok says. Sensors can be included to alert the crew when service is needed, too, such as when the trash compartment is filling up.
“We are working with our [airliner] OEM and airline customers to understand what kinds of smart technologies they would find most useful,” says Kwok. “The goal is a lavatory that looks and feels clean and actively fights germs.”
As for maintainability, that research is being focused on improving the durability of moving parts, shrouds and other areas of heavy usage. “We expect even more intense cleaning in the future, with harsher chemicals and potentially UV light,” he remarks. “So a focus of our research is on various finishes that stay looking new over time.”
Until recently, the newest lavatory technology—such as touchless appliances—was only available on widebody aircraft, but that is changing. “Narrowbody aircraft are flying longer routes, and as a result, more passengers are using them,” states Kwok. “This means we have to raise the standard for robustness and accommodate a wider range of needs.”
Wheelchair Access
Along that line, a more recent innovation in lavatory technology was introduced by London-based Acumen Design Associates. Appropriately branded Access, it is the world’s first expanding PRM lavatory, according to Daniel Clucas, Acumen’s senior designer. The product was developed as a joint collaboration with ST Engineering in Singapore, which will build and market it to airlines. “We worked closely throughout the design process to conceptualize and refine the concept,” says Clucas.
Access is targeting the narrowbody market—specifically the Boeing 737 and Airbus A320—which Clucas says has been largely neglected. “With more long-haul routes being flown by narrowbody aircraft, the need for true PRM accessibility is paramount,” he explains. “For narrowbody aircraft, we determined that the current lavatory options are either so small that the passenger cannot even fit inside while still on the onboard wheelchair or so large that they take up valuable cabin space.”
Space limitations also favored the narrowbody market. “Cabin floor space is at a higher premium than [for] widebodies. In order to offer a large PRM space, you can’t just re-pitch some seats to create the space you need, so we had to offer a fully accessible PRM lavatory that has the same footprint of a standard one,” Clucas says.
The lavatory is designed for installation in the 737 or A320 D or E cabin location, which is just forward of the aft doors. If a reduced-mobility passenger needs to use the lavatory, the crew unlatches and pulls the aft wall out, into the door area, increasing the enclosed interior volume by 40%. “The expansion creates an L-shaped interior floorplan, which is perfect to allow a pivot transfer from the onboard wheelchair to the toilet,” says Clucas. “With the aft wall returned to the stowed position, the lavatory has the same footprint as a standard system,” he notes.