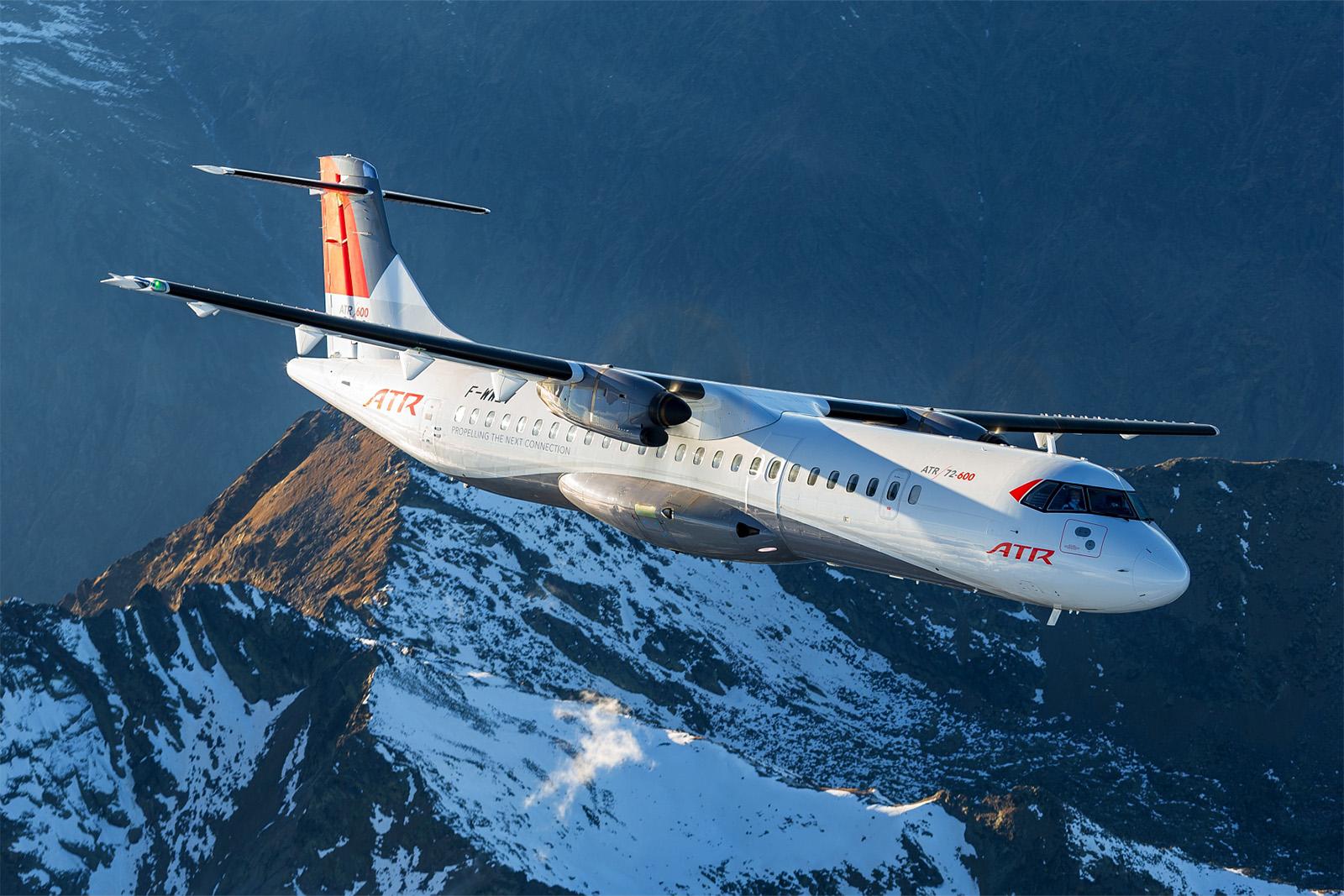
TOULOUSE—After the Pratt & Whitney Canada PW127 XT engine resulted in a major extension of maintenance intervals in 2022, ATR has received approval for a comparable improvement on the nose landing gear, and engineers are working on alleviating the servicing needs of more subsystems.
The effort aims to address pain points customers have described for a long time. The aircraft manufacturer aims to increase customer satisfaction, as delivery lead times tend to curb regional carriers’ appetite for new ATR aircraft. Production delays have negatively affected the orderbook in an already small market.
“Our customers say, ‘we have been telling you for 10 years there was a problem, and you have been doing nothing,’” ATR CEO Nathalie Tarnaud Laude said Feb. 12 during the airframer’s annual press conference. ATR is beginning a 2-3-year journey where it will be investing $10-20 million to solve maintenance issues, she explained. It is making sure the 50-seat ATR 42 and 70-seat ATR 72 turboprops remain competitive, she stressed.
The improved nose landing gear (iNLG) was certified late last year, Daniel Cuchet, senior vice president for engineering said in an interview. The calendar interval for heavy maintenance now stands at 12 years, up from nine years. “That yields a 15-20% reduction in the maintenance costs of a major subsystem,” Cuchet said. “We worked on materials and production techniques, and made more calculations to justify [that] the iNLG can withstand more cycles.”
Corrosion has been another focus. “We are collecting data from 30 customers who have their own maintenance workshop,” Cuchet said. “Then we will decide how to better prevent corrosion—switching to another kind of aluminum, another metal such as titanium or composites, or modifying a component’s shape.” For instance, rain may worm its way into the airframe from an open passenger door and should be better drained, he noted.
ATR engineers are also looking at increasing the existing two-year calendar maintenance interval to three years. This may involve part redesigns, new fatigue modeling and new procedures, such as additional but quick inspections. “This is laborious but fruitful work,” Cuchet said.
Last year, customer support and services accounted for 40% of ATR’s revenues—$480 million, a 15% increase over 2023.