
Integrated circuits made of GE’s silicon-carbine wafers can support powerful electronics even at extreme temperatures.
A state-of-the-art ramjet struggles to accelerate when activated below approximately Mach 3.5. The insides of a supersonic turbofan start melting at speeds above Mach 2.5. To invent a reusable, air-breathing propulsion system for a hypersonic vehicle, technologists must find a solution to the yawning gap between the top speed of a turbofan and the minimum speed of a ramjet.
As both a latecomer to the current hypersonic propulsion race and a decades-old veteran of high-Mach research, General Electric thinks it has discovered the missing piece: a rotating detonation combustor.
By harnessing the powerful energy release that comes from fuel detonation, the company that built the Mach 3 engines to power the North American XB-70 Valkyrie bomber and the canceled Boeing 2707 airliner half a century ago thinks it can lower the Mach number for the cutover speed between a turbofan and a ramjet low enough to make a full-scale, turbine-based combined-cycle (TBCC) propulsion system feasible at speeds faster than Mach 6.
- Rotating detonation to be paired with dual-mode ramjet
- A high-Mach turbofan in the F110 power class is also in development
A Nov. 16 subscale demonstration at the GE Global Research Center here indicates this unique approach—-specifically, a TBCC system composed of a high-Mach variant of a Mach 2.5-class turbofan paired with a rotating detonation-dual-mode ramjet (RD-DMRJ)—can work, executives said during a media event to unveil the tests results and overall concept on Dec. 13.
“This is a huge accomplishment for us. It validates one of the critical technologies that is fundamental to differentiating us in this space,” said Mark Rettig, GE Aerospace’s vice president and general manager for business and technology development at the Edison Works experimental unit.
The laboratory rig test—held 18 months after GE secretly launched the internally funded program—showed sustained rotating detonations of a highly compressed fuel-air mixture even when exposed to a supersonic airflow necessary for flight speeds above Mach 5, Rettig said.
The next step is to demonstrate a full-scale DMRJ in a ground laboratory. A new dual mode sized for an F110-thrust-level TBCC architecture is almost ready for testing. A team of researchers at GE Aerospace’s Edison Works unit and GE’s recently acquired hypersonic propulsion company Innoveering designed the engine, joining an elite club of DMRJ producers in the defense industry alongside Northrop Grumman and L3Harris Technologies-owned Aerojet Rocketdyne.
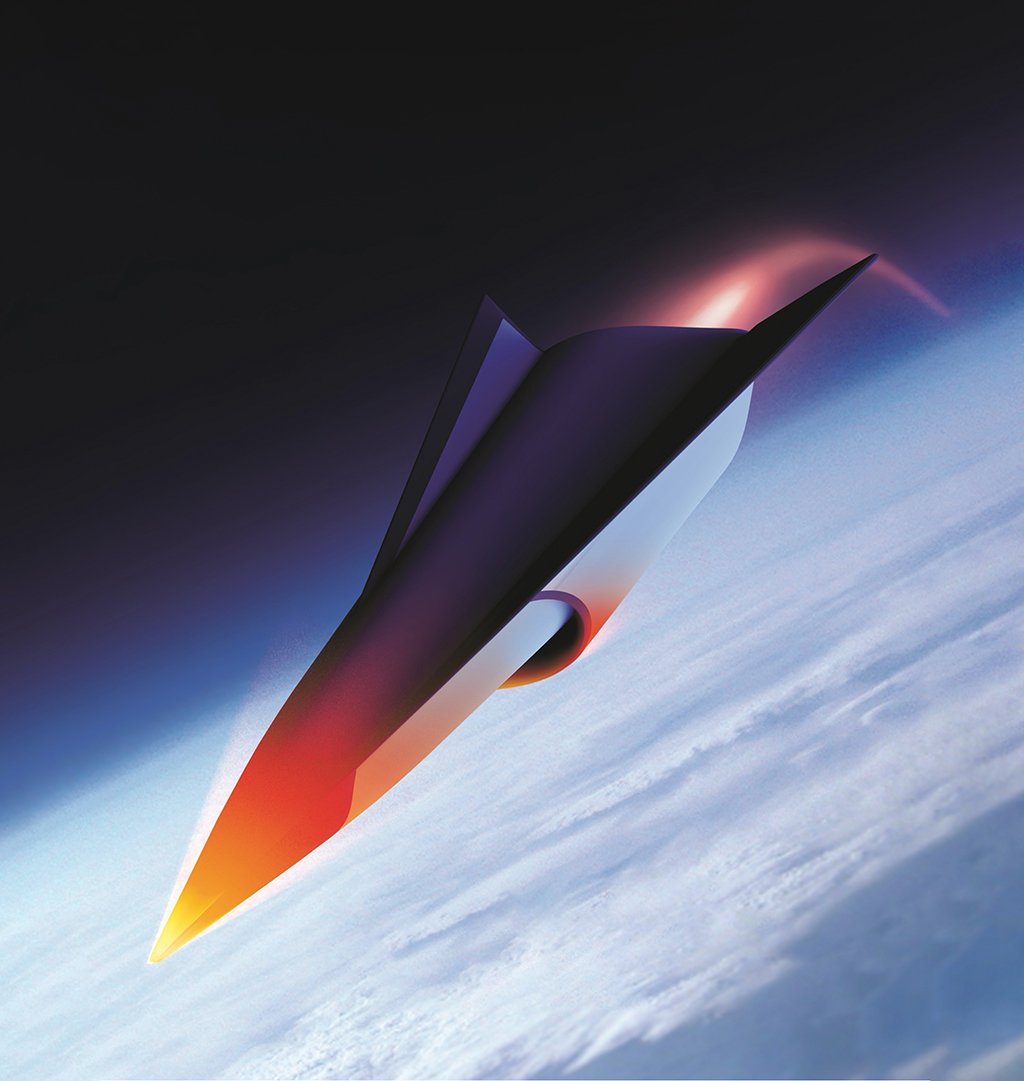
“When we integrate [a rotating detonation combustor and a DMRJ], we find out that the limitations that exist today with regard to transition or takeover Mach numbers can be improved greatly, and we find out that the length associated with a standard deflagration combustor is greatly reduced,” said Craig Young, GE Aerospace’s director for engineering and hypersonic propulsion.
GE’s DMRJ is scheduled to enter testing in the third quarter of 2024, but trials could begin months sooner, with the team running ahead of schedule, Rettig said.
The DMRJ is slated to be integrated with a full-scale rotation detonation combustor for another ground rig test by the end of 2024 or early 2025, Rettig added. Finally, a the RD-DMRJ is planned to be combined with a high-Mach turbine engine for a ground rig test of a hypersonic TBCC system by the end of 2025.
The full TBCC system is designed to deliver a new kind of hypersonic capability. The cruise missile demonstrators—DARPA’s Hypersonic Air-Breathing Weapon Concept or the U.S. Air Force’s Hypersonic Attack Cruise Missile, for example—are sized in roughly the same category as the Lockheed Martin AGM-158 Joint Air-to-Surface Standoff Missile, which requires less than 700 lb. of thrust from the propulsion system.
By contrast, an F110-class, high-Mach turbofan in GE’s project could produce more than 17,000 lb. of thrust without an afterburner, which requires a DMRJ in the same size range. The most powerful scramjet demonstrated on the ground to date—an Aerojet Rocketdyne design funded by the Air Force Research Laboratory (AFRL)—achieved 13,000 lb. of thrust in a test announced in September 2019. An aircraft in that size category can serve a wide range of applications, including surveillance, bombing, transport and space launch missions.
The goal of fielding a high-thrust, air-breathing hypersonic engine propelled several startups into existence before GE entered the race. Atlanta-based Hermeus, for example, plans to integrate a similar-size Pratt & Whitney F100 turbo-fan with a self-designed ramjet to power the hypersonic Darkhorse for testing scheduled in 2025. Hermeus already demonstrated a turbojet-to-ramjet transition in September 2022 with the Chimera engine, which includes a precooler to chill and energize the airflow before it enters the ramjet.
Hermeus established an early lead in the hypersonic propulsion race with its founding in 2018. GE secretly decided to launch its TBCC project in May 2022, or only four months before Hermeus achieved the turbojet-to-ramjet transition milestone, albeit using a subscale J85 jet engine.
But GE thinks it can catch up and surpass new entrants. Although a late entrant in modern TBCC development, its research in high-speed flight goes back decades. Following development of the YJ93-GE-3 turbojets for the Mach 3-capable XB-70 Valkyrie, the company tested a scramjet engine for the AFRL in the late 1960s.
The first element of GE’s research in TBCC systems began emerging in the early 2000s. The NASA-funded Revolutionary Turbine Accelerator tested components of a Mach 4-plus turboramjet propulsion system.
Meanwhile, GE’s research staff turned their attention to pressure gain propulsion for high-speed flight, starting with pulsed detonation engine (PDE) technology. A PDE yields a high-energy release similar to that of a rotating detonation engine (RDE) but is mechanically more complex because a series of valves must open and close to purge the combustion chambers after each pulse. In comparison, an RDE is mechanically simpler, but the challenge is sequencing fuel ignition correctly to sustain fuel detonation in rotating waves around an annual combustor.
Since 2015, the GE research team has been focusing on maturing RDE technology, with support from the AFRL’s Advanced Turbine Technologies for Affordable Mission-Capability program. In a test chamber here, GE built a copy of an AFRL-designed RDE and test rig, allowing the company to build on the government laboratory’s results.
By 2022, GE had spent two decades on building blocks for a hypersonic TBCC, including a high-Mach turbine engine design and a rotating detonation combustor. A missing piece in GE’s portfolio, however, was a DMRJ system. Such an engine is capable of extracting thrust by igniting a fuel-air mixture through the combustor in either subsonic or supersonic airflows. The latter is necessary at speeds generally higher than Mach 5, as the heat and drag of a subsonic flow become too intense to sustain acceleration. Then in late 2022, GE acquired Innoveering, a startup founded by former directors of the General Applied Science Laboratory, a pioneer of hypersonic research since the early 1960s and owned since 2018 by Northrop Grumman.
The acquisition of Innoveering gave GE all three pieces of the company’s preferred TBCC system: a high-Mach turbofan and state-of-the-art DMRJ with a novel rotation detonation combustor. In this concept, a common air intake supplies airflow to a turbofan from takeoff to a speed somewhere above Mach 2.5. Then the turbofan is cocooned, and airflow is diverted to the DMRJ, with the rotating detonation combustor used to overcome the lower energy release from a conventional combustion process at speeds well below Mach 3.5.
In addition to propulsion research activity, GE’s hypersonic project can benefit from decades of internal research and production of high-temperature materials and electronics. During a facility tour on Dec. 13, GE demonstrated the silicon-carbide ceramic matrix composites in mass production for its commercial turbofan engines and the silicon-carbide wafers used to make integrated circuits for guidance systems and other electronics.
What remains unclear is the government’s interest in a large, reusable hypersonic vehicle. No unclassified programs of record have been announced within the six-year planning window annually published by the Defense Department. The AFRL, however, has released plans to develop a reusable hypersonic testbed powered by an air-breathing propulsion system. The Mayhem program would be a “good fit” for the DMRJ module of GE’s hybrid TBCC configuration, Rettig said.