
Virgin Orbit had barely tweeted news of the successful Jan. 17 space debut of its LauncherOne vehicle on social media when new launch contracts began arriving in the company’s email inbox.
A testament to the pent-up market demand for small-satellite launch capability, the speedy reaction to the long-awaited demonstration of the new space-access vehicle paves the way for multiple follow-on Virgin Orbit missions by year-end and a potential doubling of the rate in 2022.
- First successful privately developed air-launched, liquid-fueled rocket
- Payloads deployed for NASA’s Venture Class Launch Services program
The glitch-free flight of LauncherOne on its second demonstration test was a critical and much-welcomed milestone for the Long Beach, California-based company. Coming almost nine years after the air-launch concept was first unveiled by Virgin founder Richard Branson, and six years after the start of full-scale development, the flight followed last May’s first demonstration mission, which ended abruptly when the rocket motor shut off after just 4 sec.
After an exhaustive analysis and modifications to beef up the oxidizer feed line at the heart of the first flight failure, the path to the Launch Demo 2 test was then delayed until January 2021 by the COVID-19 pandemic. With the LauncherOne system now proven, design changes verified and the first 10 small satellites placed in orbit, Virgin Orbit is already focusing on the next steps to ramp up its production and launch-cadence capabilities.
“There are around a dozen launches on the firm manifest, and we are essentially sold out for this year,” says William Pomerantz, vice president for special projects at Virgin Orbit. “We always try and hold back a couple of spots for people who really need to go in a hurry, but other than those we are sold out for this year and getting there pretty fast for 2022.”
Additional launches are being firmed up in the wake of the Jan. 17 demonstration, which was a confidence booster to the market, says Pomerantz. “There were a lot of people saying, ‘I’m excited about your vehicle’ the moment [we] reached orbit. Within minutes of us tweeting we had reached orbit, there were signing contracts showing up in our inbox. So we’re fitting all that into the manifest, and that was as expected. I think that’s how it goes when you’re bringing a new launch vehicle online,” he says. As for the identity of the new customers: “stay tuned,” adds Pomerantz.
Although Virgin Orbit has yet to detail which payloads will be carried on subsequent flights, the company says the next launch—like the first—will be based out of Mojave Air & Space Port in California. “That’s just months away hopefully. Then we start looking at places like Guam,” says Pomerantz. “That will be a little later on, but not too much later on, in the manifest.”
The Guam launch, from Andersen AFB, will be for the U.S. Defense Department, while launches from elsewhere will cater to other government customers, including the UK’s Royal Air Force. Commercial customers include Swarm Technologies, Sitael of Italy and Denmark’s GomSpace. Additional launches will take place from a wide range of sites, including Japan and the UK.
Designed to carry up to 661 lb. to polar orbit, LauncherOne can also deliver up to 1,100 lb. of payload to a low-altitude equatorial orbit. For the Launch Demo 2 mission, however, LauncherOne’s payload weighed around 253 lb., says Virgin Orbit, which has become the second privately funded company after U.S.- and New Zealand-based Rocket Lab to successfully deploy a dedicated smallsat launch capability.
Produced as part of a $4.7 million 2015 NASA contract under the agency’s Venture Class Launch Services program, the research satellites lofted on Launch Demo 2 are designed for a wide variety of projects, ranging from tracking space debris to space weather. The satellites were “parked in exactly the right orbit—within a small portion of a degree of inclination and a kilometer or two of apogee, and really that’s just the spacing out between the different satellites,” says Pomerantz. “It was right on the money.”
The orbital test mission began with the release of the two-stage LauncherOne from Cosmic Girl, the company’s converted Boeing 747-400 carrier aircraft, at an altitude of 35,000 ft. as it flew past the California Pacific coastal island of San Nicolas. The 747, which was flown to the launch zone from Virgin Orbit’s Mojave facility by Chief Test Pilot Kelly Latimer and co-pilot Todd Ericson, dropped the rocket while executing a special zoom climb maneuver.
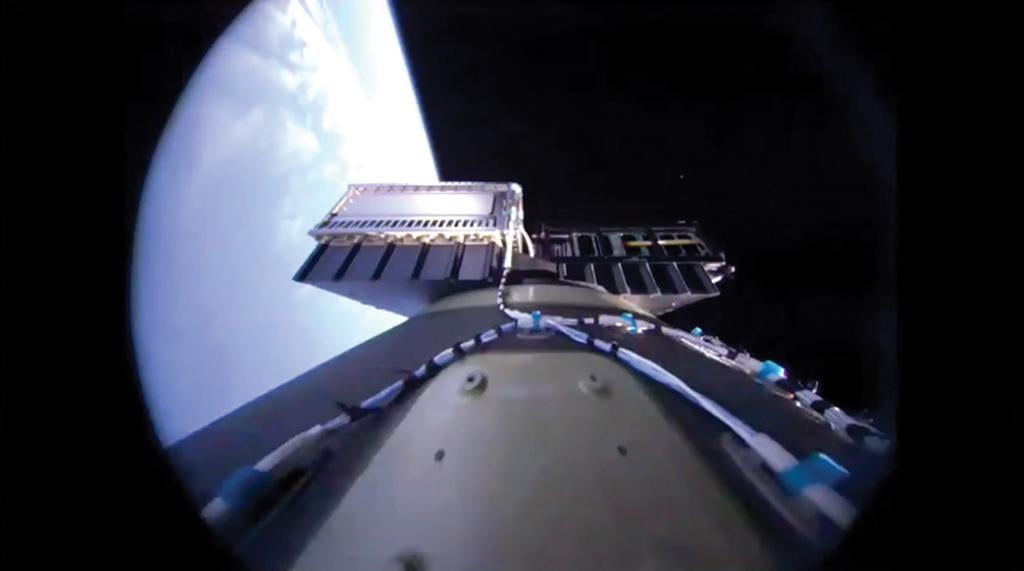
Having entered a racetrack pattern prior to launch, the crew approached the drop zone on a southeasterly heading at 30,000 ft. and Mach 0.7. In the runup to the zoom climb maneuver, the crew accelerated the 747 to Mach 0.85 before stabilizing at that speed for a 2g pull-up and climb. With the aircraft pitch attitude at 32.5 deg. and flightpath angle at 29 deg., the rocket was released as the 747 passed 35,000 ft. and the speed bled off to Mach 0.67. Vehicle deployment occurred just 8.9 sec. after the planned “D-minus” drop time set from the takeoff from Mojave some 58 min. earlier, says Latimer.
With the 747 relieved of the 57,000-lb. weight of LauncherOne from beneath its left inboard wing, the crew easily rolled the aircraft to starboard to maximize the distance from the rocket. “We aimed for a bank angle of around 45 deg. and no more than 60 deg.,” says Latimer, who adds that the aircraft’s speed reduced to just 180 KIAS at the top of the climb before the nose was lowered.
After release, LauncherOne’s Newton 3 (N3) first-stage liquid oxygen/RP-1 rocket ignition sequence began on cue at 3.25 sec., and the main engine started just 2 sec. later. “We could see and hear it when that motor got going,” she adds. The N3 accelerated the vehicle to around 8,000 mph after a burn lasting just under 3 min. The first-stage burn represented the first time the 73,500-lb. vacuum-equivalent-thrust booster had completed a full-endurance run in flight.
Following main-engine cutoff and successful stage separation at 3 min. 2 sec. into the rocket flight, the smaller Newton 4 (N4) upper stage ignited to continue accelerating the test payload into a polar orbit at around 17,500 mph. Fairing separation occurred 25 sec. after ignition of the 5,000-lb.-thrust engine, which ran for its allotted initial run of just under 6 min.

Seven seconds after engine shutdown, the second stage then performed a “BBQ” roll maneuver in which it rotated around its axis for thermal balancing of the payload. Just past 46 min. after shutting down, the N4 was relit to circularize the orbit. The second burn, lasting just under 5 sec., was followed by the final shutdown and payload deployment, which occurred about 56 min. after rocket release.
Although initial data indicated that the relight and payload separation commands had been issued as planned, Virgin Orbit delayed confirmation until additional information was received from a ground tracking station in Mauritius in the Indian Ocean. The system that decoded the telemetry data “crashed, and we had to reboot, and then start it again,” Pomerantz says. “Although we had immediate data that was strongly suggestive that we had deployed all of them, we didn’t want to get it wrong.”
Payload deployment capped off a flawless flight, says Pomerantz. “Everybody is pretty much still walking on sunshine. I cannot believe how smoothly that day went because it was only our second time doing this.”
As well as marking the first full flight duration burn of the N3 and vacuum burn of an N4, the mission was also the first time the horizontally launched vehicle had flown through Max Q (maximum dynamic pressure) as well as demonstrating first-stage separation, fairing deployment and N4 ignition.
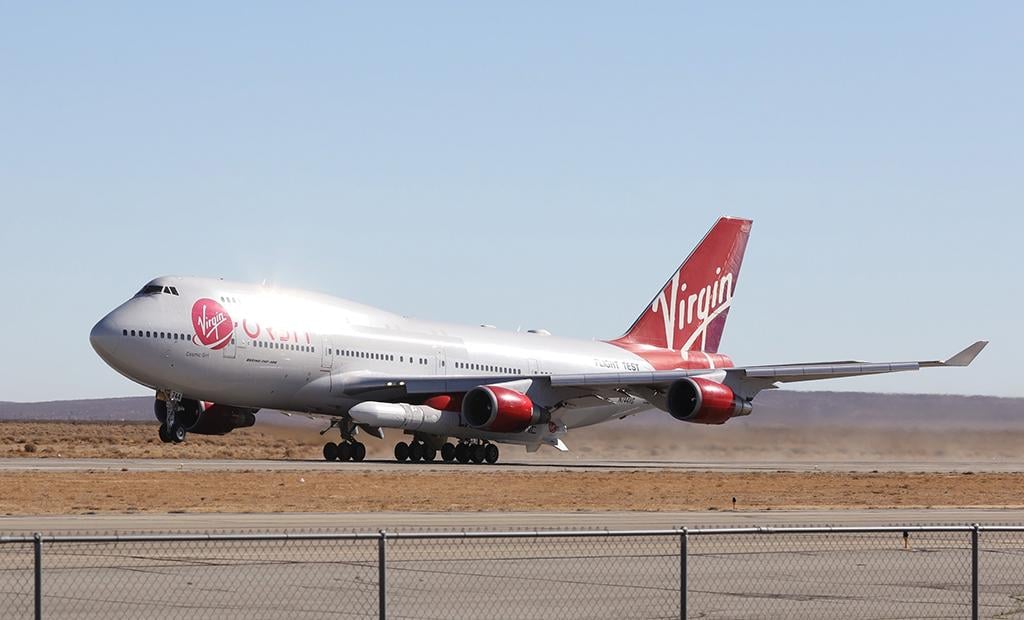
Although the company is conducting a full data review of the mission, the key lessons learned are “mainly going to have to do with questions about whether we were a little too conservative about this or [built] in more margin than we needed about that,” says Pomerantz. “But at the heart of it, the hardware all seems to have done exactly as it was meant to do both on the aircraft and on both stages of the rocket.”
In readiness for the start of operational launches, Virgin Orbit has meanwhile been adding extra production capacity as it closes in on completing work on the next vehicle, dubbed Rocket 4. “We have a full factory with several rockets in production right now. We are preparing for a full ramp-up and a steady launch cadence,” says CEO Dan Hart, who adds that work on the next vehicle is a “few weeks away from being ready.”
Key to the expansion is the addition of a new hybrid additive and subtractive manufacturing machine developed in partnership with DMG-Mori. Based on a pioneering machine called the Lasertec 4300, which has been used by Virgin Orbit to print large parts up to 3 X 3.5 ft., the newest Lasertec 6600 version has just been installed at Long Beach. “It’s four times as big,” says Pomerantz. “They designed it around our feedback on the 4300, because we were the first one to get that and we had this really tight working relationship with them.” As rates increase, largely due to advanced manufacturing processes, Virgin Orbit hopes to eventually manufacture as many as 24 rockets per year.
Comments