Targeting MRO Skills Gap, PSA Airlines Innovates Training Strategies
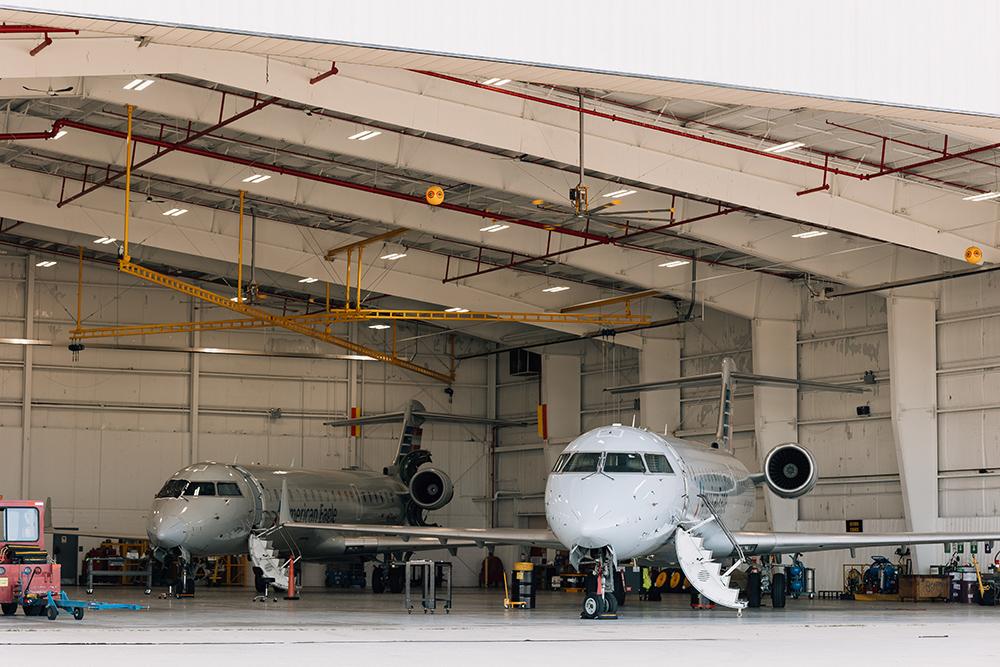
As the MRO workforce faces a growing skills gap due to retirements and increased recruiting of graduates straight out of airframe and powerplant (A&P) schools, regional carrier PSA Airlines is attacking the problem from several angles. In addition to totally revamping its training strategy for new recruits, the airline, an American Airlines subsidiary, is developing and deploying several new technology innovations to improve learning for new maintenance technicians.
“Our experience as a regional carrier allows us to evaluate a lot of new hires directly out of A&P schools, and the discrepancy between the skills of those new technicians and those required in the fast-evolving aviation maintenance sector has reared its head in a couple of different ways,” said James Ellis, PSA’s assistant director of maintenance training, during the recent Aviation Technician Education Council annual conference.
Ellis reported that new technicians were often not only lacking in skills related to advanced avionics, composite materials and digital troubleshooting skills, but also in soft skills such as effective communication, teamwork and adaptability. “These skill gaps are ultimately not just about operational efficiencies, but safety as well,” he added, noting that they could also contribute to inefficiencies that increase maintenance and operational costs, reduced workforce satisfaction and higher turnover rates.
To ease new technicians more successfully into the workforce as they learn to work on PSA’s aircraft, the airline recently switched to a progressive training model. Instead of immediately throwing technicians into general familiarization (gen fam) training courses, new hires first spend at least one month learning on the shop floor so they have a practical understanding of the aircraft, components and concepts they will be encountering in these courses. Following gen fam training, trainees start to learn skills and concepts in order of importance to make them as productive as possible on the shop floor. For instance, the airline prioritizes subjects based on where it typically sees the most technical issues, such as pneumatic bleed leaks or door pressurization problems.
“I’m only investing in that student as much as they need to be proficient at that given point. I’m not giving them more information than they need to know—I’m giving them just as much information as they need to be productive and efficient at that particular point in time,” said Ellis.
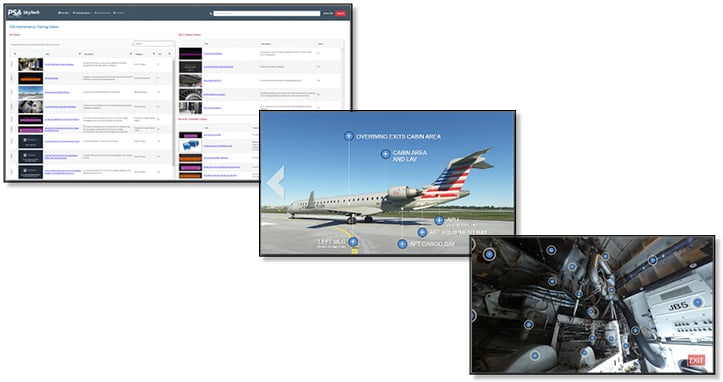
To improve new technicians’ retention of information, PSA recently implemented a video training platform called SkyTech, which is similar to an internal YouTube channel featuring videos that cover common maintenance issues. It has produced more than 100 videos since last summer and Ellis said the tool has seen “tremendous success” with tech-savvy younger workers. However, he stressed that SkyTech is not intended to replace technical data, but rather to be used as a reference tool.
PSA has also developed a Virtual 360 Aircraft tool, which provides users with a complete 360-deg. view of specific areas of an aircraft. Users can navigate around an aircraft using controls similar to those featured in Google Maps and hover over particular areas to see information about components. The airline plans to tie this functionality to SkyTech via hyperlinks so users can click on an area and watch a related video.
Since implementing the progressive training model and new digital tools, Ellis said PSA has seen post-training employment attrition rates drop by more than 20% year-over-year. He added that participant feedback has been “overwhelmingly positive,” with nearly 100% of trainees reporting that they would recommend the training track to their peers.
Moving forward, PSA plans to develop even more training technologies. It is looking at implementing a tablet-based augmented reality system to walk trainees through steps of specific maintenance tasks.