
Supply chain delays are putting pressure on the aircraft painting market.
Aircraft ownership transitions and longer life spans have led to high demand for aircraft painting services, but tight capacity, workforce shortages and supply chain delays are challenging the market. Amid this landscape, aircraft painting specialists are navigating new technologies that could help with workforce and sustainability concerns.
According to Nealson Kretly, senior account manager at International Aerospace Coatings (IAC), paint demand came booming back after the COVID-19 pandemic as airlines returned their fleets to service. “Everybody was trying to capture the market again. We’ve never seen that many aircraft waiting to be painted at some point on our schedule,” he says.
Post-pandemic, Kretly says IAC had to turn away 250 aircraft from its painting pipeline due to capacity issues. The company is at 100% utilization in the U.S., and its partnership with Boeing to repaint the OEM’s 787s and 737 MAXs has increased IAC’s growth requirements. “It puts even more pressure on the system because we now really need to increase our capacity in the U.S. Aircraft painting is the last step before Boeing delivers aircraft, so if there’s a bottleneck in that process, this could create a massive impact on their supply chain,” he says.
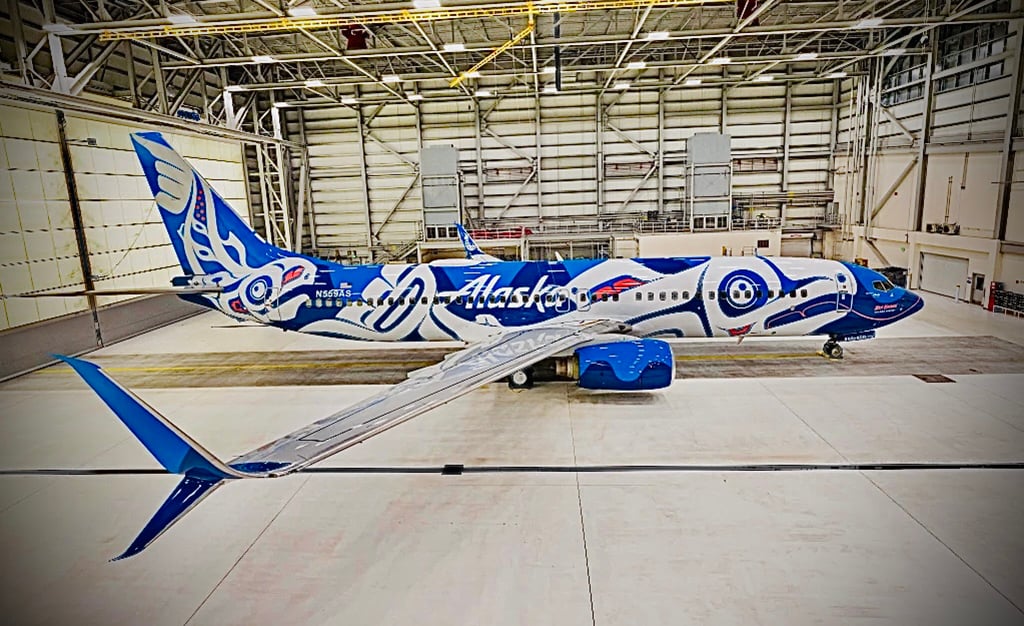
Kretly adds that real estate in the U.S. “has gone completely nuts” post-COVID, which has complicated efforts to add new paint hangars. “Before, maybe you could make a business case to build a new hangar and make it exactly how you want it,” he says. “Now, it’s challenging to make the business case, so you might have to look into something that’s older and retrofit it to your needs.”
Across the Atlantic, several aircraft painting companies in Europe have recently opened new paint facilities. For instance, UK-based Airbourne Colours just opened a new paint facility at Teesside Airport in October, which Sales and Marketing Director Simon Cracknell says was aimed at trying “to counteract the growth in the marketplace” in response to “lack of available space.”
Cracknell notes that as airlines retain aircraft longer due to engine problems on new-generation aircraft, paint refreshes are in demand. For instance, he cites Airbourne Colours’ customer Jet2, which has decided against retiring its Boeing 737 Classic aircraft for the time being as it renews its fleet with newer Airbus models. Airbourne Colours recently repainted one of these older 737 Classics for Jet2 at East Midlands Airport.
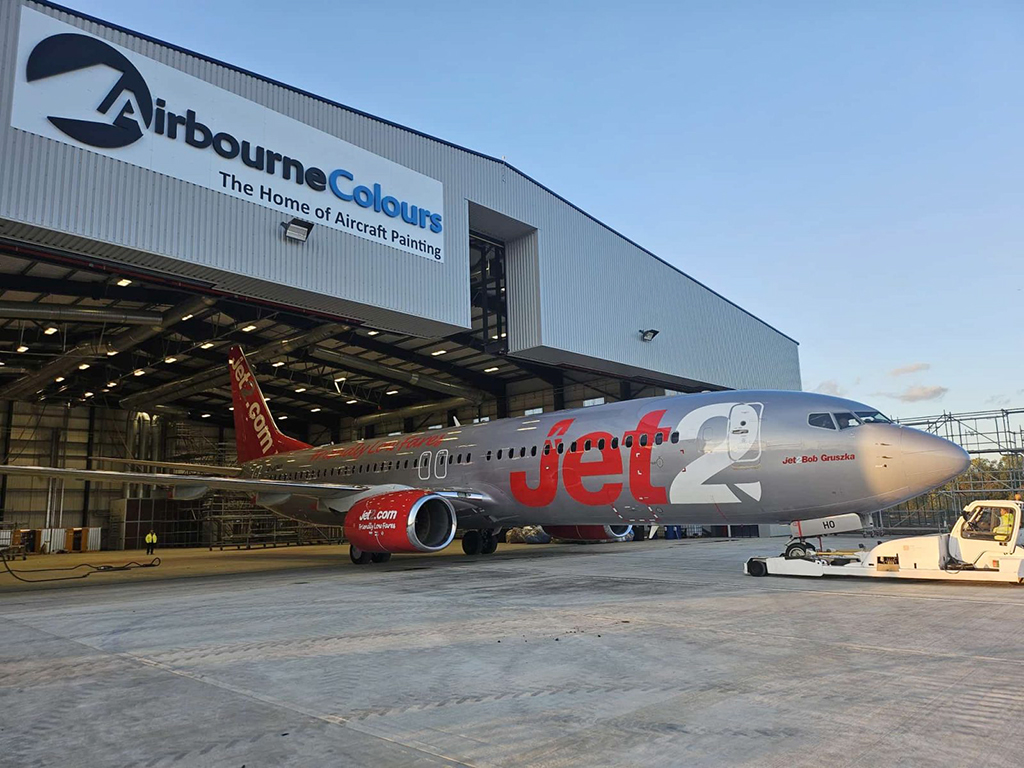
MAAS Aviation, which operates paint shops in Europe and the U.S., recently opened two new facilities in Mobile, Alabama, for Airbus. The company is seeing longer intervals between painting on some aircraft due to improvements in paint formulations and fewer aircraft transitions due to extended leases and OEM delays. “I think that will normalize as the OEMs start getting their supply chains organized or improved, but I don’t think it’s a quick fix,” says Chief Commercial Officer Richard Marston.
Cracknell says supply chain issues continue to trickle down throughout the segment. “When you look at the pool of companies that we can go to globally, the predominant three major paint suppliers (AkzoNobel, Mankiewicz and PPG), you’ve got very little choice,” he says. “A lot of the supply chain isn’t local. We are seeing [the supply chain] getting a little bit better compared to where it was maybe two years ago, but it does continue to have some issues.”
Despite supply chain issues causing delays in aircraft painting, business is still booming. While Marston says capacity for painting narrowbodies is stable, he notes that there is an aircraft painting capacity strain for widebodies in Europe.
“Everybody’s crying out for widebody paint hangars, and some of our competitors are opening and commissioning new ones,” he says. “Part of that is the shortening interval of painting for some of the composite aircraft. Because of their nature—expanding and contracting—the paint [intervals] are not as long as some of the narrowbodies, and you have to paint them more often. That’s driving an increased capacity requirement, which is great for painting.”
Rene Lang, executive managing director of aviation at paint manufacturer Mankiewicz, says composite aircraft require primers with good flexible material properties, such as the company’s Alexit FlexPrimer. He says the primer provides the necessary adhesion and flexibility for composite aircraft while preventing cracking and adhesion loss in coatings, even in areas of the aircraft stressed by high levels of vibration, such as engine nacelles.
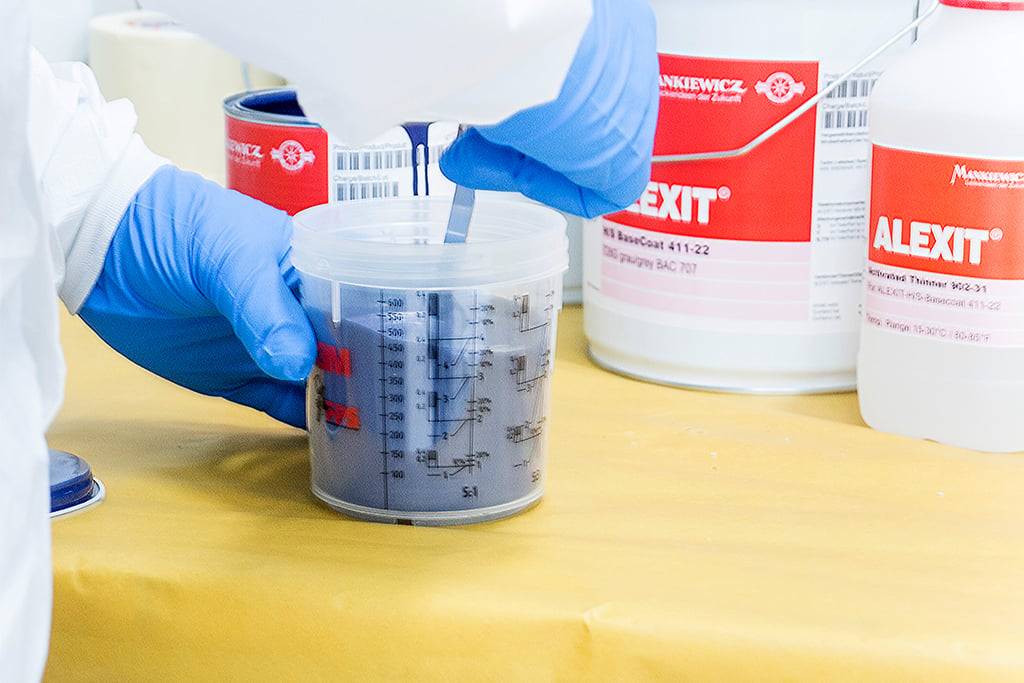
“In addition to flexibility, surface quality is another challenge with composites,” Lang says. “These parts often have more imperfections in their surface structure than other substrates and, therefore, require a suitable pretreatment to ensure that they can be perfectly painted later.”
When it comes to cracking and paint damage, IAC’s Kretly points out that the social media era has increased pressure on airlines to maintain pristine paint. “With access to the internet, people can call airlines out [on social media]. If you have missing paint or damage, people will call out the company online and say, ‘Look at that bad paint job.’ Their aircraft have to be spotless to differentiate themselves,” he says.
SEEKING SUSTAINABILITY
Beyond developing primers better formulated for composite aircraft, paint manufacturers are also developing products aimed at better longevity and sustainability. The aircraft paint segment has introduced base-coat-clear-coat systems as a replacement for single-stage paints, which require multiple layers, adding time to the painting process and weight to the aircraft. According to nearly every source Inside MRO spoke with, base-coat-clear-coat systems provide longer life spans between paint intervals, better UV resistance and better color retention.
Manufacturers are also removing chromates due to environmental and health concerns. “Chromates have excellent corrosion protection and adhesion properties and release self-healing powers when components are mechanically damaged on the surface. However, chromates harm health and the environment during processing and are no longer permitted in many other industries,” says Lang.
“On the MRO side, we are getting to a point where, in many cases, we’re going to have to start reformulating some of our formulas to be more sustainable, with some substances of concern being regulated out in parts of the world, so that’s a big driver for us in product development,” says Sean Purdy, PPG’s global platform director for aerospace coatings and sealants.
While chromates are still used in some structural areas of the aircraft, both Mankiewicz and PPG have been developing chromate-free products with the aim of eventually providing similar alternatives for all parts of the aircraft. For instance, PPG has developed what Purdy says is the world’s first electrocoat primer for the aerospace industry. Called Aerocron, the chrome-free primer uses electrodeposition to fully coat a part “to a very fine thickness, which is extremely controllable and allows for total paint coverage with precision across the part,” he says.
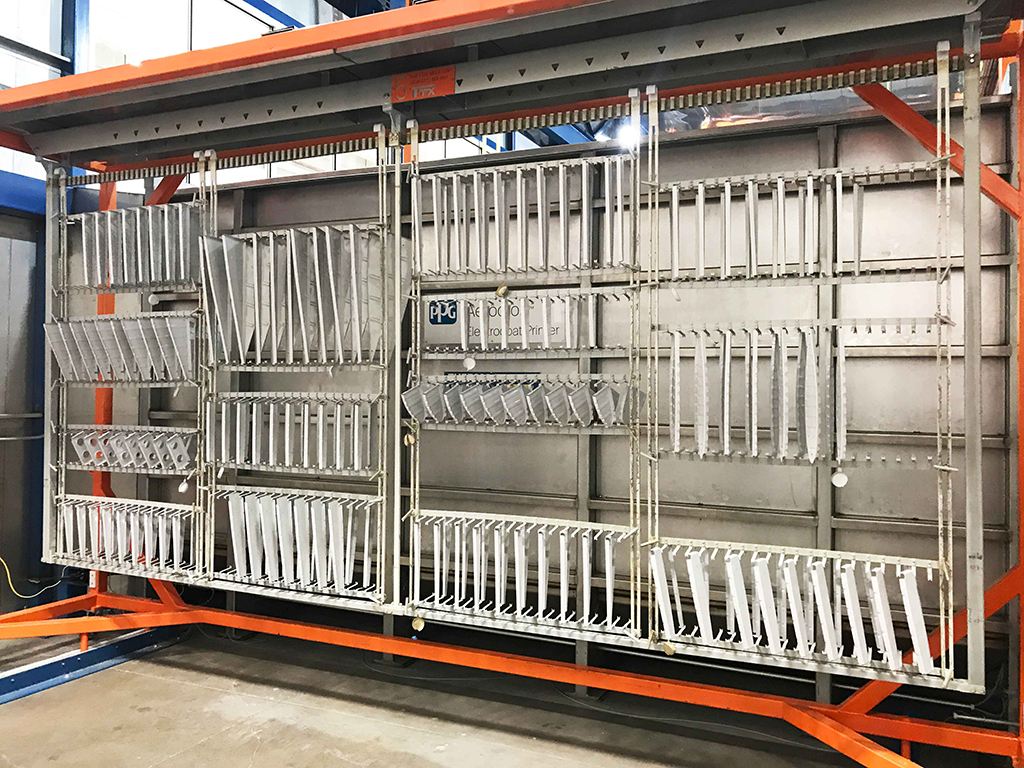
Painting specialists are also seeking sustainability advances within their facilities. For instance, Airbourne Colours’ new Teesside facility is using air recirculation technology to reduce heating costs, and IAC is using electrostatic guns to avoid paint overspray, which reduces paint waste and carbon dioxide emissions.
According to Marston at MAAS Aviation, “there is a world of difference” between sustainability features in modern paint shops compared to 30 years ago. “Now, our facilities are very modern, even down to the 1,000-lux high-powered lighting. Everything is environmentally-, humidity- or temperature-controlled, so regardless of what’s going on outside—whether it’s hot or cold—it’s always stable in the hangar,” he says.
Marston also points to changes within the systems that handle paint waste and liquids. “Our hangars have underground sumps, so when you’re stripping, cleaning and washing the aircraft, nothing goes out on the apron,” he says. “All the waste is collected, and it’s disposed of responsibly. What we try to do is separate wet waste and dry waste. We recycle all the paper. We have a solvent recycling plan for cleaning tools and things.”
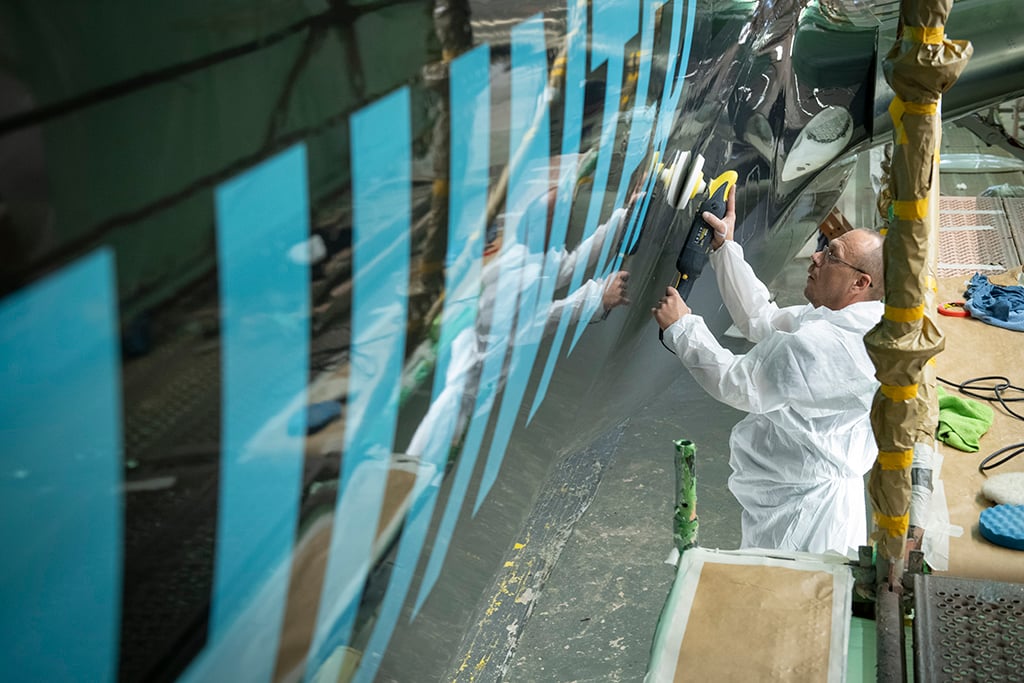
ROBOTICS POTENTIAL
Some stakeholders in the aircraft painting segment are aiming to reduce waste and improve environmental concerns by using robotics.
Dutch startup Xyrec is seeking to commercialize robotic technology to both paint and remove coatings from entire aircraft. The company has been testing its Laser Coating Removal (LCR) robot for several years with an undisclosed aircraft manufacturer to prove that the technology can successfully and safely strip paint and coatings from aircraft. Xyrec also tested its Automated Paint Robot (APR) with Airbus in 2019.
According to Xyrec CEO Peter Boeijink, the LCR can completely remove paint from a Boeing C-17 in approximately 20 hr., and the APR uses digital ink printing to apply maskless aircraft livery designs quickly, in one pass, while automatically measuring the thickness of paint applied. Boeijink expects the LCR to go into production in 2026 and for the APR to go into production by the end of 2026 or the beginning of 2027.
Removing paint and coatings from aircraft is typically a very labor-intensive process that uses a large quantity of chemicals and water, generating a significant amount of chemical waste. As MAAS’ Marston notes, “When we paint an aircraft, out of the seven days that it’s in, you’re painting for 8 hr. or so, depending on the complexity of the livery. The work is in the sanding, the stripping, the cleaning and the constant masking.”
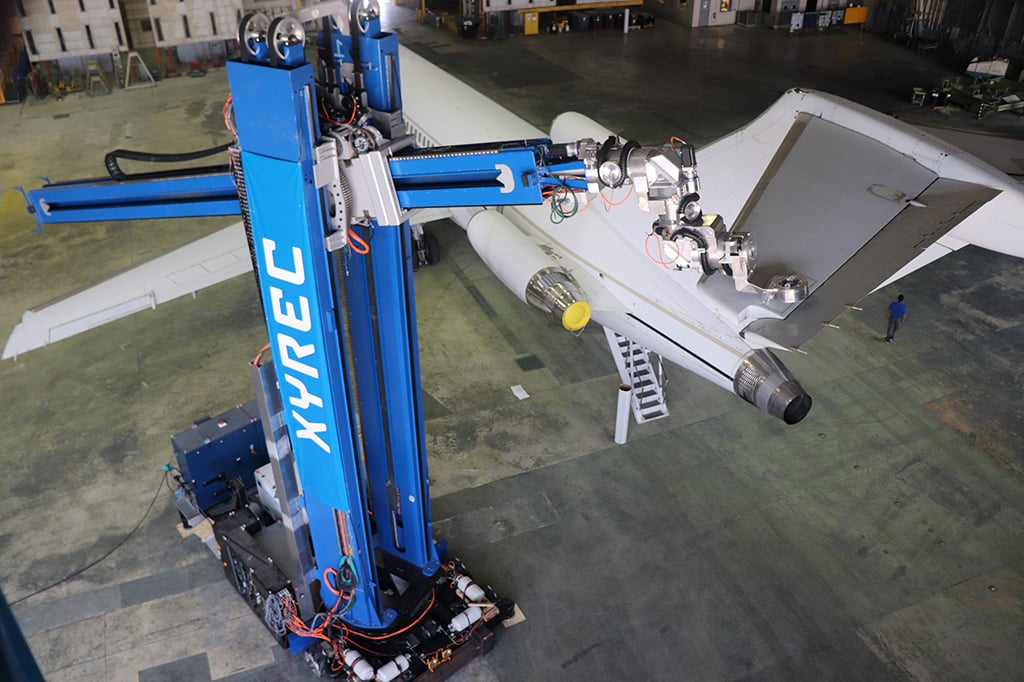
The LCR vacuums paint particles as the laser passes over the aircraft surface, collecting them in a sack for disposal. Boeijink says the system generates approximately 2 lb. of waste in powder form for a widebody aircraft, whereas traditional paint removal methods use approximately 475 gal. of chemicals and 3,700 gal. of water.
Boeijink says the LCR system could provide further sustainability benefits by using electrical power generated by wind turbines or photovoltaic panels. “We have a proposal ready for companies that want to do that, where we construct the whole hangar, including the sustainable energy supply, in a fixed price conclusion and competitive to the current electrical power cost in the U.S.,” he says.
Although some aircraft painting companies see challenges with this technology making it into production environments, they suggest that robotics could provide significant benefits in the segment.
“We’ve been looking at robotics for sanding technology. In the paint process, sanding the aircraft is the longest task and it’s very repetitive and hard,” says IAC’s Kretly. “It’s hard to have a robot that can complete that range of tasks on every platform that comes through [the hangar]. We don’t have one specific bay just for Boeing 737s—we can paint a Boeing 737 and the next day we’ll paint an A320. I think that’s a challenge, but [paint-focused robot manufacturers] have made great progress.”
Marston has similar concerns, noting that he foresees difficulties in a robot navigating an airframe’s contours and rivets.
Kretly also notes that the technology will likely face regulatory hurdles. “We go by the aircraft maintenance manual and structural repair manual guidelines, which are put out by the OEM,” he says. “They say ‘chemically stripped’ or ‘sand the aircraft,’ but they don’t say ‘robotically sand the aircraft,’ so it’s language that they will have to indicate [in those manuals] once this technology is more accepted.”
Boeijink stresses that the OEM’s involvement in the testing of Xyrec’s robotic systems will alleviate most of these types of concerns. He says the aircraft OEM working on testing the system has finished the derisking phase of the project to prove that the technology works, and the regulatory authorities do not need to be involved, “as the conditions are well described, so there’s no question about what to test, how to test and what the outcome of a test is.”
Xyrec is also pursuing a development in which the APR could incorporate drag-reducing sharkskin film directly into paint. While products such as Lufthansa Technik’s AeroShark film have received attention for their ability to reduce drag, fuel and carbon emissions, Boeijink says printing this texture directly into paint could save significant time in application while adding no additional weight.
VR AND AI
Aside from robotics, aircraft painting specialists are considering other technology use cases as well. For instance, PPG is looking at how artificial intelligence could help it achieve color matches faster and Marston says MAAS Aviation has been talking to some of its paint suppliers who are investing in drone-based inspection technology for paint.
Another technology gaining headway in the aircraft painting segment is the use of virtual reality (VR) for paint training. Several paint manufacturers, such as PPG and AkzoNobel, have been offering VR paint training in recent years to help train new painters in a format that eliminates paint waste, reduces costs and improves safety.
IAC has a VR training partnership with AkzoNobel and Kretly says all new hires undergo the training before stepping foot in the hangar. “It’s a great way for us to simulate what a real paint application would look like for new employees so they can have a good perspective of what they need to do and build their confidence prior to entering the real situation in the hangar,” he says.
Marston says MAAS Aviation’s employees undergo progressive levels of VR paint training the longer they stay with the company, and the company has been lucky in retaining staff—particularly considering the industry’s workforce shortages.
“We’re quite lucky in that we have a really robust training program. Painting aircraft is a difficult job. You can’t just do it from your bedroom; you’ve got to be in the hangar,” he says.
Cracknell at Airbourne Colours says a limited pool of qualified aircraft painters and the impact of Brexit have compounded the company’s workforce challenges in the past few years. In response, the company is working with a local college in Teesside to develop long-term training opportunities for aircraft painters.
“As far as aircraft painting is concerned, there aren’t any sort of long-term training courses that are available,” he says. “The plan is to come up with a course—very much like a national vocational qualification course—where we can start to put graduates and apprentices through and eventually turn them into aircraft painters.”
PPG offers an Aerospace Coatings Academy to help customers learn about new products, painting techniques and best practices. “This has been very popular with our customers, as it helps us to introduce them to our products and how to use them in the most efficient and effective way,” Purdy says. Beyond paint, the program also covers topics such as sealant and adhesive application.