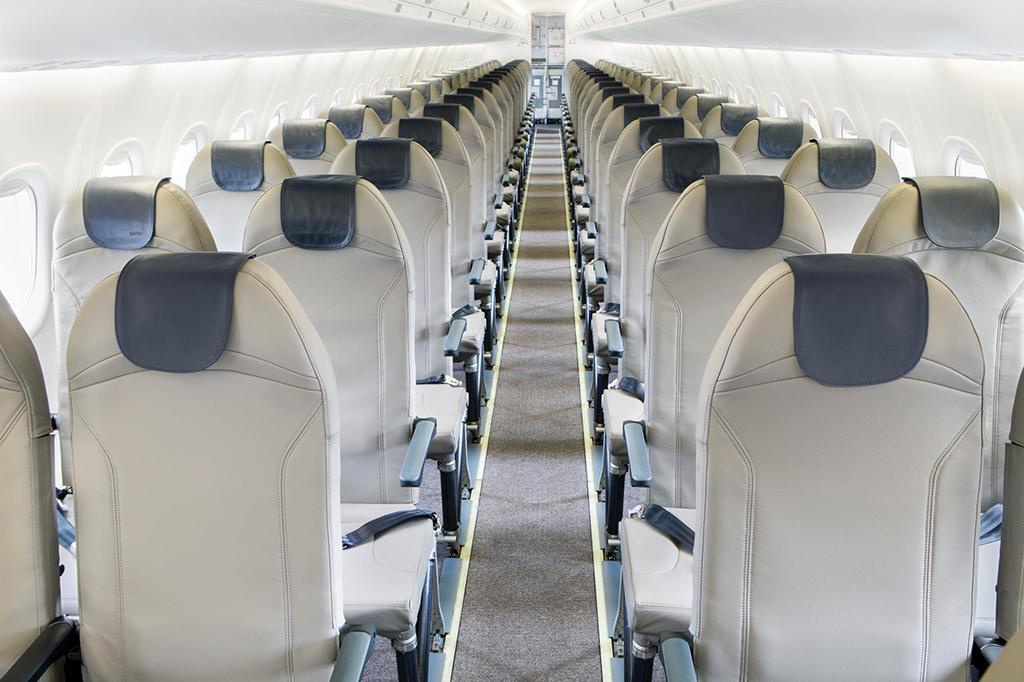
Seat design is evolving relatively fast by aerospace industry standards. A seat is not as complex as a turbofan engine, but passengers will quickly identify seating with a given carrier—meaning seat manufacturers are competing intensely on comfort and aesthetics. Meanwhile, they are also under pressure from operators to cut weight and keep maintenance needs in check. Delivery lead time has been an issue amid a context of strong demand.
In recent years, new players have shaken up the market and succeeded with innovative ideas at a time when established suppliers were experiencing production issues.
Startup companies begin with economy seats because they are less complex. “We brought on quite a few,” says Christian Kley, Airbus’ head of seat purchasing. “Acro is a relatively young player; it established itself in our catalog in the last five years. Geven has evolved from a small family company in the early 2000s to a very solid position. Its market share stands at 10-15% on the [Airbus] A320 family.” Meanwhile, “Expliseat’s products feature a titanium structure for light weight, but it comes at a higher price,” Kley says. This may explain its relatively slow adoption.
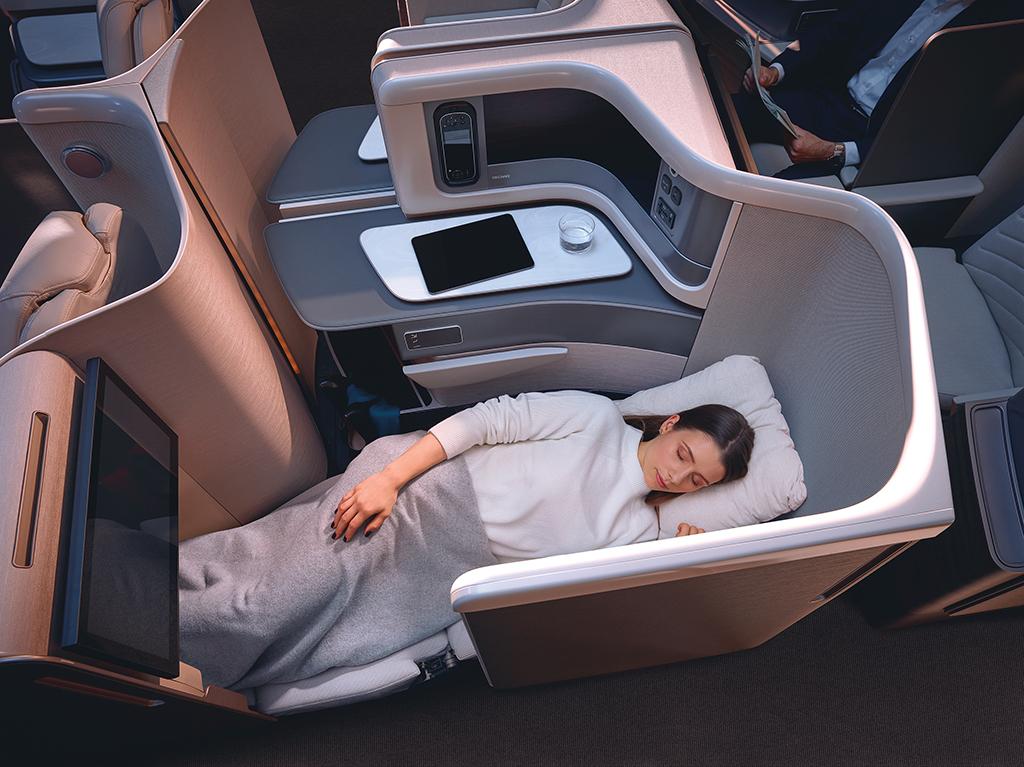
The current marketplace is thus significantly different from five years ago. Back then, Kley says, three companies dominated the economy seat market: B/E Aerospace (now part of Collins Aerospace), Recaro and Zodiac Aerospace (taken over by Safran).
What is at stake in seat design? “The seat can contribute to a unique selling proposition—the business card of an airline,” says Mark Hiller, Recaro Aircraft Seating’s CEO. Benjamin Saada, Expliseat’s CEO, adds that total seat weight in a cabin accounts for 10% of an aircraft’s operating empty weight.
But there are nuances in design drivers. “We talk about passenger experience, rather than comfort, as we strive to have the passenger spending his or her travel time in the least unpleasant position possible,” says Saada. In a car, occupants can use settings depending on their size, build and habits. “In an aircraft, technology would make this doable, but we do not want the passenger to spend too long with settings. So we are looking for comfort for as many people as possible and acceptability for the smallest and tallest ones,” Saada explains.
To design a seat, Expliseat uses digitally simulated passengers. Pressure points on the back are studied to avoid the most sensitive areas. Such simulations help find new ways to arrange components. Moving up the tray table by a mere 1 cm (0.4 in.) improves comfort for 5% of passengers, whose legs then will not touch the folded-up tray table.
In the future, different versions of a seat may be created that take into account the average size of a passenger in different regions.
In its quest for simplification, Expliseat got rid of the footrest. “A footrest is useful for a small passenger, but is in the way of a tall one,” Saada says. “Moreover, as a moving part, it is heavy and needs maintenance. So we repositioned the luggage bar, which maintains a piece of luggage under the seat, [and] it can act as a footrest.”
A design can be improved by studying the seat’s behavior in service. Recaro has equipped an economy seat with sensors that it installed on airplanes flying with TAP Portugal. “It collects data on how passengers use the seat and how it behaves,” Hiller says. A first batch of data has been analyzed.
Saada is on the same page. “Thanks to customer feedback, we have discovered use cases and therefore progressed in seat design,” he says. “We have put in place an incident monitoring system. We collect customer data and translate [it] into technical information, which in turn will be injected into our design. Such a cycle requires extensive organization, which we have implemented and are improving.” Expliseat, founded in 2011, is building on the 20 million flight hours of experience it has accumulated with 15 carriers.
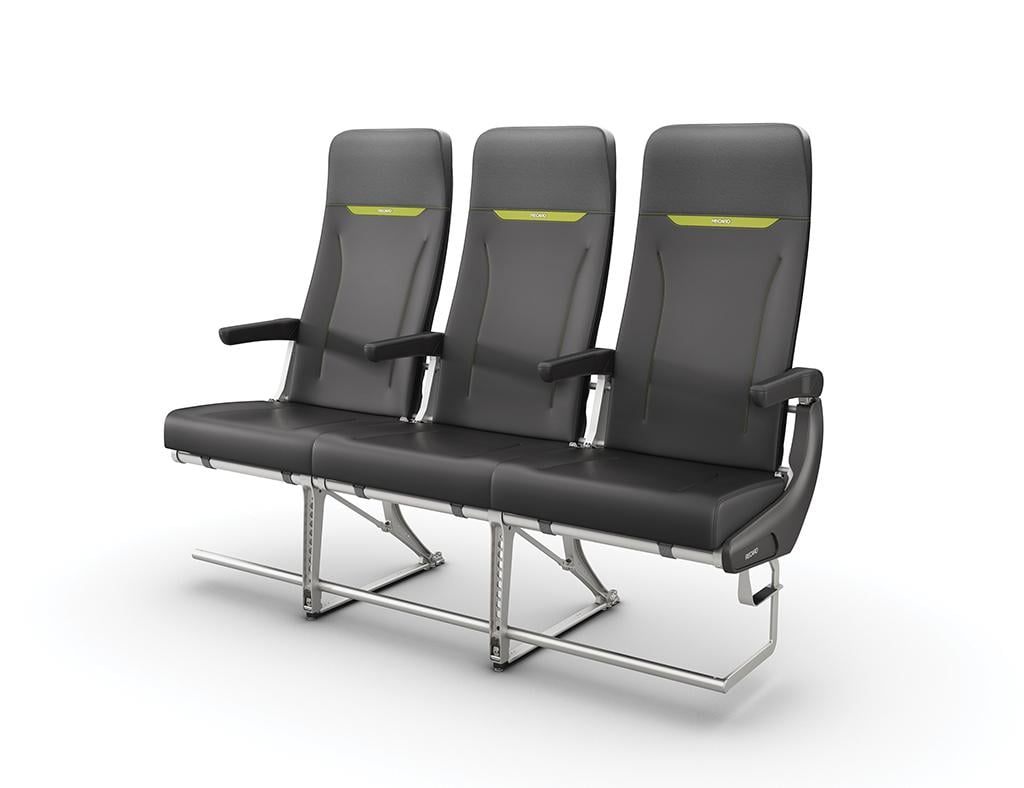
Materials should be carefully chosen, as they influence weight, maintenance needs and costs. Acro Aircraft Seating offers different materials for the seatback. In a basic Series 3 seat, the skeleton uses a glass-phenolic composite material, says Al Roots, Acro’s head of industrial design. “Weight and flammability are why we use them. Phenolic resins and glass-phenolic composites are inherently fire-retardant and have superior flammability properties. In addition, phenolics yield very low levels of smoke and combustion products under both flaming and smoldering fire conditions.”
In higher-end seats, Acro uses carbon fiber for its lighter weight.
Apart from carbon fiber, Expliseat uses titanium for structures. The metal was chosen rather than aluminum for its greater hardness. “With aluminum, there is a risk of a deep dent opening a chemical breach and leading to corrosion,” Saada says. Titanium is naturally corrosion-proof.
Additionally, new production processes are emerging. Recaro already uses 3D printing for some structural parts. “It enables the manufacturing of complex geometry parts, adding functions that could not be integrated with die-casting or milling,” says Hiller.
Acro has used 3D printing mainly for prototyping. In the near future, the process will become viable for the manufacturing of parts that otherwise require complex machining, says Roots. In his view, 3D printing is well-suited to low-volume production and would therefore allow cost-effective customization.
The technique can contribute to a reduced part count. “There is the danger of overcomplicating seat designs by adding extra layers, such as more padding. More components add complexity, weight, [and] implications for certification and cost,” Roots says. “We allow the engineering features, such as ribs, to be visible rather than covering them with shrouds.”
The part count is a factor in maintainability. “In its simplest iteration, Acro’s Series 3 has just 63 parts per triple seat,” says Roots.
On an economy seat, very few components need servicing, but the seatback recline system is one of them. The system’s cylinders need periodic resetting, with an interval of 1-2 years, Expliseat’s Saada tells Inside MRO. “We have created a system that is independent from the rest of the seat. The operator’s maintenance technicians can reset the cylinders or replace them with new ones under a rotable scheme. Replacing the cylinders takes less than 5 min. for a row of three seats.”
A maintainability feature of Acro’s seats also can be found in the seatback reclining system. The drawback of a recline button on the seat arm is that it has a long and complicated cable running around the seatback. When the recline mechanism breaks, a number of components have to be removed to access the cabling.
“We have located the recline lever on the front spar,” Roots says. The cable run is very short with minimum bend. The recline mechanism and associated cabling can be accessed easily under the composite foam seat pan cushion and fixed in minutes, he says. Moreover, the armrest itself can be removed and replaced in seconds.
An Acro Series 6 seat does not have a seat pan structure. Other seats incorporate an aluminum seat pan, which is prone to cracking, Roots says. Instead, Acro has developed a cushion made of a composite foam structure mounted directly onto the spar tubes. The cushion can be removed, enabling instant access to the seat structure as well as mechanical and electric elements.
In economy, there has been a consistent tendency toward increasing cabin density, which calls for slimmer seats. Design engineers use every possibility to offer the passenger maximum personal room while consuming as little space as possible in the cabin.
An Acro seat skeleton curves around the passenger’s behind, creating a bucket silhouette that both results in an ergonomically correct shape and maximizes space efficiency, according to Roots. Acro’s composite seatback is curved in the horizontal and vertical axes. Thus, it matches the natural shape of the spine and, the company says, provides 2 in. of additional legroom as the passenger sits farther back on the seat pan.
Some constraints are external. “There are design and engineering challenges when we add inflight entertainment (IFE) packaging,” says Acro’s Roots. “In IFE system integration, boxes are getting smaller, but passengers tend to ask for more facilities in the seat, such as USB sockets.”
Recaro’s Hiller adds, “As for IFE equipment, we need to match innovation cycles in electronics, which are different from innovation cycles in seats.” IFE equipment has an impact on seat certification. “If we integrate a different display size, we need to recertify the seat, including a 16g crash test in case of hard landing,” Hiller says.
The head of the crash-test dummy hits the back of the forward seat where the display is placed. Some shock absorption is provided by a mechanism that lets the display move forward or by elements such as foam behind the display.
An economy seat typically weighs 8-15 kg (18-33 lb.), Hiller says. This begs the question: Is there a case for an ultralight seat? “It is all about finding the sweet spot in robustness, weight, comfort and price,” he says. “Our 8-kg seat meets those needs. A few years ago, we had a concept for a 5.6-kg seat, but the price would have been pretty high. The market was not ready yet.”
Expliseat started with a bare-bones seat, the TiSeat E1, which featured a reduced part count and very light weight of just 4 kg. That design evolved into the more comfortable TiSeat E2, which can be as light as 5 kg—the exact weight depends on the options. The titanium composite TiSeat E2 is 60% lighter than the competition, Expliseat says. The E2’s configuration is “flexible,” thanks to options such as seatback recline, more comfortable foams, the inflight entertainment system, an electric outlet, a tray table and pockets.
Expliseat has moved to advertizing more comfort, from an almost exclusive focus on weight. The TiSeat E2 was co-designed with Peugeot Design Lab. “Thanks to our cooperation with the automotive sector, the E2 seat is soft and enveloping—something the economy-class [seat] had lost,” says Saada.
A business-class seat, which can transform into a bed and includes a shell or furniture to provide a level of privacy, is much more complex and heavier—usually 80 kg—than an economy seat.
Business-class seats are about to make strides in maintainability. Predictive maintenance could be integrated. The system could identify a part, such as an actuator, that might break and order the replacement. A business-class seat already has electronics built in, so adding predictive maintenance capability would be affordable.
“It is a major element in the bigger picture: The connected cabin, with a digital backbone and applications for maintenance as well as passenger wellbeing,” says Airbus’ Kley. The OEM is testing a connected business-class seat on an A350 test aircraft. “The technology is available. If the tests are conclusive and positive, it will move into the market,” Kley says.
He would not specify which of the big names in business-class seats—Collins, Recaro, Safran and Stelia Aerospace—is involved.
From the airframer’s perspective, seat suppliers need to improve delivery lead time. For a complex design a customer chooses from the business-class seat catalog, it typically takes at least two years from the first discussion to installation, says Kley. “Customers do not understand why the seats’ lead time is longer than the aircraft’s. Reducing business-class seat lead times to 10-18 months should be doable for business class, and below nine months in economy,” he adds.
Manufacturing seats is not particularly difficult, says Expliseat’s Saada. “The real challenge is delivering customized seats with a short lead time and large volumes.”
Recaro’s Hiller mentions the same problem. “A challenge in the aircraft seat industry is the short lead time,” he says. “Carriers order aircraft and decide on seats and customization later.”
Moreover, each seat has several variants depending on the side (left or right) and row. A first-row seat has its tray table integrated in the armrest, while a last-row seat has no display in the back. The number of variants is greater than in the automotive industry but with a lower production volume.
Airbus uses a buyer-furnished equipment (BFE) model for most of its aircraft. To qualify and be part of Airbus’ BFE catalog, a supplier has to meet the airframer’s performance standards in engineering, production and support. Compared to economy-seat suppliers, “Airbus tends to be more selective with business-class seat suppliers because it is a tough business to be in,” Kley says. “The technology is more sophisticated and requires a different level of know-how.”
A dozen suppliers in economy- and business-class seats are represented in the Airbus BFE catalog. Borders tend to blur, Kley notes. “A business-class seat on a narrowbody can be a premium economy seat on a widebody.”
What could be the future features and design drivers in aircraft seats? In business class, a challenge has appeared recently with the emergence of narrowbodies in long-haul operations, most notably the A321XLR. “Airlines want a full flat-bed seat with full aisle access and full privacy. When trying to maintain a competitive seat count, this is difficult to design in a narrower cross-section than [for] the widebodies,” says Kley.
In business-class seats, there is also a trend to replace foams with inflatable bags as a lighter alternative.
Textile maker Lantal is developing heating and cooling systems for business-class seats. A specially designed heat mat uses resistive wires. A ventilation system pulls air through the seat cushion to create a cooling effect.
“We could introduce flexibility to reconfigure the cabin between two flights, depending on the number of passengers,” Hiller says. “Seat pans could be flipped up, and the row could move along rails, thus enabling pitch variability.” The idea has yet to be turned into a product, which would involve integrating the feature into the booking system of the airline.
With the COVID-19 pandemic, health protection may become a crucial driver. And surface materials can improve hygiene levels. “There are a number of materials already in the market that have antimicrobial qualities, such as upholstery, plastics and paint,” says Acro’s Roots. “To improve hygiene levels in the future, additives with antimicrobial properties could be integrated at every stage of the manufacturing process.”
Meanwhile, greener processes and operations will continue to shape commercial aviation.
Expliseat has made progress in using recycled material in new seat manufacturing. Thus far, the company uses offcuts of preimpregnated carbon fiber. It took two years of research and development to prove recycled fiber meets technical specifications. Another year was needed to bring the approach into production.
The next step, in Saada’s view, will be to use offcuts from suppliers. Traceability is a challenge but looks feasible, he says.
Expliseat also offers seat upgrades in which the structure remains unchanged, but other components are replaced or added. After two upgrades, the seat may have to be entirely replaced. In the future, the seat structure’s composites may be recycled to manufacture new structures.