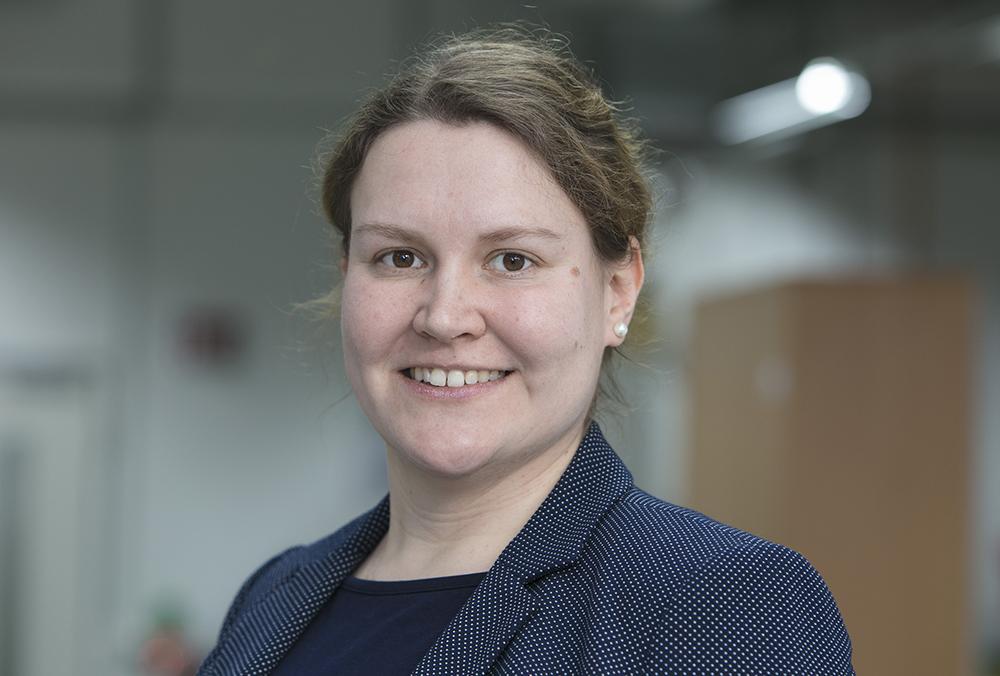
Aenne Koester, head of additive engineering and manufacturing at Lufthansa Technik
Additive manufacturing already prints tens of thousands of polymer parts for major MROs every year. The technique saves money and time by simply replicating OEM parts quickly, or it redesigns replacement parts to make them better and lighter than OEM predecessors. Aenne Koester, head of additive engineering and manufacturing at Lufthansa Technik, speaks with Aviation Week about the company’s use of additive polymer manufacturing and how the aftermarket can make additive parts manufacturing even faster.
Has Lufthansa Technik (LHT) used additive polymer manufacturing to both redesign cabin parts and to replicate conventional parts? If so, can you give us some examples of both types of additive polymer manufacturing?
Our aim is to leverage the various advantages of additive manufacturing (AM) for aviation in the best possible way. In LHT’s AM Center, we thus indeed use AM not only for a simple replication of conventional parts geometries, but also for a redesign of cabin components. Especially in our VIP cabin completion business, our long-standing additive manufacturing competence helps us to design cabin components in such a way that they are specifically tailored to individual customer needs. As VIP Completions are a rather secretive business, I unfortunately cannot go into much detail.
However, we also use AM to produce conventional components for commercial airliner cabins. Here, there are also examples in which we do not simply replicate the component in question, but significantly improve its function, for example by making it lighter or more robust. We have already done that for a number of everyday components such as ventilation grills, clips or covers.
How much longer does it take to design and obtain approval of redesigned polymer parts than for replication of additive polymer parts?
With regards to time, the design and approval paths for both categories are largely comparable in our experience. The prerequisite, of course, is to have appropriately skilled engineers who can easily exploit the benefits of AM in the designs and take into account the challenges of the AM process during the design process.
What are the major delays in redesigning polymer parts?
In the best case, redesigned additive parts for aircraft cabins require the same amount of time as their conventionally manufactured predecessors. However, this often depends on the criticality of the cabin components and the available material property data of the respective manufacturing process. Whenever there is a lack of available data, additional testing will be required to ensure the required verification for an approval. This additional and nowadays necessary testing can delay the usage of additive manufactured parts.
What steps can LHT, regulators or others take to speed up use of redesigned polymer parts for the cabin?
For me, the key to using additively manufactured parts faster is knowing how material properties depend on the manufacturing process. A broad database based on evaluations of in-process samples or dedicated sample series could be an invaluable help in this regard. In order to create such a broad database and make it usable, design engineers, manufacturers and authorities should work together even more intensively than today to create common guidelines and knowledge.
Do you expect much broader use of additive polymer parts at LHT in the future? Are there new types or sizes of polymer parts you expect will be made in the future?
I expect an increasing proportion of additively manufactured components, especially inside the aircraft cabin. First, additive technology and its possibilities are still constantly evolving. Second, knowledge of and experience with the use of additively manufactured components are also constantly increasing. I personally think the increased degree of design freedom that AM offers will play an even more important role in the future. Bionic design [application of biological methods to design of technology] is key. Adjustments to the cabin design and weight reduction realized through AM can contribute significantly to the aviation industry’s effort for increased sustainability and a reduction of its carbon footprint.