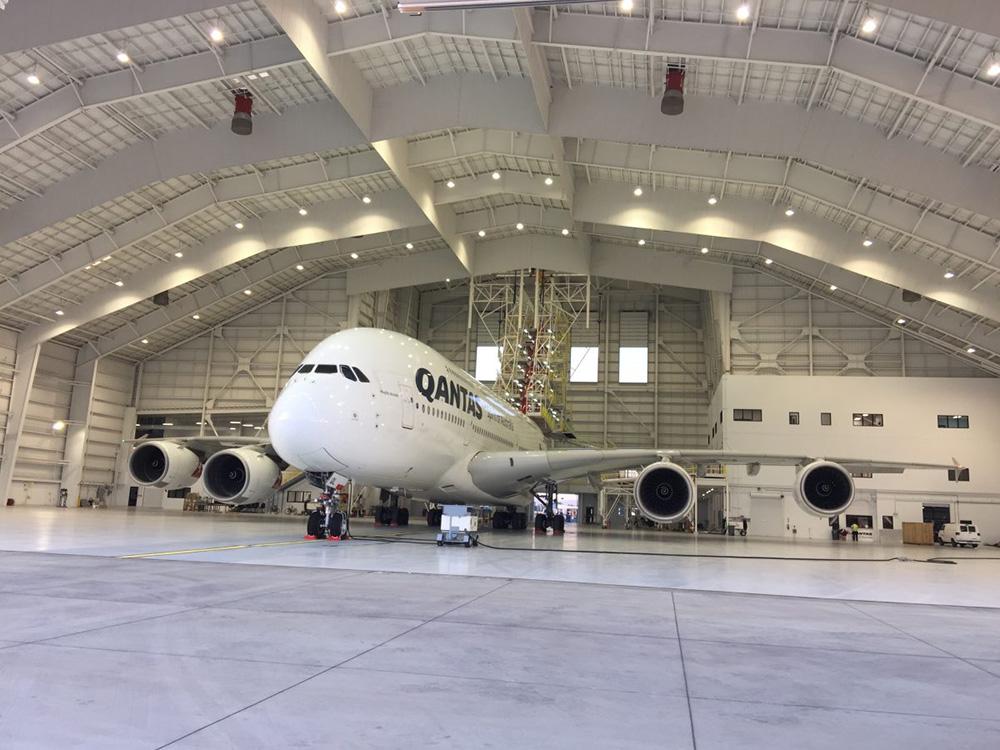
MIAMI— Paperless airline maintenance has come in waves: first some early adopters, then a lull in implementations and now a resurgence of interest. Nearly 40% of attendees at a recent IFS panel discussion of paperless maintenance are now considering deployment.
Two of those early adopters shared their own lessons for the benefit of the latecomers. Dean Reynolds is maintenance director of Executive Jet Management (EJM), which maintains 255 aircraft and helped IFS Maintenix define and launch its paperless tools more than 15 years ago. David Kelly is manager of maintenance operations at Qantas, which went paperless on its new Airbus A380s quite early and later brought the rest of the fleet into electronic documents and signatures.
EJM started the process in 2005, following an FAA advisory circular which required mechanics to enter a personal identification number (PIN) and encryption of the system to prevent tampering with that PIN. EJM established a test version in 2006, and then it made dual paper and electronic entries so the FAA could audit the system.
EJM and Maintenix then improved the test version, for example, by consolidating four data-entry pages into one. The companies rolled out version 6.3 in 2008 and made more improvements, such as enabling entries to be edited but still preserved.
Around that time, Qantas started going paperless with its new A380s. It replaced the OEM’s electronic logbook (ELB), which Kelly found unsatisfactory, and eventually extended paperless tools to its Boeing 737s. Kelly says starting with one type—the A380—made training and implementation simpler, but the A380s flew to foreign stations, so many remote workers had to be trained as well. Kelly told the panel he wishes he had never used Airbus’s ELB.
To keep the FAA happy, EJM modified its paperless forms to looks exactly like the old paper forms the regulator was used to. Reynolds persuaded regulators that electronic tools would reduce mistakes made in writing and reading entries. The FAA confirmed the reduction in errors.
Qantas had an easier time with Australia’s Civil Aviation Safety Authority, showing it how the new system ensured the right configuration and kept Qantas in compliance with regulations. Kelly emphasizes the importance of constant communication with staff and getting support from MRO leaders in each Qantas station. He says some older technicians were initially reluctant to use computers, but they were brought on board.
Younger mechanics are accustomed to and eager to use digital methods to type, rather than write, entries. They also want portability and see little point “in running downstairs to record data,” Kelly says.
Another virtue of the new system is that it provides one-to-many records. Instead of thumbing through paper, everyone at Qantas who needs the data can simply search the same system for what they require.
Reynolds agrees that getting senior mechanics on board first helps ensure that everyone will go along with the new tools.
On challenges, Reynolds says helping define Maintenix paperless tools meant there were delays and gaps in getting new versions in place. He says a few older mechanics threatened to retire before they would adjust, but in the end they all stayed.
Kelly says Qantas’ main challenge has been making sure there is a backup in place in case of a glitch in the electronic process. For example, Qantas must remove wasp covers from pitot tubes just before takeoff, and that task must be entered before release for departure. The airline must ensure that any electronic glitch is covered by a backup so aircraft take off on time. “You must have a backup,” he stresses.
However, Kelly says compliance is much better since Qantas adopted paperless. The airline has also eliminated massive amounts of paper and warehouse space needed to store it. Reynolds agrees, noting EJM also has a significantly fewer printers to maintain.
Inefficient reading of handwritten notes is over, too. “All that’s gone,” Reynolds says. One-page paper forms that sometimes required appending other paper sheets for complex defects are also gone, with electronic pages flexible enough to accommodate all the necessary information. Mechanics changing shifts can now find defect status quickly, rather than thumbing through many pages. “The benefits are huge,” he adds.
“Information is more accessible; everyone sees the same data,” Kelly stresses. For operators contemplating going paperless, he recommends IATA’s website for a very helpful guide to getting ready for paperless.