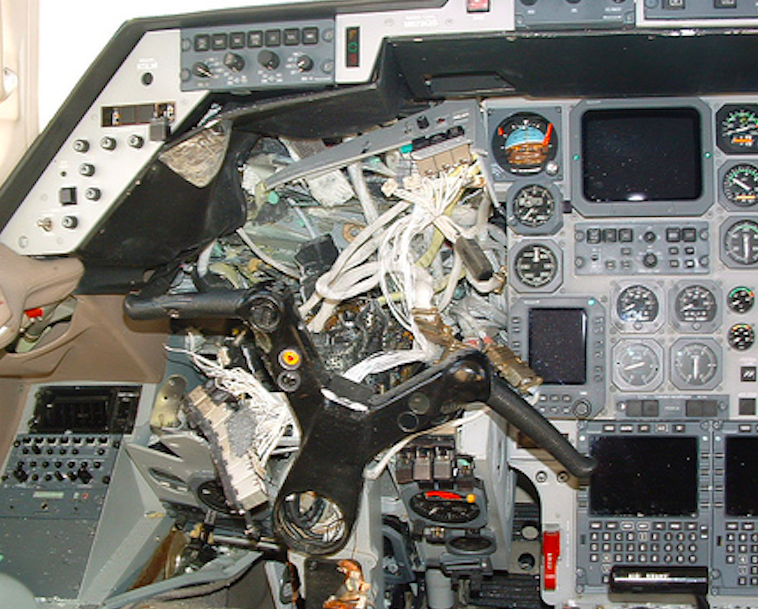
In our profession we have been trained to calmly and proficiently handle a wide variety of events that can occur without warning. But no one has ever been trained to have the wing spar of a glider crash through the instrument panel, spraying sharp debris, and rendering vision almost impossible from facial wounds and an insurmountable blast of 500 kts of air.
These were just a few of the challenges facing the pilots of a Raytheon Hawker 800XP that experienced a mid-air collision with a glider while on descent into Reno-Tahoe International Airport (RNO), Nevada, on Aug. 28, 2006. In a brief fraction of a second when the captain noticed a white glider filling her windscreen she grabbed the yoke and tried to turn away from the glider, but the impact at that immense speed was brutal.
The first officer heard an alarming “Whoomp” just as the instrument panel exploded before his eyes. In a microsecond all hell broke loose. The debris in the cockpit and the roar of noise were nothing they had ever experienced.
The captain reflexively determined to regain control of her stricken jet, but nothing in her training had prepared her for this situation. The instrument panel had been turned into tiny shards. In fact, the obliterated wires, glass, plastic and steel were now spilled over the yoke, actually constraining its movement.
Without instruments, not only did the pilots have no idea of critical flight information such as their airspeed, they had no other information to tell them the status of their engines, flaps and gear, all of which would be necessary for landing. They had no way of knowing that a large segment of the right wing was missing, or that one of engines was no longer functioning due to damage. A punctured fuel tank was rapidly causing a fuel imbalance, adding further to the abnormal flight characteristics of the normally docile Hawker.
The next minutes of their harrowing struggle in which they successfully landed the crippled jet at nearby Carson City airport illustrated supreme professionalism. The glider pilot bailed out and parachuted to the ground. He was faulted by the NTSB for not using his transponder.
There is no realistic training to prepare a pilot for an event such as this. Your chances of encountering a similar event are almost nil, and yet as pilots we need to be prepared to handle the many sudden surprises that occur in the real world. Not every surprise will be comparable to a mid-air collision. For fixed-wing pilots, events such as runway incursions, lightning and hail strikes, automation failures, and stalls can suddenly disrupt an otherwise routine flight and require immediate reaction. For helicopter crews, the list begins with a litany of components in the flight control system that can suddenly fail, loss of tail rotor control or Vortex Ring State.
It is worth examining the important lessons reinforced by the actions of the Hawker crew and others who have dealt successfully with surprise events, as well as examining the limitations of human performance and information processing when confronted with surprise. The historical record also includes examples of flight crews who have been unsuccessful when confronted with surprise, and those tragedies contain equally important lessons.
Simulator Responses Can Be Very Different
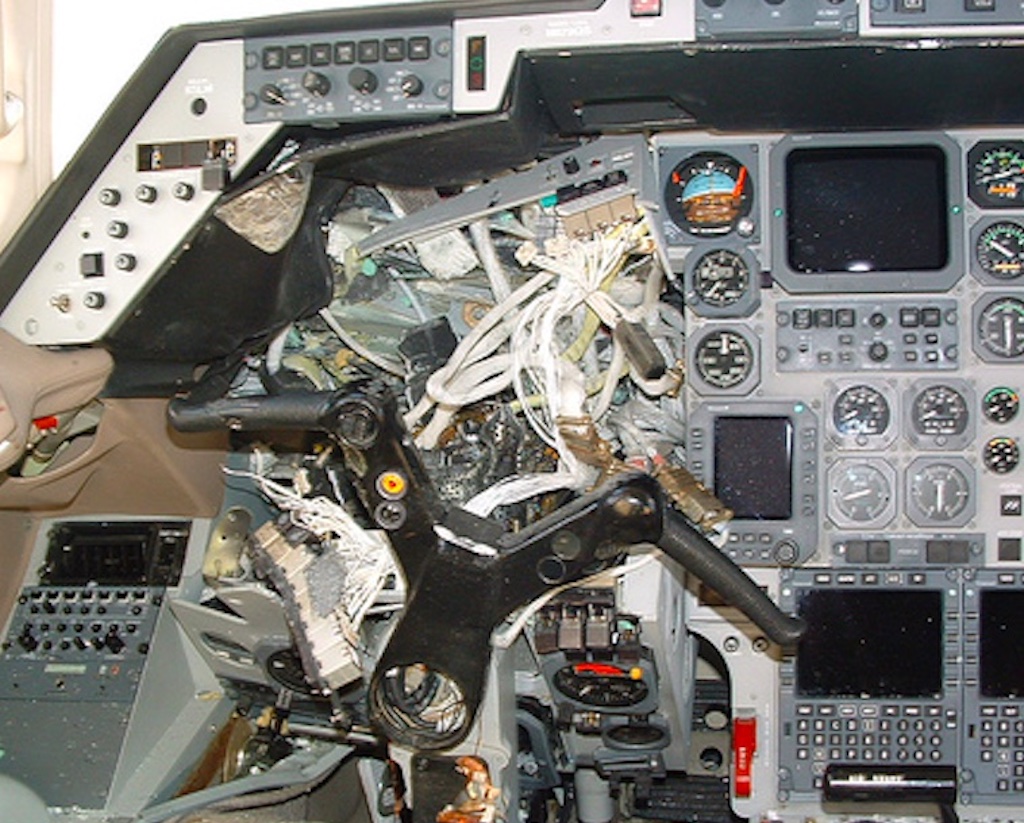
Prof. David Woods of The Ohio State University Department of Integrated Systems Engineering has researched complex human-machine systems for over 40 years and notes that a pilot’s response in a simulator can be very different to comparable events in the real world. Specifically, pilots tend to respond to an abnormal situation faster in the simulator, thus a 5-to-10 sec. response in the simulator might even double in the real world
This correlates with the digital flight data recorder pilot reaction times from eight real-world rejected takeoff (RTO) incidents that showed a range of 4.1 to 9.2 sec., with an average of 6.5 sec. Boeing engineers analyzed 69 rejected takeoffs documented in a special NTSB study, “Runway Overruns Following High Speed Rejected Takeoffs,” and noted that the crew had incorrectly interpreted the cause of the RTO in 53.8% of the 69 rejected takeoff events.
Human Factors Engineering, a textbook written by several notable human factors researchers, cites a large body of research on human detection and reaction to complex problems, and the rejected takeoff problem exactly fits the definition of a “complex problem.” The difficulty and speed of selecting a response or reaction are influenced by several variables. Three of the variables are particularly critical in the RTO problem. These are decision complexity, expectancy, and speed-accuracy tradeoff.
While our takeoff Go/No-Go performance numbers are primarily based upon the engine-failure scenario, there are many other maladies that can afflict an aircraft and make it un-airworthy for flight. A high-speed tire failure can cause stimuli that pilots have never experienced before. The complexity of the Go/No-Go decision for a tire failure exceeds the simple decision in the accelerate-stop criteria currently used in RTO certification that is reinforced the many times a pilot returns for recurrent simulator training.
Christopher Wickens, former head of the Human Factors Division at the University of Illinois Urbana-Champaign, and author of Engineering Psychology and Human Performance, found a very definable relationship between response-time and error-rate. In other words, there is a trade-off between speed and accuracy. When pilots scan the instrument panels rapidly because of time pressure, the accuracy of a pilot’s perception will suffer and the probability of error will increase.
This was illustrated by the crash of TransAsia Airways Flight 235, an ATR 72-600, on Feb. 4, 2015, during its initial takeoff from Taipei. Shortly after takeoff, a fault in the autofeather system on the right engine caused it to autofeather the engine. The flight crew misdiagnosed the problem and shut down the fully functioning left engine, resulting in a loss of control and crash into the Keelung River. Forty-eight of the 58 people on board were killed.
Our industry learned many decades ago that reaching up to make changes to throttles and fuel levers during an engine failure on takeoff was prone for mistakes. Thus, the industry standard cemented the concept that other than maintaining aircraft control, a flight crew would take no actions during an engine failure on takeoff until attaining a safe altitude and only then going through a deliberate, methodical process before any knob or lever was moved.
Expectancy means that we react more rapidly and accurately to situations in which we anticipate certain actions or events as opposed to a situation in which the events are a surprise. For example, the slightest abnormality in the aircraft’s performance or handling during a takeoff in the simulator is quickly interpreted as an engine failure. But the real world has many other different surprises.
This author’s lengthy search of NASA Aviation Safety Reporting System (ASRS) files found that only two of the 175 business jet high speed rejected takeoff (RTO) reports were caused by powerplant malfunctions. In fact, more than 96% of the high-speed RTO incidents in the NTSB, FAA and NASA ASRS records were due to non-engine causes. An important point from this data reveals that the real world has other surprises that are more likely to cause a high-speed RTO.
It simply isn’t feasible to train for all the possibilities that might cause a high-speed RTO. Additionally, the possible damage to an aircraft’s structure and handling characteristics following a high-speed tire failure (which is four times more likely to happen than an engine failure) or an animal strike (which is two times more likely) creates a bewildering number of factors that can’t be quickly turned into a simple Go/No-Go decision.
Abrupt Control Deterioration
A professional pilot needs to know an aircraft’s aerodynamic handling characteristics and limitations for all phases of flight, varying flap conditions, changes caused by environmental conditions, as well as the conditions that cause instruments to display misleading information.
A presentation entitled “Loss of Control,” given to the International Society of Air Safety Investigators in September 2011, revealed that 31 of 71 loss of control (LOC) accidents were due to unintentional stalls. Incidentally, aircraft were configured with gear and flaps extended (either partially or fully) in 52 of the 71 accidents. Furthermore, in the slower speed regime, the aircraft tends to be at a higher angle of attack that can further limit its maneuverability without stalling the aircraft.
Fully two-thirds (45 of 71) of the LOC accidents occurred within 1,000 ft. of the ground. This unfortunately means that most of the accidents occur with very little margin of safety. There are a troubling number of real-world factors that will cause a rapid stall without warning at an angle of attack (AOA) far below the critical AOA. Many of these phenomena will negatively change the aircraft’s behavior such that the aircraft is unrecoverable. In-flight conditions to include frost, ice, heavy rain, flap configuration, ground effect, cross winds, anti-icing fluids, deteriorated wing seals and the effects of Mach waves during transonic flight cause large reductions in a wing’s actual stall AOA.
High-performance airfoils exhibit stall behaviors completely different from low-performance airfoils, to include lack of aerodynamic warning, an abrupt loss of lift, and an uncontrolled rapid roll that cannot be arrested by flight control inputs. Deteriorated aerodynamic seals, especially those near the leading edge of the wing, cause a significant loss in the maximum lift of a wing as well as decrease the stall AOA. These airfoils are especially susceptible to any form of contamination. It is important to realize that the wing’s critical angle of attack may change with no apparent visual, tactile or performance cues associated with a contaminated condition.
The point is that training is giving the impression that stalls are relatively benign and can be easily recovered, when in fact real world conditions that are causing “stall by surprise” can occur rapidly, at AOAs far below the normal stall AOA, and that creates grave deterioration in the effectiveness of flight controls to respond. By the time the pilot is caught by surprise, the aircraft’s handling characteristics are already severely degraded, perhaps beyond the point of recovery. The safety implications and consequences of this misleading information are significant in upset prevention and recovery.
Primal Response
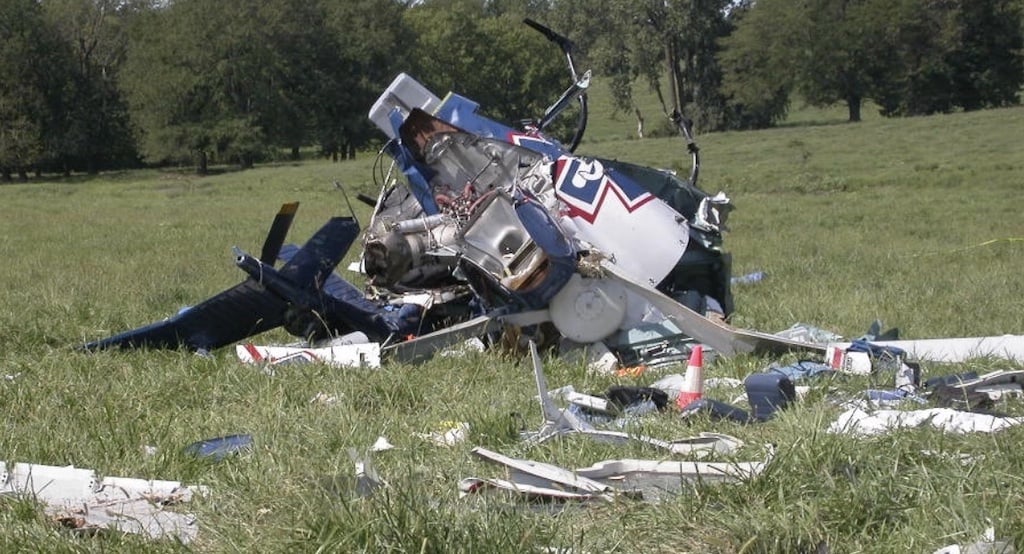
Some conditions require an immediate (and accurate) control input, or what is often termed primal response. The NTSB’s recreation of the Air Methods Eurocopter AS350 B2 helicopter accident near the Midwest National Air Center at Mosby, Missouri, on Aug. 26, 2011, illustrates this important point. The pilot, flight nurse, flight paramedic, and patient were killed.
Initially safety investigators were perplexed at how a highly trained former AH-64 Apache pilot failed to apply the proper autorotative flight control inputs after an engine failure due to fuel exhaustion.
During simulator recreations of the accident sequence, test pilots reacted to the flameout with simultaneous aft cyclic, down collective, and left pedal. The flameout was initiated at approximately 300 ft. AGL at a cruise airspeed of 115 kts. By utilizing these control inputs, the helicopter successfully landed, utilizing 27 sec. to transition into autorotation, bleeding off the kinetic energy during the cyclic flare, and setting down.
In contrast, when the simulator scenario attempted an initial pilot reaction with just the collective and no cyclic under the same entry conditions, time to impact was less than 5 sec!
The simulator flight tests concluded that when a loss of engine power occurs in the AS350 B2 at cruise airspeeds, the pilot must simultaneously apply aft cyclic and down collective to maintain rotor rpm. Additionally, these reactions are required within about 2 sec., or else the rotorcraft will be in an unrecoverable condition.
There are several important lessons from the Mosby accident. First of all, there are flight conditions in which the primal control inputs must be exactly correct for that specific make/model of aircraft, as the consequences of less-than-correct control inputs will further aggravate the loss of control.
Second, the correct control inputs must be made immediately, or else the condition of the aircraft will exceed the limits for recovery. Despite the credentials, experience and military training of the pilot, the training conducted in his transition into a civilian rotorcraft was ineffective.
This leads us to a third major point. Abrupt, unanticipated motions can overwhelm a flight crew. The sensory systems are poorly suited to abnormal accelerations and can overwhelm the body’s sensory, vestibular, proprioceptive (sense of body position and movement), and motor mechanisms. Some surprises, for example Vortex Ring State or loss of tail rotor control, will cause abrupt aircraft motions that can overwhelm the body and interfere with a pilot’s ability to focus vision and make accurate, fine-tuned appropriate corrective movements.
The fourth point highlights the pervasive nature of negative habit transfer. How do we train to instill the right “primal response” in a pilot when his or her background comes from aircraft with significantly different handling characteristics? Manufacturer Robinson Helicopter, found that highly experienced fixed-wing pilots habitually apply fixed-wing control inputs to disturbances that can produce mast-bumping contrary to the training they’ve received in helicopters.
Is it possible to “un-train” those primal responses learned over decades in one type of aircraft and implant a different set of primal responses? The Robinson data suggests perhaps not.
Real Danger
There is a real danger when there is a mismatch between the pilot’s expectation and reality. This is especially the case when an aircraft is behaving in a sudden and threatening manner but is not responding normally to the pilot’s control inputs. The Boeing 737 Max crashes of Lion Air Flight 610 on Oct. 29, 2018, and Ethiopian Airlines Flight 302 on March 10, 2019, will long be etched in accident investigation and engineering journals as examples of this phenomenon.
Ethiopian Airlines Flight 302’s cockpit voice recorder revealed the pilots’ struggle to manually bring the airplane out of a dive by pulling back on the control yoke and turning the trim control wheel. With both pilots pulling back on the stick, the front end of the plane continued to drop, until reaching 40° nose down. The two pilots together were not strong enough to break the counter forces on the control surfaces.
Not only were these flight crews desperately fighting against insurmountable control forces, simultaneously the cockpit was erupting with multiple alarms and alerts. This included continuous control column shaking and low airspeed warnings on one side of the aircraft. The pilots received alerts warning that the computer had detected conflicting airspeed, altitude, and angle-of-attack readings.
The mental confusion caused by multiple alarms and alerts in a cockpit is a condition that manufacturers should not allow. From a human performance standpoint, it is unrealistic to expect a pilot to troubleshoot an underlying problem causing unusual aircraft motions while struggling to control an aircraft that isn’t behaving in a predictable manner.
A review of 246 Aviation Safety Reporting System (ASRS) entries involving abrupt aircraft motions following the sudden disengagement of the autopilot indicated significant temporary spatial disorientation caused by somatogravic (vestibular) illusion and adverse kinesthetic (awareness of body position and movement) feedback from the flight controls, both of which significantly compound the ability of the pilot to promptly and accurately detect and make measured deliberate control inputs. The insight from these ASRS reports helps to explain how highly experienced pilots in many loss of control events have been unable to quickly detect and react to abrupt undesired aircraft motions.
Priorities After A Surprise
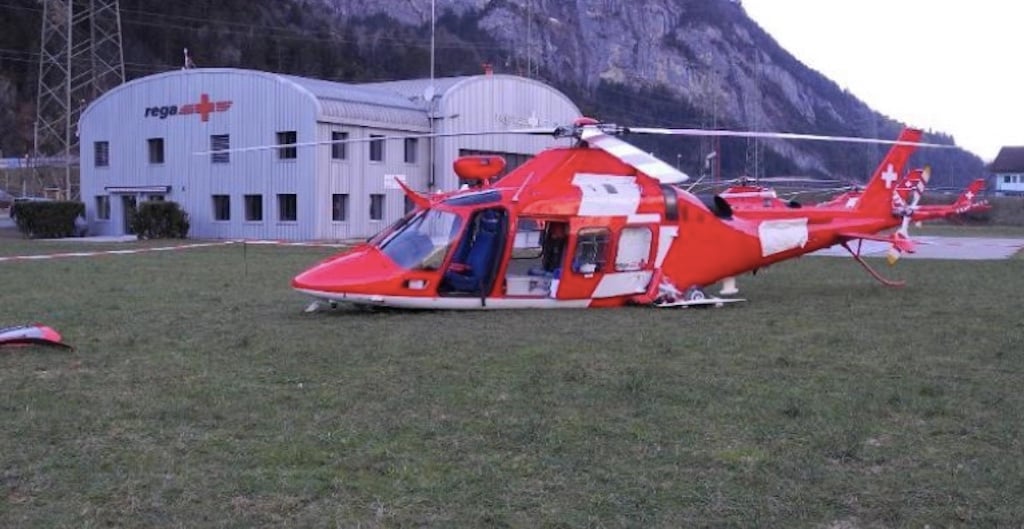
No one can predict when an engine might have a compressor surge on takeoff, when an aircraft taxis across the runway during takeoff, or a flock of geese obscures the windshield. It is realistically impossible to predict and train for each and every possible situation.
Are there general principles that can apply across a spectrum of surprise events? Fortunately, our profession has been given a number of great examples to follow when faced with sudden surprises. The flight crews of the United Airlines DC-10 emergency landing at Sioux City, Iowa, the Miracle on the Hudson, and the Hawker midair collision with a glider over Carson City prioritized the three key elements that have been a cornerstone in handling an aircraft emergency.
First and always—Aviate. Everything else is secondary to getting and maintaining aircraft control. When flying a fixed-wing aircraft, David Carbaugh, Boeing’s former chief pilot of flight operations safety, recommends attaining an appropriate pitch attitude and thrust setting. How do you know the appropriate pitch attitude and thrust settings for your aircraft? You should familiarize yourself with the typical pitch and thrust settings during normal operations.
Carbaugh advises pilots to confirm suspected instrument anomalies by cross-checking with other instruments, being aware of the reliability of each instrument used for the cross-check. An aircraft’s pitch and roll attitude information is generally reliable, especially as comparators would quickly point out an discrepancies between the captain’s and first officer’s primary flight displays. An engine’s thrust setting using the N-1 gauge would also be considered a reliable source of information.
The situation for “surprise” motions in a helicopter are too numerous and complex to summarize in a few sentences. As indicated by the Mosby accident investigation, in some emergencies it is necessary for the pilot to make an immediate and accurate control input to counter the abrupt undesirable motion of the rotorcraft. It is important to note that a majority of these conditions cannot be safely replicated for training purposes in an actual helicopter. Thus, it leaves open the immense question on how the industry safely trains its pilots to handle these surprise conditions.
This author has traveled to a wide variety of training operators, literally from Switzerland to Hawaii, to sample their techniques and suggestions, and this will be reported in a future article. There simply isn’t space here to delve more into rotorcraft-specific mechanical and environmental conditions that can cause abrupt undesirable motions.
Secondly, Navigate. In other words, get pointed in a safe piece of sky. If a malfunction occurs while on departure from Aspen, stay on the escape maneuver that avoids getting any closer to the threatening terrain. If you are on the North Atlantic Track System and must begin an immediate descent due to an engine failure or loss of pressurization, follow the prescribed procedure for getting off the track to avoid causing a loss of separation with aircraft following the same track at adjacent lower altitudes.
Thirdly, Communicate. In a situation such as the initiation of an emergency descent due to a loss of pressurization, your timely communication with ATC can alert the controllers if there is an aircraft on a converging flight path with your own. In the Hawker example referenced earlier, even though the copilot couldn’t hear a thing over the roar of the airstream thrusting through a hole in the instrument panel, he still attempted to communicate the aircraft’s emergency status to ATC. This resulted in Reno Approach watching the aircraft’s emergency descent and dispatching first responders to Carson City Airport.
The Hawker flight crew deservedly joined the ranks of elite aviators as role models of how to handle a surprise. Hopefully, you will never be confronted with a glider’s wing spar smashing through your instrument panel.
Endnote: In 2007, the Flight Safety Foundation presented NetJets pilots Capt. Annette Saunders and First Officer Mitchell Merchant with the Professionalism Award for safely landing their Hawker 800XP after colliding with a glider at 16,000 ft. The award is given to crewmembers who, by relying on skill and quick thinking, display outstanding professional performance.