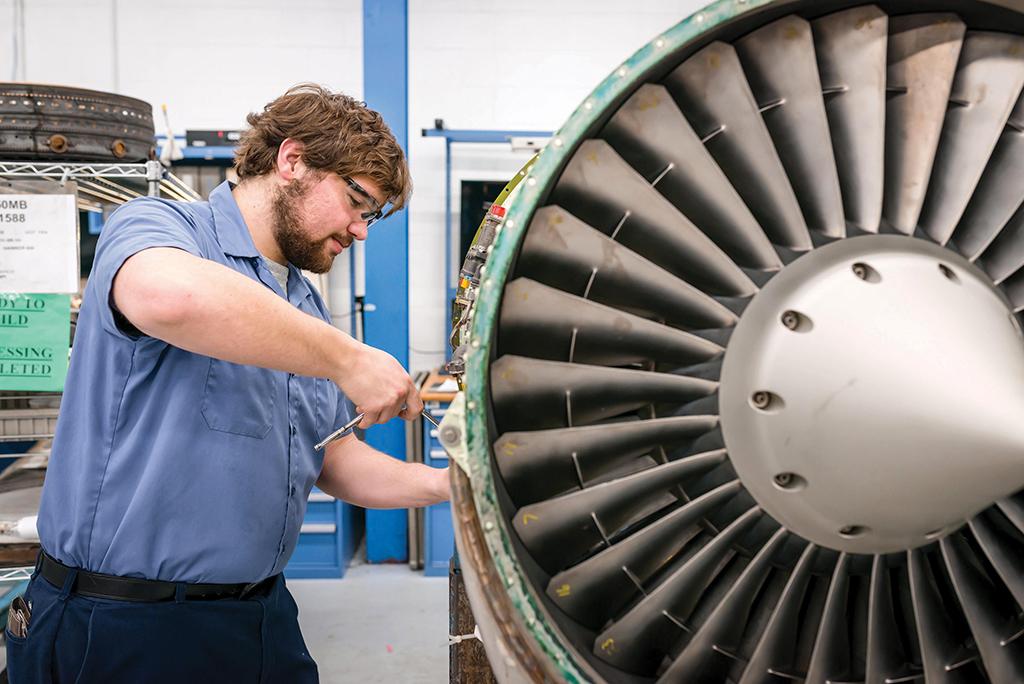
A technician at StandardAero’s Houston facility working on a TFE 731 engine.
Operators of older business aircraft are facing ongoing supply chain issues and materials shortages, particularly for the legacy engines powering them. Little if any relief is in site.
“Legacy engines are more impacted by non-availability of parts from the OEMs,” says Stacy Hollis, Duncan Aviation’s engine service sales. Honeywell TFE 731 engines represent the majority of the legacy engines serviced by the MRO provider, followed by the Pratt & Whitney-Canada PW 300 series.
Hollis reports that the shortages for legacy engines encompasses any and all parts—not just major components. However, turbine blades have been the most impacted by availability issues.
“Turbine blades from Honeywell and Pratt & Whitney-Canada have had significant delays in the last couple of years and it doesn't seem to be getting any better,” he remarks. “Some turbine blade sets may arrive in a few weeks once ordered, while other orders may take a few months to arrive.” Although these are parts for older engines, Hollis says that the engines continue to power aircraft with high monthly utilization rates.
Asked about sourcing used serviceable material (USM) as an alternative to new parts for legacy engines, Hollis stresses that they are almost non-existent. “In recent years, that market has been exhausted, so the best option I can offer are new parts directly from the OEM,” he says. “This has become the new normal in our industry.”
Used Serviceable Material
There is a continuing industry struggle for both new and used parts. “Used serviceable material is in high demand for MROs and OEMs, so we are constantly looking for options there,” says Brian Campbell, StandardAero Business Aviation vice president, global sales and marketing. “Another option is to provide our customers with exchange engines. However, due to the high demand for rental engines, availability is difficult and rental pools are frequently depleted.”
StandardAero is OEM authorized to provide heavy engine MRO services for legacy engines such as the Honeywell CFE738, HTF7000, TFE731, Pratt & Whitney PW300, PW500, Rolls-Royce Spey and Tay, out of primary MRO facilities in Van Nuys, California; Dallas; Houston; Augusta, Georgia; and the UK—as well as regional service centers in the U.S., UK, Brazil, South Africa and Singapore.
“OEM constrained parts are in high demand, driven by the strength of the industry’s recovery and continued, lingering pandemic impacts on the aerospace industry’s supply chain,” says Campbell. “Unfortunately, availability of a single part can cause a significant impact to turnaround times, especially if the part is sole-sourced.”
As Campbell explains, StandardAero’s in-house parts repair capabilities sometimes can enable the company to avoid new-parts roadblocks.
While the MRO works closely with OEMs to develop component repairs, “on many occasions, we are completely reliant on the external supply chain for OEM sole source parts,” he says. “To help address that, we work hard to educate operators regarding these industry dynamics and encouraging them to become more proactive about planning ahead and establishing longer lead times to work through the supply chain issues. Proper coordination and scheduling their maintenance and service needs, in advance, is key.”
As with other MRO executives, Campbell is not optimistic that things will change soon. “Due to current industry and economic conditions, we don’t envision any significant near-term improvements,” he cautions.
Start Early
“Start the conversation early,” when it comes to legacy engine support, suggests Phil Stearns, Stevens Aerospace & Defense Systems’ director, sales and marketing. He specifically points to the Pratt & Whitney Canada JT15D, which he reports is the most prominent legacy engine serviced by the Greenville, South Carolina-based MRO.
In the business jet world, the JT15D is among the most prolific. According to statistics from Jetnet, there are 4,102 in service, powering a total of 2,051 aircraft. Of that group, the Cessna Citation II—produced between 1978 and 1994—represents the largest user at 450. Other older, no longer produced Citations, along with the Beechjet 400/400A, Hawker 400XP, and Mitsubishi Diamond 1A also use this engine.
For operators that do not want to overhaul JT15D engines, many “are looking at sourcing used mid-time engines—1,500-2,000 hrs. remaining” to buy time at a lower cost, Stearns explains. “Although a viable option, a couple of issues to consider are the unknown and possibly risky condition of mid-time engines and the immediate timing needed to buy them once they are found. These are hot commodities. With no zero-time JT15Ds available, the mid-time sets are usually sold immediately once on the market. A set may be available today and the next set may not become available for months—it’s very unpredictable.”
Stearns adds that Stevens spends considerable time locating mid-time JT15Ds, which could take anywhere from a few days to a few months. Most JT15D engines come off retired aircraft.
With regard to USM, Stearns cautions that this could be very helpful in combating certain material shortages, but the availability and quality of USM varies widely. “Good quality, life limited parts (LLPs) are less likely to be available as USM,” he says. “For example, hot-section parts can represent a bottleneck, as high quality hot-section used serviceable parts are rarely available.”
Stearns advises JT15D customers to allocate up to one year in to acquire a mid-time JT15D, “even if it sits on the shelf for months. The important thing is that you can get an engine you can fly for the next several years,” he notes. “Just don’t wait until the last minute, or your airplane will be sitting on the ground.”
Kyle Ballantyne, Honeywell Aerospace’s legacy turbofan product line director, reports that supply chain health has been improving throughout the year, and expectations are that will continue into 2024. Honeywell supports about 9,000 TFE 731 turbofan engines, and in excess of 10,000 TPE 331 turboprop units.
“Honeywell has been driving supply chain capacity improvements in collaboration with the supply base,” says Ballantine. “We established new supplier readiness and supplier development organizations, and have focused on rapid improvement, capacity expansion and establishing dual sources. In fact, we have generated double-digit volume supply year over year, yet demand has continued to grow at a faster rate.”
Specifically, Honeywell and its authorized service center network have collaborated to increase the USM supply through repair development and sourcing surplus engines to part out, in lieu of manufacturing new parts. “We have utilized our rental bank and USM across the Honeywell network to keep the fleets operating,” he says.
This article appeared in BCA's Q4 2023 issue.