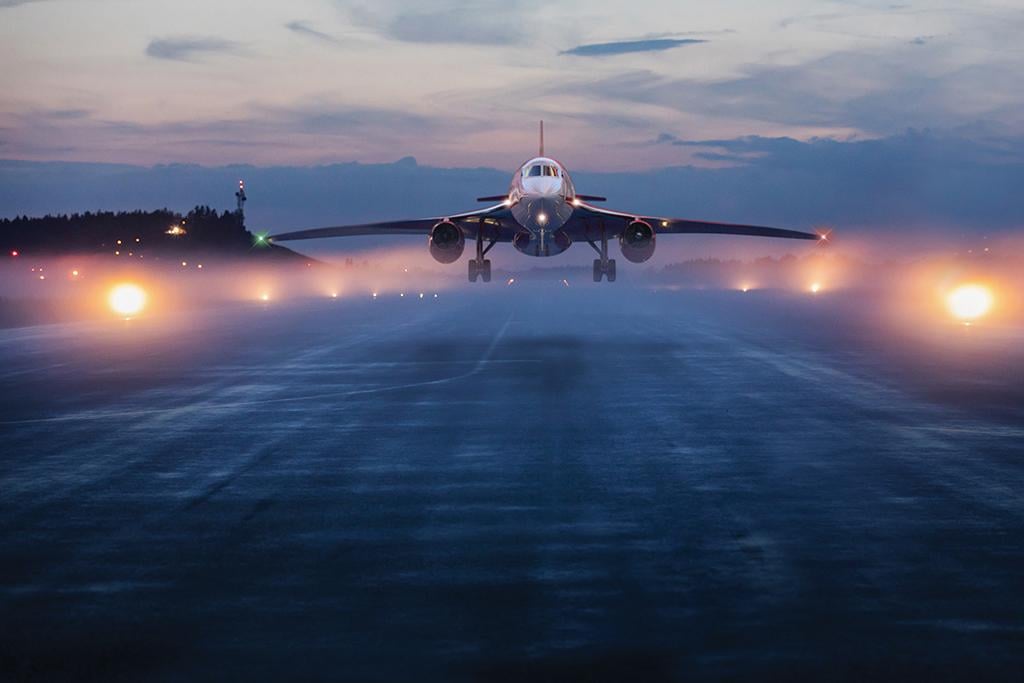
It’s the history of aviation. Go faster, higher, farther. So, imagine a world, a decade or more from now, when people can fly between most business destinations in 3 hr. or less. Leave New York at dawn, arrive in London in time for lunch, depart after 6 hr. of meetings and fly back to the U.S. East Coast for dinner with the family and help with the kids’ homework.
The transpacific trips take a little longer. Flying times from New York to Tokyo, Beijing and Singapore will require, respectively, 3.5, 3.6 and 5.0 hr. Westbound, travelers can leave after a late dinner and arrive home before brunch because of the time-zone changes.
Such thinking is emblematic of business tycoon and philanthropist Robert Bass of Fort Worth. “Audaces fortuna iuvat,” Latin for “fortune favors the bold,” could be his motto, as he took a $2.4 million inheritance and turned it into $5 billion through investments and partnerships in a wide array of industries. He’s a long-term business aviation advocate, having owned several subsonic jets, and in 2003, he made an audacious bet that business travelers would want to fly at double the speed of then-current-generation aircraft.
Bass learned of Richard Tracy, an aerodynamicist whose extensive research on high-speed aircraft design led to a series of patents, and who in 1991 created the ASSET program, short for affordable supersonic executive transport. He was intrigued at the prospect of bringing a Mach 1.6 supersonic business jet (SSBJ) to market that could cut as much as 3 hr. off trip times between Europe and North America. The ASSET SSBJ would cruise twice as fast as the Mach 0.80 large-cabin aircraft of the day.
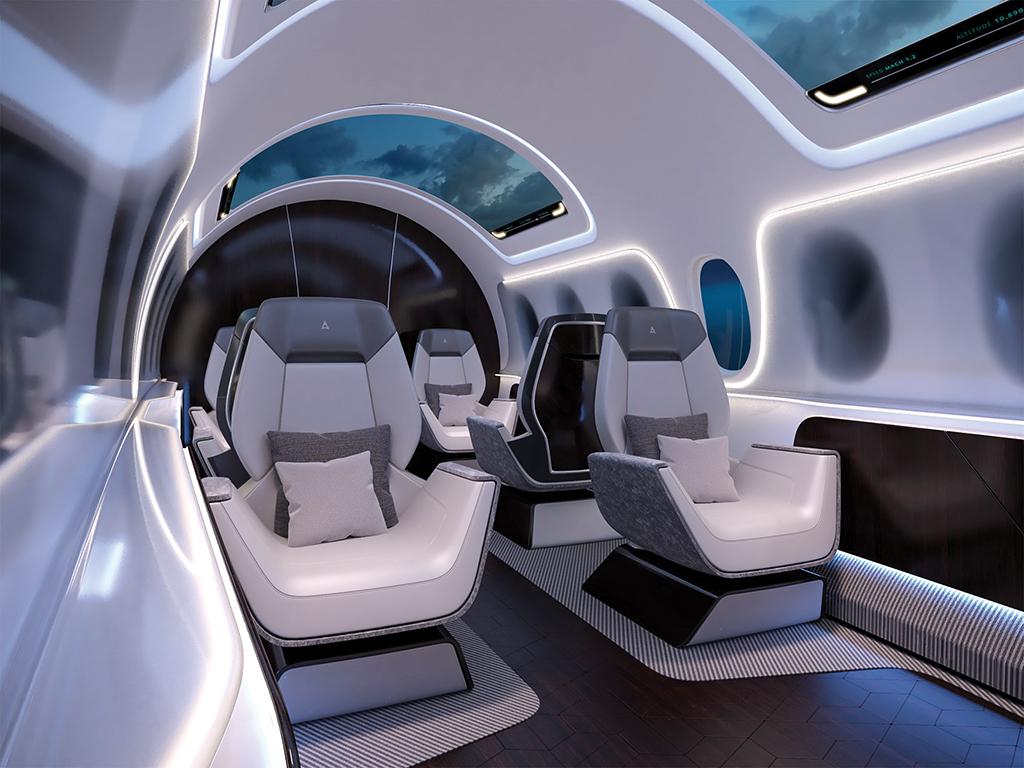
So, Bass formed an investment firm, bought Tracy’s ASSET Group and formed Aerion Supersonic in Reno, Nevada. The aircraft would be priced at $80 million, about twice the cost of the day’s average large-cabin, long-range business jet.
While not as swift as the Anglo/French Concorde, the ASSET SSBJ’s speed advantage over subsonic aircraft could slash more than 3 hr. off transatlantic trips. Maximum range would be more than 4,000 nm, sufficient to fly from New York to Sao Paulo, Paris to Washington or Rome to New York. The ASSET SSBJ would also consume one-fifth the fuel of the Concorde on such trips, due to its considerably smaller size and weight, advanced aerodynamics and twin-engine design.
Only months after Bass formed Aerion Supersonic, the Concorde made its final flight. The 100-passenger supersonic transport proved to be a technological marvel during its 27 years in operation, but never a commercial success; only 14 were put into passenger service. Without hefty government subsidies from the UK and France, the Concorde’s operating economics would have grounded it long before 2003. Its bottom line was its downfall. But operating expense would not necessarily discount the value of an SSBJ.
Notably, there is a far different time and money equation in business aviation than in for-profit airlining. “[It] is the value of time . . . [that’s leading] to increased interest in the feasibility of small supersonic civil aircraft,” wrote Pres Henne, then Gulfstream’s senior vice president for programs, engineering and test, now retired, in the May/June 2005 issue of Journal of Aircraft. Business travelers are willing to pay a price premium to save time. This was demonstrated when the long-range Gulfstream G650 was introduced. Its 30-35-kt. speed advantage over slower jets earned its manufacturer 400+ orders.
As for the prospects of a supersonic business jet, Henne wrote, “Once the concept has been proven on a small scale for the more affluent, then technical advances and commercial competition have typically led to larger-scale vehicles that appeal to a broader segment of the population.” An entry-level supersonic business jet carrying 8-12 passengers had the potential to reignite development of larger civil super-sonic aircraft.
Other, more-recent studies reinforce Henne’s conclusions. “The U.S. is experiencing a resurgent interest in civilian supersonic flight,” according to research performed by the Institute for Defense Analyses (IDA), a non-profit think tank in Washington. The IDA’s research study was commissioned by the White House Office of Science and Technology Policy in November 2018 to determine if, how and when the federal government might support civil supersonic flight.
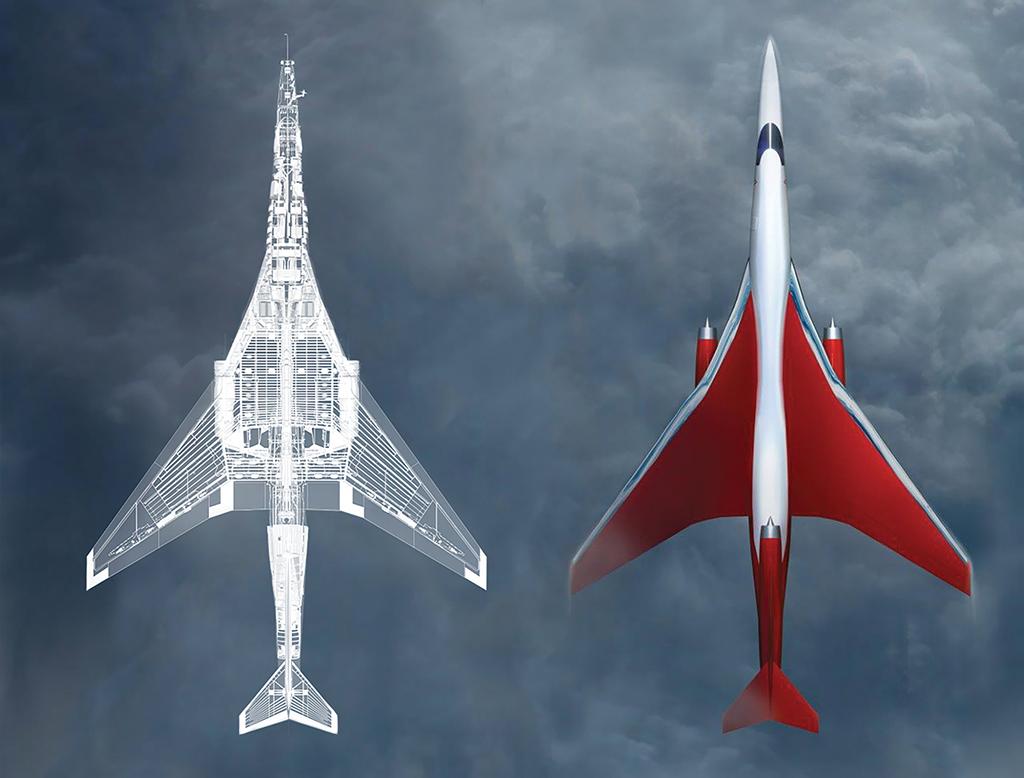
The renewed interest is being fueled by 50 years of advances in engines, materials, design tools and flight control technologies that hold promise to make supersonic flight far safer, more efficient, more economical and more practical than it was when the Concorde and Russian Tupolev Tu-144 supersonic transports were designed, according to the IDA.
In part as a result of the IDA’s report, the FAA issued a Notice of Proposed Rulemaking (NPRM) in mid-2020 that floats the idea of incorporating new supersonic aircraft, certified to be operated at Mach 1.8 or below and with MTOWs of 150,000 lb. or less, into revised FAR Part 36 noise standards.
The IDA makes reference to the Diffusion of Innovations principles advanced by Everett Rogers, an eminent American communication theorist and sociologist. These hold that once about one in 40 people embrace a concept or technology, it starts to overcome market inertia and achieve widespread acceptance by “early adopters,” a term he created. The 2.5% so-called innovators will pay a price premium to gain access to the latest technologies. Tesla automobiles, iPhones and LCD big screen TVs all were made popular by early adopters who paid top dollar at the time these breakthrough inventions came to market. Newer derivatives typically are bigger, more capable and less expensive.
Climatic Challenges, Opposition
Electric cars, cellphones and giant-screen televisions, though, don’t have the high-profile, atmospheric influence and thus controversy of supersonic aircraft. The IDA report cautions that “[d]espite anticipated technical advancements, the physical realities of flight in this regime are such that supersonic aircraft are still likely to have a greater environmental impact [in terms of noise and emissions] than their subsonic counterparts.”
There’s considerably more pressure to “go green” today than when the Concorde made its debut. When environmental activist Richard Wiggs founded the Anti-Concorde Project in 1966, he had few followers. Now, the “flight shaming” movement, started in Sweden, has strong following around the planet and new supersonic aircraft will become prime targets. In August 2020, a consortium of 62 climate change, environmental and public health organizations, including the Center for Biological Diversity (CBD), Natural Resources Defense Council and Earthjustice, blasted the FAA’s plan to revive supersonic aircraft.

“The Trump administration’s plan to revive these super-polluting planes is a huge threat to our climate and the air we breathe,” says Clare Lakewood, legal director at the CBD’s Climate Law Institute, a non-profit group with 1.7 million members. “We need rules that protect our air and climate from aviation pollution, not ill-conceived efforts to revive a particularly dirty form of transportation,” she says, citing a 2019 study by the International Council on Clean Transportation that claims a new fleet of SSTs would emit more than 100 million tons of carbon emissions each year.
Pressure from environmentalists doubtlessly will accelerate the aviation community’s transition from fossil fuels to synthetic fuels, either derived from plant or algae biomass feedstocks or by combining carbon dioxide harvested from the atmosphere with hydrogen. The goal is to make aviation carbon neutral by 2050.
However, even using 100% carbon-neutral fuel, supersonic aircraft will burn considerably more of it and create proportionately more water vapor as a byproduct of that combustion. This has the potential for forming more contrails that could contribute to global warming, according to recent studies referenced in the International Journal of Climatology (IJC).
“The artificial cloudiness generated by contrail outbreaks alters the atmospheric radiation budget, potentially impacting the surface air temperature, particularly the diurnal temperature range (DTR), or difference between daytime maximum and nighttime minimum temperatures,” wrote Jase Bernhardt and Andrew Carleton in a March 2015 IJC report.
Environmental concerns notwithstanding, a renewed focus on supersonic airplanes is likely to bring attention to ground travel times between office or home and the airport as well. After all, what’s the net benefit in reducing the flight time from New York to London to 3 hr. if you spend 1.5 hr. at each end in a taxi? Should Aerion or other supersonic business jets actually enter service, they are likely to boost point-to-point urban air mobility (UAM) vehicles, a segment now drawing considerable investment and technological development, because they hold the promise of slashing travel times between launch points and airports by 80%, or more.
Environmental, political, financial and other challenges aside, market studies by Gulfstream, Meridian, Teal Group and Rolland Vincent Associates, among others, indicate there will be market demand for 200-500 small supersonic aircraft over the next 20 years.
With today’s technologies, there are no showstoppers to building and certificating a viable supersonic business jet. The real challenge is finding ways to satisfy all the present-day competing needs and concerns, ones that have changed greatly in the past two decades. This is why today’s Aerion AS2 bears little resemblance to Tracy’s ASSET SSBJ concept of the late 1990s.
Learning From History
“Malum consilium quod mutari non potest,” roughly translated from Latin as “bad is the plan that cannot change,” is another apt descriptor for development of the Aerion AS2. The original plan was to build a lean, twin-engine aircraft with 4,000+ nm of range.
During the past two decades, the aircraft has been through at least a half dozen major design iterations, now making it a considerably more mature design with attainable performance targets. It’s also one of the longest-running aircraft development programs in the history of business aviation, so it’s useful to look at its history.
When Bass started to invest millions of his own dollars in Aerion, he hired Brian Barents, a well-respected veteran executive with successes at Cessna, Learjet and Galaxy Aerospace, and charged him with advancing the aircraft to market. Bass’ plan was to mature the technology, line up risk-sharing partners and team with a major general aviation airframe manufacturer for final design, development, certification and production. Board members included Bass as chairman, Barents as vice chairman, Tracy as chief technology officer, Michael Henderson, the former program manager for Boeing’s high-speed civil transport program, as COO and Robert Morse, a partner at Bass’ Oak Hill Capital.
For the first three years, Aerion quietly conducted market research, accomplished preliminary design work and gauged vendor interest. The program was formally unveiled at the October 2004 NBAA annual convention. Detailed design work was scheduled to begin in 2005. Once all risk-sharing partners were aboard, Aerion planned for a five-year development program. Entry into service was slated for 2011.
Tracy’s ASSET SSBJ was a low-risk design, the aircraft to be constructed from conventional materials and using proven systems. He chose aluminum alloys for the fuselage and carbon-fiber reinforced composites for the wings. It was to have a 17-ft.-long, two-section main cabin with a 5-ft.-long galley up front. The aft cabin would have had a super-midsize cross-section aft, tapering to a midsize cross-section up front, affording seating for eight passengers, 12 people in a pinch if the galley was converted into a seating area. The svelte, but 145-ft.-long ship was intended to have per-mile operating costs that would be competitive with large-cabin business aircraft having similar 4,000+ nm range, such as the Bombardier Challenger 604, Dassault Falcon 900C and Gulfstream GIV-SP.
Two critical enabling technologies would make possible the Aerion SSBJ. First, Tracy capitalized on his 1964 Ph.D. from Caltech in hypersonic aerodynamics to design a revolutionary supersonic laminar flow, trapezoidal shaped, 1,400-sq.-ft. wing that would improve lift-to-drag performance by 20% over older, highly swept delta wings, such as that used on the Concorde. A scale section of his wing was tested on an F-15 at up to Mach 2 to prove its
efficacy.
Second, the Aerion SSBJ would piggyback on an improved version of the popular and proven low-bypass JT8D turbofan engine. Pratt & Whitney was developing a JT8D-219 upgraded turbofan for re-engining the U.S. Air Force’s fleet of Boeing 707s modified as E-8 J-STARS (Joint Surveillance Target Attack Radar System) aircraft that would have considerably higher temperature margins. This allowed for a 3,000-hr. TBO for the -219s intended for the Aerion.
Aerion hired Rolland Vincent in 2004 to conduct worldwide market research as to the viability of the initial concept. More than 100 business aircraft operators were interviewed and presented with a variety of designs. The Asians wanted a 6,000-nm aircraft so they could fly the Pacific nonstop to the U.S. The Europeans supported a 5,000-nm aircraft for missions to most major U.S. cities, including ones on the West Coast. U.S. operators wanted at least 4,500 nm of range. Virtually all who participated in the survey said they wanted a larger cabin, an improvement later incorporated into the design. They also insisted on incorporating an integral airstair for the main entry door and high flow rate, single-point pressure refueling capability for quick ground turns.
By mid-2007, Aerion was still searching for risk-sharing partners at the Paris Air Show. Program cost had ballooned to $2 billion and the projected entry-into-service date slipped to 2013. The revised plan, however, was snuffed by the 2008 Great Recession, as potential program partners pulled in their reins and attempted to survive the extreme economic turbulence. Skies became even stormier in 2011 when the Joint Stars reengining program was canceled. This effectively killed Pratt & Whitney’s development of the upgraded -219 turbofan, leaving Aerion in search of a suitable engine to serve in its place.
Undaunted, Bass continued to support the program, ultimately leading to the second-generation AS2, a trijet design announced in May 2014. MTOW was bumped to 121,000 lb. from 90,000 and fuel capacity increased to 62,000 lb. from 45,400. Range was increased to 4,750 nm at Mach 1.4 and 5,300 nm at Mach 0.95. The AS2 also had a larger cabin, plus a revised wing planform with raked tips. Overall length was increased o 170 ft. from 145, nearly 60 ft. longer than a BBJ. The AS2’s unprecedented tip-to-tail distance was bound to create ground-handling challenges at general aviation airports, particularly on congested FBO ramps. The price soared to above $100 million.
Aerion’s fortunes appeared to reverse in September 2014, when Airbus’ Defense and Space unit agreed to collaborate on AS2 development and industrialization. Airbus was keenly interested in Tracy’s supersonic laminar flow wing technology, even though the French consortium wasn’t interested in building a next-generation supersonic transport. Toulouse engineers believed Tracy’s revolutionary airfoil might open the door for a new generation of jetliners that would cruise at Mach 0.95-0.99 on less fuel than conventional airliners at Mach 0.785.
Bass called the collaboration “a major step forward.” With Airbus’ support, Aerion then targeted 2019 for first flight of the AS2 and certification in 2021. Aerion officials claimed Airbus’ support “decisively kicks the program into high gear.” Company officials conceded that $4 billion would be needed to bring the aircraft to market.
Aerion opened its order book in June 2015, pricing the aircraft at $120 million, and at the November 2015 NBAA Convention, Kenn Ricci, chairman of Direction Aviation Capital, announced an order of 20 AS2 SSBJs to be placed in service with the firm’s Flexjet fractional ownership unit, thereby becoming the first fleet customer. However, Aerion acknowledged that first flight of the AS2 again had slipped to 2021 with entry into service in 2023.
Little more than three years into the joint venture, Airbus bowed out. Lockheed Martin was enlisted in December 2017. Lockheed/Lockheed Martin had extensive experience building supersonic military aircraft, including the F-104 Starfighter, SR-71 Blackbird and F-22 Raptor. But as one former advisor to Aerion notes, Lockheed’s success in building commercially successful civil transports has been checkered at best during its entire history.
Hyperspeed Leap for AS2
Aerion underwent a step change in March 2018. Barents, with Bass’ blessing, recruited Thomas Vice, then recently retired as president of Northrop Grumman’s Aerospace Systems unit, to join Aerion as president and chief commercial officer. Vice left Northrop Grumman in 2017 when it became apparent that Kathy Warden, not he, would be tapped to lead the company. After 31 years with Northrop, it was a bitter disappointment.
Vice left with a multimillion-dollar severance package, but while he was financially set for life, he was not finished with his engineering career. He “wanted to work on the next big revolution,” he posted on his LinkedIn page, noting he “joined Aerion to revolutionize global mobility.” He added that he’s “always had a passion for engineering and fast machines.” In August 2018, Aerion Corp. appointed Vice as chairman, president and CEO. Bass and Barents both left the board.
Under Vice’s leadership, the AS2 program was about to undergo a major makeover. He enticed Boeing to become a venture partner in early 2019, knowing then-Boeing CEO and President Dennis Muilenburg was keenly interested in civil supersonic aircraft. Boeing engineers continued to study supersonic transport designs well after the company’s Mach 3 Boeing 2707 was canceled in 1971. In return for its investment, Boeing succeeded Lockheed Martin and landed two director positions — Mike Sinnett, Boeing’s vice president of product strategy and future airplane programs, and Ken Shaw, vice president of supply chain at Boeing Global Services.
Aerion and Boeing almost immediately shelved Tracy’s supersonic natural laminar-flow wing design, concluding that while it reduced wave drag by 20% at high speed, it wasn’t the best solution for subsonic and transonic “boomless cruise” speeds. The team decided on a cranked arrow wing design, one that provides a better balance of performance and drag characteristics. “Laminar flow does have a significant benefit, if you’re only going after [shock] wave drag,” Vice said. “But the new cranked arrow wing has the best lift-to-drag performance of any [supersonic] wing I’ve seen. It has almost all the benefits of a variable geometry wing, but without the weight penalty.”
The cranked arrow airfoil was developed using a new set of 3-D computational fluid dynamics (CFD) design tools that Aerion created in house. “We had to solve optimization of the wing because we couldn’t find the design tools out there,” Vice explained. “Now, we have so much data that we had to bring machine learning into the optimization tool set.”
Other major changes include putting the wing-mounted engines into underslung nacelles with cylindrical inlets and exhaust nozzles, adding variable geometry to both ends. (See “GE Affinity Turbofans to Power AS2” sidebar.)
Today’s version is expected to be half again as heavy as Tracy’s original ASSET design, have a third engine, fly farther and have a more comfortable cabin. Major changes include wing shape and aerodynamics, choice of engines, nacelle and fuselage loft contours, as well as cabin cross-section. As of mid-2020, all of the major suppliers were on board and are all top-tier aerospace firms, including GE Aviation for engines and electrical power distribution, Honeywell for avionics, BAE Systems for digital flight controls, Collins Aerospace for actuators and Safran for landing gear, brakes and nacelles.
Two ground-test articles are planned and five fully conforming flight-test aircraft will be used in the certification program. Aerion plans to break ground on a new headquarters facility, complete with flight test center and manufacturing plant, in Melbourne, Florida, by year-end. In short, the AS2 is far closer to becoming a reality.
Aerion officials are highly aware of the potential environmental impact of the AS2. Accordingly, they have committed to making the aircraft carbon neutral from its first flight. It will be constructed from renewable, sustainable materials wherever possible. Its new Aerion Park campus in Florida will be powered by “clean energy” and have the goal of emitting zero waste. The airframe, systems and engines are being designed to use synthetic fuel, but the aircraft will also be able to use fossil fuel, if needed. Vice says Aerion intends to plant 100 million trees by 2036 to offset the total emissions of 300 AS2 SSBJs in operation.
Maturing of the design has caused Aerion to rein in some performance goals. Vice now predicts that the AS2 will fly 4,200 nm at Mach 1.4, 5,400 nm at Mach 0.95 and 3,500 nm at “Boomless Cruise” Mach 1.1-1.2 cutoff speeds, where its shockwave dissipates before reaching the ground. Mach cutoff banks on an atmospheric phenomena called the “caustic layer,” a relatively low altitude level at which mild shockwaves are refracted into dozens of small shocks that deliver no perceptible noise on the ground. The big challenge is modeling atmospheric temperature changes, wind, humidity and other factors that influence shockwave refraction. This will potentially require the AS2 to change its super-cruise Mach speed dynamically during flight to assure that no perceptible sonic boom that it creates reaches the surface.
The airplane routinely will cruise at FL 570-600, altitudes not attained by any civil aircraft except for the Concorde. Flight time between most business destinations will be 3-5 hr., such as London to New York, Montreal to Moscow and Paris to Chicago. The AS2 will shave off 2-4 hr. from most transpacific trips, even with a 1-hr. refueling stopover in Anchorage or Honolulu.
The biggest obstacle is money. The firm already has more than $500 million invested. Insiders believe it will take a total of $5 billion to get it to the finish line, 25% more than the firm predicted in 2018. Boeing and Spirit AeroSystems have suffered setbacks as a result of the Boeing 737 MAX grounding and the COVID-19 deep recession, causing them to pull back financial support for the AS2 and even to dissolve their engineering teams at Aerion.
Vice now forecasts first flight in 2025 and entry into service in 2027. Vincent’s projections push out entry into service until 2029.
Is it worth the wait? Vice believes he can sell as many as 300 AS2 SSBJs during its first decade of production, bringing in as much as $40 billion at retail prices. He also believes the AS2 is just the first step in returning supersonic aircraft to the civil market and envisions a world where travel distance no longer is a barrier. He also believes innovation can solve environmental issues, most particularly sonic boom and carbon impact. Future Aerion supersonic aircraft will cruise faster and farther than the AS2, as well as carry more people. Commercial SSTs are in Vice’s plan, ones with the net carbon footprint of Bertrand Piccard’s Solar Impulse.
Even if Vice’s plans at Aerion for a new generation of SSBJs and SSTs prove too ambitious, his Bob Bass-like “Go Big or Go Home” leadership approach will pay long-term dividends for the business aviation community. Environmental activists will continue to crank up the pressure on the aviation industry to slash or eliminate emissions, even though aircraft account for only 2.4% of the world’s CO2 production. Plainly stated, business aircraft emit considerably more emissions per seat mile than jetliners, even though they only make up 2% of all aircraft emissions — 0.048% overall.
If the business aviation community zeroes out its net emissions by switching to 100% synthetic fuel and planting new forests to absorb CO2, it can pride itself on doing its part to help heal the earth. If new subsonic business aircraft can be built from renewable materials in manufacturing plants that emit near zero waste, future generations will laud the progress.
When Tom Vice talks about “disruptive change” at Aerion, it is not just about speed. It’s also about a revolutionary approach to how all aircraft can be built, operated and recycled so as to be kinder to the planet. That’s a worthy goal all by itself.
Comments