Opinion: Suppliers Go From Just In Time To Just Don’t Know
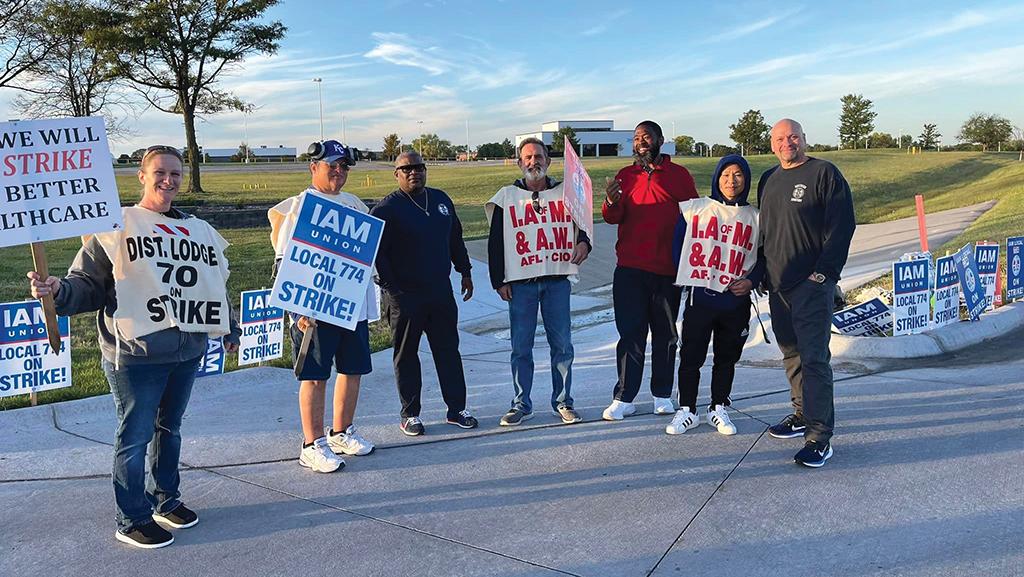
International Association of Machinists & Aerospace Workers Local 774 members on the strike line at Textron Aviation in Wichita in September.
Credit: International Association of Machinists & Aerospace Workers
Misaligned supply and demand, now exacerbated by the International Association of Machinists & Aerospace Workers strike at Boeing, continues to affect the supply chain in a profound way. Production master schedule changes by the airframe OEMs are obfuscating production rates and spurring suppliers...
Opinion: Suppliers Go From Just In Time To Just Don’t Know is part of our Aviation Week & Space Technology - Inside MRO and AWIN subscriptions.
Subscribe now to read this content, plus receive full coverage of what's next in technology from the experts trusted by the commercial aircraft MRO community.
Already a subscriber to AWST or an AWIN customer? Log in with your existing email and password.