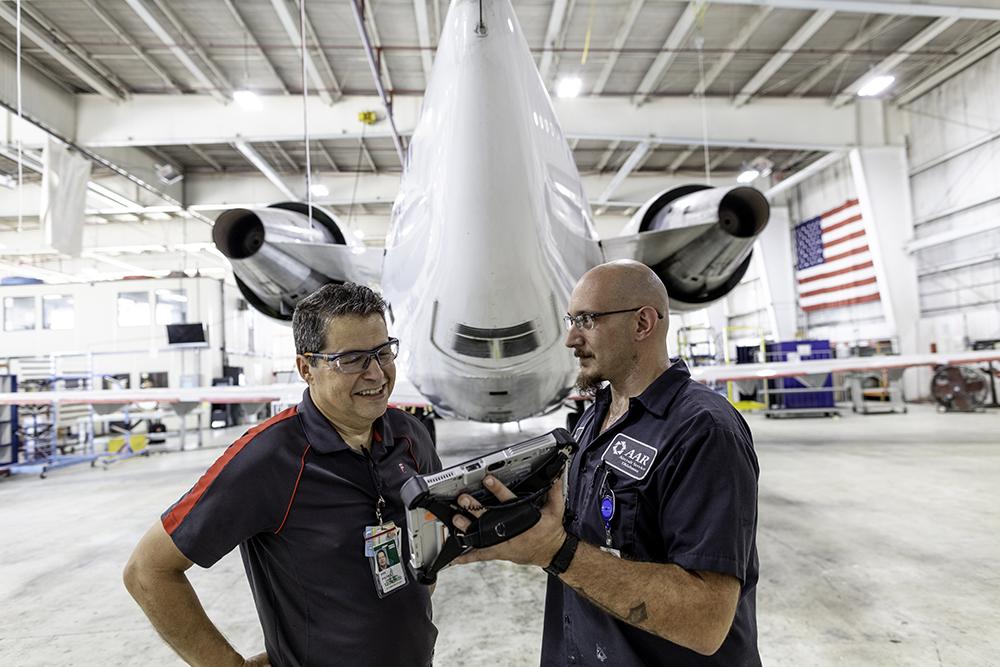
AAR has adjusted technician work schedules to offer more weekends off in response to workforce pressures.
MRO industry stakeholders have long felt the pressure of the technician shortage, but as maintenance demand ramps up and companies struggle to meet their growing workforce needs, the changing labor landscape is presenting new challenges.
U.S.-based maintenance provider AAR Corp. said in its recent 2023 Mid Skills Gap Report that the traditional technician career pathway—in which new graduates start at repair stations before progressing to airlines—is becoming less common as companies struggle to find qualified talent. The report says major airlines are beginning to hire and train mechanics right out of school rather than following the natural career progression, which is causing problems for independent MRO providers.
“I kind of think of AAR as the minor leagues of baseball,” explains Ryan Goertzen, vice president for workforce development at the company. “We get technicians and grow their experience, usually on a customer’s airplane, and then they eventually go to work at the customer. The problem today is you can’t do that because there are not enough people. You ultimately end up hurting yourself as a major air carrier because you’re hurting your MRO provider.”
Considering this changing trend, Goertzen stresses the importance of workforce collaboration between MROs and airlines, such as making flow-through agreements and leveraging an airline’s brand to attract new talent.
AAR currently has about 200 open positions at its U.S. repair stations, and it is hoping to create up to 600 new positions in the next few years. So it has needed to pursue new hiring avenues, including seeking out international talent from Latin America. “We’ve had some really good luck using the United States-Mexico-Canada agreement to get some technicians from Mexico, as an example, into and throughout our various MRO facilities,” Goertzen says.
AAR’s report notes, however, that work visa restrictions in the U.S. have limited its efforts to improve this situation, compared with more flexible immigration policies in Canada that include a pathway to citizenship. The company currently has technicians from 29 countries working at its Canadian repair stations.
Goertzen says AAR recently partnered with the Teamsters Union to speak with legislators and immigration reform experts on Capitol Hill about ways to spur change in federal policy that would make it easier for U.S.-based MRO providers to hire international talent. He stresses that the idea is not to recruit cheaper labor or replace American workers but to fill gaps created by the shortage of homegrown technicians. Goertzen also notes that hiring skilled talent from abroad would enable MROs to accelerate hiring of new graduates.
“For every highly skilled technician I bring in, I can usually bring in something like 3 to 5 relatively new technicians to grow along this pathway together,” he says. “The argument is that we would actually accelerate U.S. technician growth by having some more skilled people to leverage in the facility.”
Net-Generation Workforce Demands
Meanwhile, AAR has also needed to rethink how it operates in order to manage workloads efficiently with fewer technicians. It has moved to what it calls a “total facility crew approach,” which divides work into four 10-hr. days, depending on the lines of maintenance, with a small crew on weekends. The report also notes that strong technician preference for weekends off prompted it to adjust schedules and workflows.
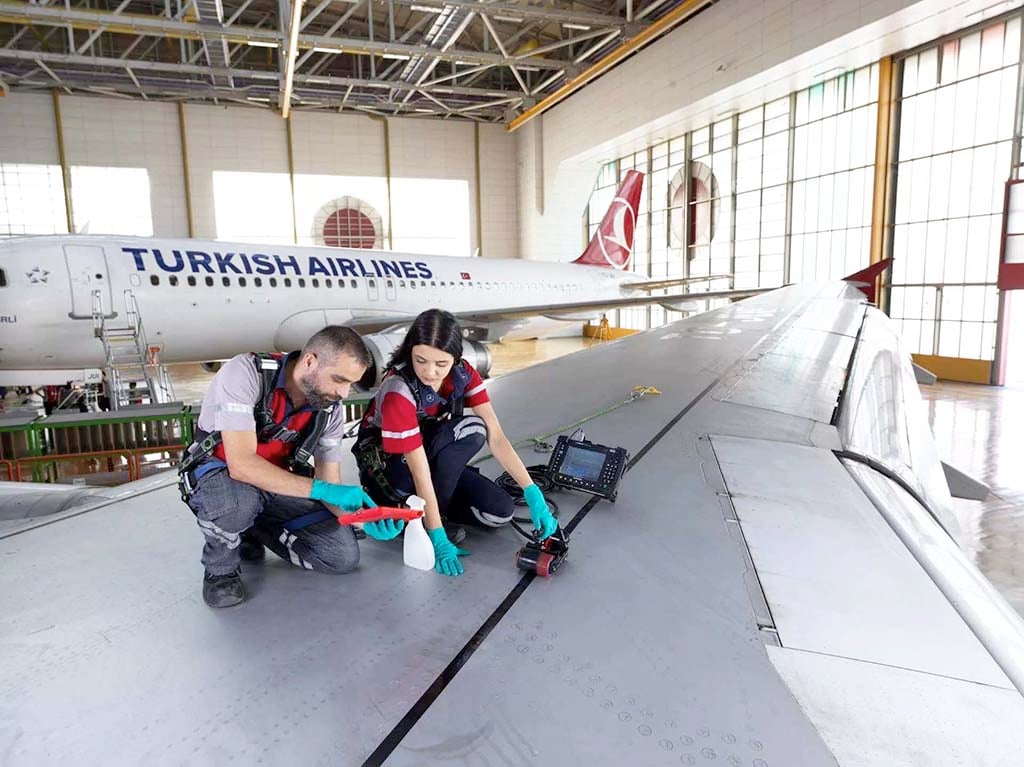
“People were leaving and even taking a pay cut to get weekends off,” says Stan Mayer, vice president for operations at AAR Airframe Services in Oklahoma City. “Now everyone has three weekends a month off and works one weekend.”
Goertzen adds that the company has been forced to confront growing demands for higher flexibility post-pandemic. “We’re a 24/7 kind of operation, so there’s only so much flexibility [we can offer]. You can’t do maintenance from home, but we are doing what we can to keep and retain the best talent by providing some opportunities to do flexible scheduling,” he says.
At Aviation Week’s recent MRO Europe conference in Amsterdam, panelists considered ways in which industry can respond to changing attitudes about work-life balance, particularly among younger generations.
Jonas Murby, a principal at consultancy AeroDynamic Advisory, argues that the MRO industry’s growth will require it to capture labor market share from other industries. “This is a time where you have emerging technologies in other areas that appear more attractive to the young generation, so we really need to reinvent the jobs of technicians to fit the new generation,” he said. “The next generation wants to enjoy life. They don’t want to work night shifts, and they want to work from home.”
Murby also suggested that interest in technology among younger workers could provide opportunities to tackle these types of issues. “[Younger generations] live in a different digital dimension, and we need to take that into account as well,” he said. “How can you redesign a technician job to work from home?” One potential remote- work use case Murby cited was the ability for technicians to review drone-based aircraft inspections from home. He also suggested that incorporating technologies such as augmented and virtual reality into training could add flexibility. However, he cautioned that training itself has become a precarious business for some companies.
“I spoke with an airline in Europe a few weeks ago and they said they lose 80% of their technicians in training. And then you don’t know how long the rest of them will stay, so it’s a really profound problem,” said Murby.
Bilal Karaman, senior vice president for aircraft maintenance at Turkish Technic, noted that recruitment has not been as difficult for the MRO provider, but enticing technicians to stay long-term has become tricky. “In Turkey, working in aviation is still trendy among young people, so we don’t have a big problem recruiting, but keeping this new generation interested in working in the same job for 30-40 years is a challenge,” he said.
Karaman argues that continuing to increase salaries alone will not solve the problem. “That just makes people temporarily happy and then they’re benchmarking again. The problem is the newer generation just doesn’t want to work in the same job for 30 years,” he said. “They get bored, and when people are bored they either leave the company or—what is maybe even worse—they stay and we have an inefficient worker who’s always complaining and doesn’t do their job. So we try to keep people motivated.”
One way in which Turkish Technic is engaging younger employees is through a portal that enables staff to pitch ideas about how to improve maintenance practices and the overall workplace. Karaman said Turkish Technic receives more than 700 submissions through the portal every year.
Recent Workforce Initiatives
Aviation industry companies have lately launched an assortment of initiatives to attract and train talent. In Florida alone, several new partnerships are driving significant opportunities for future MRO workforce growth.
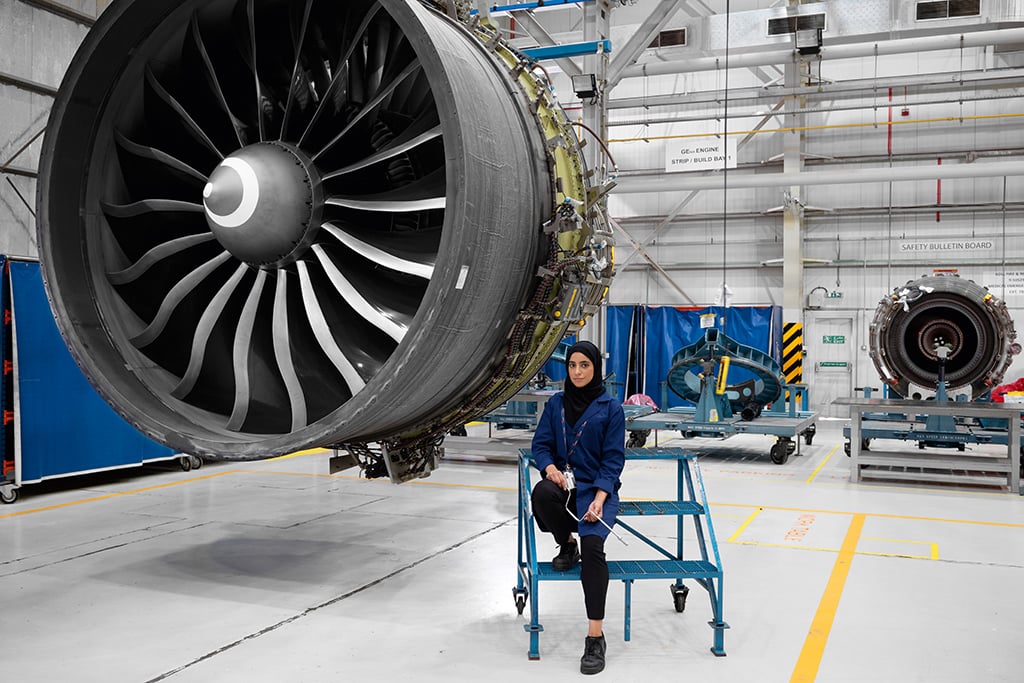
E-commerce giant Amazon partnered with Florida-based Part 147 school International AeroTech Academy this fall to offer a career training program for maintenance technicians. Steven Markhoff, president and CEO of International AeroTech Academy, says the program has already grown significantly since it began offering classes in September.
“The response from Amazon employees in the area has been unbelievable. We have a long wait list of Amazon employees that are signing up now for our next class,” Markhoff told Aviation Week in October.
At Miami-Opa Locka Executive Airport, Barrington Irving Technical Training School launched a specialized workforce development program in which its Flying Classroom—which previously focused on STEM education for children and teens—will begin offering aviation technical training to adults. In addition to training in areas such as aviation maintenance, adaptive manufacturing, and composites and sheet metal, the program also teaches soft skills such as financial literacy, time management and leadership.
AAR and nonprofit Choose Aerospace, which has been developing an aviation maintenance curriculum that could be implemented in high schools, are also working to expand workforce initiatives in South Florida to help the company support a new three-bay hangar facility. AAR is working on a memorandum of understanding with Florida Memorial University to launch Choose Aerospace’s general aviation curriculum at the school and to help it establish its first maintenance program in conjunction with Miami-Opa Locka Executive Airport.
At last month’s Dubai Airshow, several maintenance providers in the Middle East announced training and workforce initiatives to develop talent pipelines in preparation for the region’s significant MRO industry growth.
Etihad Engineering announced a new technical training facility at Abu Dhabi International Airport that will enable it to offer 400 more courses per year to an additional 6,000 trainees.
Lufthansa Technik (LHT) and Saudia Technic are introducing a joint training program in January 2024 in which Saudia technicians will receive immersive training at LHT’s facilities in Dubai and Hamburg.
Sanad, which is building up capacity to service more engine types and expand into new maintenance segments, recently launched its Future Leadership Program. The program selects local students to attend what Sanad CEO Mansoor Janahi says is one of Europe’s top business schools, identify relevant business issues and present a capstone project to the MRO provider.