Repair Cycle Services Bring Turnaround Time Guarantee Opportunities
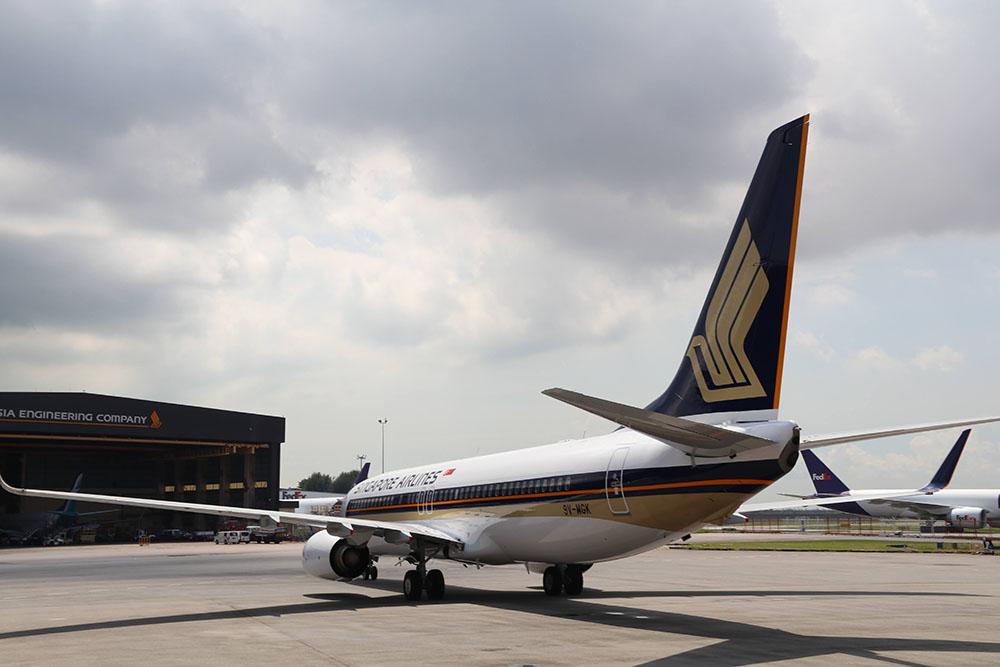
Singapore Airlines recently extended its repair cycle management services contract with Airinmar.
Experts detect rising demand for component repair cycle services and proactive turnaround time management in response to continuing cost and supply pressures.
In September, component specialist Airinmar extended an agreement with Singapore Airlines, indicative of the continued appeal for repair cycle management services, especially in the last 18 months, reveals Matt Davies, Airinmar’s general manager.
Airinmar’s services are designed to consolidate repair management, improve turnaround time (TAT) and reduce repair cost. Davies believes the supply chain challenges the industry has experienced over the last few years have contributed to this demand, particularly with the shortage of expertise and the pressure on costs.
“It’s important to note that our repair cycle management services are not a one-size-fits-all solution, so when an operator is considering such a service it could be for a variety of reasons,” Davis says.
For example, Airinmar can support the efficiency of an airline’s in-house repairs team by utilizing its consolidated quote management portal, which means dealing with one service provider versus 200-300 different suppliers, the company states. Further, an airline could consider such services to reduce maintenance expenditure by utilizing engineering services that assess and reduce the costs of components repairs with their pre-existing approved suppliers.
According to Davies, complications in the supply chain have presented opportunities and threats alike. “As far as opportunities go, higher repair costs mean our services to reduce repair cost on a no-win no-fee basis become even more valuable to airlines,” he says.
Conversely, he believes supply chain disruptions that led to worldwide part shortages have created more workload for supplier managers tasked with finding solutions and mitigating risks.
TAT guarantees in the current environment can be difficult to attain, but Davies says the three key elements of TAT guarantee enforcement are the contracts, data and persistence. He notes that the quality of data and Airinmar’s ability to persistently follow-up on claims and remedies has been largely unaffected in the current environment.
“The contractual language of any TAT guarantee is fundamental to your ability to enforce it; unambiguous language setting out expectations and remedies is critical for holding the supplier to account,” Davies says.
However, Airinmar still sees some OEMs applying force majeure on their TAT guarantees due to impacts from the pandemic and the war in Ukraine on labor and material supply. “It is our job to assess any reason given for rejecting a TAT guarantee remedy and working that through with the supplier,” Davies says.