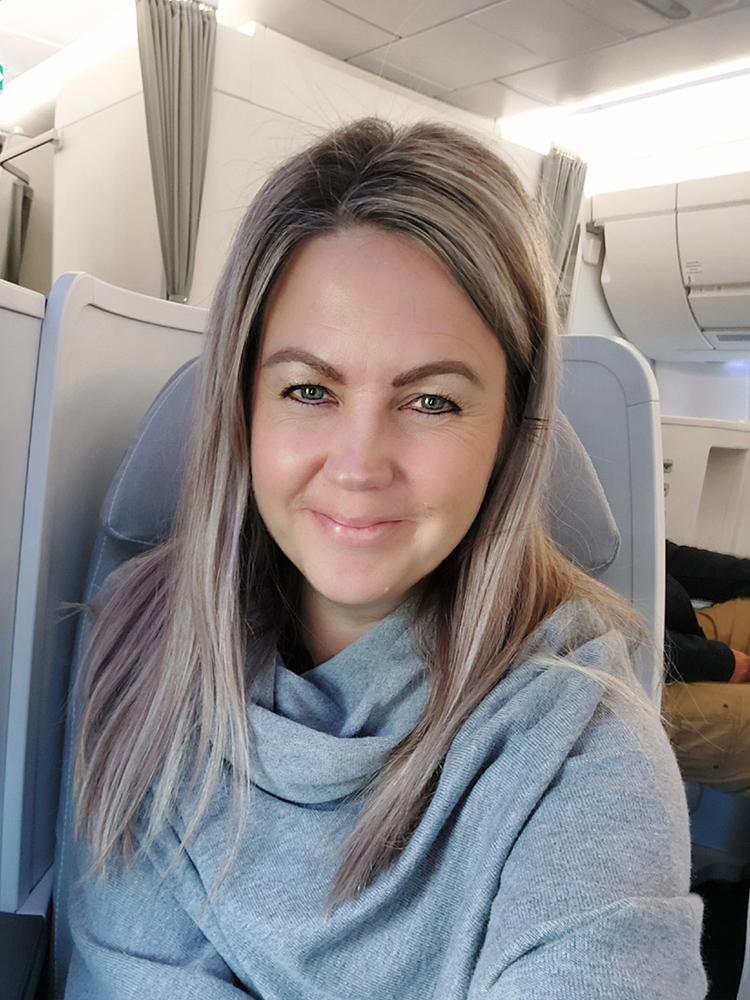
Mervi Moldakainen, director of technical procurement at Finnair
Mervi Moldakainen, Finnair’s director of technical procurement, speaks with Aviation Week about aftermarket supply chain trends and the new technologies the airline is looking at for aircraft maintenance.
What is Finnair’s key priority in terms of technical procurement?
There is no doubt about our number one priority, which is safety in everything we do, both within our own organization and with our partners. We will not compromise on that. We value technical reliability, quality and cost-effectiveness and ensuring availability of technical maintenance services to support seamless airline operations, so this is one of our ongoing priorities. In addition to the above, we value punctuality, and a reliable supply chain.
Are you seeing any notable trends with supplier behaviors in 2024?
Aircraft maintenance markets remain hot. The supply chains suffer from resource constraints that limit business growth in different regions and ultimately drive-up costs, and different suppliers are competing for the same workforce. The worst inflation is receding in Europe, but strong demand for services continues to impact price levels upwards. The high trend in OEM supplier escalation rates will continue in 2024, and long spare part lead times have led us to consider various contingency mechanisms.
How are you collaborating with MROs, and how is this influencing buying decisions?
It is important to know your partners well. We value close, long-term and reliable partnerships. Good relationships with open communication are invaluable, especially during disruptive events that might otherwise be challenging to resolve. In our experience, it is worth building long-term relationships rather than changing MROs constantly. Apart from this, we strive to keep our market knowledge up to date, by monitoring how MROs are developing in different regions and extending their capabilities. We aim to improve safety and productivity in collaboration with our suppliers, developing processes together in ways that deliver mutual benefits in our business relationship. For all kinds of sourcing projects, we prefer a partner who is willing to develop and perhaps an opportunity to expand their collaboration with us with a wide range of services. Innovative pricing models with mutual risk sharing mechanisms are always attractive. Sustainability has become one of the strategic themes for Finnair and nowadays it is on the agenda with all our supplier relationships. On sustainability matters we all can share and learn the best practices together.
How are you using new technologies to advance technical processes for aircraft maintenance?
Finnair is increasing and utilizing digital information sharing and recordkeeping as we move toward paperless maintenance processes. The development of digital interfaces between different systems to facilitate the flow of information supports these efforts. We are always keen to adapt to new technologies and, for example, we are currently investigating piloting 3D printing capabilities, machine vision technologies and drones in our technical operations. Learning to use artificial intelligence in predicting more detailed maintenance requirements for an aging fleet would be interesting and we are always keen to learn more.
From an airline perspective, how are you responding to high costs in the aftermarket?
We take advantage of our long-term contracts and supplier cooperation. In best cases, Finnair has been able to find win-win solutions with our suppliers by streamlining operations and reviewing the extent of the work scopes. In parallel, we make more use of market research, aviation (MRO) events and data. In some categories, we have started to source services from outside of our region and expand to new areas. Procurement project costs are based mostly on total cost and productivity rather than individual project or service price tags.