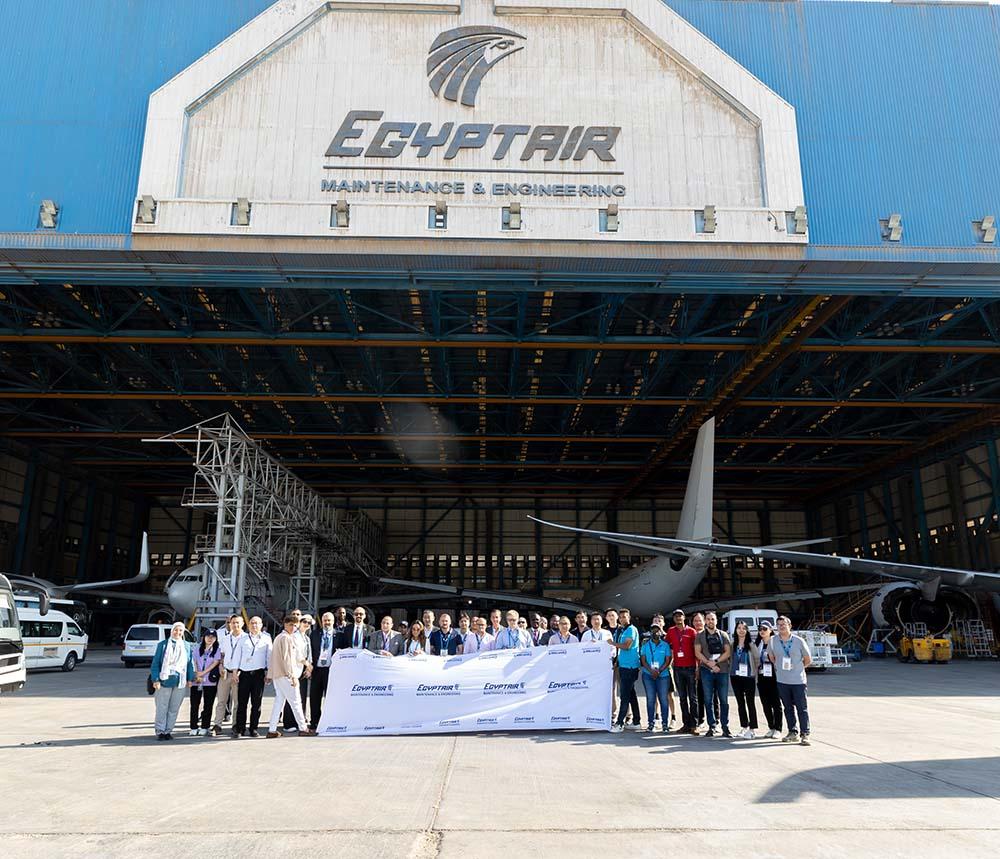
Inside The Hangar
Aviation Week Network recently had the chance to tour EgyptAir Maintenance & Engineering’s facility in Cairo, Egypt. Read on for an inside look at the facility’s airframe, engine and component MRO capabilities.
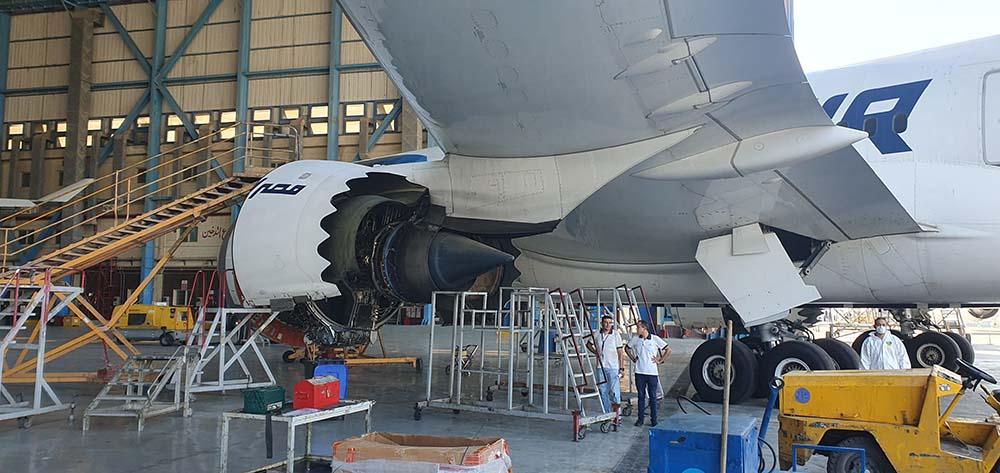
Airframe Capabilities
EgyptAir M&E’s G8000 hangar is mostly dedicated to the Airbus family, with two widebody bays and two narrowbody bays. Boeing aircraft have a separate dedicated hangar, but the G8000 hangar is sometimes used for work on Boeing 787s, too. This 787 was undergoing an engine replacement in the facility during the tour.
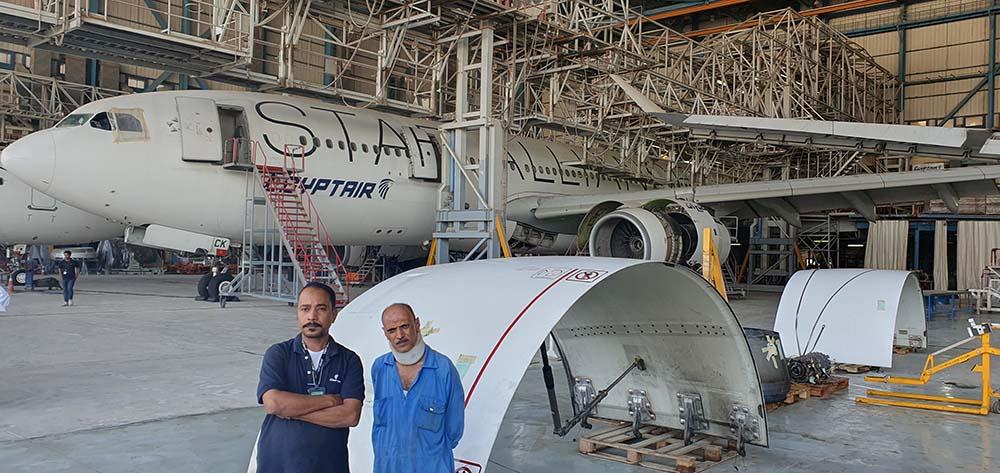
Crowning Achievements
Hangar G8000 is equipped with a movable dock which is useful for work such as modification on an aircraft’s crown area, which includes the crown panel, compartment and skin. The hangar sees plenty of maintenance activity, including bulkhead changes, landing gear replacements, structural modifications and D check capabilities for Airbus A320s and A330s.
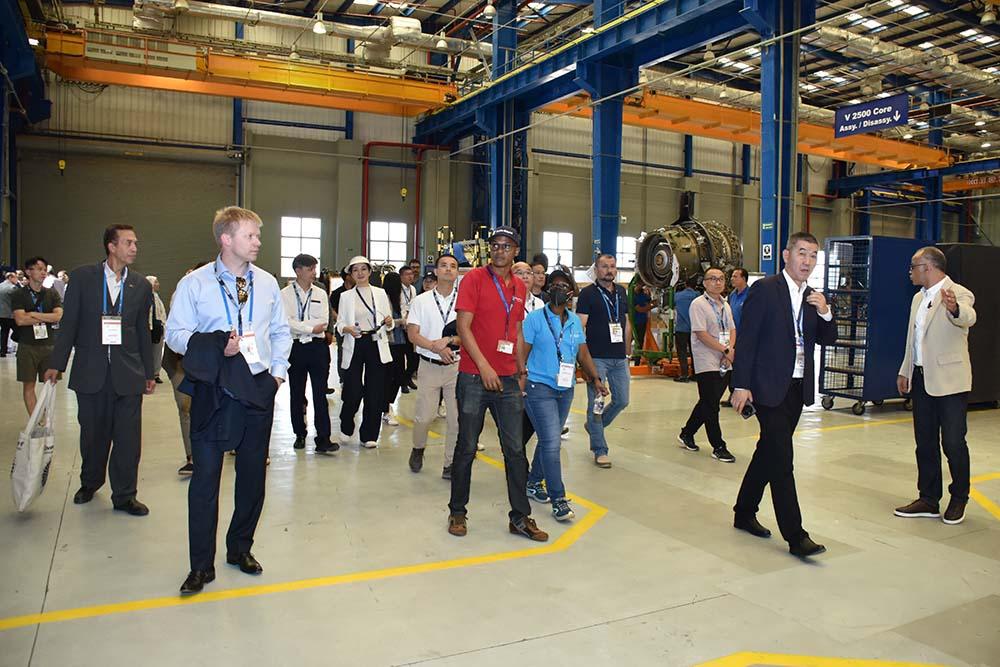
Engine Capabilities
EgyptAir M&E’s engine shop has been European Union Aviation Safety Agency and FAA approved since 2006. It has full capabilities on engines including the IAE V2500; CFM International CFM56-7B, -3C and -5C; and the Rolls-Royce Trent 700. The engine shop handles 50-60 engines a year, with a turnaround of around 120-130 days (with complex supply chains considered). Plans for growth include induction of CFM Leap 1A and 1B capabilities in the future.
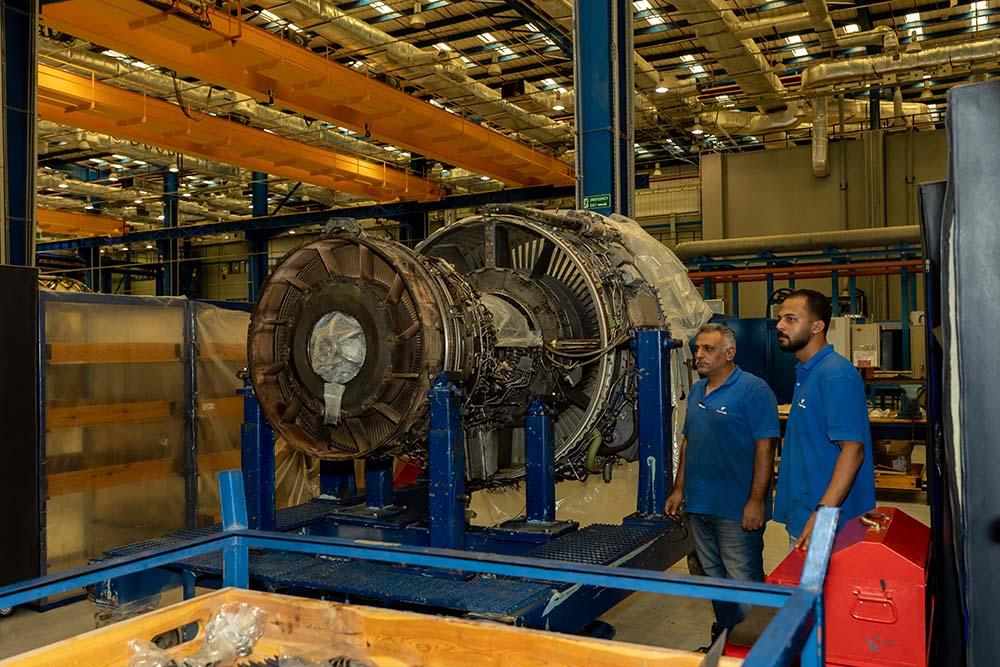
Blade Replacement
The CFM International CFM56-3 engine pictured here was undergoing a critical task to replace defective blades before going to the engine testing facility.
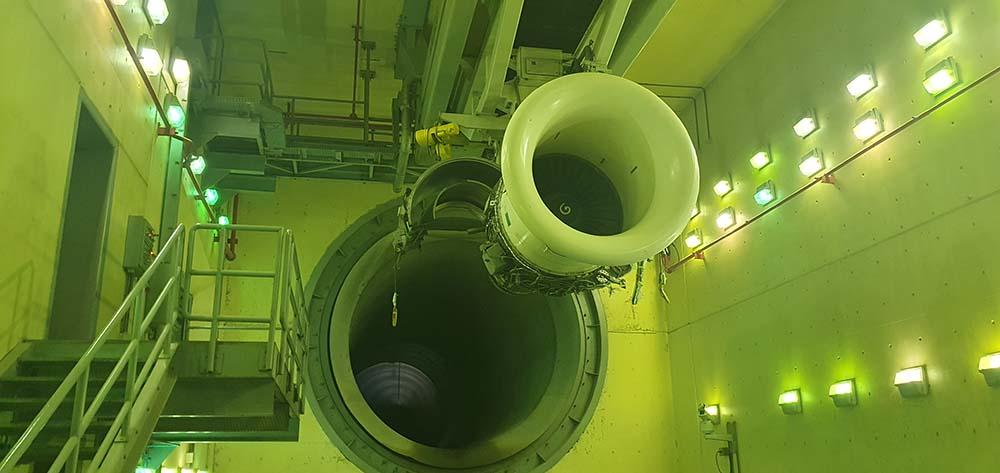
Engine Testing
EgyptAir M&E’s engine shop features an engine test cell, pictured here. Any engine acceptance test must ensure all parameters are in range and any deviations to those measurements can send the engine back to the shop.
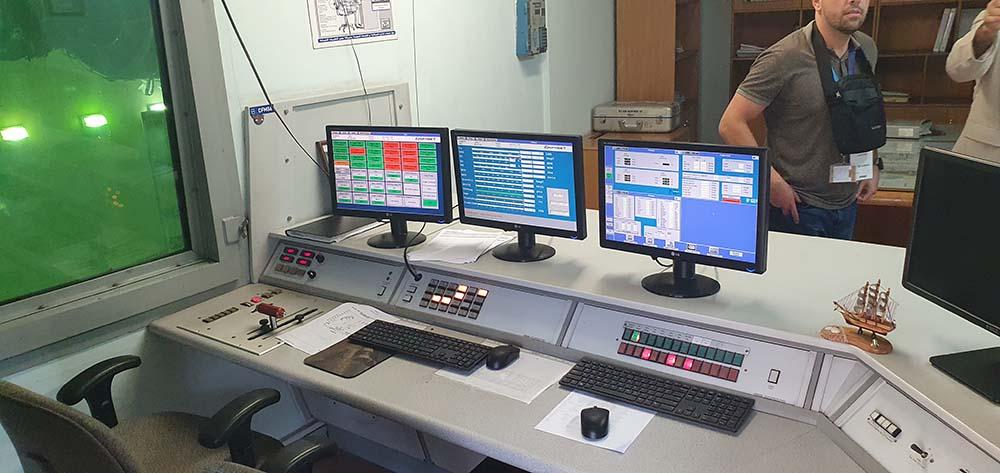
Control Center
The engine test cell control room monitors several critical parameters, including the exhaust gas temperature (EGT), engine overspeed and vibration. EGT margins are also analyzed here.
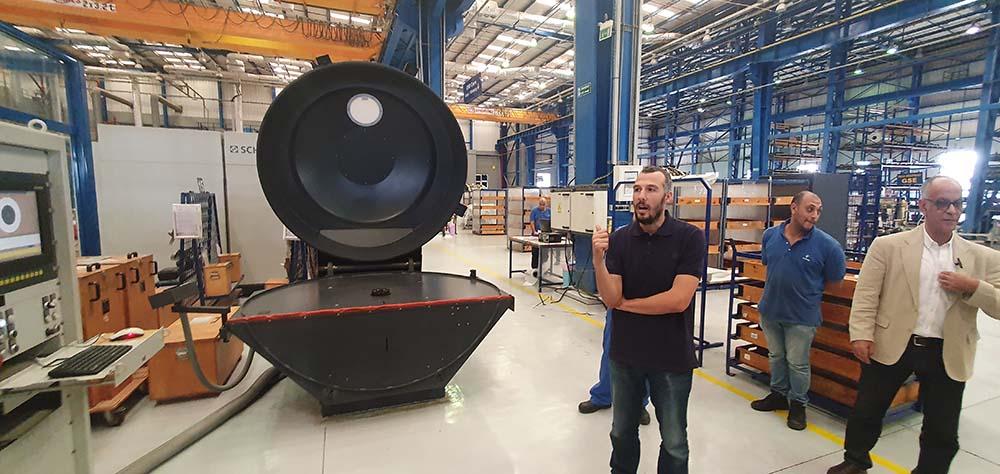
Precision Balancing
The engine shop is equipped a balancing machine used for the precision balancing of engine components.
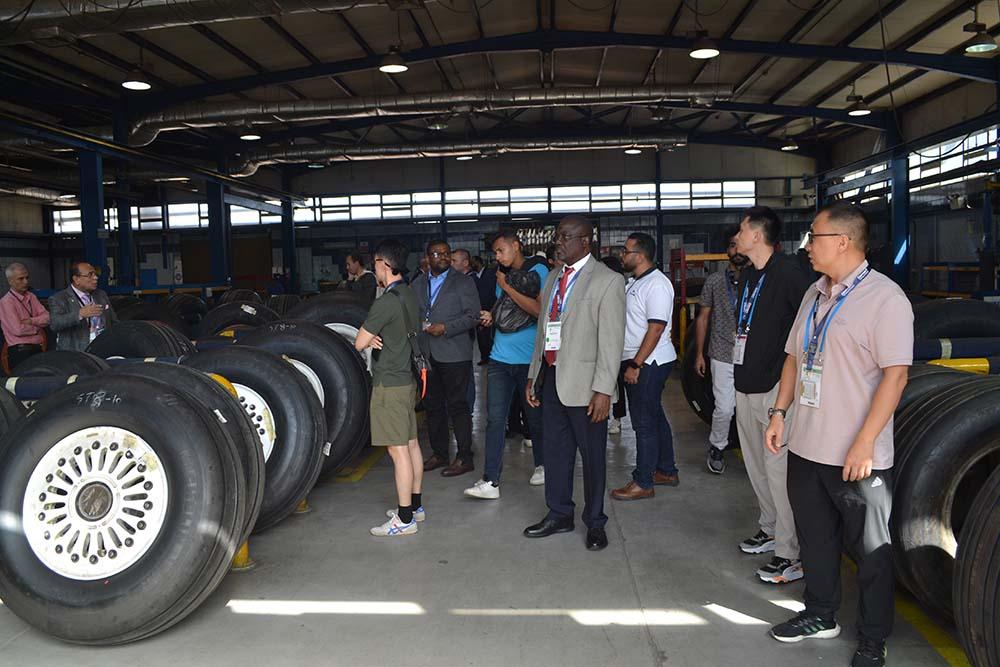
Wheels Up
EgyptAir M&E’s wheels division handled more than 4,000 units in 2023, requiring 50,000 workforce hours. EgyptAir and its charter division, Air Cairo, comprise 80% of the work, with the remaining 20% performed for other local and regional customers.
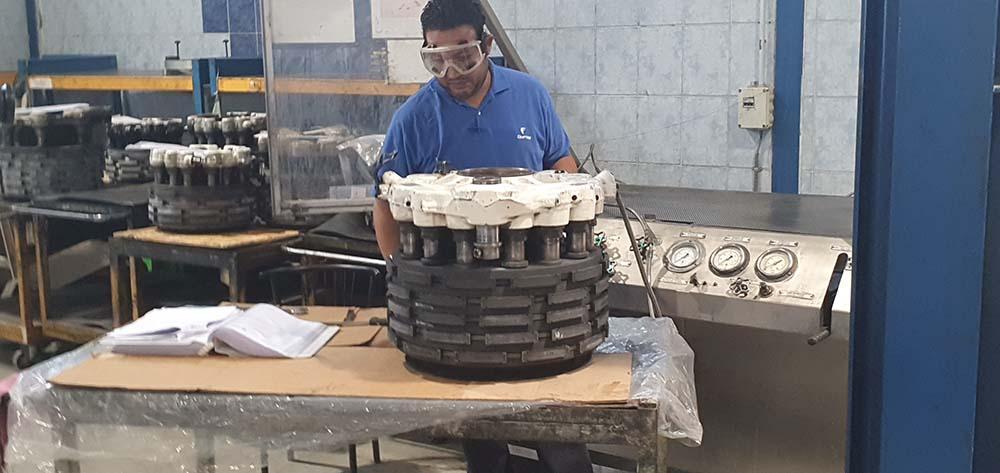
Busy With Brakes
EgyptAir M&E’s brake shop releases 40-50 brake units per month to customers. The shop’s capabilities include test, repair and overhaul according to procedures in the component maintenance manual. Its customers for these services include EgyptAir, Sky Vision Airlines, Nile Air, Nesma and Air Cairo.
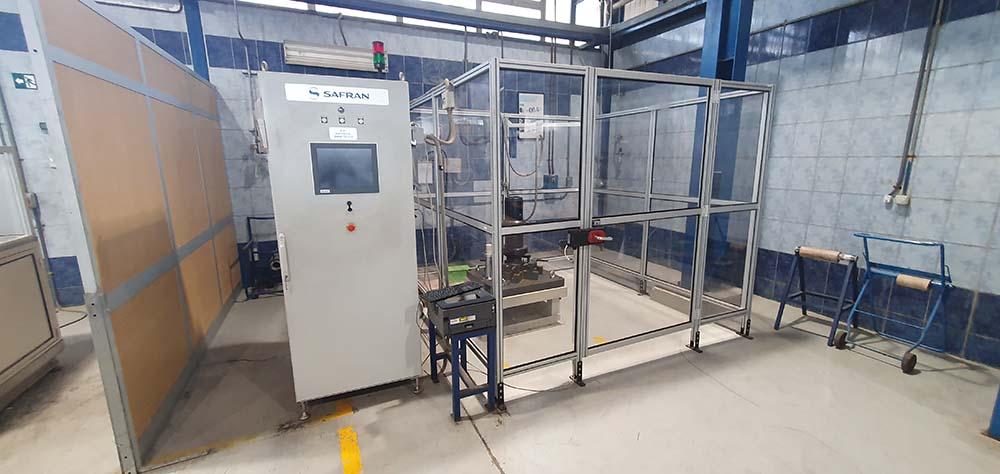
Brake Testing
The brake shop features a Boeing 787 electrical brake tester machine, pictured here.
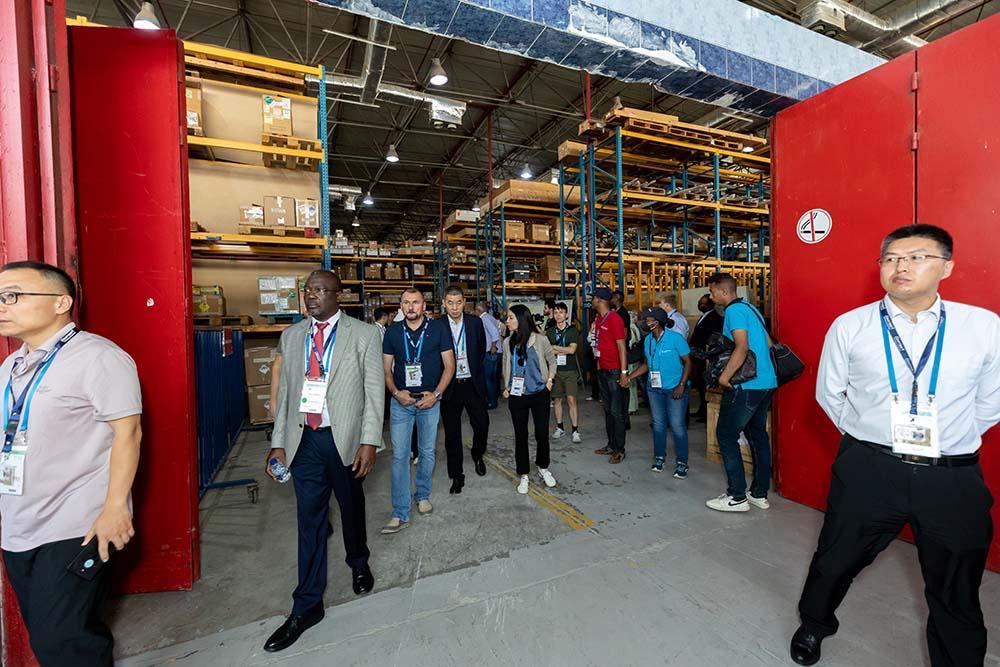
Fully Equipped
EgyptAir M&E’s parts 7,000 m2 (approximately 7,5350 ft.2) warehouse has a central air condition and firefighting system, equipped with two types of detectors for smoke and fire. There are regular checks on the environmental condition for temperature and humidity to ensure optimum storage conditions.
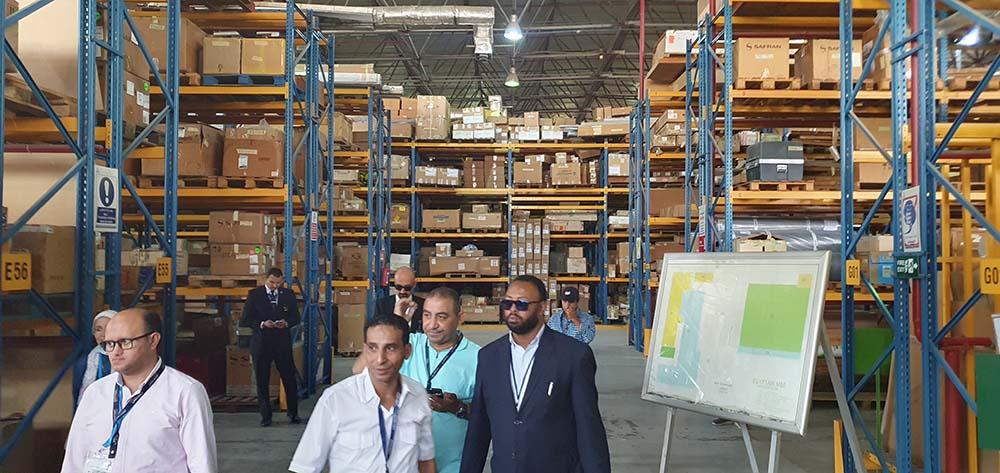
Valuable Inventory
The parts warehouse contains around 125,000 part numbers and approximately $2 billion worth of stored items.
A look inside EgyptAir Maintenance & Engineering’s airframe, engine and component MRO facilities in Cairo.