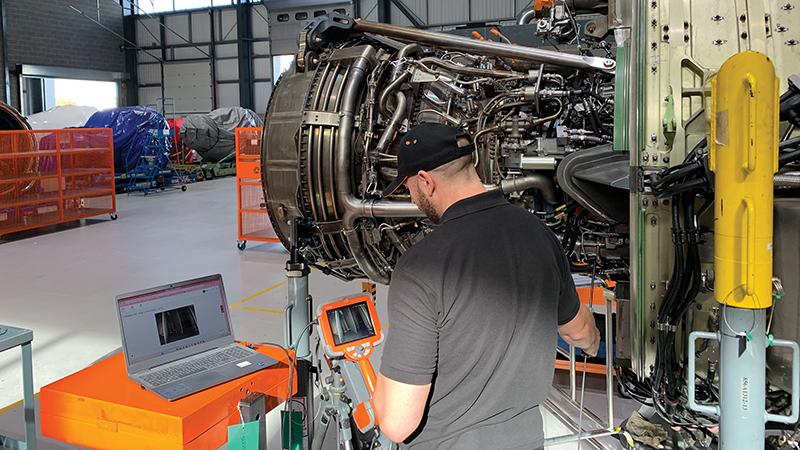
One of AFI KLM E&M’s many generative AI projects involves helping technicians find correct parts and documentation more easily.
The maintenance, repair and overhaul segment has been using artificial intelligence for many years under the less assuming name “predictive maintenance,” but technology startups, OEMs, airlines and aftermarket service providers have been developing a wide range of other use cases recently.
Beyond utilizing artificial intelligence (AI)-based simulation models to determine when assets are deviating from expected behavior or when they will need maintenance or should be scrapped, some companies have developed AI technology to simplify the maintenance processes themselves.
- Artificial intelligence tools serve as digital assistants to help technicians troubleshoot maintenance issues
- Engine borescope inspections take less time due to AI technology
For instance, GE Aerospace has created AI-powered tools for blade, borescope and fluorescent penetrant inspections of engines that are aimed at improving speed, accuracy and consistency. The OEM says these technologies simplify what is otherwise repetitive, manual work for technicians and reduce turnaround times considerably. For instance, GE says the AI-enabled blade inspection tool has cut times in half.
Dutch startup Aiir Innovations has been offering an AI tool for automated aeroengine borescope inspections for several years to customers such as KLM, GT Engine Services and TAP Air Portugal. The company says its software can analyze borescope video 75% faster than manual reviews.
Generative AI has been a particular area of interest in maintenance, repair and overhaul (MRO), and companies have developed applications aimed at simplifying maintenance technician work and customer access to pertinent information.
In November, GE Aerospace, Accenture and Microsoft developed a new tool—tentatively called GenAI Assistant—that airlines and lessors can use to access critical maintenance records more quickly. The companies want to reduce the time spent searching maintenance records from hours to minutes.
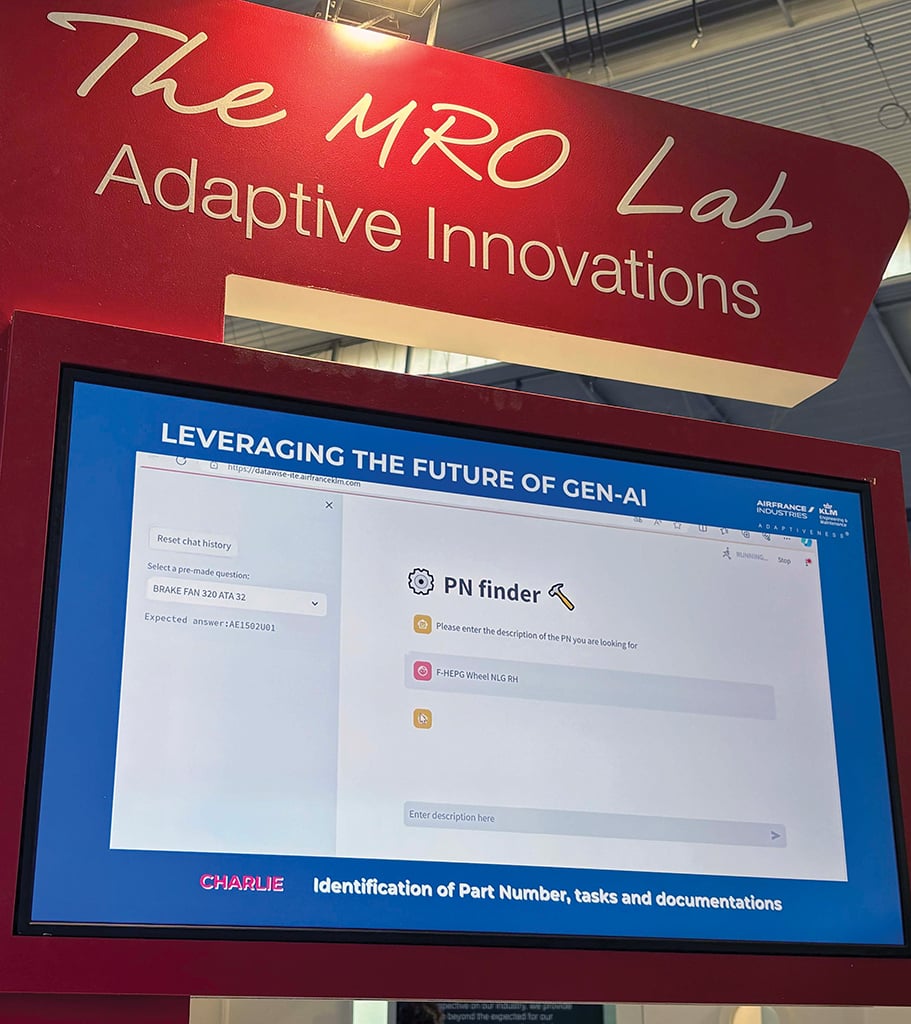
Several companies—such as AFI KLM E&M, Amygda, LexX Technologies and Veryon—have been developing generative AI-powered apps built to function like a maintenance technician’s personal assistant. These apps can provide answers to “what if” scenarios, troubleshoot issues based on data from maintenance logs or aircraft sensors or log and transcribe maintenance information via speech instantly.
LexX Technologies, an Australian tech startup, has an AI platform that can automatically process data from manuals, handwritten notes, photos, work orders and other sources. Technicians can ask the platform a question or describe a problem in their native language, and it provides what LexX says are accurate, data-based answers in simple language to help guide them through tasks. The company describes the technology as a cross between Apple’s Siri virtual assistant and the C-3PO droid from “Star Wars,” custom-tailored for the MRO industry.
AFI KLM E&M has launched more than 80 projects related to the use of generative AI across all Air France business sectors. For instance, it developed a tool called Charlie for its maintenance teams that lets technicians search and instantly pinpoint correct parts, tasks and essential documentation, which the company says is saving more than 1 hr. when repairing or replacing parts.
The MRO provider also has developed a natural language processing tool called Voice to Admin. A person using the app can speak into a device using their native language, and the app translates their words into English for a report in the company’s enterprise resource planning software. AFI KLM E&M says the tool results in higher shop productivity and better data quality.
Some companies also are hoping AI can help the industry safeguard against parts with fake or improper paperwork, which happened in the recent AOG Technics scandal. Aftermarket services provider GA Telesis recently partnered with tech startup Alitheon to develop technology that will improve traceability and provenance of aftermarket parts.
Alitheon’s FeaturePrint technology applies optical AI to create unique digital fingerprints for parts using standard industrial cameras or mobile phones. The company says its technology detects minute surface details of physical items, augmenting elements such as removable tags, QR codes and paperwork to trace part history and authenticity. GA Telesis plans to integrate FeaturePrint into its Wilbur parts provenance and records platform.
Some companies are leveraging AI to improve maintenance-related customer service, recruiting and sustainability, too. For instance, Rolls-Royce is working with startup Aerogility to use its AI-based digital twins to model the environmental impact of its products and services, such as energy consumption at its MRO sites. United Airlines has been using AI to generate messaging around delays, and it is using an AI-based tool called Textio to eliminate potentially biased language in job listings so that it can tap into a more diverse applicant pool.