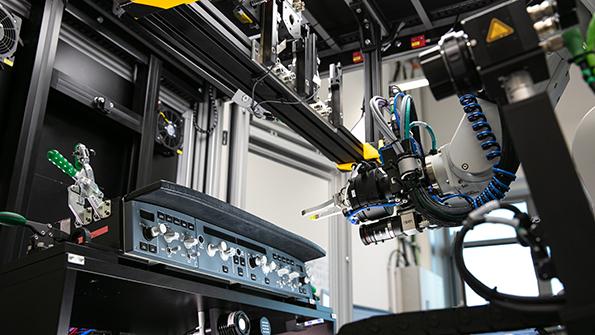
Robotics Revolution
The most common way robots are being utilized in the aftermarket is to perform inspections and certain repairs. However, companies are also investigating the use of robots for other tasks, including testing, cleaning aircraft components and transporting items across the shop floor.

Lufthansa Technik’s Automated Composite Repairs
Lufthansa Technik (LHT) is using robotics to cut down on the labor-intensiveness, time and costs of repairing composite aircraft structures. In partnership with iSAM AG, it has developed an automated adaptive robot system that can be used to repair a variety of airframe-related components, including nose radomes, fan cowl doors and inlet cowls. The system automates and optimizes previously manual processes, such as scarfing or removing composite skin and honeycomb core material.
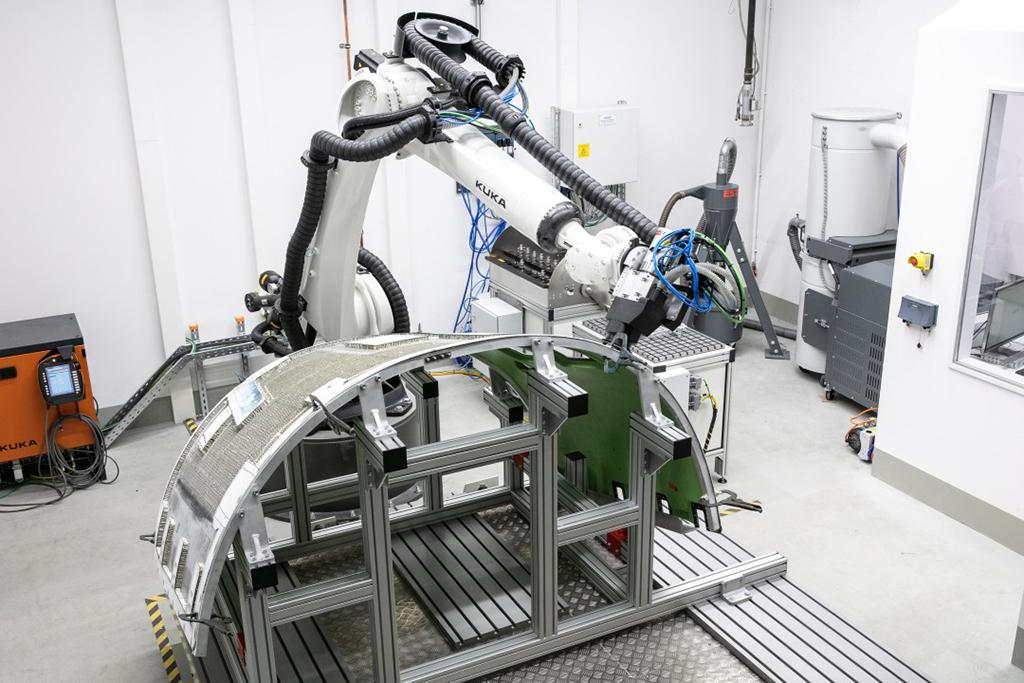
Lufthansa Technik’s Automated Composite Repairs
LHT says the robotic system has increased operating efficiency, reduced material use, created faster turnaround times and requires fewer spare parts. The system has also improved working conditions for maintenance staff. A representative for LHT says that some of these previously manual repair processes were labor-intensive and required technicians to work in uncomfortable, un-ergonomic positions. Now, technicians can conduct repairs from a control desk without being exposed to noise and dangerous substances.
While the system’s rollout was delayed by the COVID-19 pandemic, LHT says it is in the process of reactivating it and preparing it for series production. The MRO plans to conduct its first robotic repairs for customers’ parts in the first quarter of 2023.

Lufthansa Technik Ventures Into “Cobots”
LHT has also begun development of collaborative robots—or “cobots”—to make work simpler for technicians. Its Engine Services division is researching the implementation of a free-standing cobot connected to a rotary table, which can be rolled to any location in the workshop for technicians to colloborate with.
Potential use cases for the cobot include disassembly of parts and thread inspections. In the latter case, LHT says a thread inspection on an outer rear case of an IAE V2500 engine and the subsequent marking of detected defects has previously required 3 hr. of repetitive manual work to inspect 230 threads. It says a cobot could be set up to perform the inspection instead, freeing up a technician for other tasks and delivering much more consistent precision. LHT also notes that data collected during these inspections could then be converted into a digital twin, which could be used for predictive maintenance applications.

Lufthansa Technik Automates Cockpit Control Tests
LHT had already developed a robot to conduct fully automated tests of cockpit controls. First introduced in 2019, its RoCCET (robot-controlled cockpit electronics testing) robot uses sensors and cameras to check all switches and LEDs of cockpit controls. Dirk Jaster, avionics engineer at LHT Hamburg, says the RoCCET project is now focused mainly on test procedures for electronic input and output signals of cockpit panels due to a recent increase in demand. LHT is working to set up the technology for series production on its first flight-part number: a Boeing 787 mode control panel, which it says is in high demand, followed by the flight control unit of the Airbus A350.
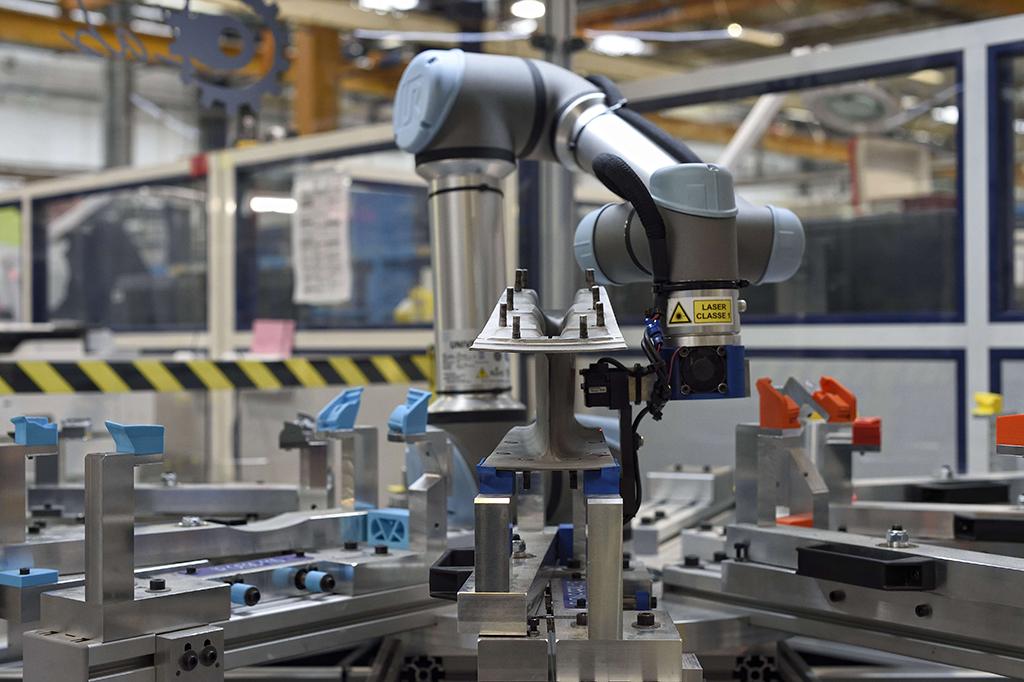
The MRO Lab Leverages Robotics
The MRO Lab at AFI KLM E&M has been testing and developing robotics for a wide variety of applications, ranging from repairs and inspections to grinding, sanding and cleaning tasks. Its engine parts repair subsidiary CRMA has developed the “Robocot” to improve the repair process for turbine center frame module panels by performing precise measurement of parts wear. Robocot is equipped with laser telemeters that scan the surface of these parts, measuring minimum thickness values and determining whether they can be repaired. AFI KLM E&M says that the previous procedure could generate an additional cost of up to €80,000 (nearly $84,000) per year.

The MRO Lab Seeks Additional Use Cases
“Robotics help us in the aftermarket to save time for routine tasks and inspections, reducing the turnaround time and increasing parts and aircraft availability,” says Ahmoss Messayeh, director of innovation at AFI KLM E&M. “Robotics is also a good opportunity for our high-skill technicians to handle higher-value tasks.”
As AFI KLM E&M adds more aircraft and engine types to its business units, Messayeh says it is continually evaluating new robotics use cases. It has ongoing proofs of concept that Messayeh hopes will “be fruitful to be industrialized in the next couple of years.”
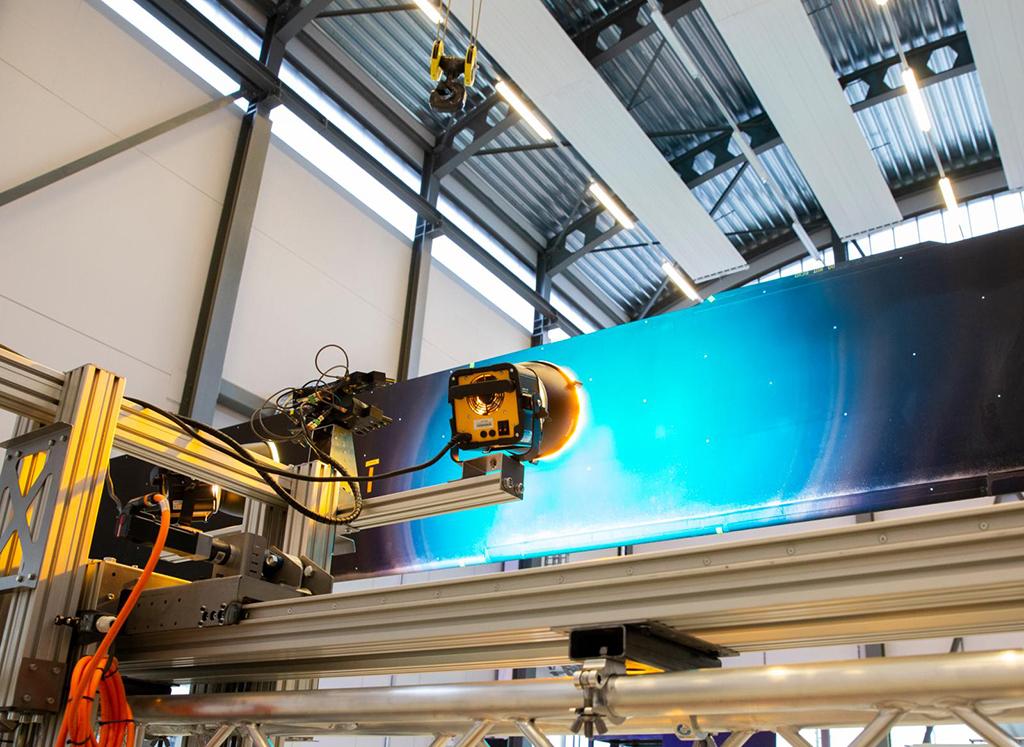
NLR Focuses On Automated Inspections
The Royal Netherlands Aerospace Center (NLR) has been developing robotics technologies to automate visual inspections. In the last year, it has focused heavily on its autonomous robot for blade inspections (ARBI). The robot, which is attached to an 11-m-long (36-ft.) rail, is used to inspect helicopter rotor blades for surface and subsurface defects.
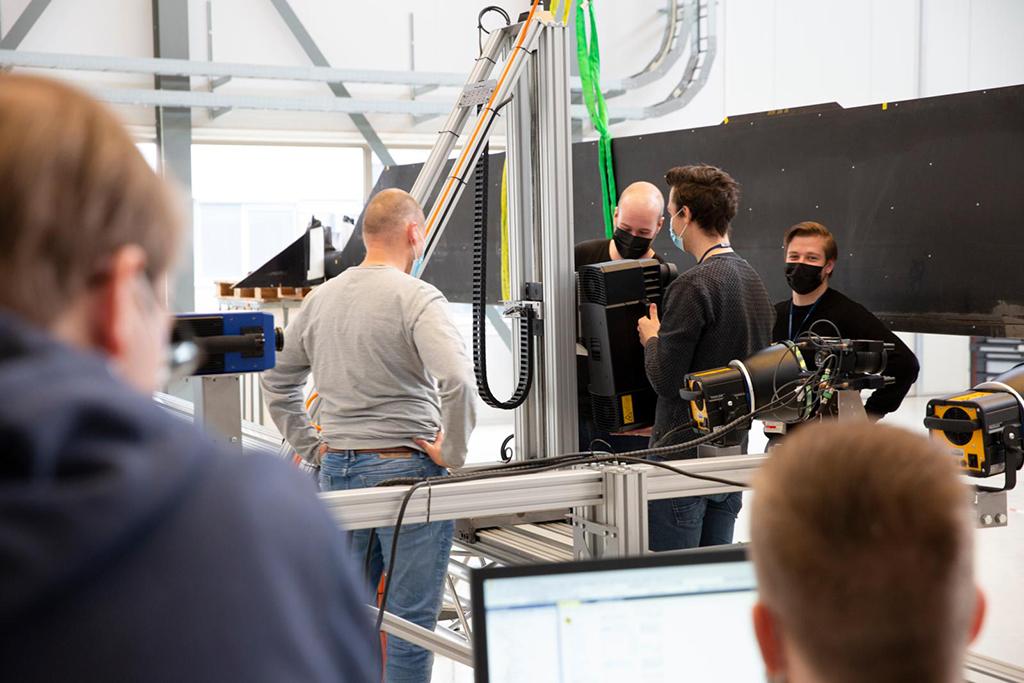
Automated Coin Tapping
Arjan de Jong, principal for MRO at NLR, says composite blades on helicopters are difficult and time-consuming to inspect because the process requires a repetitive and fairly subjective method called “coin tapping.”
“It’s difficult to listen to the different sounds of the blade while you tap it, and if you hear a difference in tone, it might suggest a defect, but that is difficult to interpret,” de Jong says. “If you can replace [manual coin tapping] with a robot that is better-suited for dull work, it brings a huge advantage to the work floor. The mechanic can do more interesting jobs than just tapping blades.”
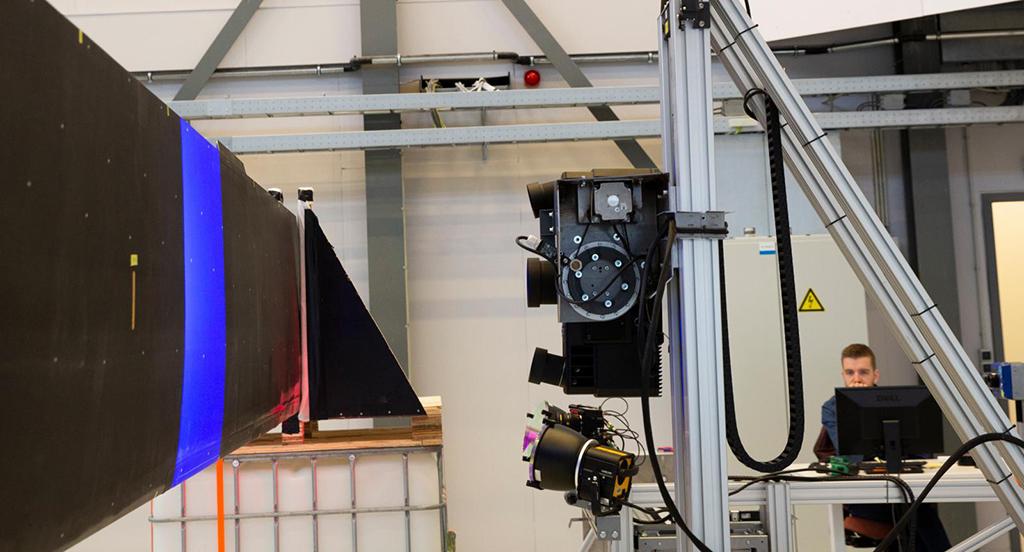
NLR’s Industry Collaboration
ARBI is currently located at a Ministry of Defense facility in the Netherlands, and de Jong says NLR is now focused on trying to qualify the robot for inspection work. It is also working with commercial parties that are interested in leveraging its robotic inspection technology on the shop floor. As part of the BrightSky consortium, NLR is working with companies such as JetSupport and KLM to implement autonomous inspection robots that can scan and assess damage on aircraft and engine parts.
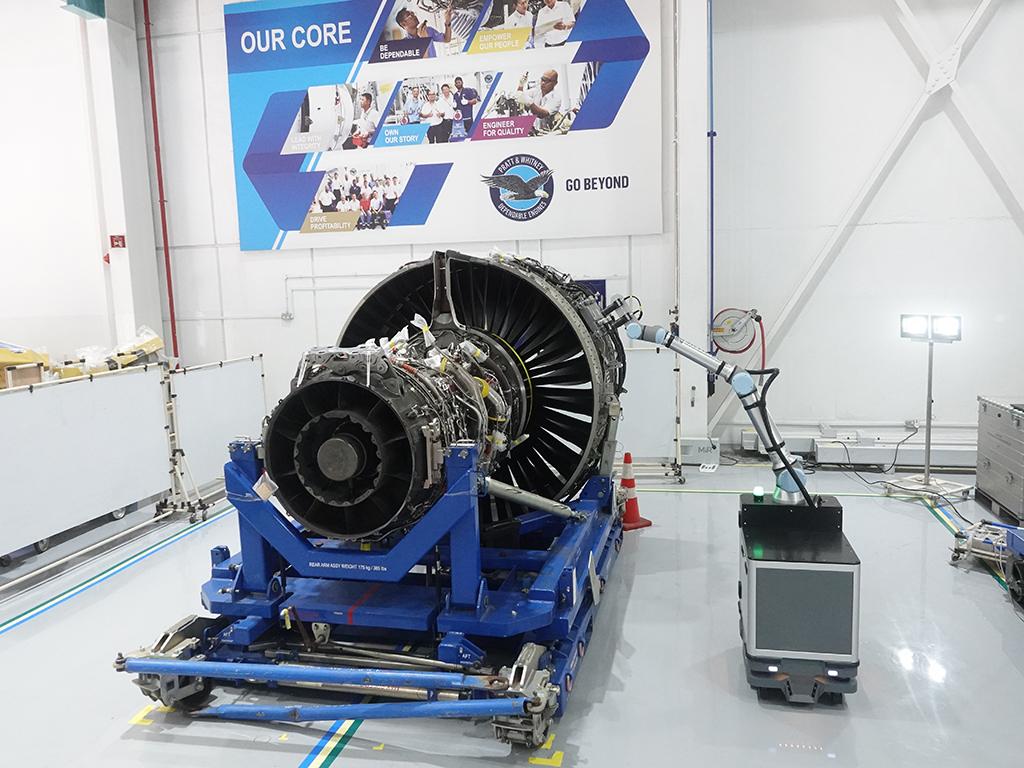
Robots Put Pratt On Path To Industry 4.0
Pratt & Whitney is utilizing robotics as part of its Industry 4.0 strategy to modernize and transform its operations. The OEM is implementing robotics for labor-intensive, high-frequency processes across its aftermarket operations, such as material removal, inspection, data capturing and machine tending. In addition to using robots to automate visual inspection, polishing and deburring processes, Pratt has developed a cobot in Singapore, where it is establishing a technology accelerator.
The cobot is mounted on an automated guided vehicle to capture detailed photos of an engine—a process that was previously performed manually by technicians. The cobot can move around to programmed locations and it is equipped with sensors for collision avoidance, which Pratt says allows it to work in collaboration with technicians.
The OEM is also evaluating the use of robots to precisely apply materials such as sealants and maskants.
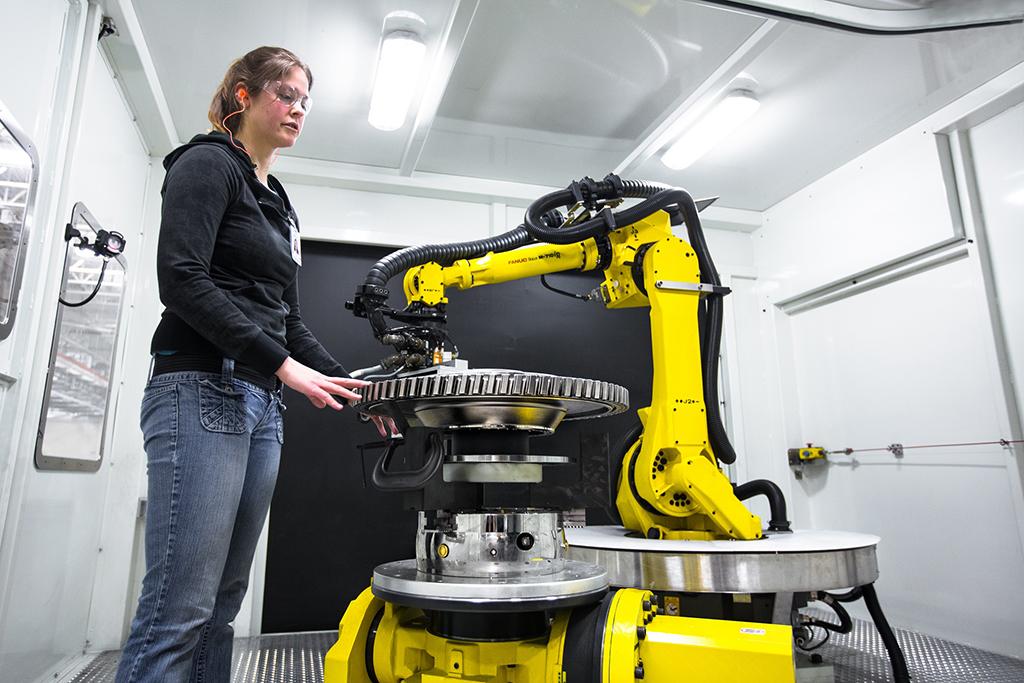
Engine OEMs Deploy Robots
Pratt & Whitney is not the only engine OEM to deploy robotics for engine MRO. GE Aviation acquired OC Robotics in 2017, adapting its snake-arm robotic technologies for engine cleaning, inspection and repair. The robots can access difficult-to-reach areas of the engine and GE has adapted them to enable tasks such as the application of thermal barrier coatings in the field. It is also using robotics systems for engine washing, welding-based repairs and fluorescent penetrant inspections.
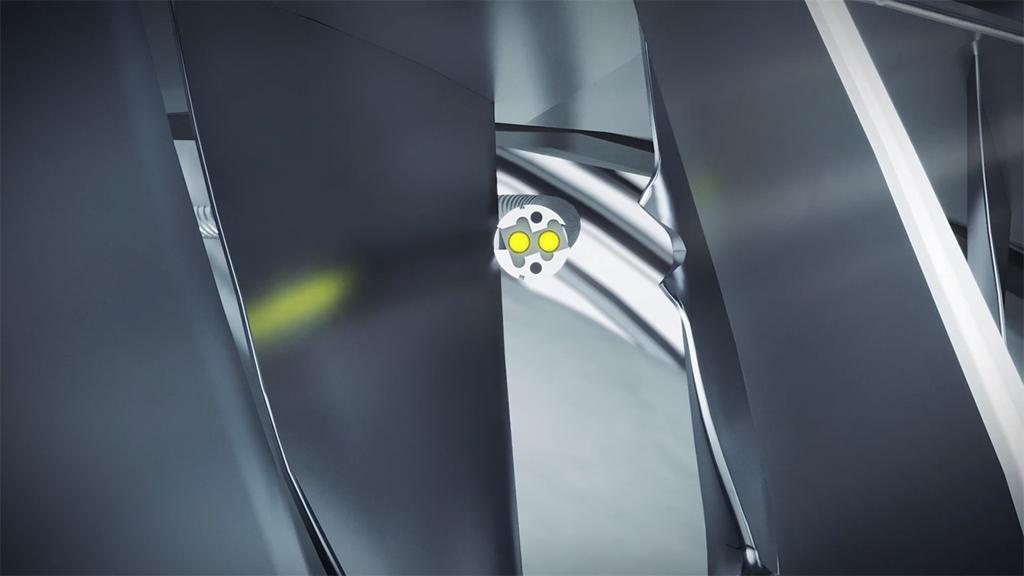
Rolls-Royce’s Robot Collection
Rolls-Royce has developed a variety of robotics applications, such as snake and small “swarm” robots that can be used to inspect difficult-to-reach parts of engines. It has also collaborated with the University of Nottingham to develop a robotic boreblending machine to repair damaged compressor blades.
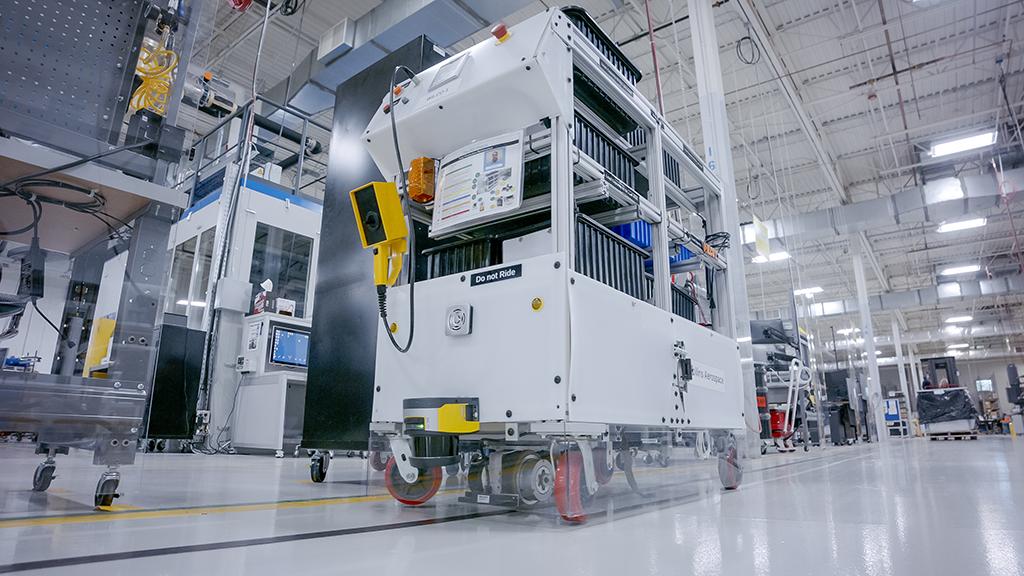
Collins Taps Robots For Smart Workshop Operations
Collins Aerospace is using robots on its MRO shop floors to move items more efficiently between different areas of the building. It first developed its Autonomous Intelligent Vehicle at its Singapore innovation hub, and its MRO shop in Monroe, North Carolina, designed a similar robot called Wilco 1 to move tools, parts or equipment as needed. It says the robots reduce walking distances and lead times for staff.
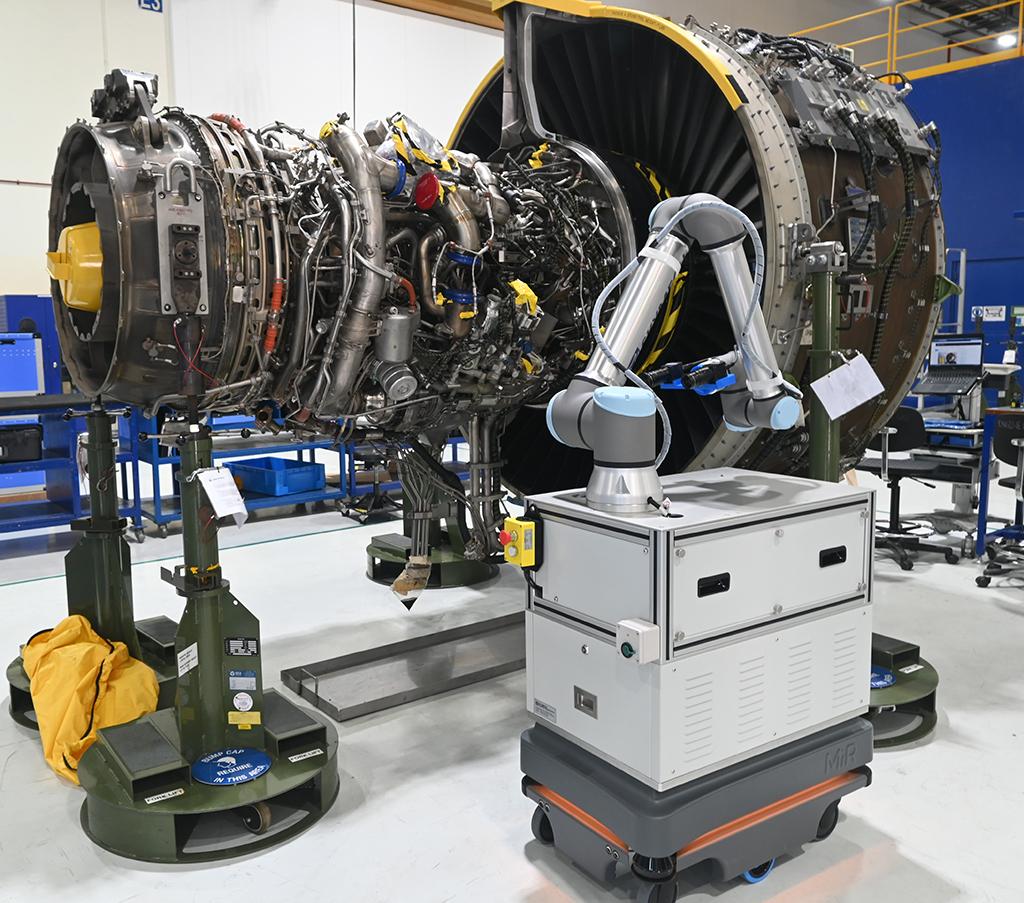
Collins Automates Inspections
In Singapore, Collins has also deployed an automated visual inspection system that uses robotics and optical character-recognition software to simplify and speed up inspections on various products. The system features cameras mounted on articulating arms of wheeled, autonomous robots, which capture a large number of photos of the items being inspected. These photos are then compared to photos of the items in an ideal state to detect irregularities.
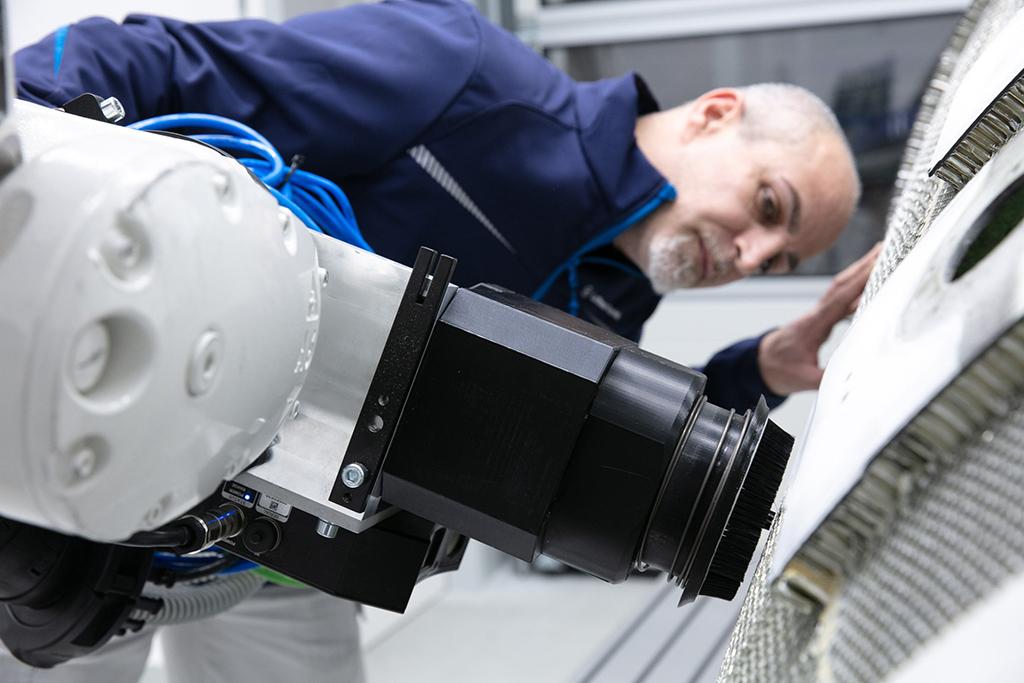
Will Robots Replace Technicians?
Although the topic of automation often creates anxiety about the eventual elimination of jobs, their adoption in the MRO industry seems to be focused more on improving the workplace environment for average technicians.
“We do not look at robots as a simple means to replace human colleagues,” says a representative for LHT. “Instead, the improvements in productivity we’re aiming at should, for example, stem from improved working conditions in which our human employees no longer have to deal with dull and repetitive tasks, but instead can concentrate on other, more rewarding tasks with higher added value.” He adds that the MRO will continue to rely on its experienced and “much more flexible” human experts for more complex tasks.
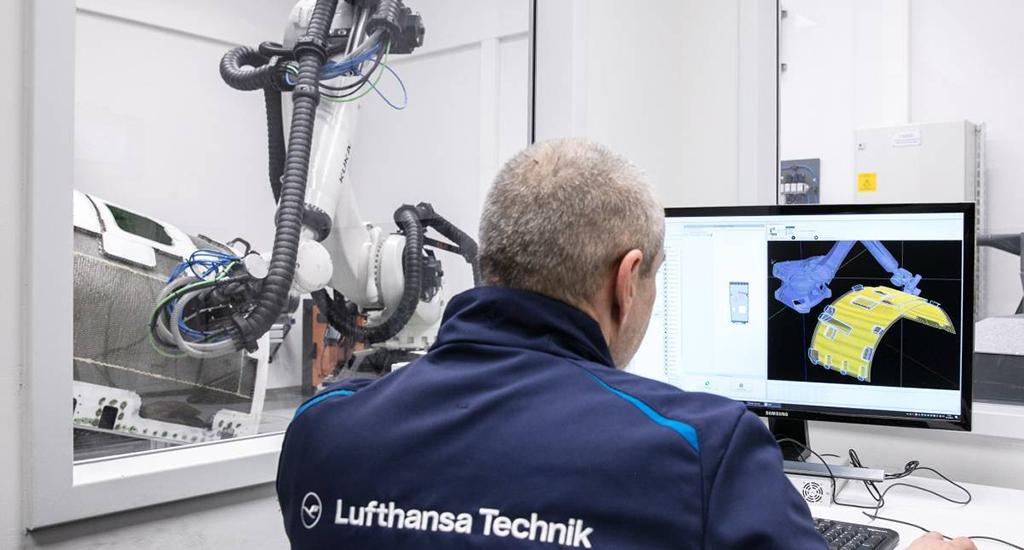
Capturing Knowledge
The efficiency and data-capturing capabilities of robotic systems could also help alleviate some of the pain many aftermarket companies are feeling in the wake of ongoing capacity issues and the COVID-19 talent exodus.
According to NLR’s de Jong, robotics technologies could potentially be leveraged to pass down legacy knowledge to new technicians. “It will also be a way of capturing skills from mechanics and putting them into a robot so that, for example, mechanics that will leave the company when they get older will have their knowledge embedded in robotic systems, so that’s good from a learning perspective” he says.
Aircraft maintenance is a physically demanding yet highly complex field, often requiring technicians to perform repetitive manual labor that calls for precision and attention to detail. Many MROs and OEMs are now turning to robots to automate various tasks with the aim of making maintenance simpler, safer and quicker.
Read on to learn more about some of the latest robotics developments across the aftermarket.