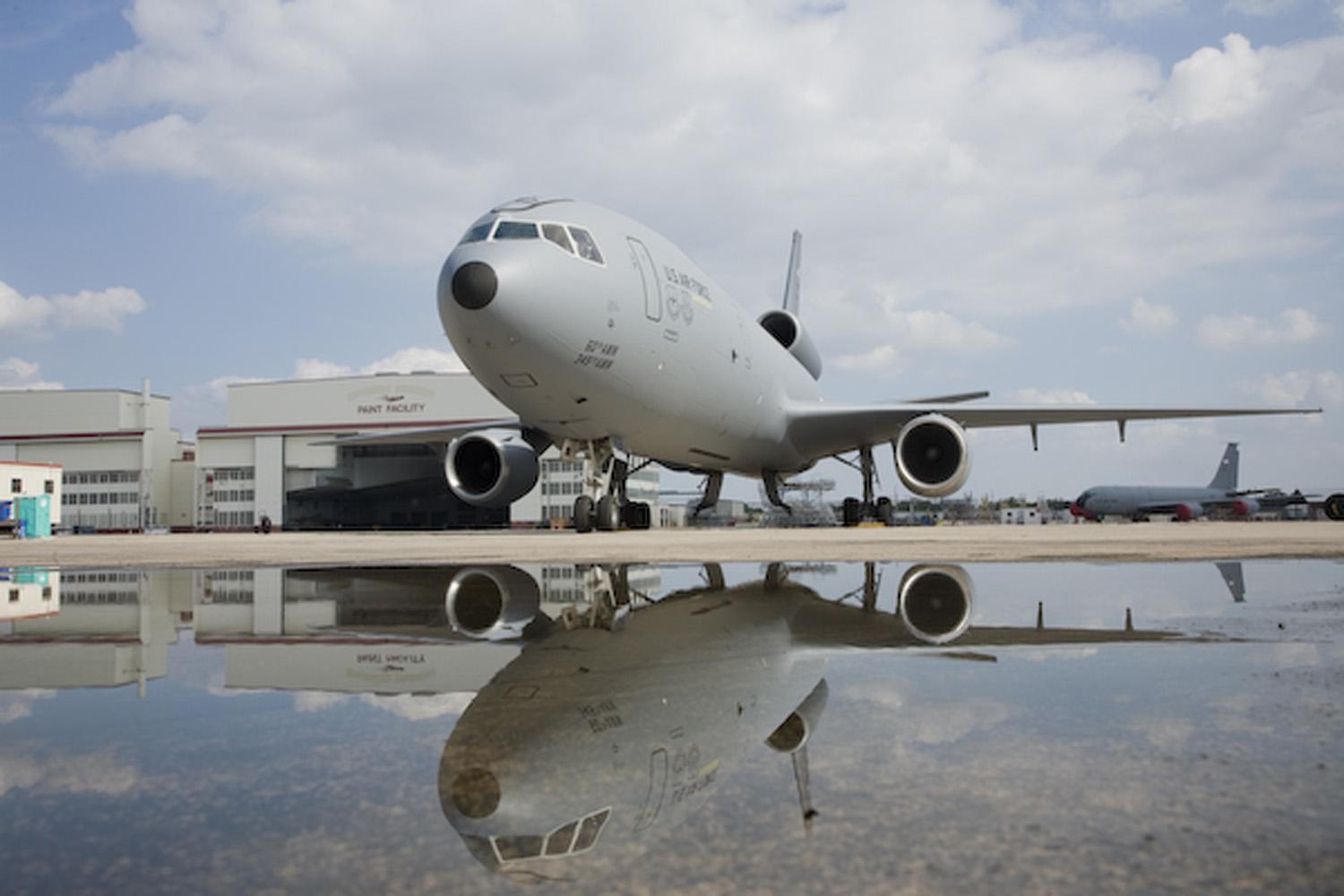
As Boeing’s largest MRO site and one of the largest military MRO facilities in the world, the OEM’s 168-acre facility at Port San Antonio has been growing steadily since it was established more than 21 years ago. Read on to learn more about how Boeing has grown the site’s military, commercial and technology capabilities, and to get a behind-the-scenes look at some of the major MRO projects currently underway at the facility.
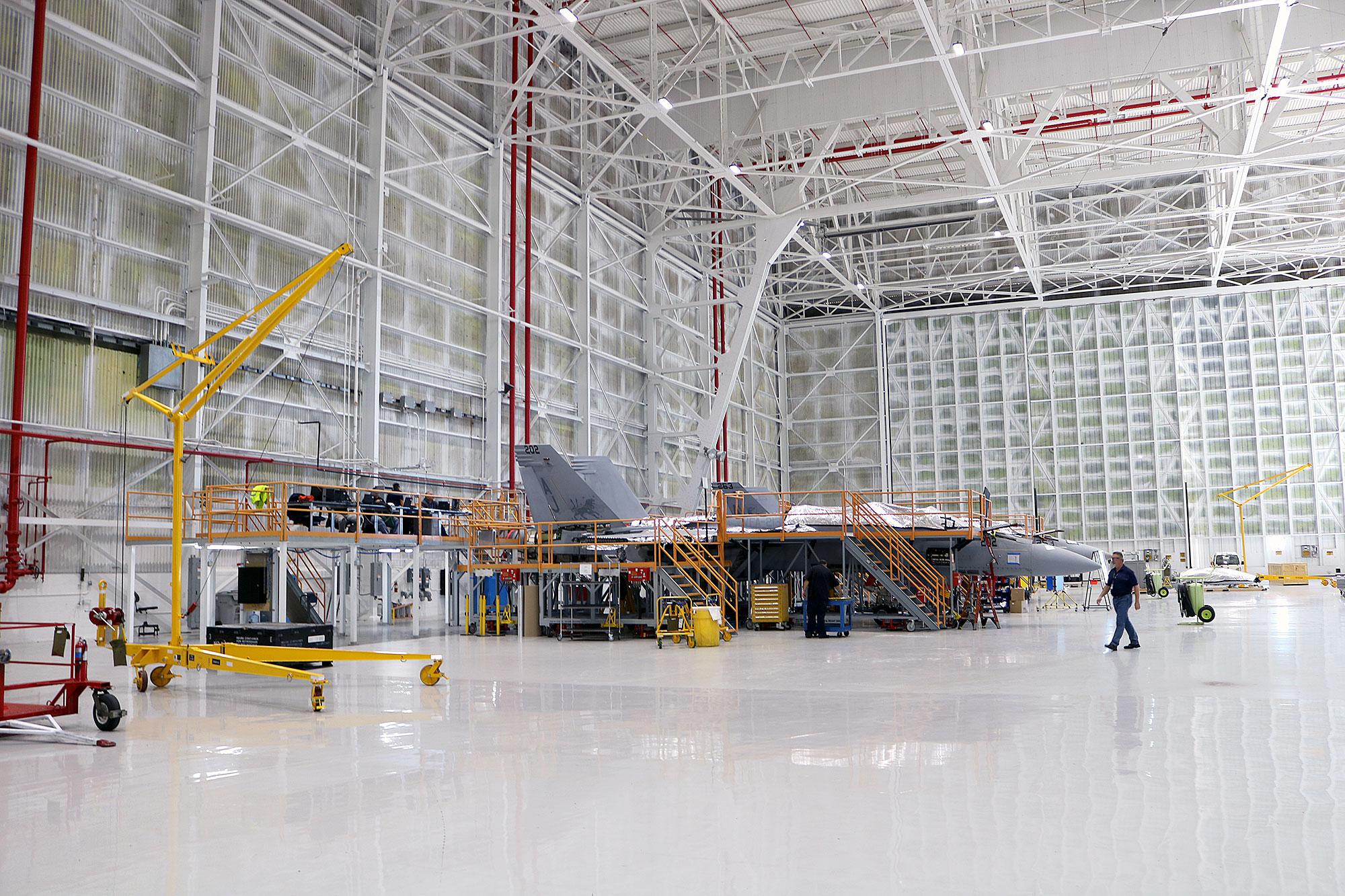
Across Boeing’s five on-site hangars, the OEM has approximately 1.6 million ft.2 of hangar space that can accommodate 33 narrowbody aircraft and 22 widebody aircraft. Boeing also has 3.5 million ft.2 of aircraft ramps, outdoor canvas hangars, run-up areas and parking pads to fit more than 30 aircraft. During Aviation Week’s tour of the site, much of this space was occupied by grounded 737 MAX aircraft which, have been undergoing maintenance work to get them flight ready for return to service.
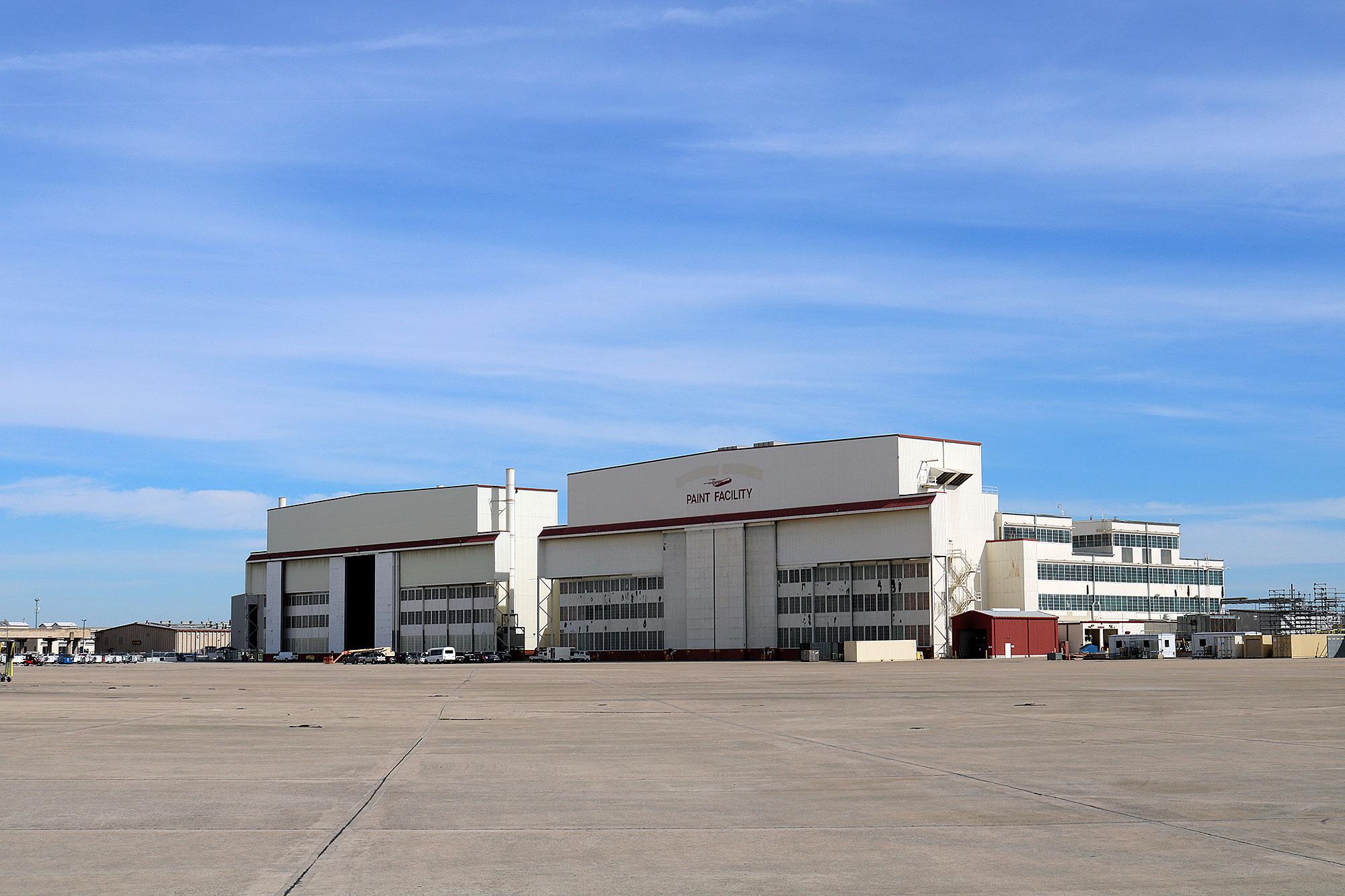
In addition to hangar and ramp space, the site has facilities for painting/de-painting, non-destructive inspection, drop-in maintenance, logistics support and corrosion control, as well as back shops and office space.
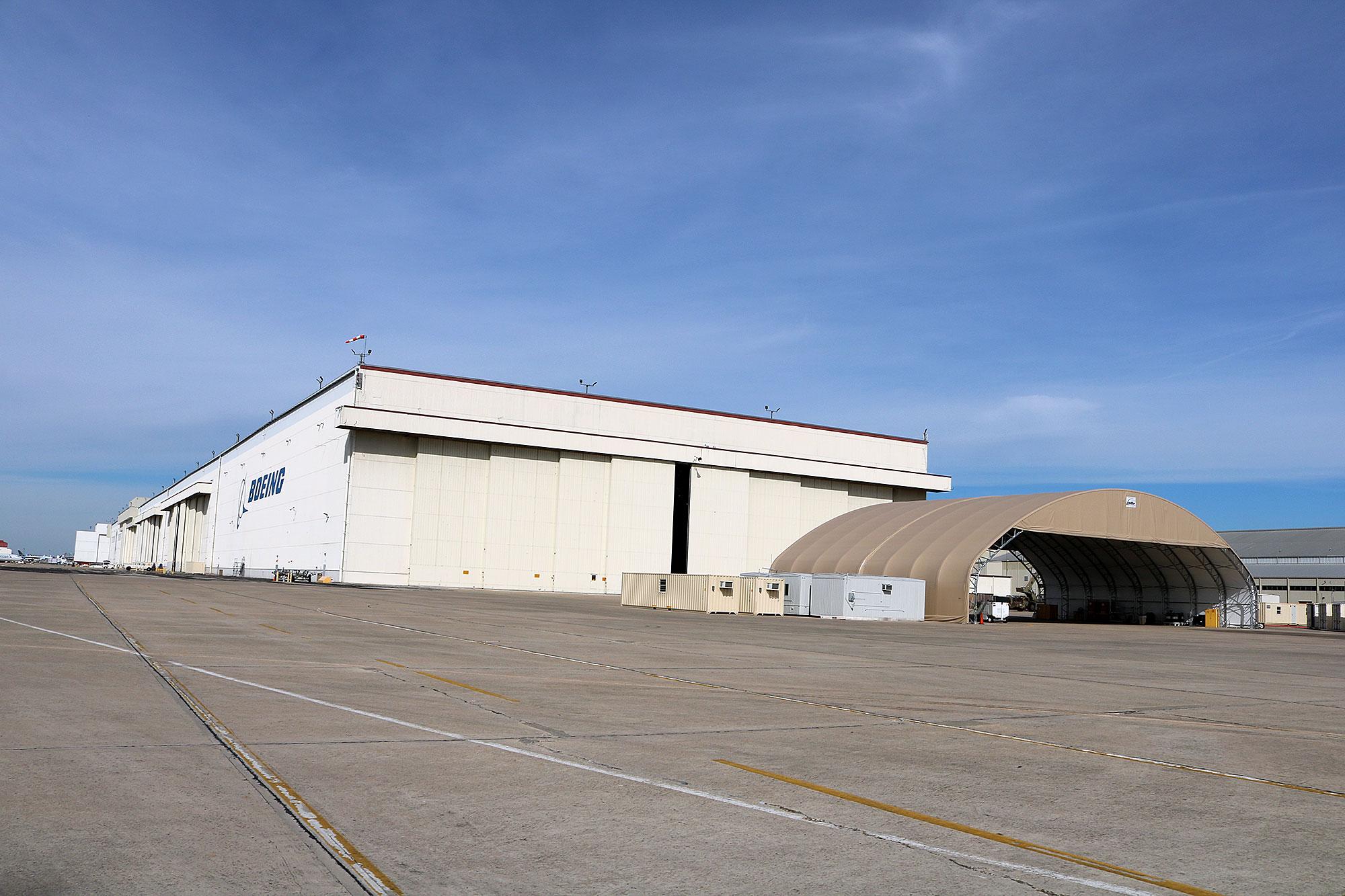
Boeing has invested more than $240 million in the Port San Antonio site, including a recent investment of $42 million in improvements and upgrades to accommodate new maintenance programs such as the F/A-18 Super Hornet Service Life Modification (SLM) program for the U.S. Navy. One of the hangars receiving an upgrade is Building 375—the largest of Boeing’s hangars on site, which it says is the largest free-standing, high-bay hangar in the world. The hangar can fit 22 narrowbodies and 17 widebodies nose-to-tail.
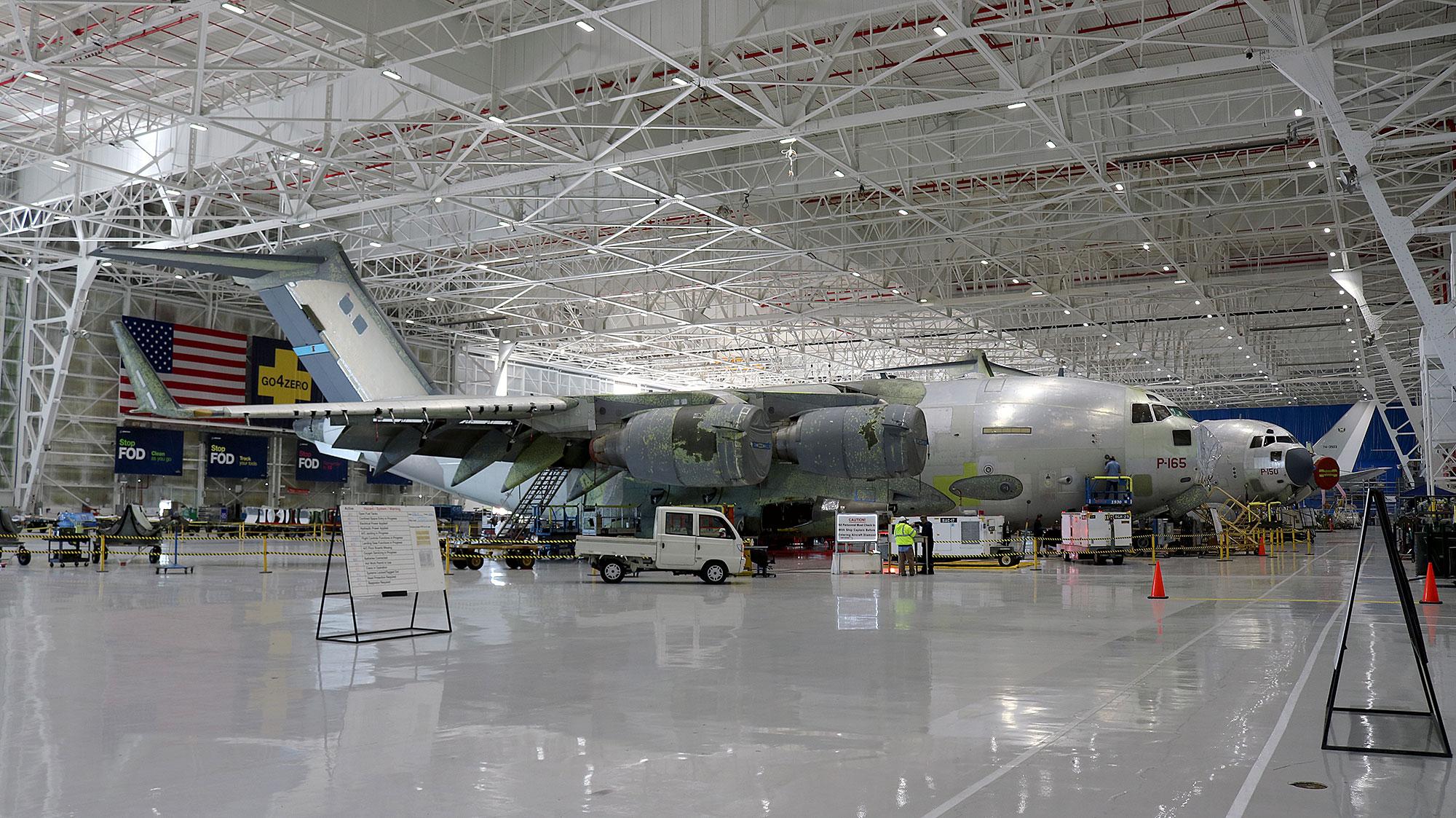
The hangar, which is about one-third of a mile long with a unique structure that features no pillars in the middle, is nearly finished with its upgrade—although Boeing still plans to add windows for natural light. At the moment the north end of the hangar is used for commercial executive fleet work, the middle portion is used for C-17 Globemaster III heavy maintenance and the south end is used for the F/A-18 program.
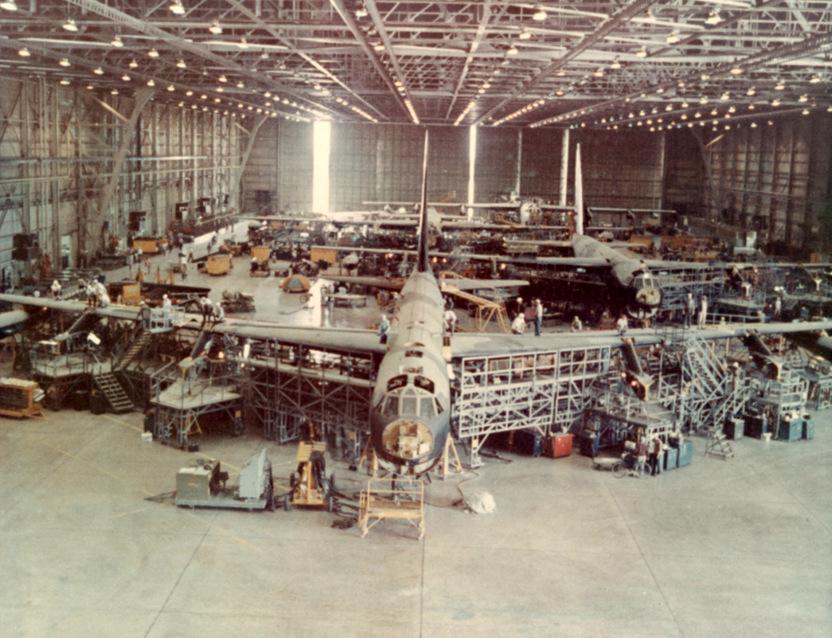
When Boeing first began operating the Port San Antonio site, it typically maintained legacy programs such as the C-17 or the McDonnell Douglas KC-10 and KC-135. According to Jay Galloway, Boeing’s San Antonio site leader, the site was only operating at about 61% capacity for its first 20 years or so. However, this has recently grown to approximately 98% capacity, and Galloway says the site is booked for the next 4-5 years thanks to new programs and “a litany of new customers.”
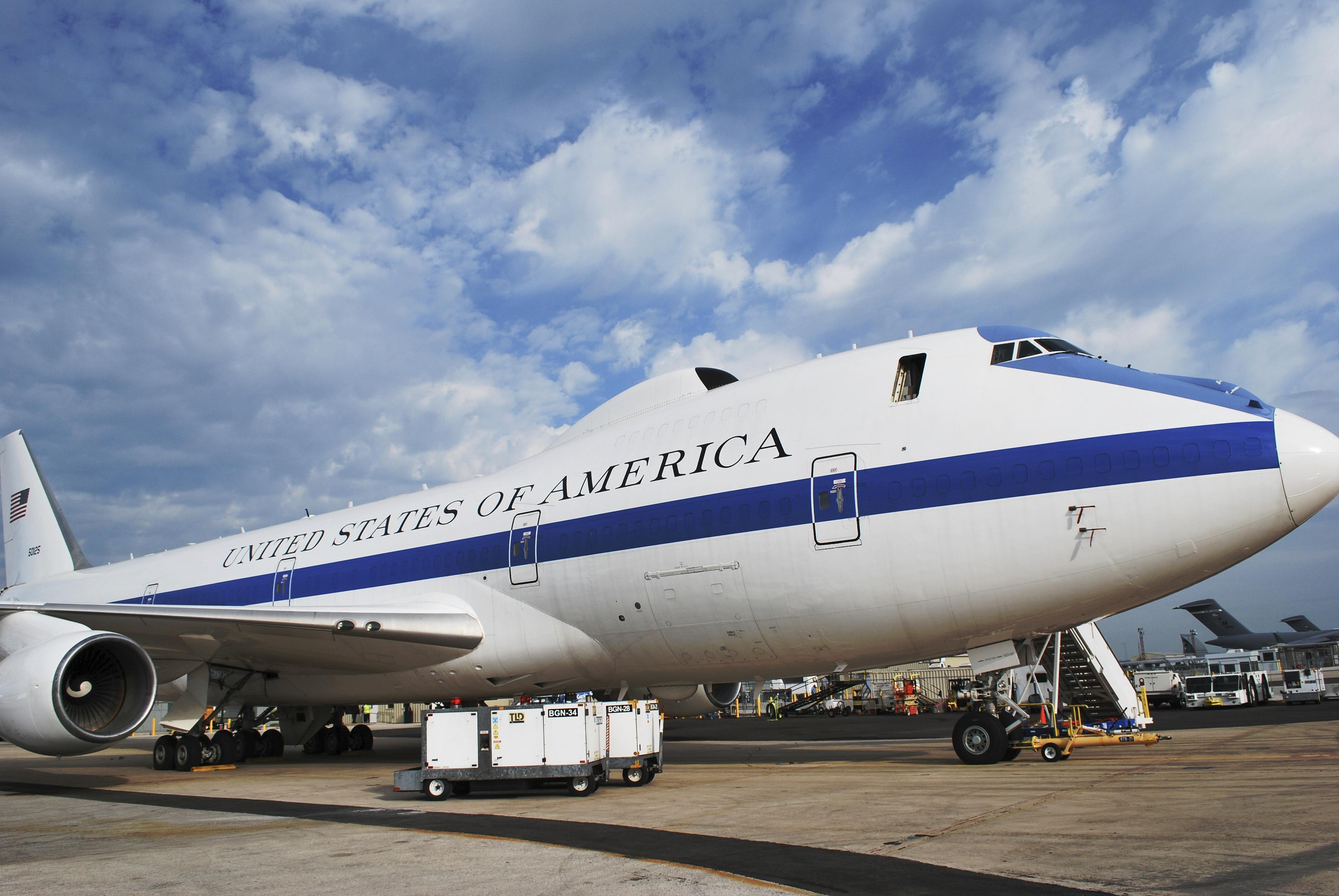
Now, the site performs a mix of commercial and military MRO for both national and international customers, ranging from recent projects such as a 737 MAX Viasat mod it recently performed for United Airlines to C-40A Clipper “Combi” passenger-cargo modifications and work on the U.S. Executive fleet.
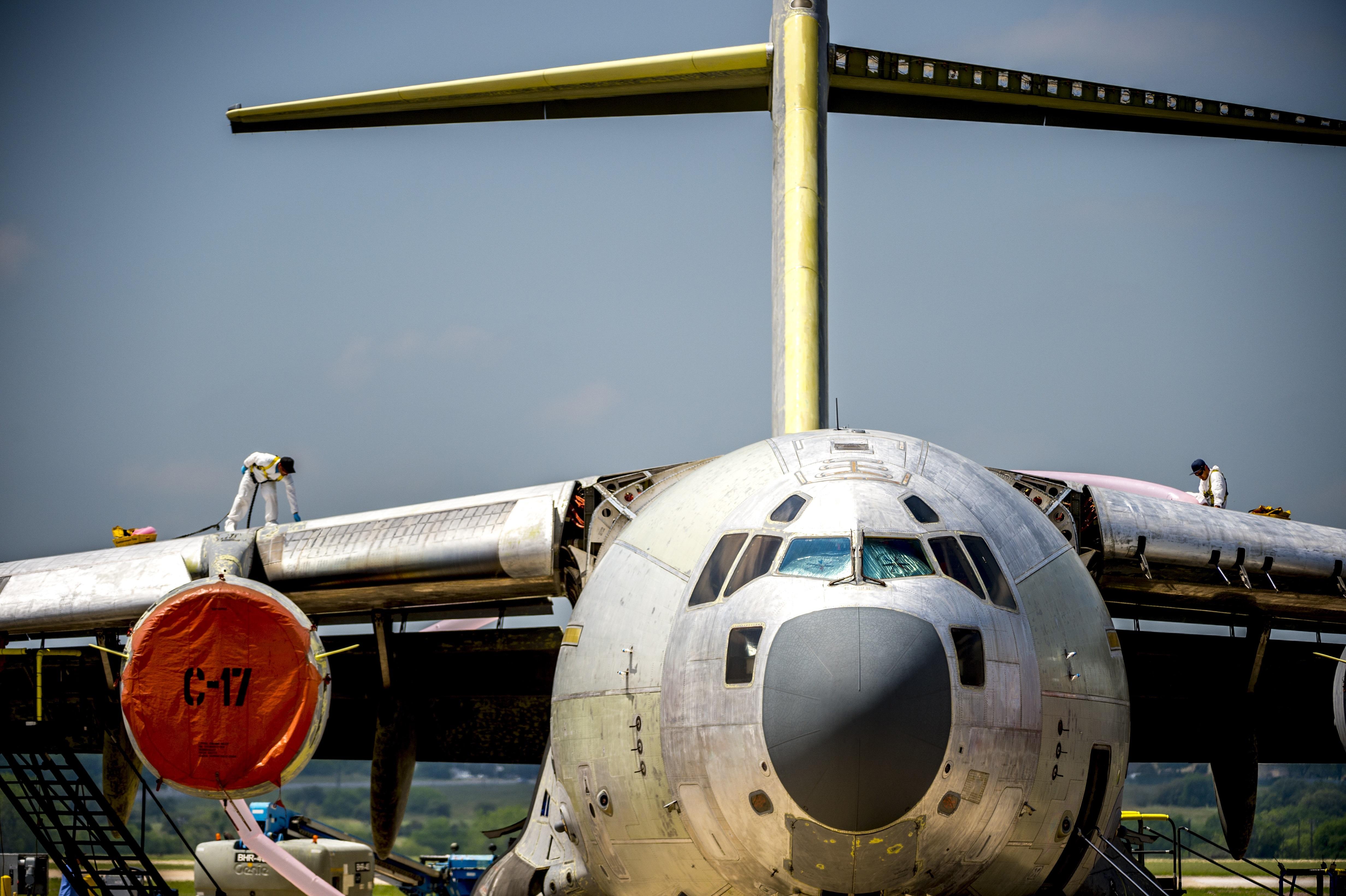
One of the maintenance programs underway is the C-17 Globemaster III Integrated Sustainment Program, which entails sustainment and heavy maintenance for global C-17 customers in eight allied countries. Galloway says Boeing has completed 27 different block upgrades to the aircraft so far.
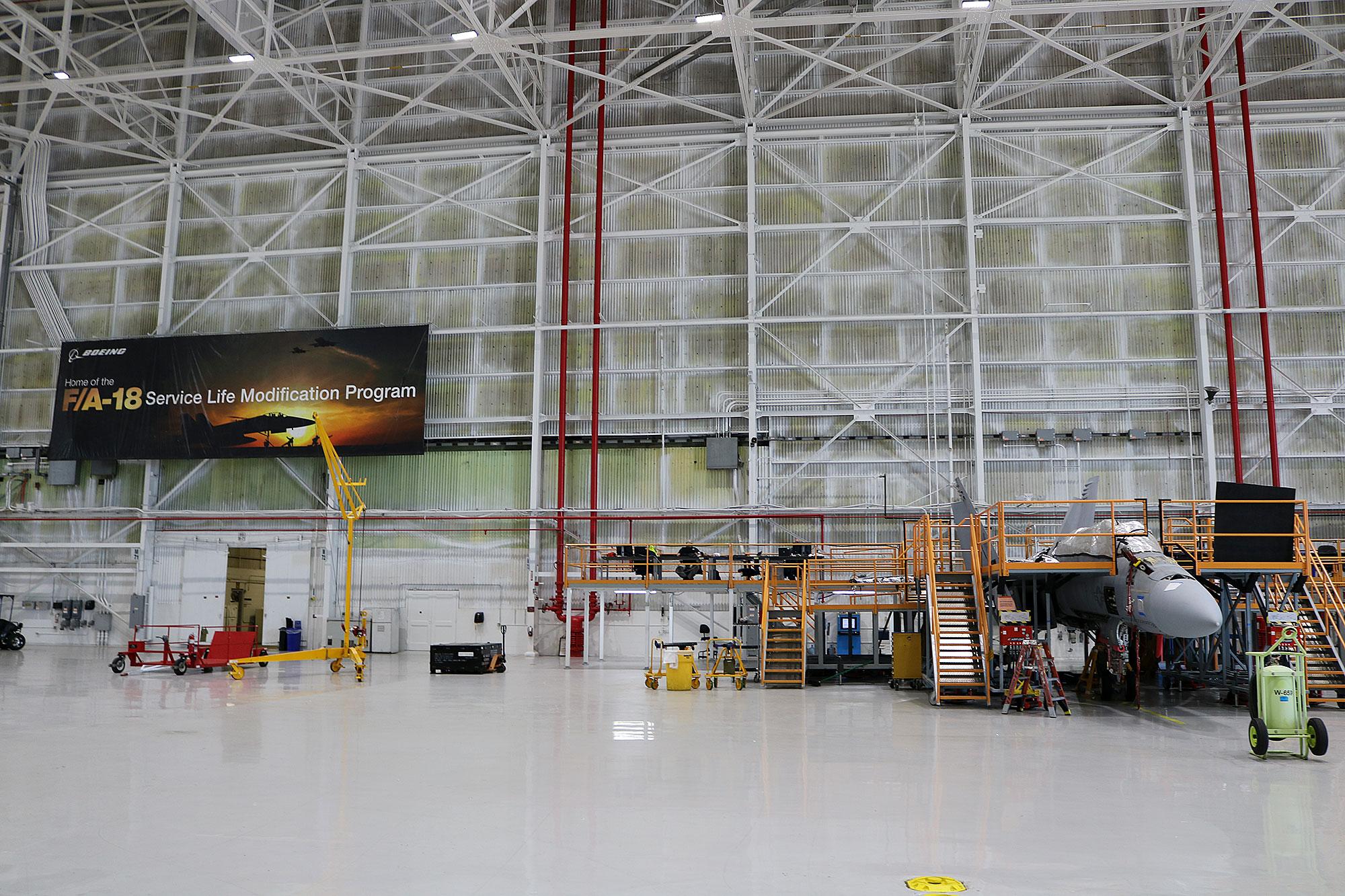
Started in June of this year, one of Boeing’s largest projects at the San Antonio site is the F/A-18 Super Hornet SLM program, which Holloway says is vitally important for the U.S. Navy fleet. The program entails extending the life of more than 500 aircraft from 6,000-10,000 flight hr., which will involve a mix of cockpit, fuel and paint work.

During Aviation Week’s visit, the site had four F/A-18 Super Hornets in-house—three of which were part of the SLM program and one that was in for mission capable work so it could go straight from “factory to boat.” For aircraft on the SLM line, Boeing is performing engineering analysis to find “hot spots” that won’t reach 10,000 hr. without needing service. Technicians are stripping open parts of the aircraft to perform inspections and fix corrosion from saltwater, as well as gutting cockpits to perform inspections and upgrade them with larger displays. The aircraft will also be de-painted via laser ablation and then re-painted.
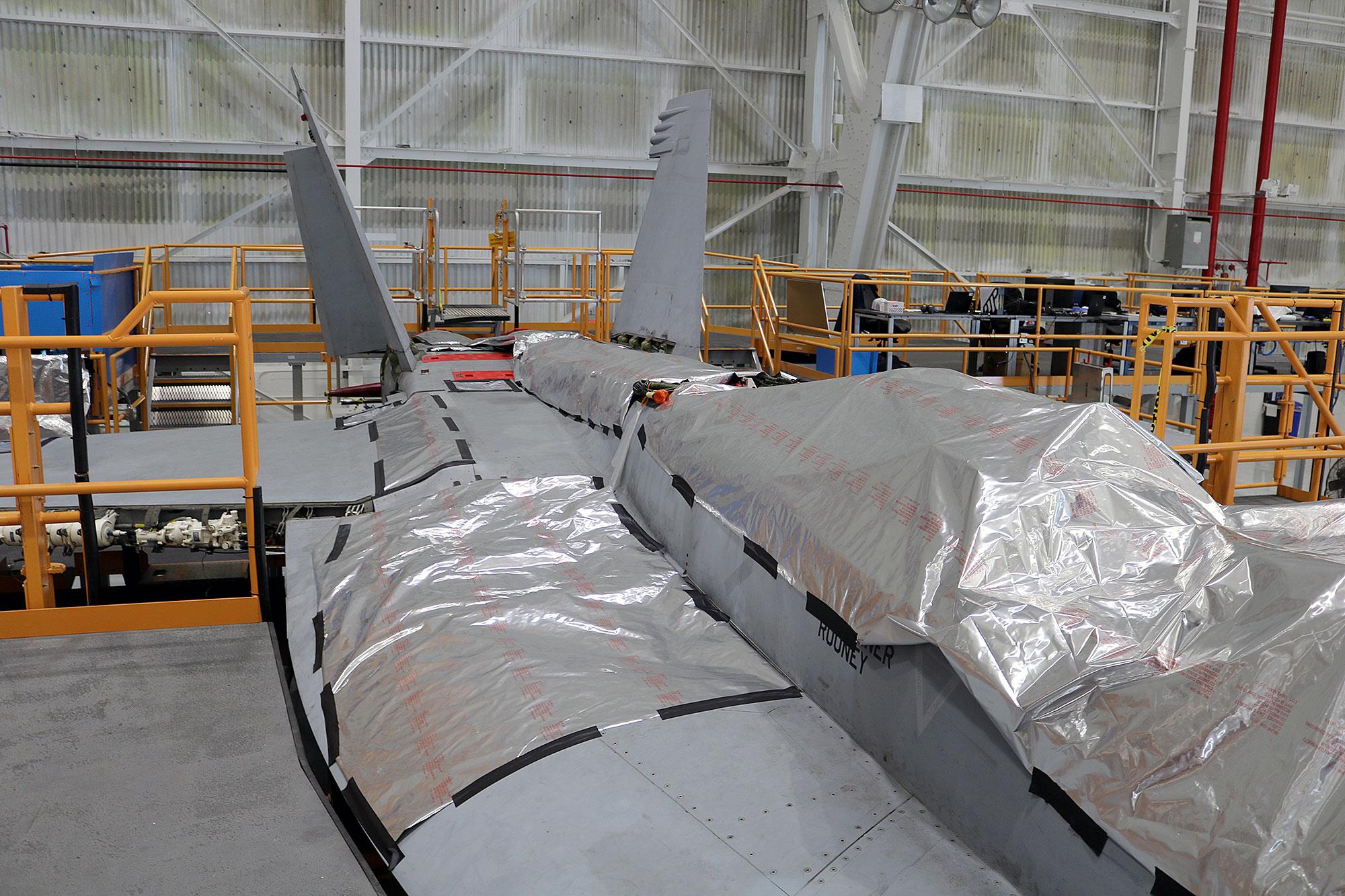
In total, the whole process for each aircraft will take around 18 months. The San Antonio site is starting with six aircraft this year, which will increase exponentially each year in a “crawl-walk-run effort.” Galloway estimates that next year the site will induct 12-16 aircraft, followed by 24 in 2021 and 32 in 2022. At the program’s peak, the site expects to work on up to 40 aircraft at a time over the 10-year project span.
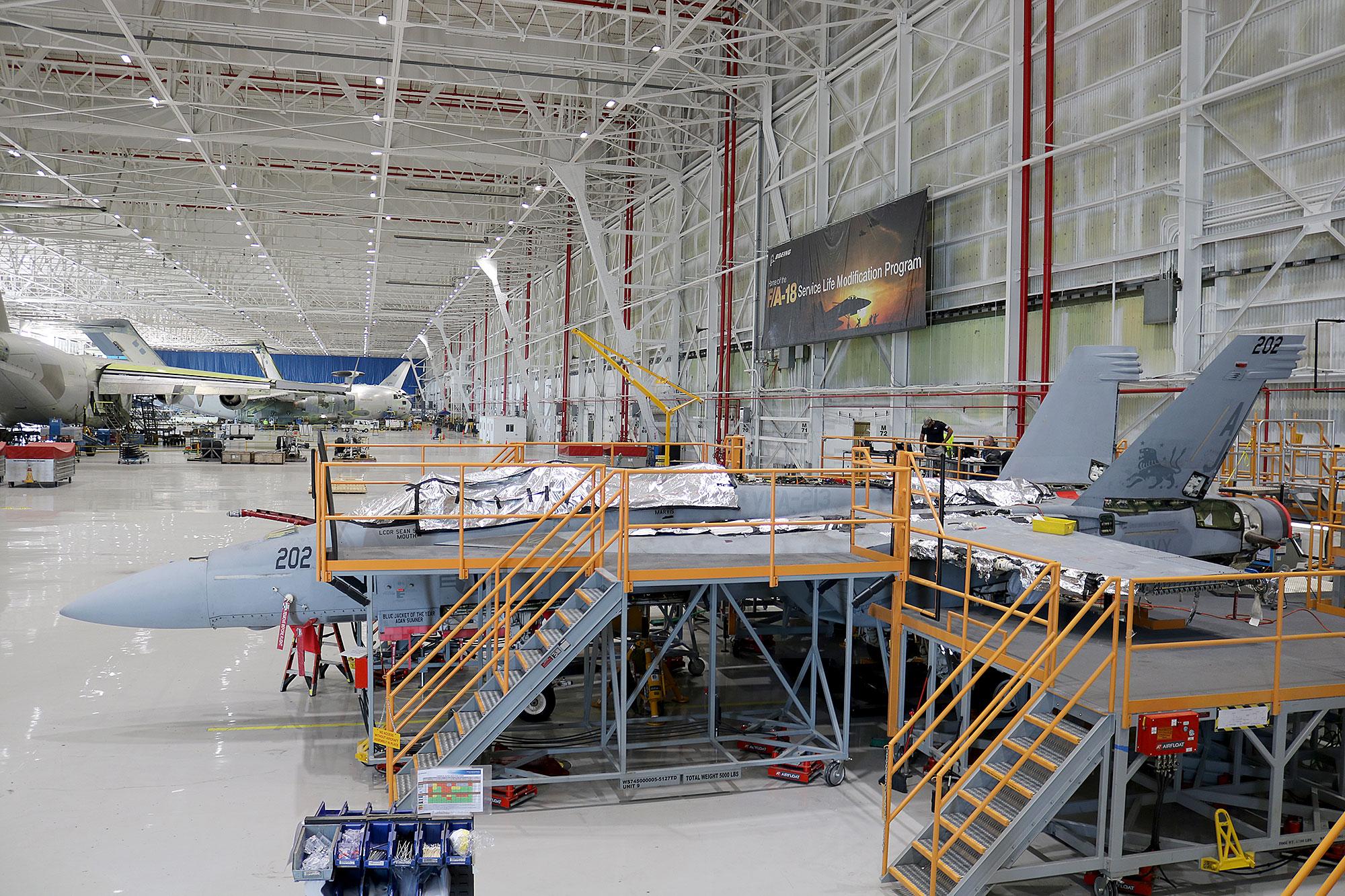
The dual-line program is split between Boeing’s St. Louis site and the San Antonio site—which is performing approximately 80% of the work. Galloway says the program is particularly exciting for San Antonio because it has not historically been a site for fighter maintenance, so it could pave the way for future fighter work.
“The F-15 is in some dire need of longeron upgrades and some other mission system mods, and we’ll probably be doing that work down here as well in the near future,” he says. “We’re going to become a big site for fighter aircraft—it’s going to get very noisy around here in a good way.”
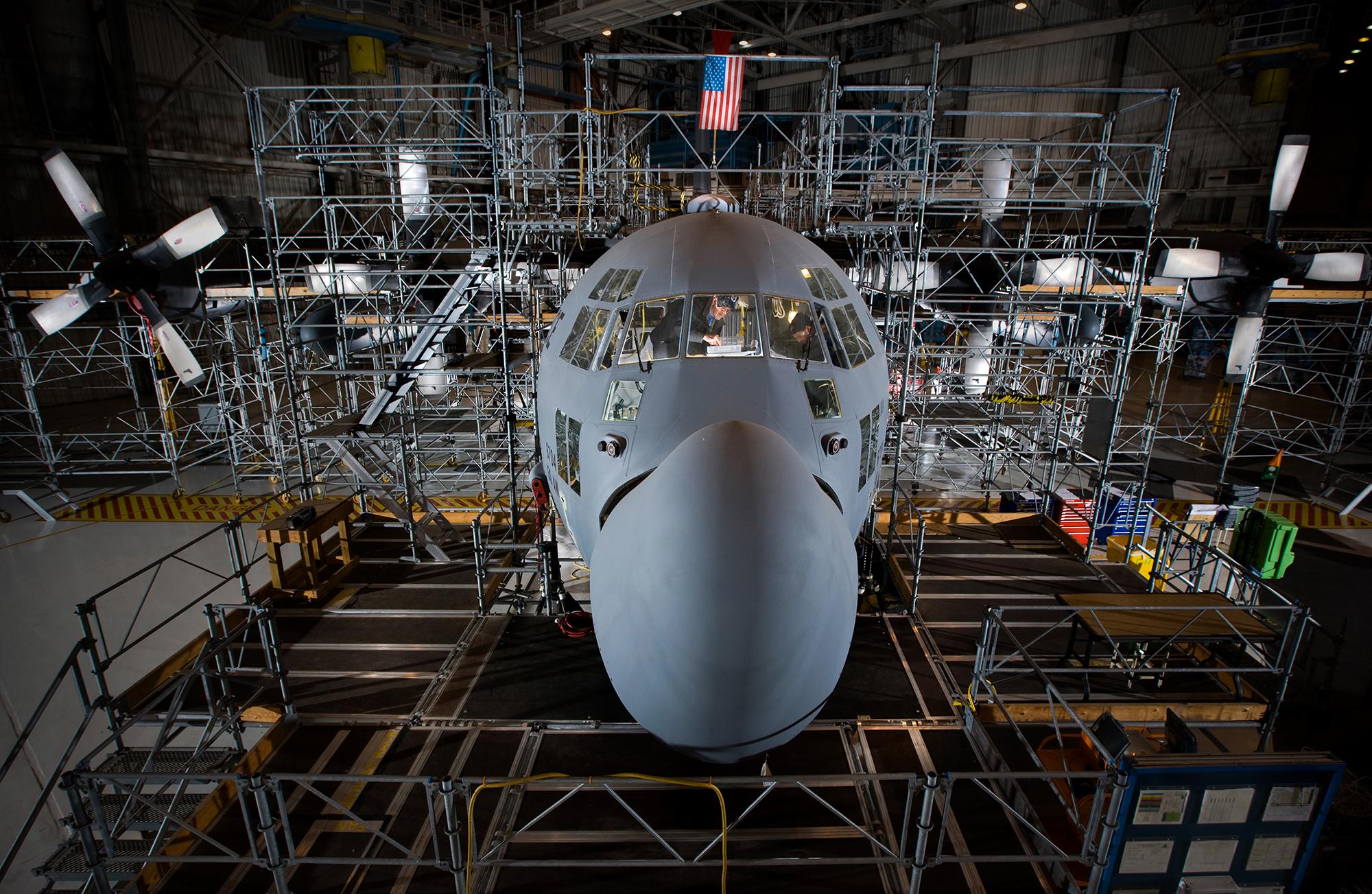
As the San Antonio site ramps up defense work, it is also borrowing ideas from the military. Modeled after the U.S. Air Force’s Big Safari program, which focuses on rapid procurement, Boeing has set up a rapid-response hangar at Port San Antonio to handle special requests or urgent needs falling outside the scope of routine maintenance contracts.
Galloway says the need to speed up the contracting process within aerospace has become important enough to Boeing’s customers that it decided to set up the hangar for rapid-response modifications, such as adding Wi-Fi, maintaining fuel tanks or replacing engines. He adds that although Boeing “hasn’t done anything big yet” at the hangar, it is working on ramping up its operations.
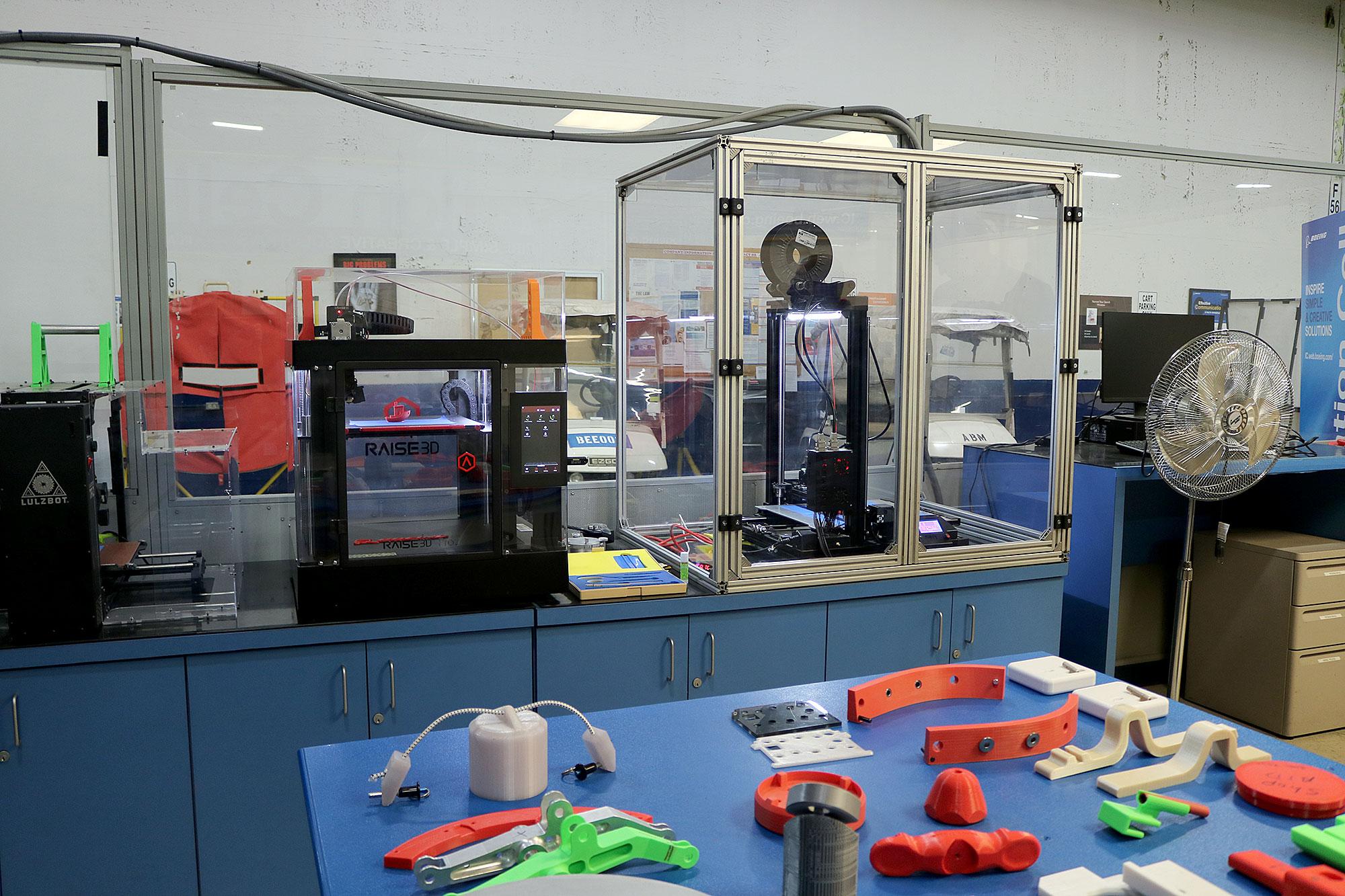
The Port San Antonio site is also transforming courtesy of its recent adoption under the Boeing Global Services (BGS) umbrella in 2017. According to Galloway, being a BGS site means San Antonio is now able to leverage its new technology innovations, such as big data analytics and predictive maintenance.
“We’re going to get the benefit of all that—which is immensely helpful when you’re doing heavy maintenance on airplanes—because it can predict what you’re going to get when the airplane gets here,” he explains. “It can help you predict what you need in your supply chain to be effective when the airplane gets here so you’re not waiting on things.”
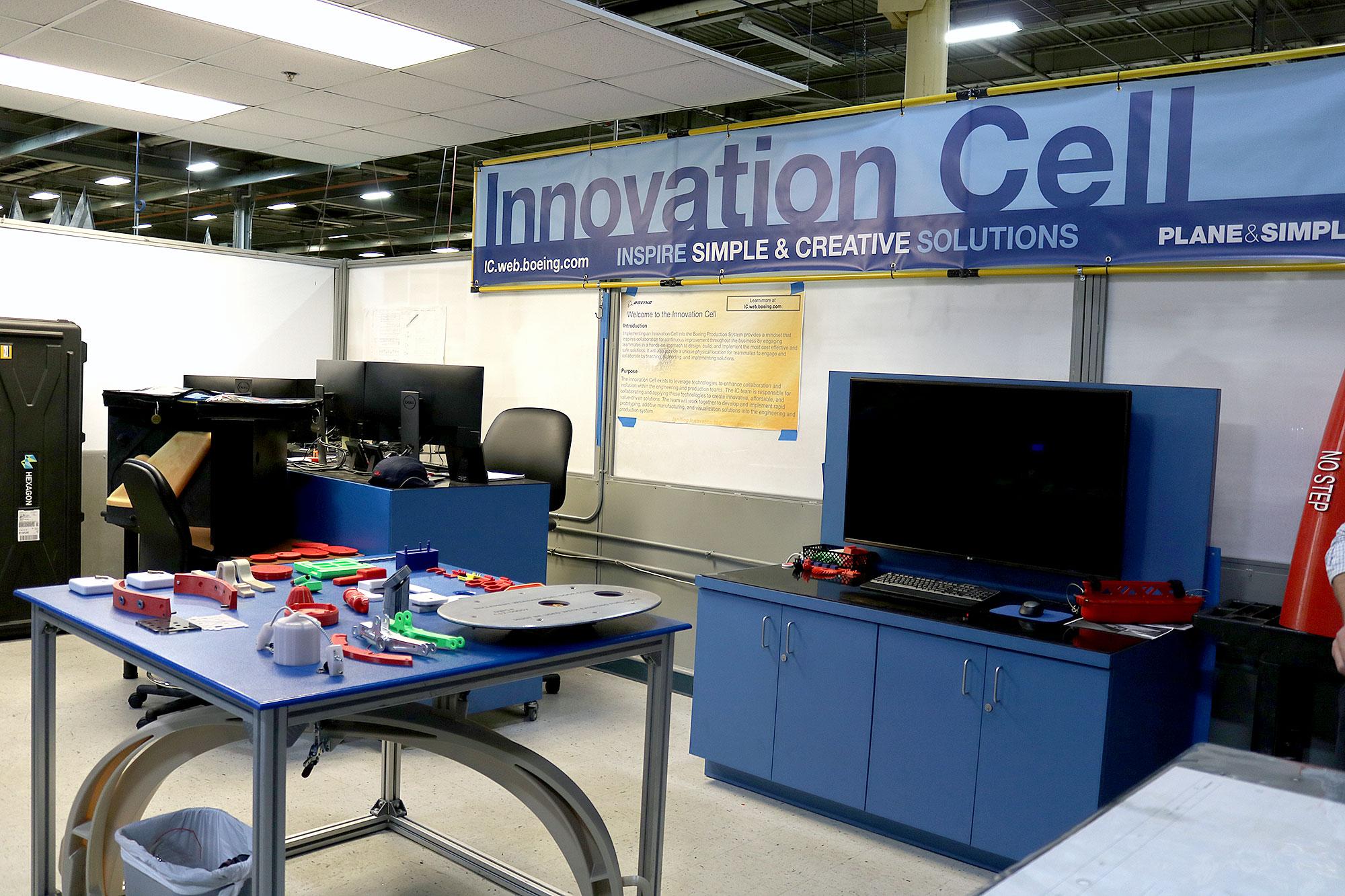
One way in which the site is working to drive technology adoption is through the establishment of an Innovation Cell, which Galloway says is part of the site’s plans to become an MRO center of excellence for innovation. Boeing’s plans for the Innovation Cell are to rotate all of the site’s employees through the space for a set period of time to introduce them to new technologies such as 3D printers so they can figure out how the tech can be used to tackle challenges encountered on the job.
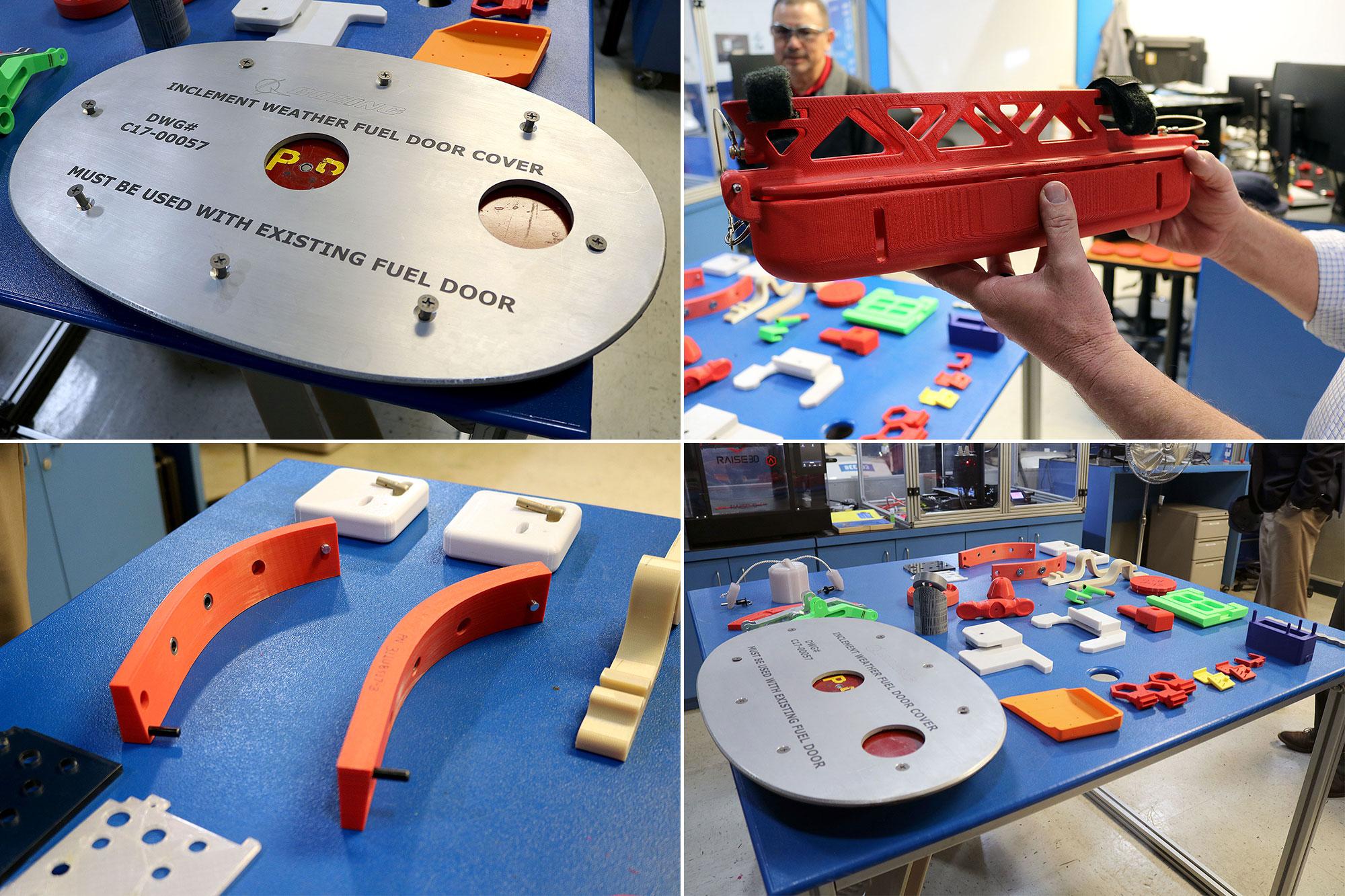
Galloway says Boeing has already established three patents out of the Innovation Cell less than one year in. Pictured here are some examples of solutions created at the Innovation Cell, including a fuel door cover for when it rains, a tool for drilling holes on contoured surfaces and a 3D-printed C-17 drain mass recovery tool, which consists of drain pans that attach to the aircraft itself for more convenient handling.
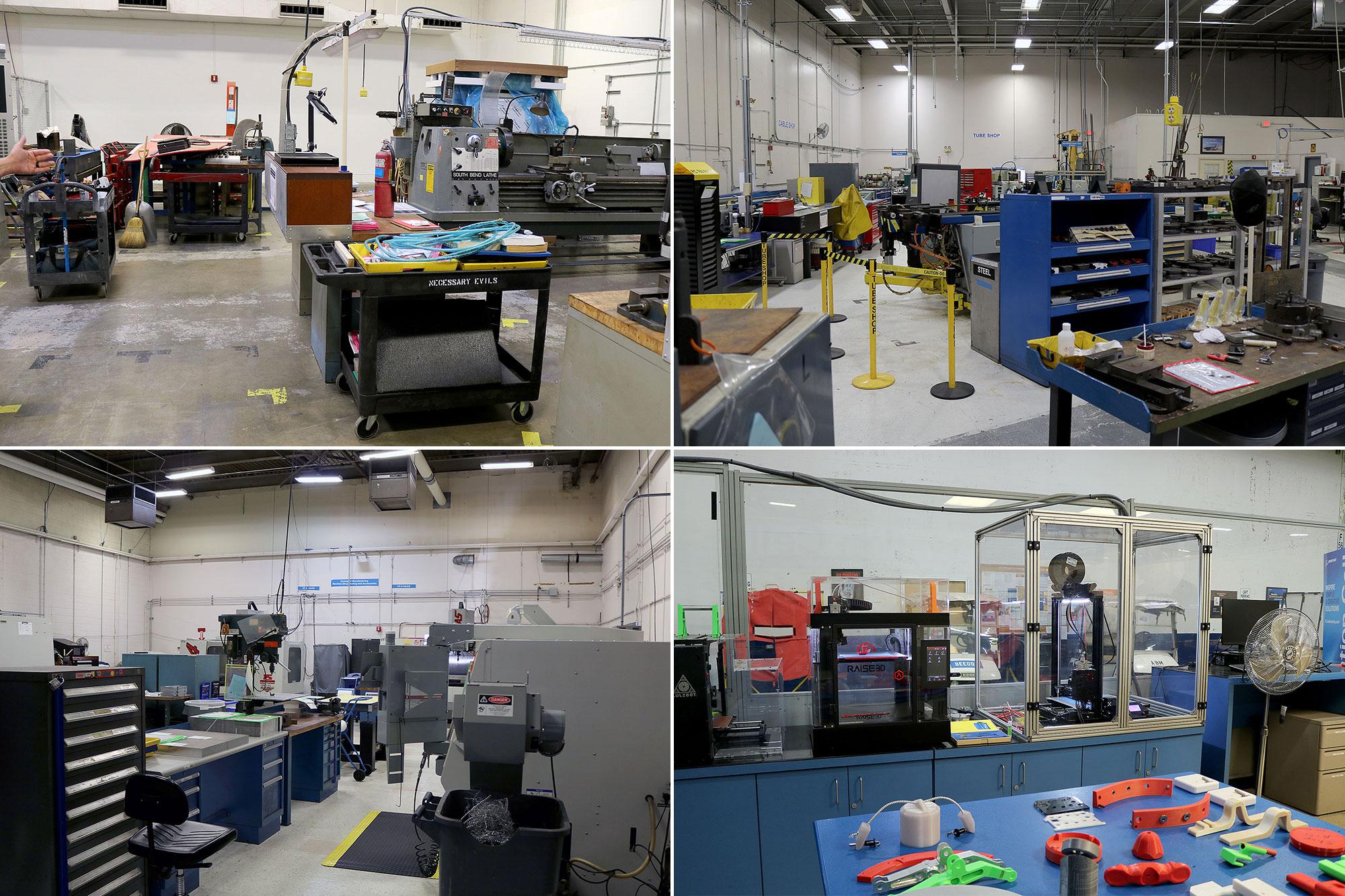
Galloway plans to expand the Innovation Center soon to a larger area within the site’s back shop. The company has purchased additional machinery to flesh out the Innovation Center, including a mini CNC machine and a Fortus 450 3D printer that can print parts of up to 30-in. Meanwhile, the back shop itself is used to build parts in-house to cut down on cost and time. Galloway envisions the site building 200-300 parts per day in the future to keep up with new programs, which he says would be “hugely impactful” to Boeing’s business in San Antonio.
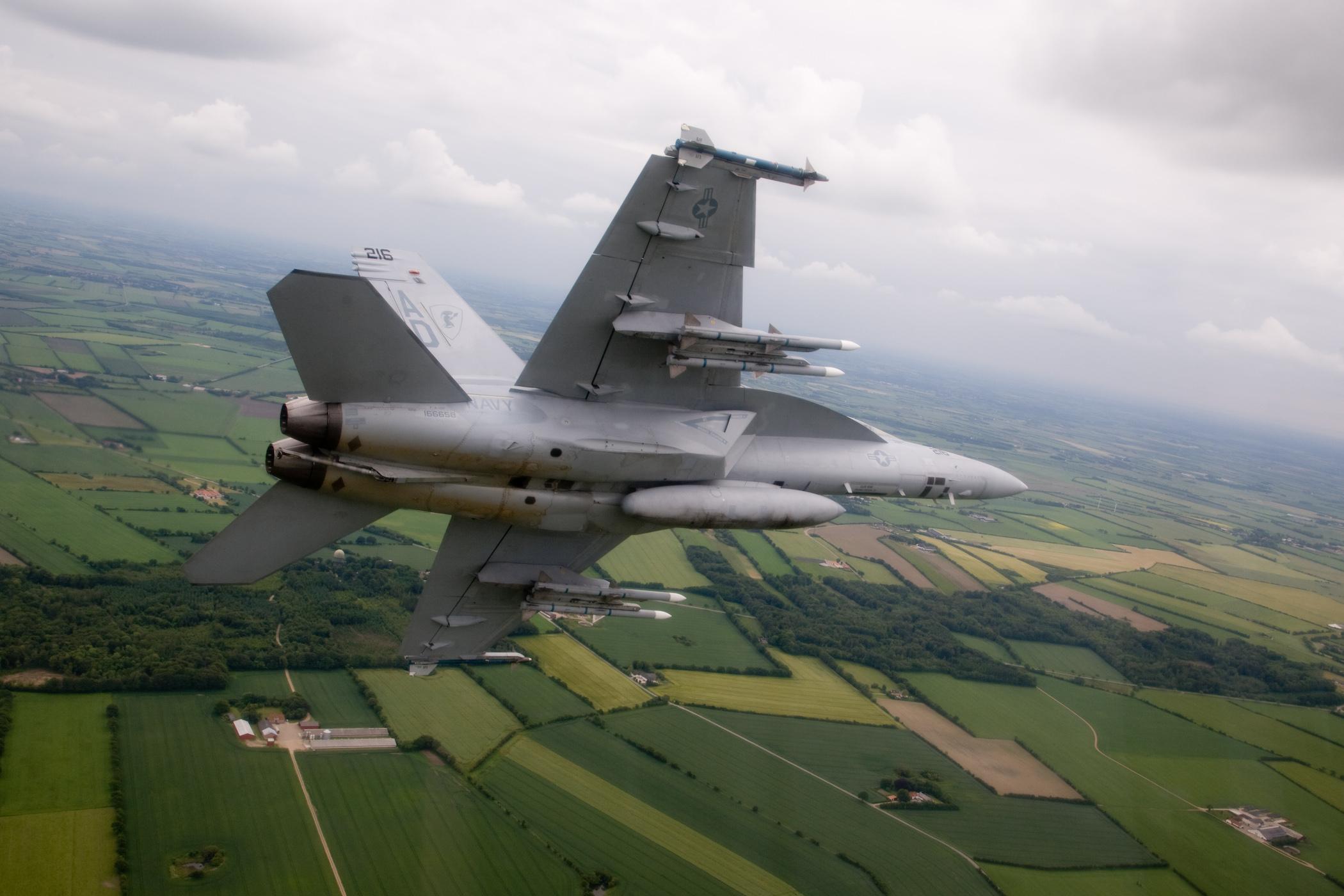
Another technology being implemented at the site is laser ablation for de-painting aircraft. “De-painting an aircraft with chemical stripper is an awful, ugly, arduous, environmentally unsound, unsafe process, so we want to get rid of it—and this is the perfect path,” says Galloway. Boeing has a three-story working prototype to laser C-17 aircraft and Galloway says the U.S. Navy is funding the technology for full scale laser ablation, which Boeing is on contract to provide for F/A-18s.
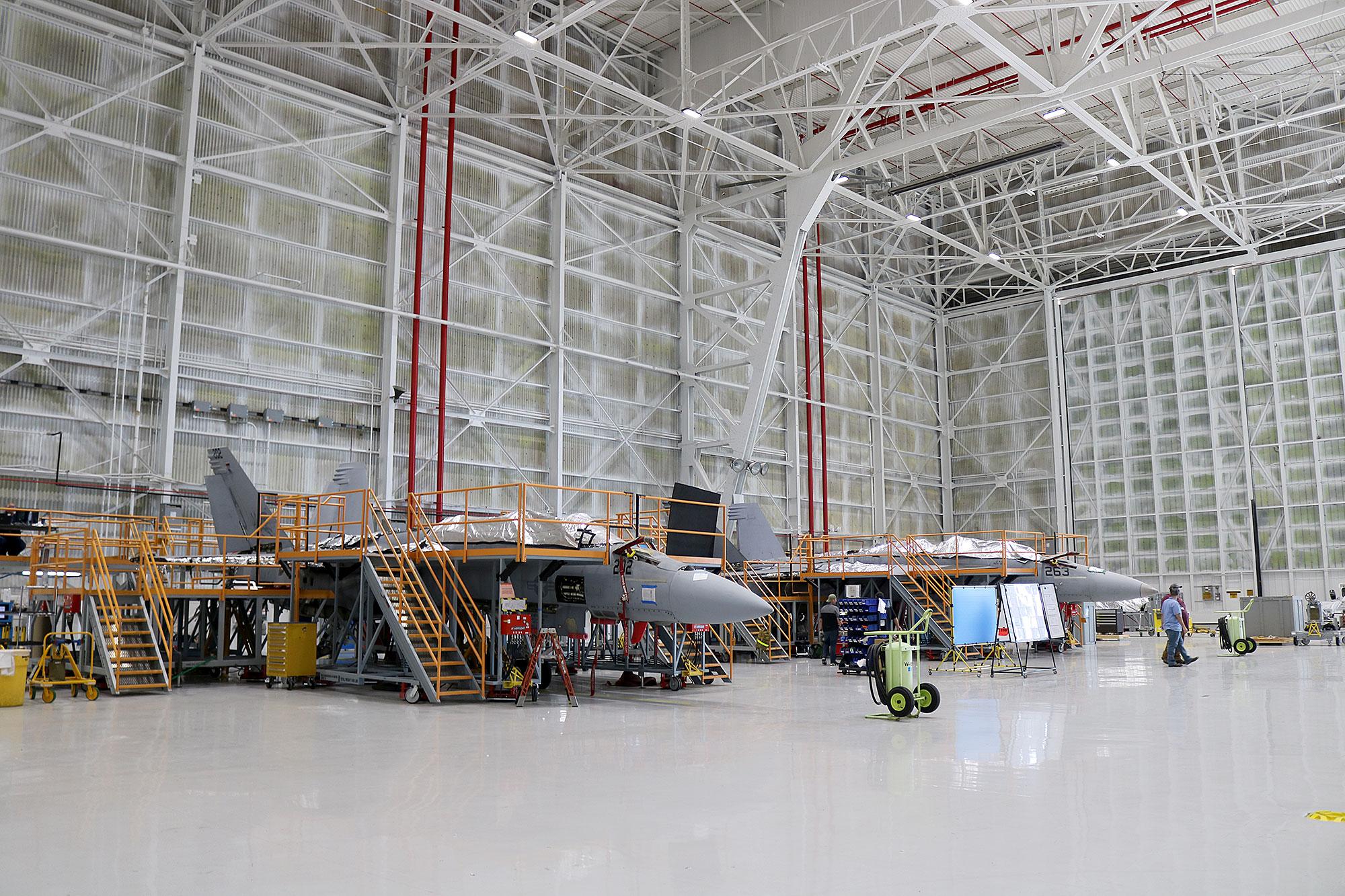
In terms of other technologies, the San Antonio site is paperless and recently rolled out a new software system tailored for MRO called GOLDesp. It is also pursuing RFID for tracking parts and tools, as well as 3D printing of parts through the Innovation Cell.
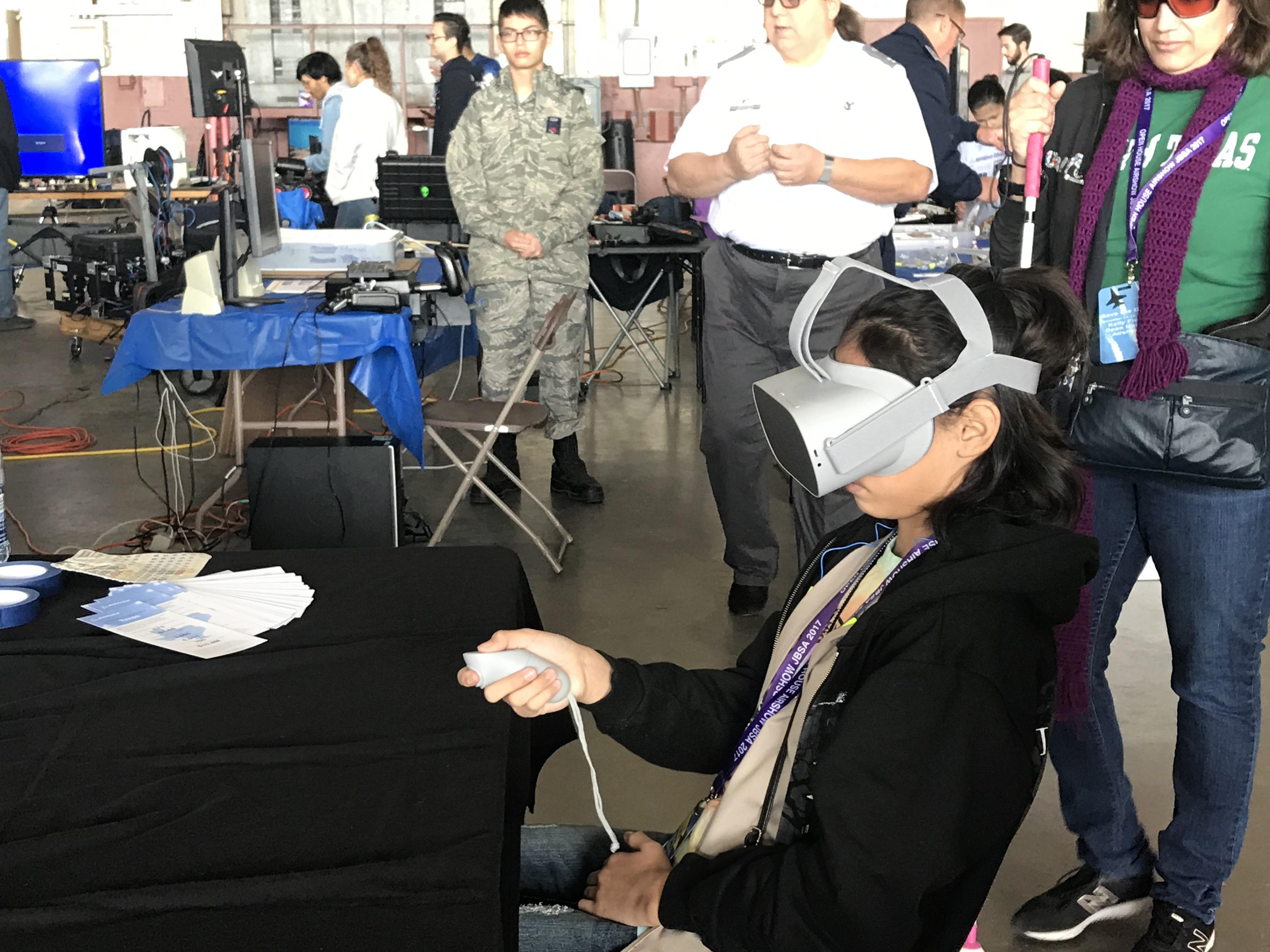
Boeing is hoping to leverage Port San Antonio’s upcoming Innovation Center to help it collaborate with other local innovators and stakeholders. The company is already working with Port San Antonio resident Southwest Research Institute and has participated in STEM initiatives on site, such as the Kelly Field Youth Aerospace Expo, where it engaged with youth through displaying technology such as 3D printers and virtual reality headsets. Boeing also recently donated $100,000 to the Port’s San Antonio Museum of Science and Technology for STEM programming in lower-income neighborhoods.
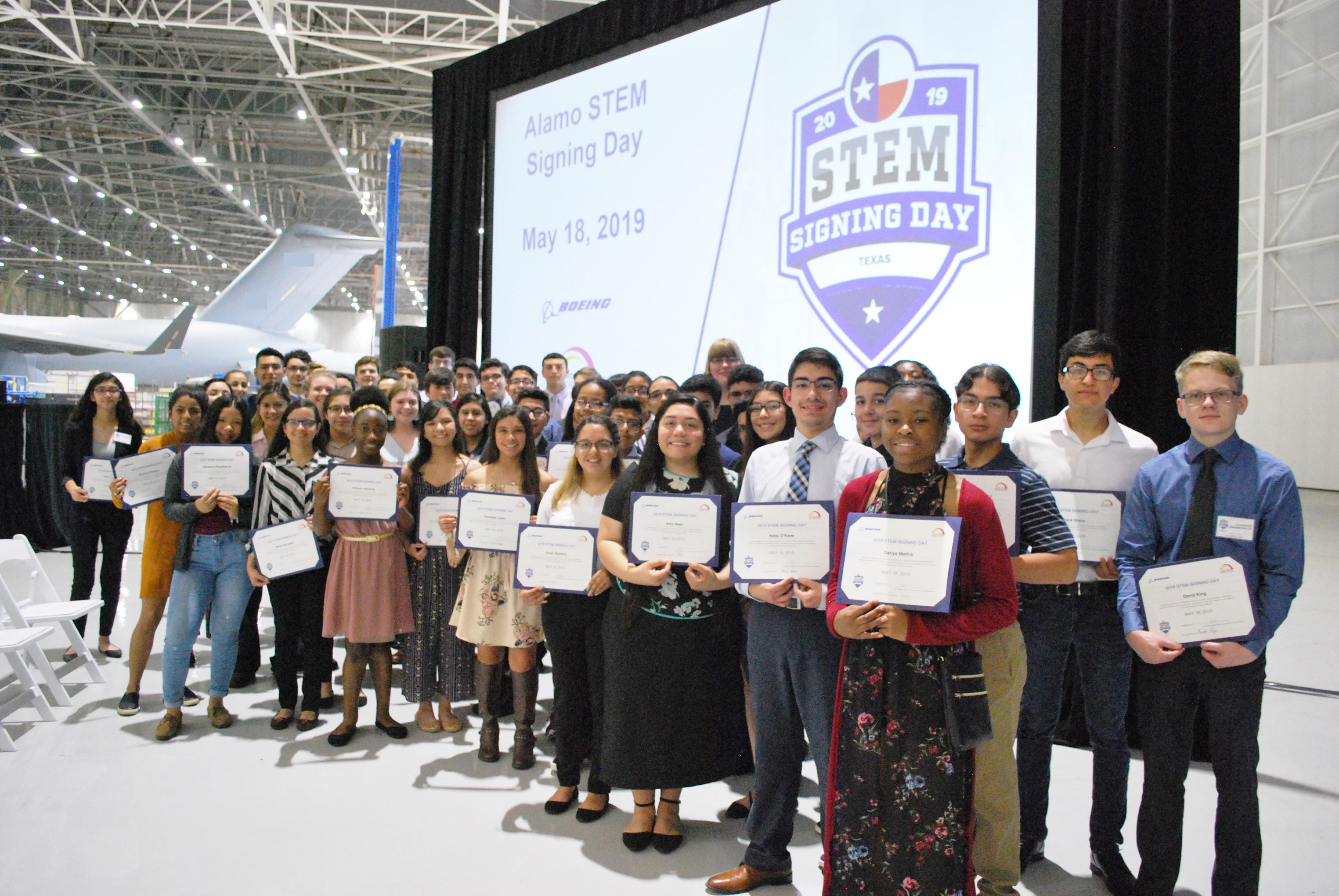
The San Antonio site recently held a STEM signing ceremony for 60 students going into high school or college who were choosing either a STEM endorsement or a STEM career. Boeing brought the students on-site to participate in a large signing ceremony reminiscent of the ones in the sports industry, which took place on a stage underneath the wing of a C-17.
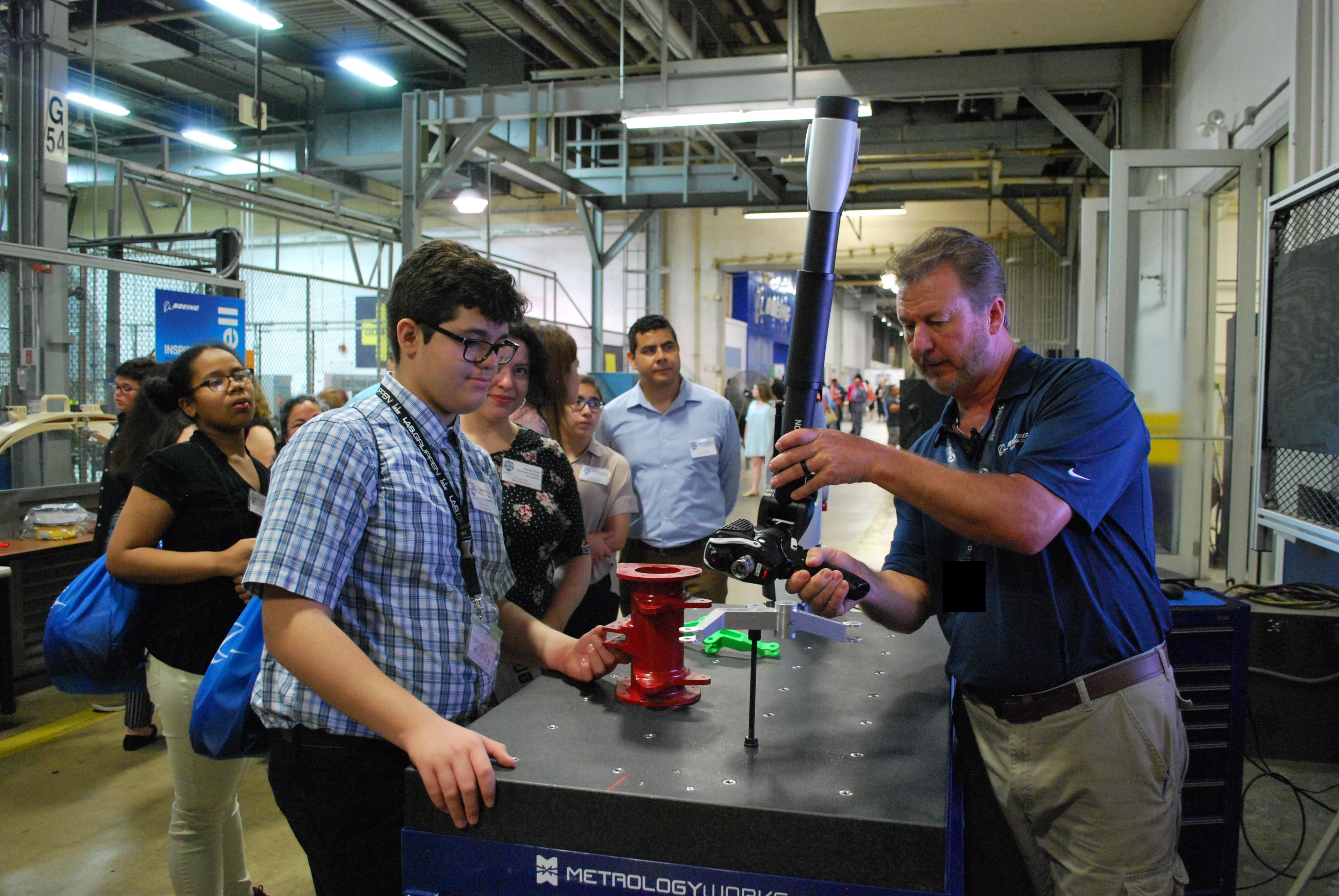
According to Galloway, these STEM initiatives are a crucial part of building up the workforce pipeline, since hiring skilled technicians remains a challenge despite San Antonio’s large veteran talent pool.
“I go through thousands [of applicants] to get hundreds [of hires],” says Galloway. “It’s hard to find the right kind of talent—sometimes you have to be patient because it takes a while. You have to work with places that are developing talent, such as trade schools, colleges and universities.”
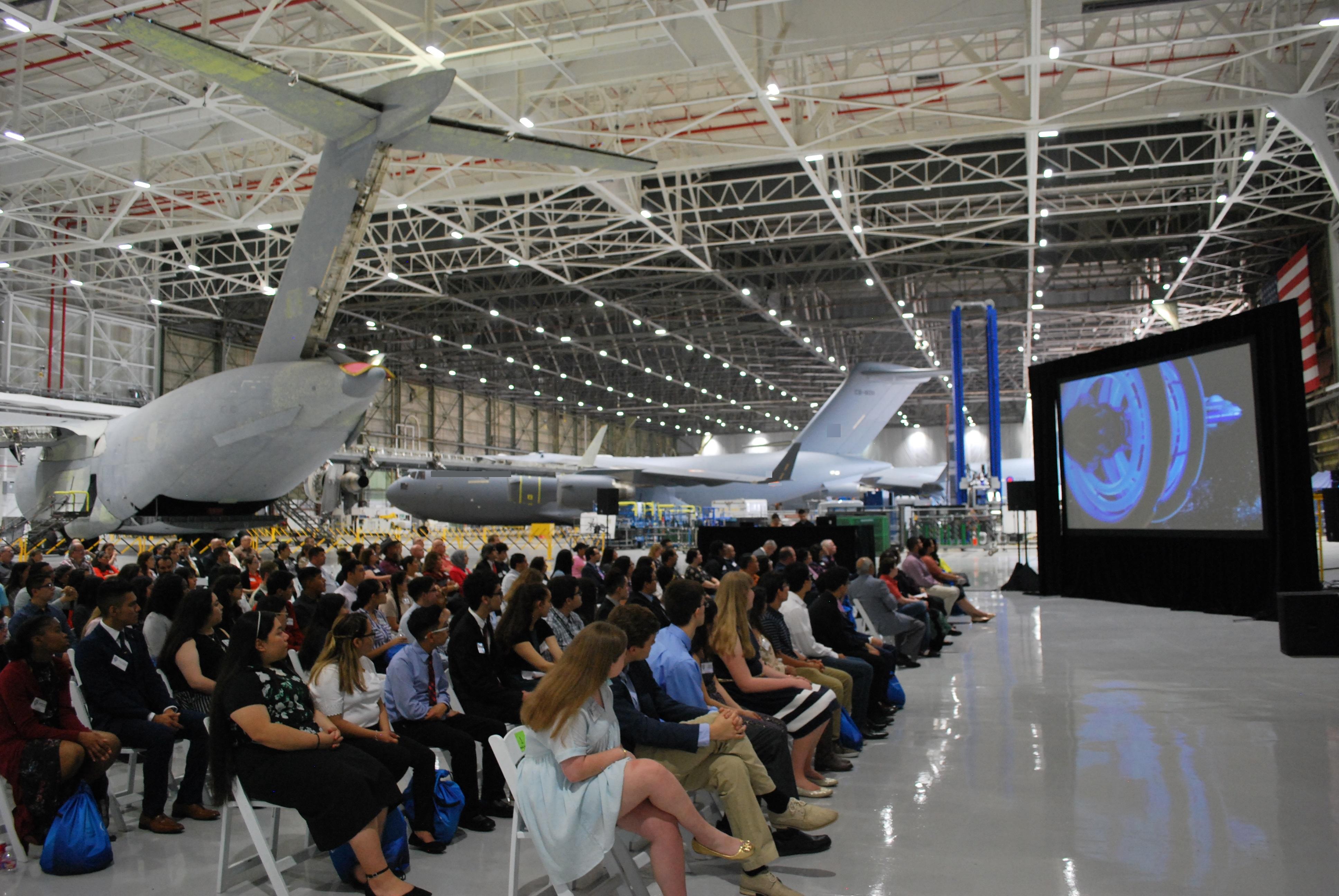
Boeing San Antonio is working with local schools such as Hallmark University and St. Philips College, while also taking advantage of larger Boeing workforce initiatives such as those with USO Pathfinder, which connects transitioning veterans to career opportunities. Nearly half of Boeing’s workforce at the San Antonio site are veterans and the company is planning to double its staff of approximately 1,200 employees over the next two years.
A look at how Boeing’s 168-acre facility at Port San Antonio is growing maintenance programs, innovation and workforce.
Comments