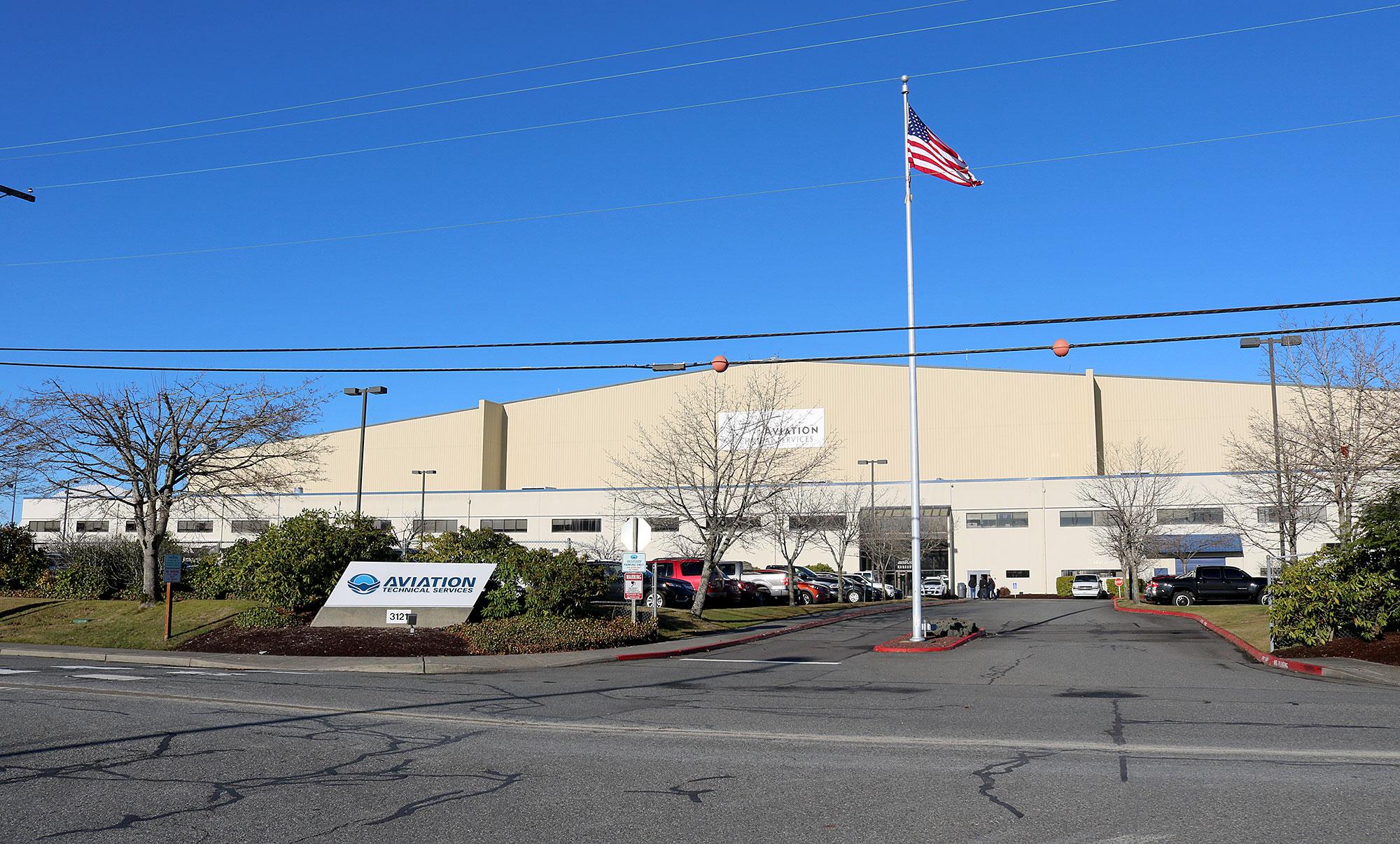
In addition to its 253,000 sq. ft. hangar space, Hangar 1 houses office space for its employees and airline customers. ATS partnered with Ghafari Associates Aviation Division in 2016 to develop a multi-phase 10-year plan to remodel the facilities. First to be overhauled was the engineering department, which had an immediate need for growth. ATS says the next focus will be operational improvements and equipment for the hangars and component areas.
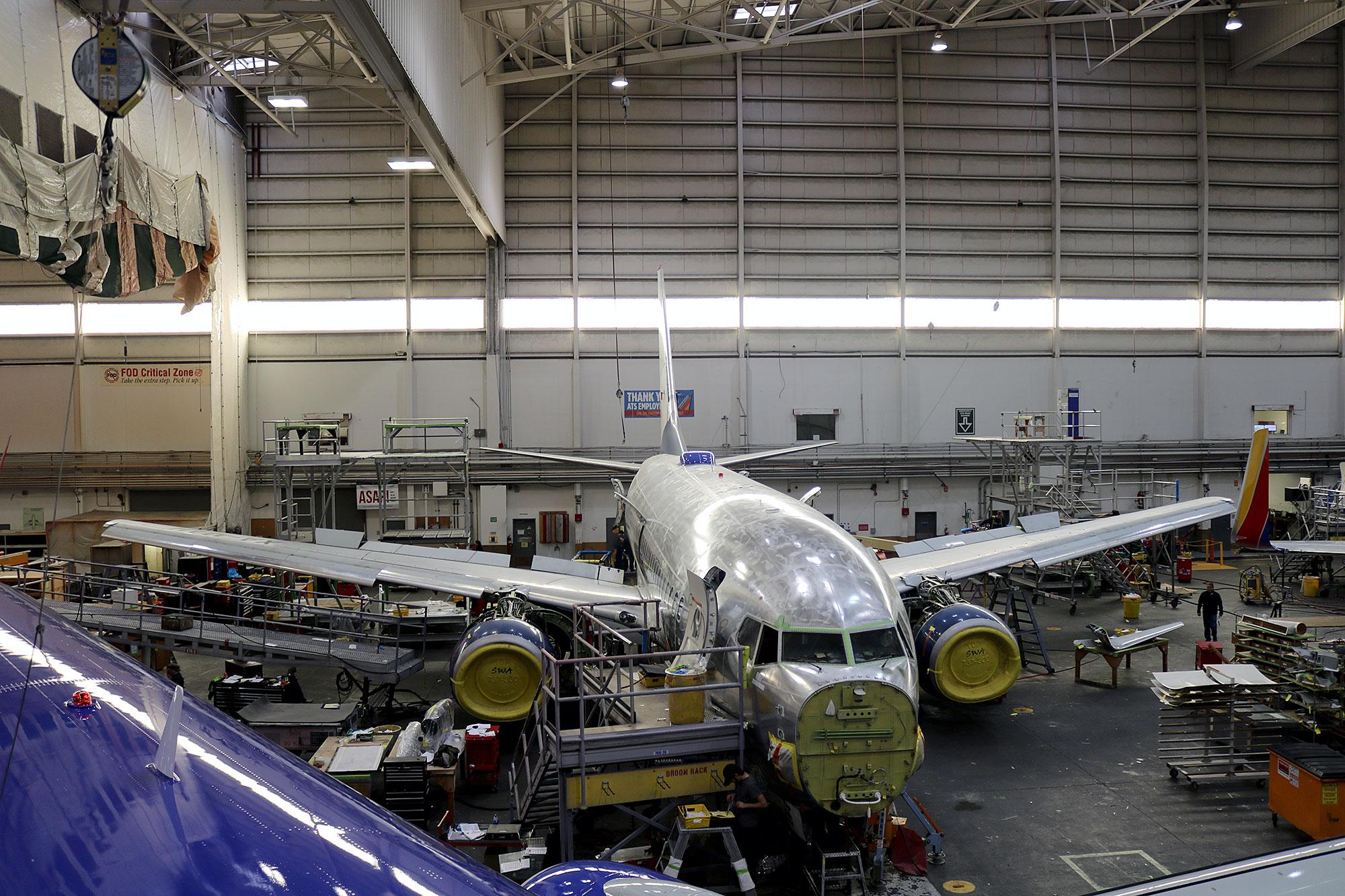
Hangar 1, which can fit up to 11 737 aircraft, was bustling during Aviation Week’s visit. ATS delivers over 500 Boeing and Airbus narrow and widebody aircraft annually to many major carriers. Most recently, the MRO has been heavily focused on its Skyline program.
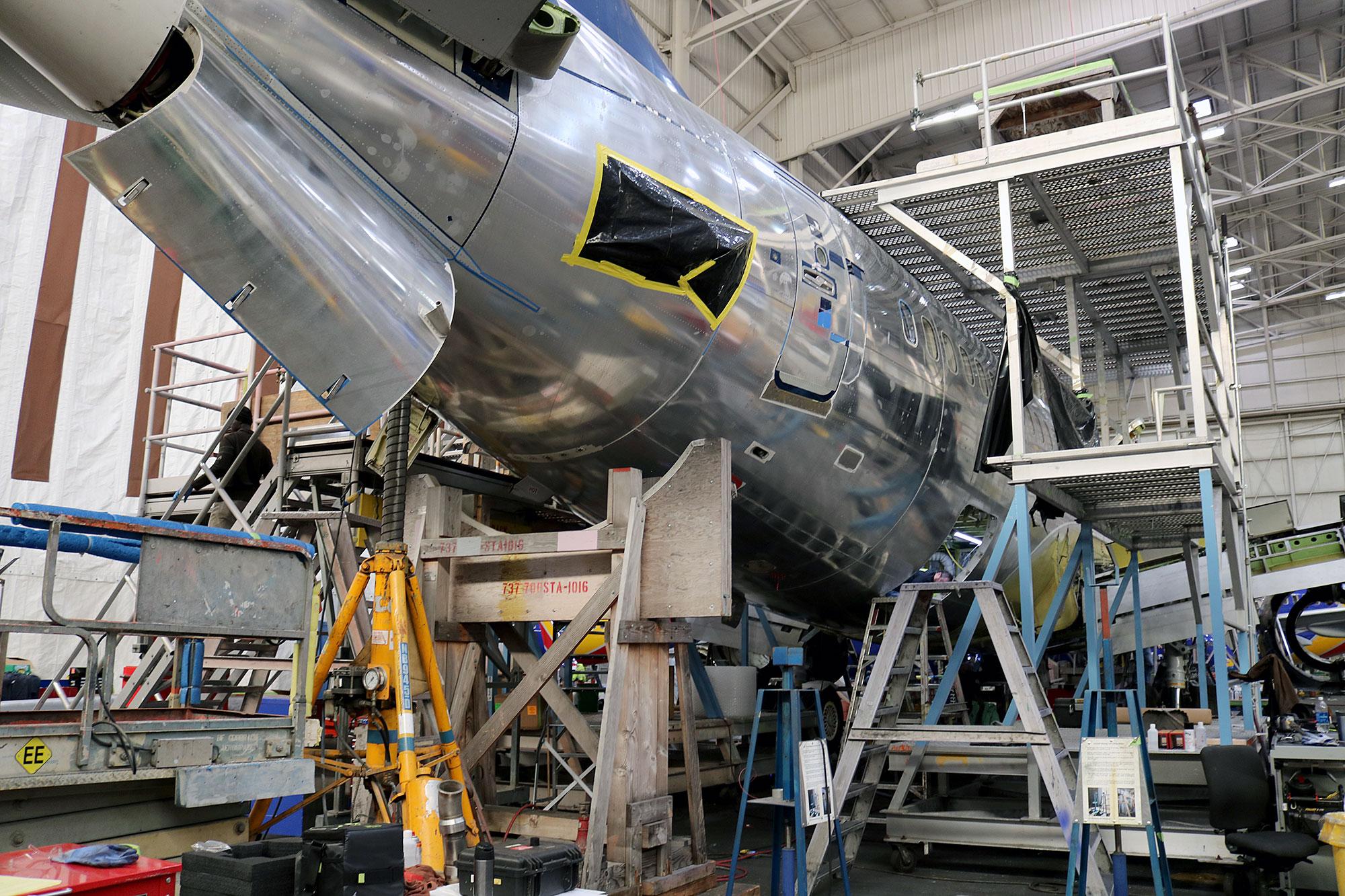
ATS says the Skyline program is how Southwest—one of its biggest clients—is able to add capacity quickly to meet demands. Through the program, ATS brings used aircraft purchased by Southwest into its fleet specifications. According to a spokesperson for ATS, these aircraft look brand new by the time the MRO is done with them.
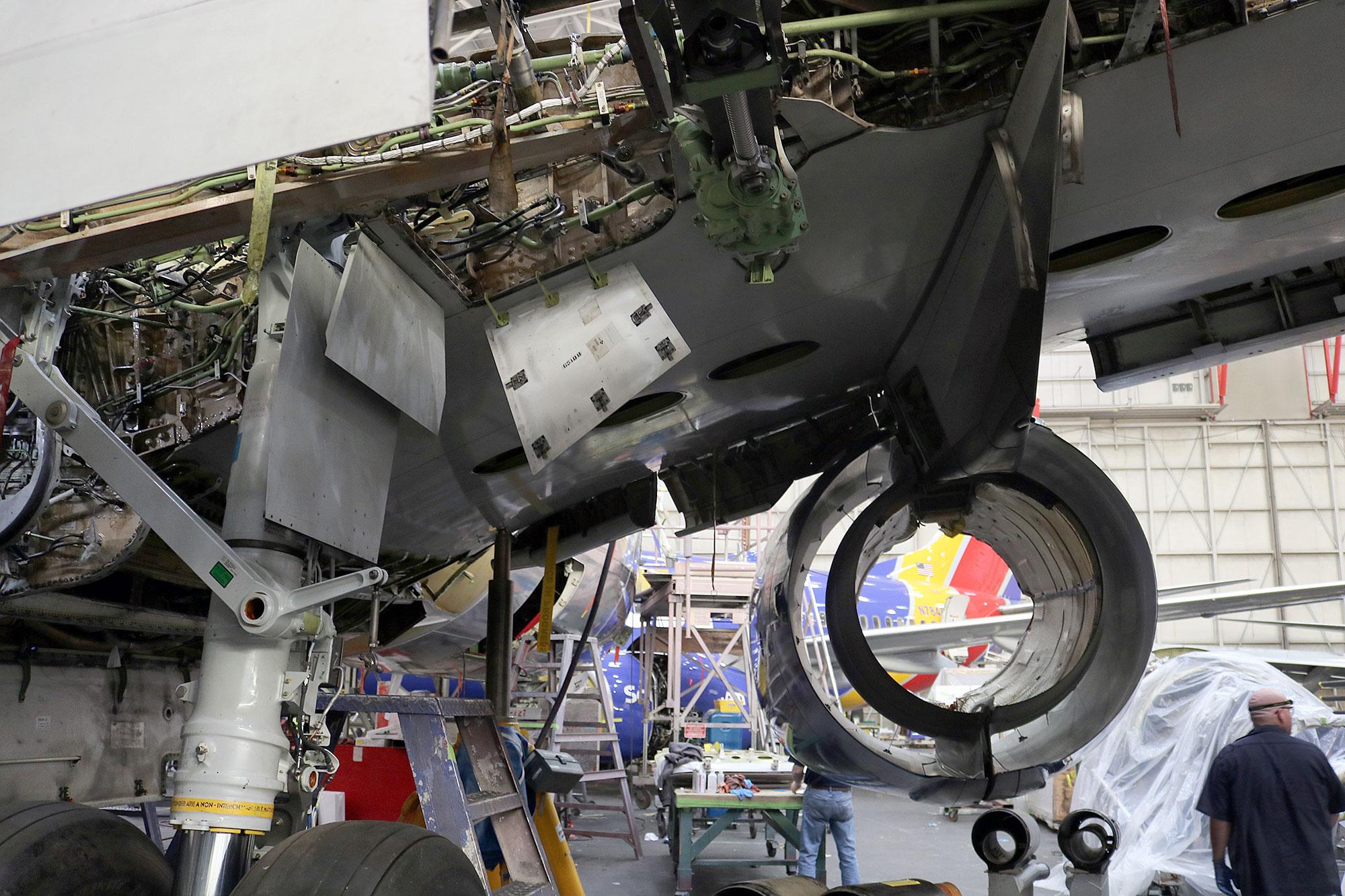
To date, the average conversion span time for the Skyline program is 60 days, with the range of transitions running somewhere between 41-83 days depending on the age and condition of the aircraft.
According to ATS COO Paul Dolan, the MRO is focusing on improving span times for 2018. "We're working hard to deliver shorter, more consistent span times to our customers," says Dolan. "We call it Velocity and we’re already making gains in our Airframe business. We look forward to rolling out Velocity to all our businesses over time."
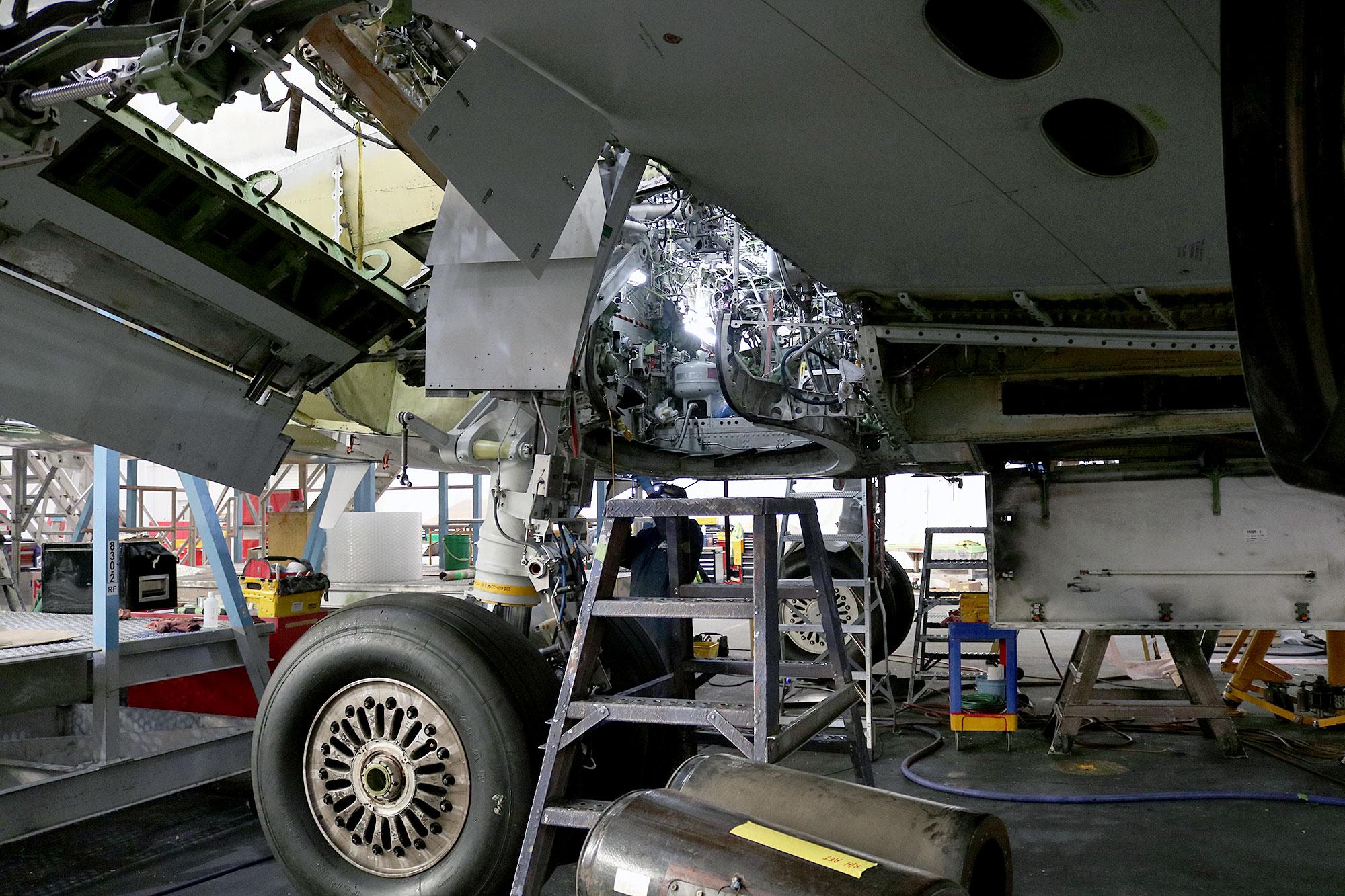
So far, ATS has completed 80 aircraft for Southwest through the Skyline program since its start in 2014. 27 aircraft were completed in 2016 and ATS says the final number of completions for 2017 will be 15.
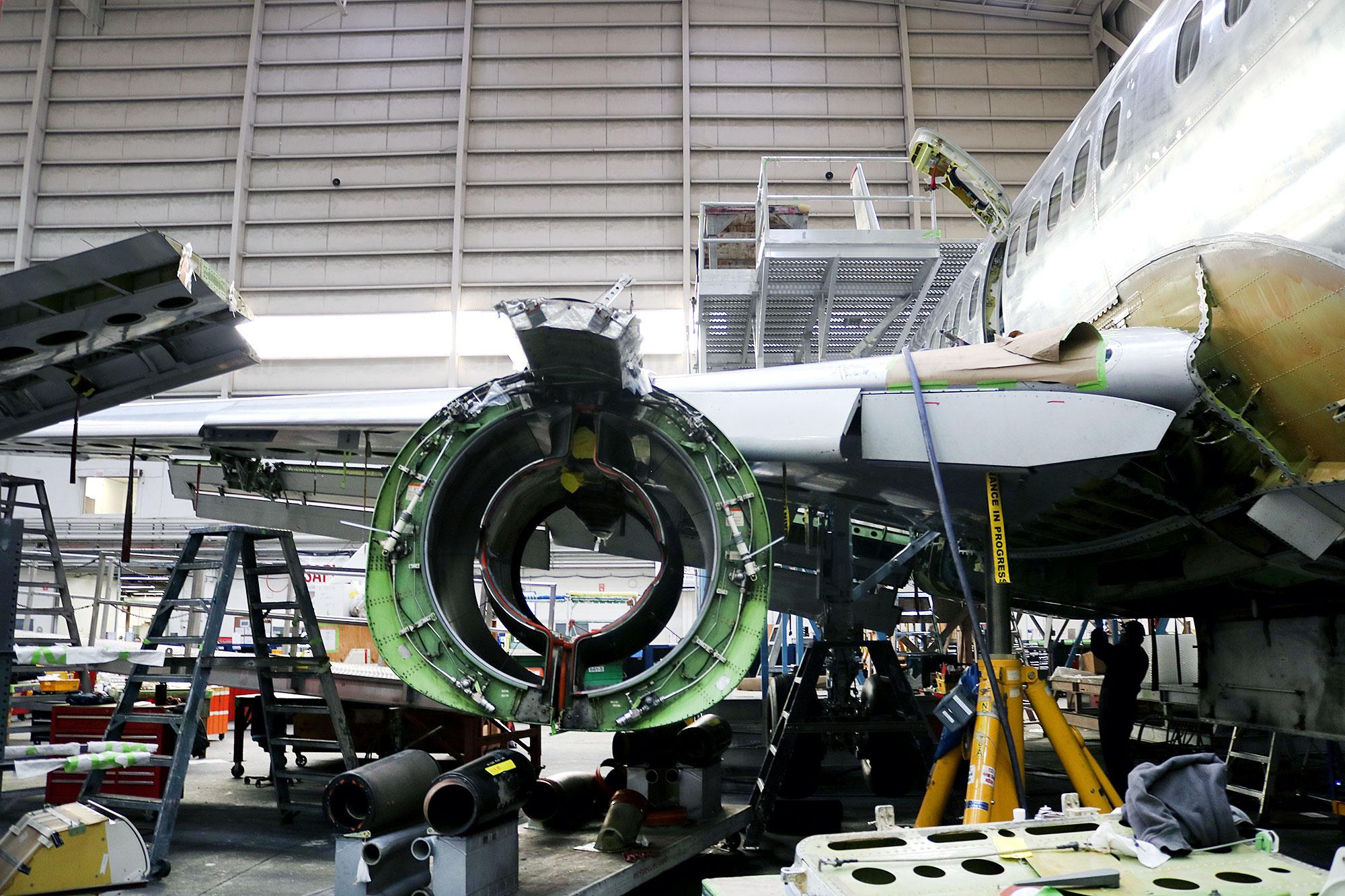
ATS recently completed a similar project for a major European airline, where reconfigurations were performed on nine mid-life Airbus A319 aircraft being introduced into the carrier’s fleet.
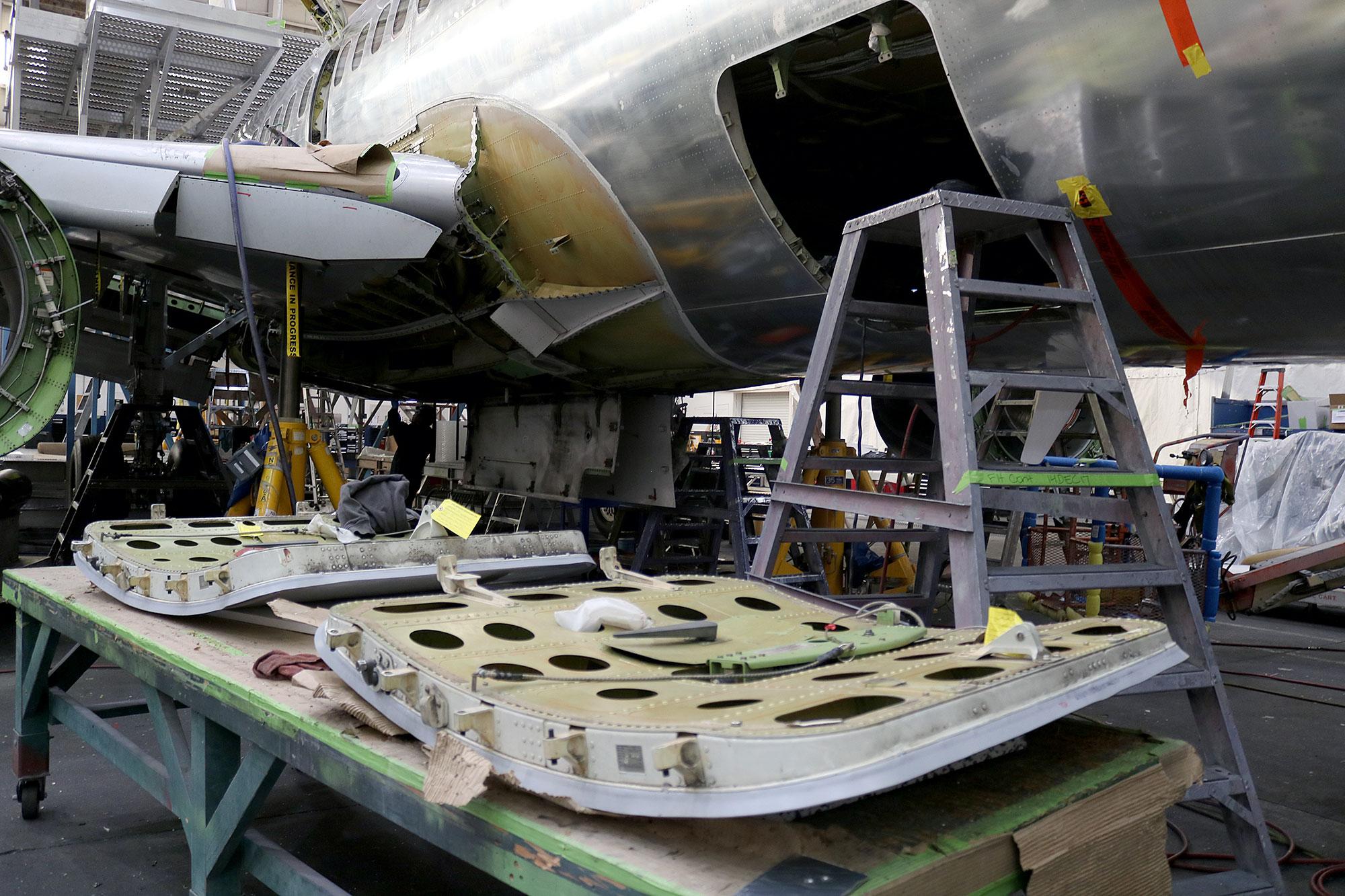
According to ATS, its MRO of the Year win for 2016 was thanks in part to having both the engineering and supply chain for the aircraft in conversion under one roof. ATS says the timeframe to resolve issues during conversion is significantly reduced because engineering or supply chain can lay eyes on the issue and work directly with maintenance to get it resolved.
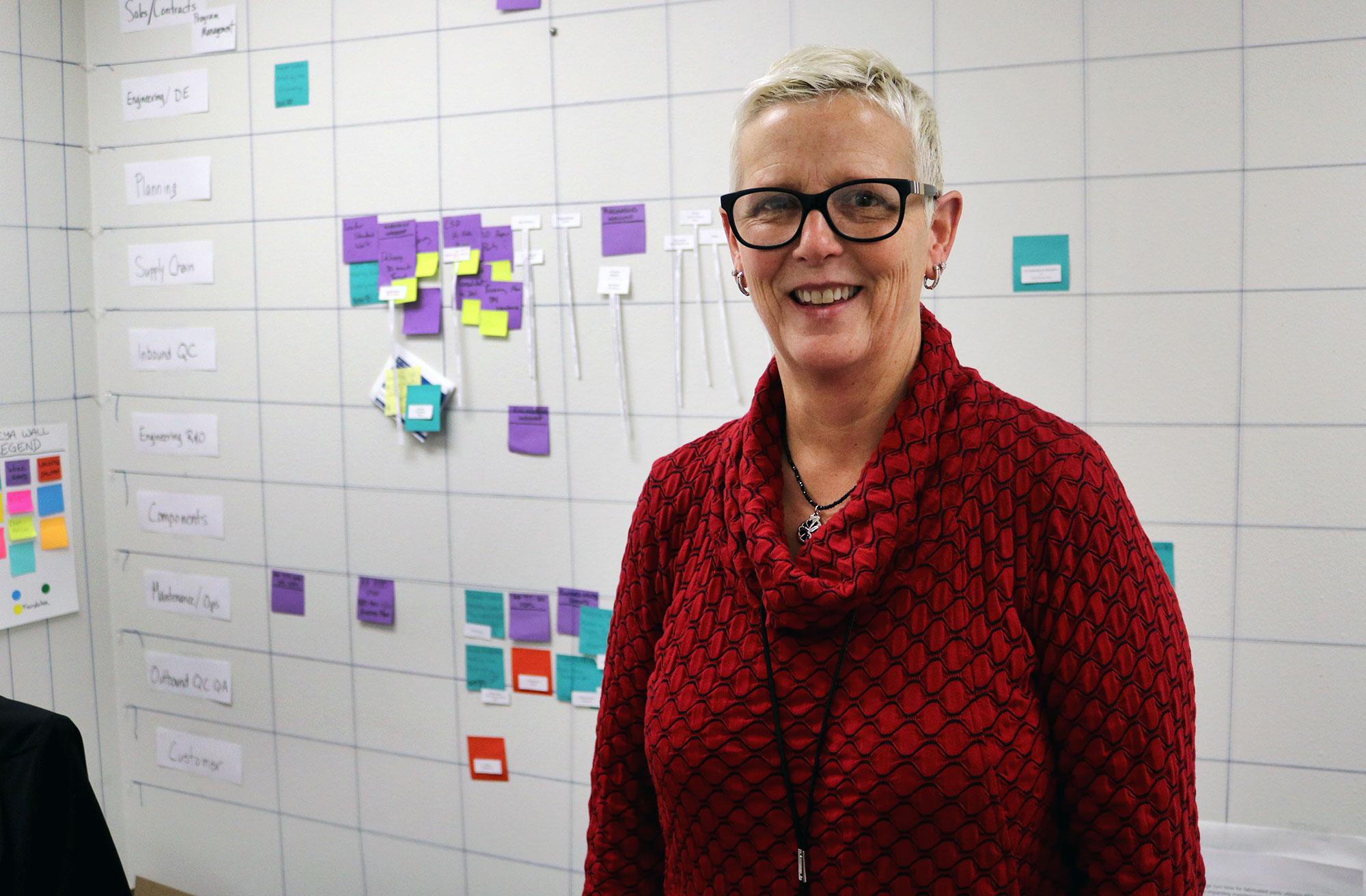
Carla Bowman, director, operations excellence, is ATS’ new operations guru. After 39 years in the aviation industry, Bowman came to ATS from Boeing to help the MRO grow the company and make it a “one-stop-shop.” With office walls covered in documents and charts plotting out ATS’ road map for growth spanning through to 2020, Bowman says she is focusing heavily on removing waste, reducing span times for ATS’ Skyline project and “springboarding into the digital age.”
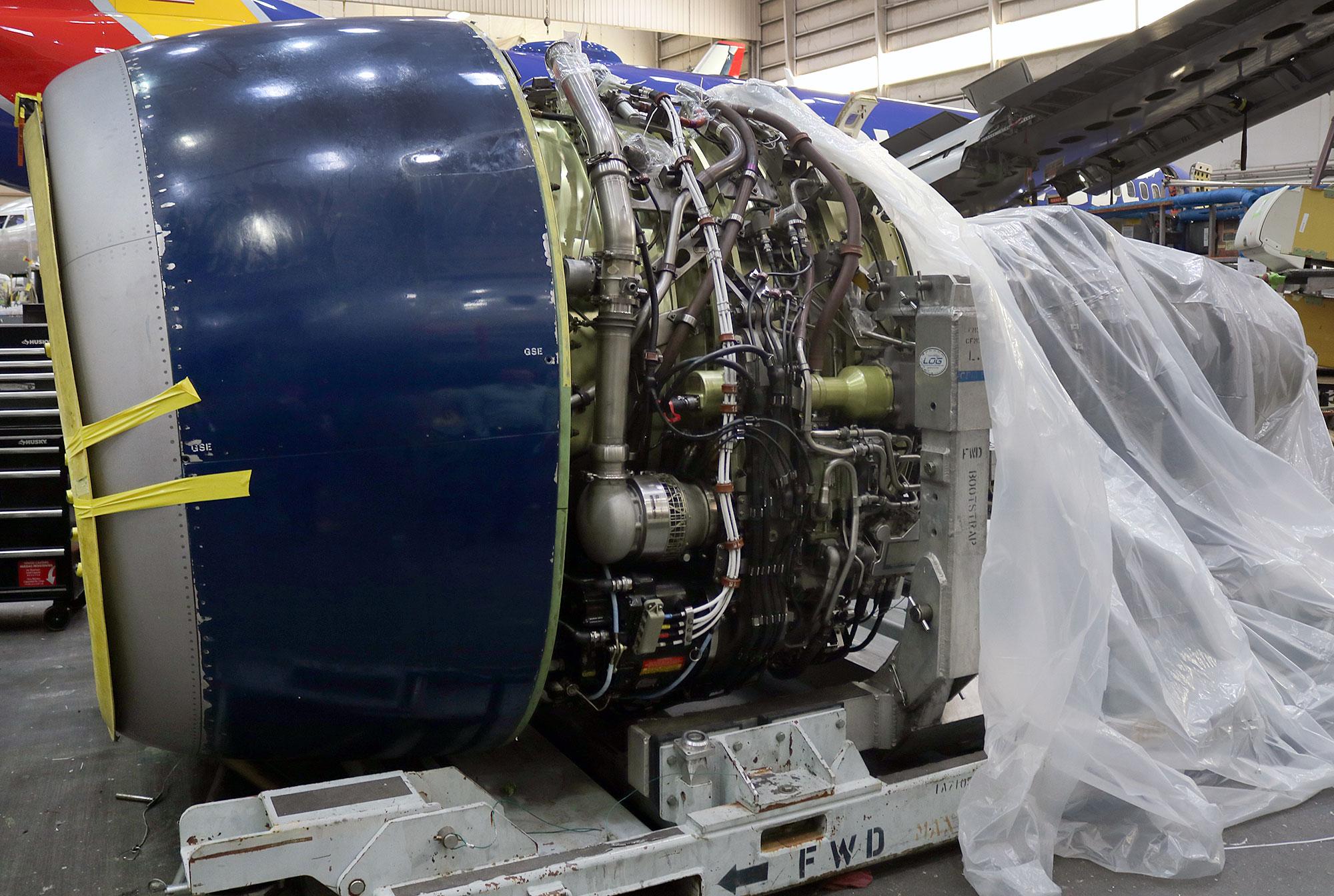
Bowman says reduced span times for the Southwest project will guarantee aircraft are ready early so the carrier can sell those seats, which will add even more financial benefit to the already reduced costs the Skyline program provides. The ultimate goal, says Bowman, is industry leading turnaround times and predictability.
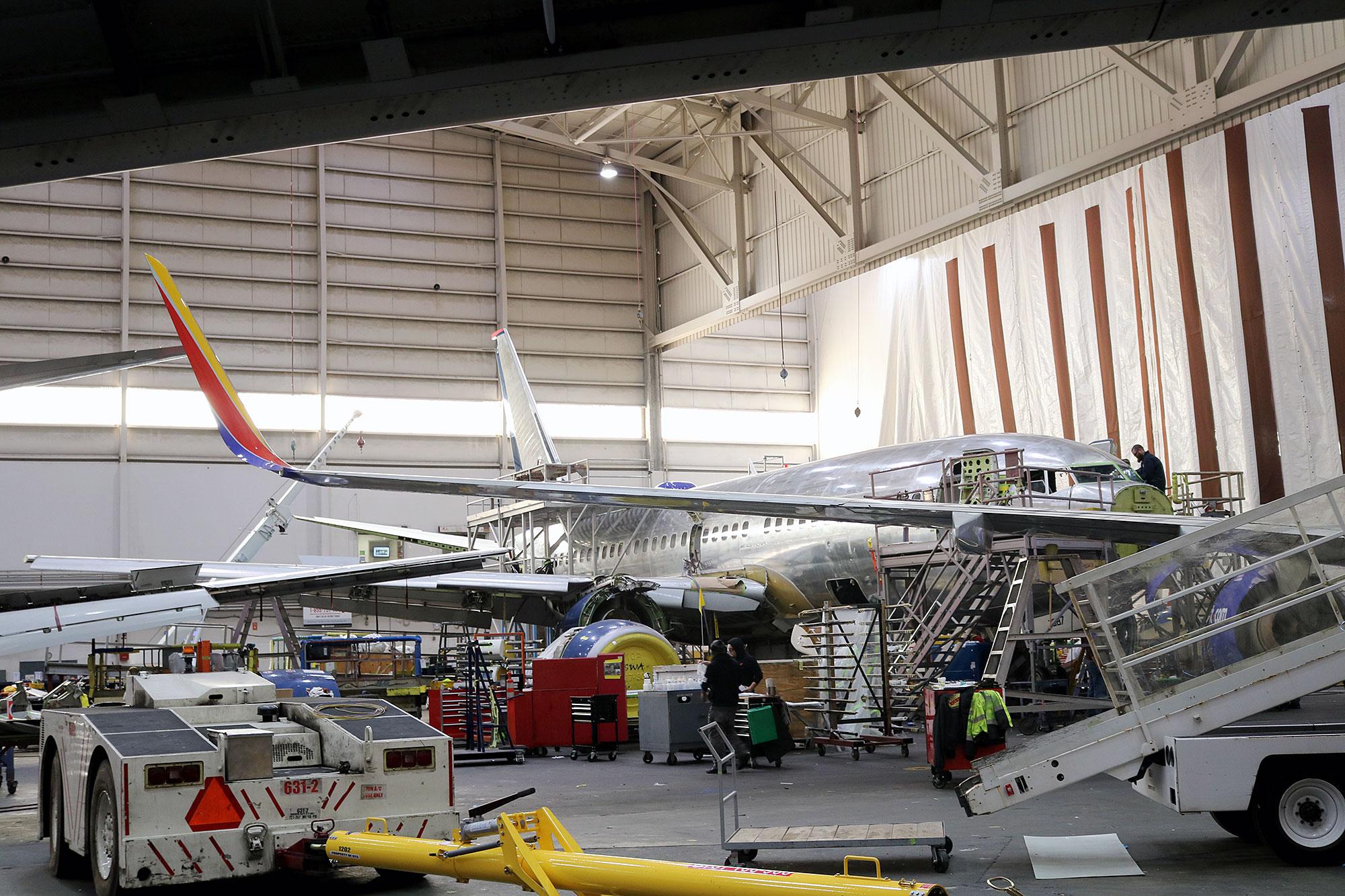
This aircraft is in the process of being transitioned. ATS strips the aircraft, sands it to inspect the fuselage skin, and completes maintenance and modifications to bring it up to fleet specifications.
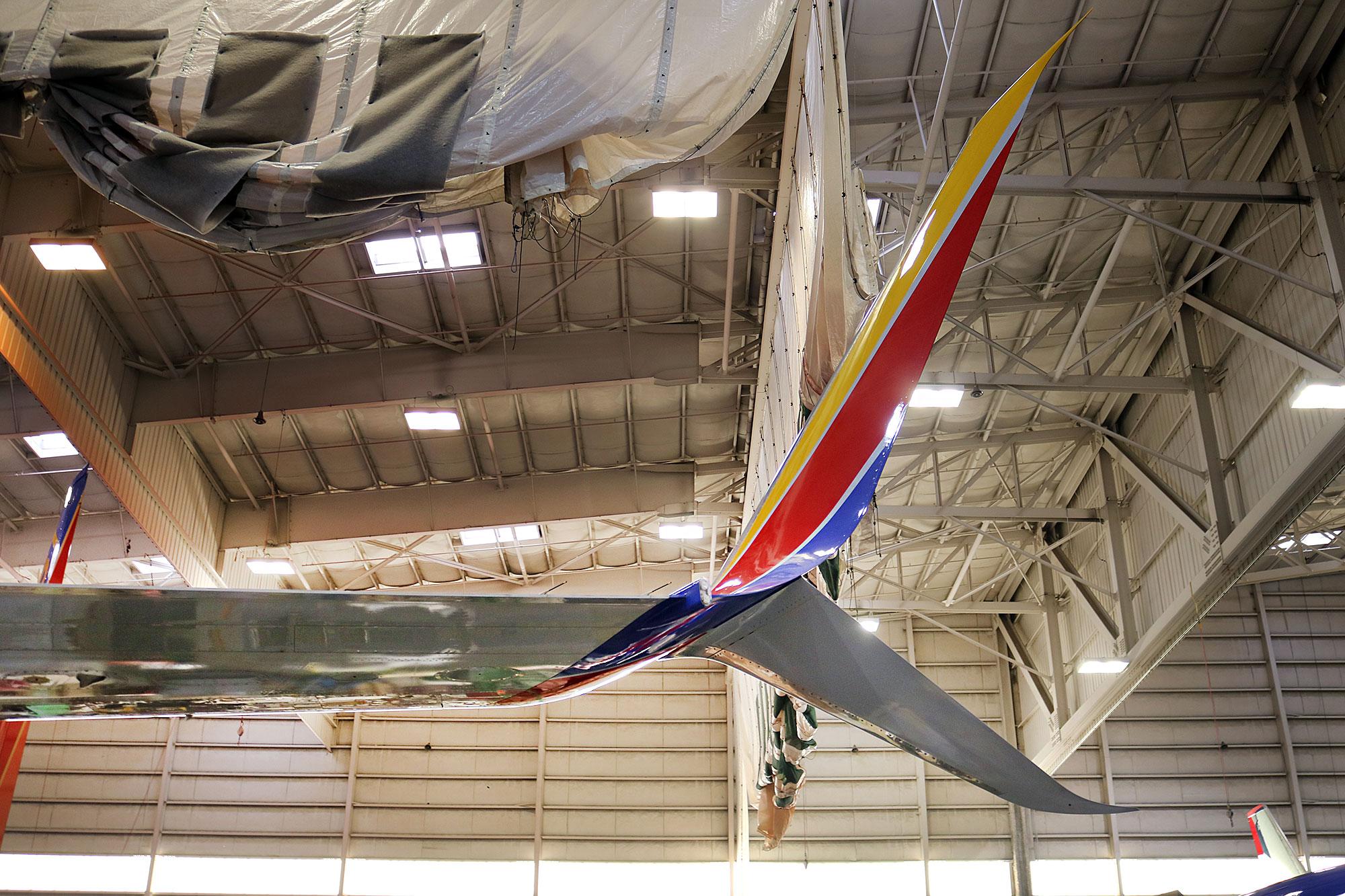
These split scimitars, sold by Aviation-Partners Boeing, are being installed on aircraft right out of the factory. Southwest expects the addition of these split scimitars on winglets to boost annual fuel savings per aircraft by up to 2%.
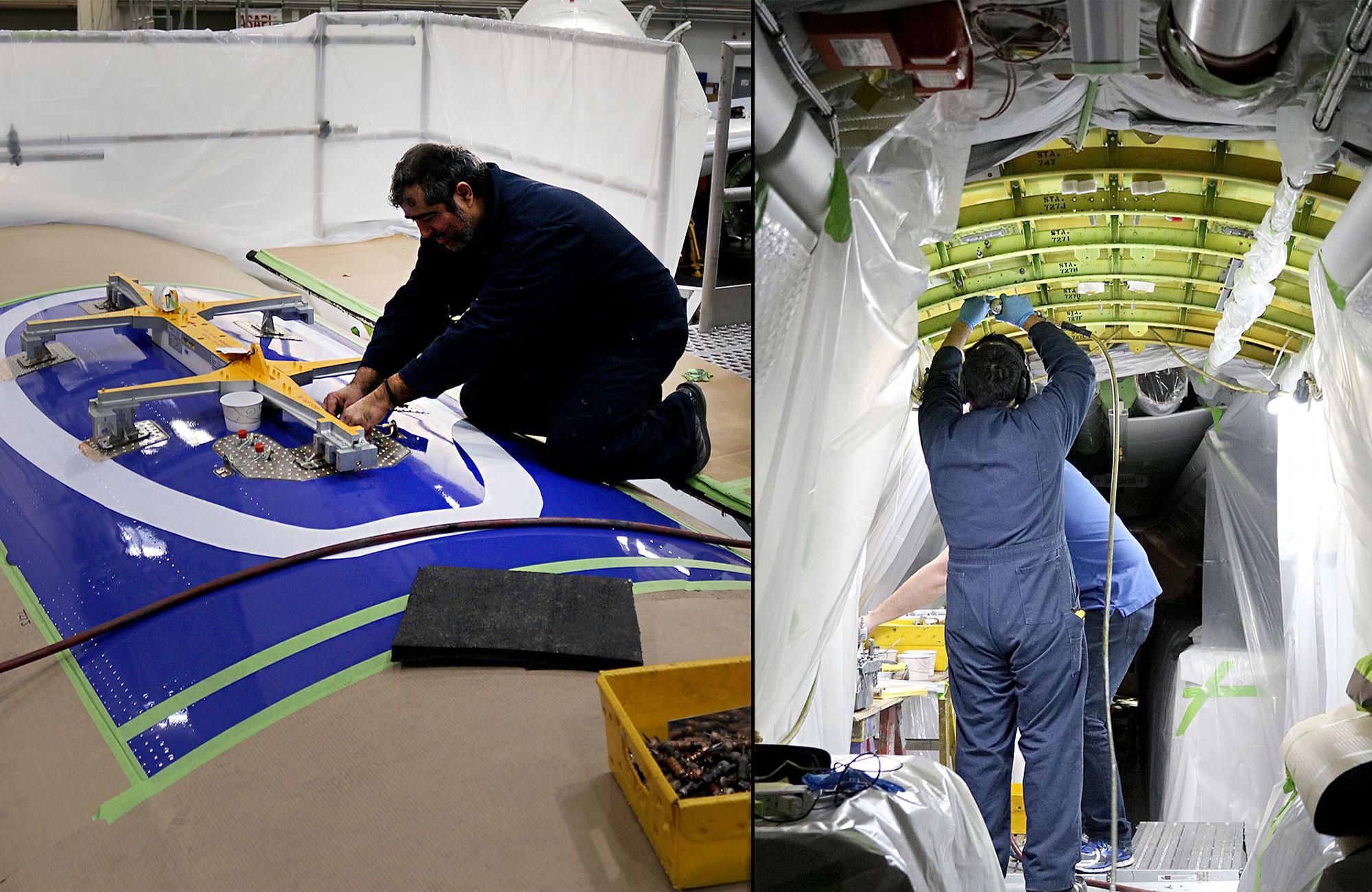
Technicians inside and on top of an aircraft work to install Wi-Fi.
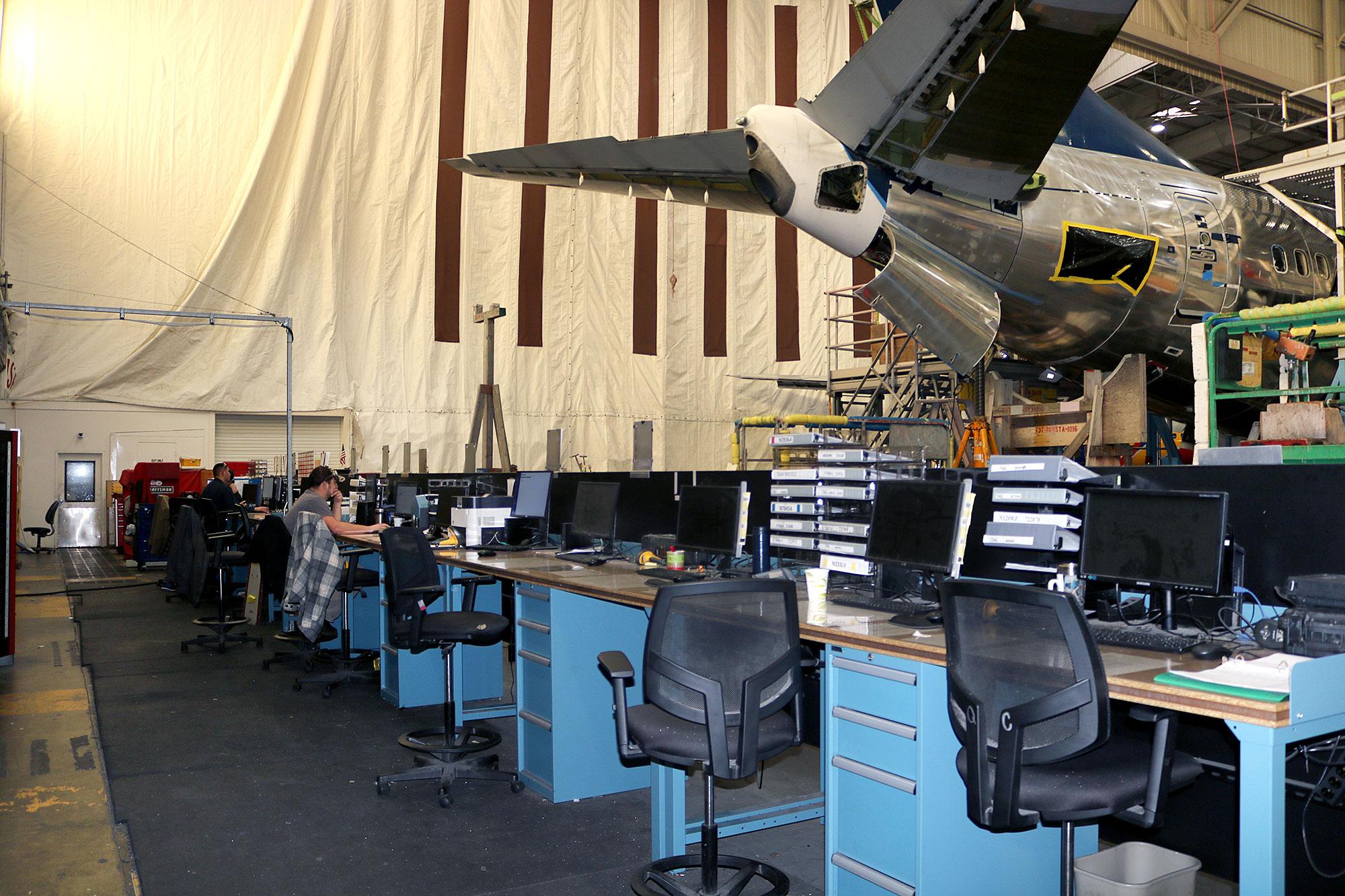
ATS has implemented these long desks to put team leads directly in front of the aircraft they are responsible for. Leads run the aircraft and crews while making sure all work is performed correctly.
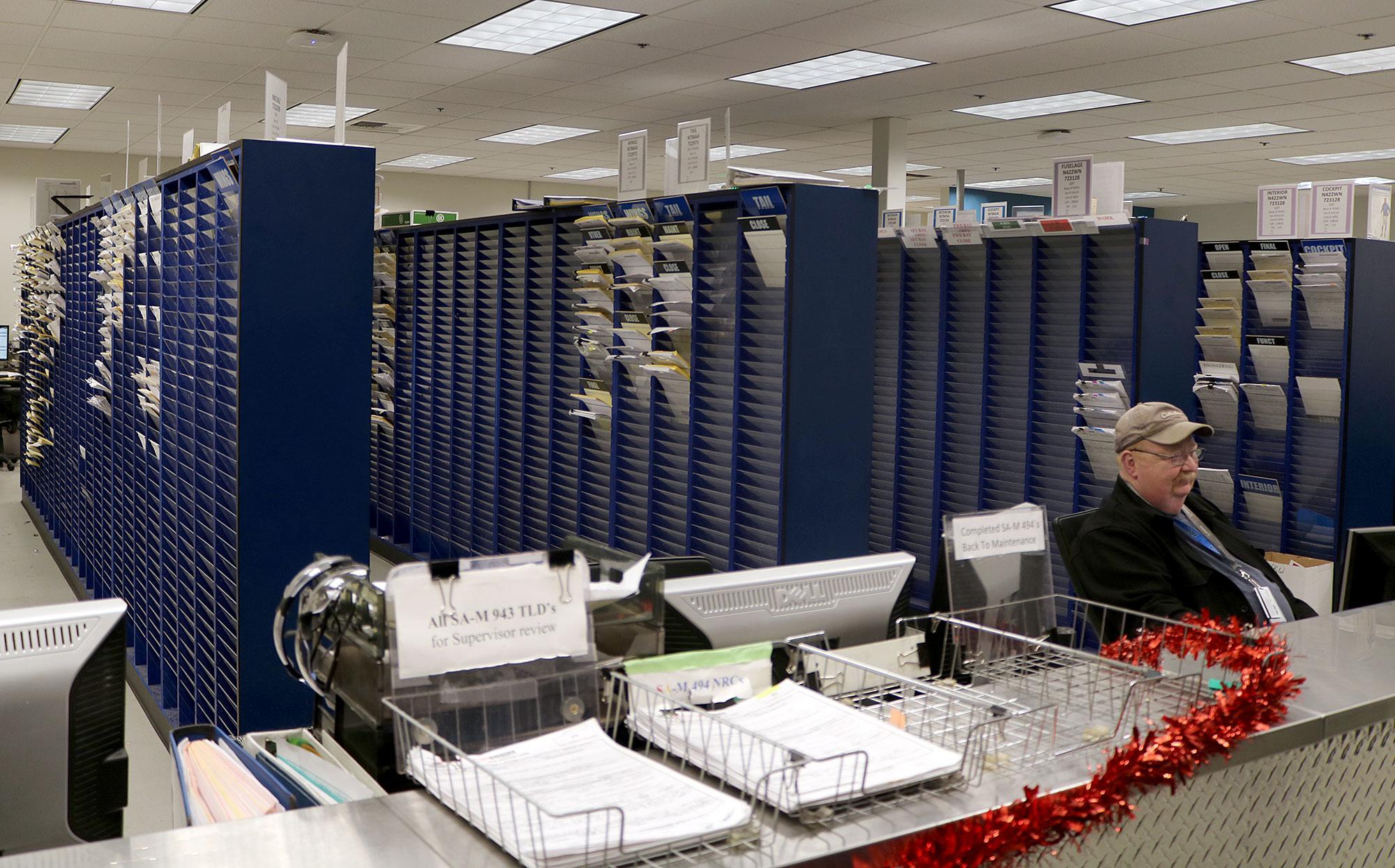
The Maintenance Control room is where supervisors assign and manage work for technicians each day.
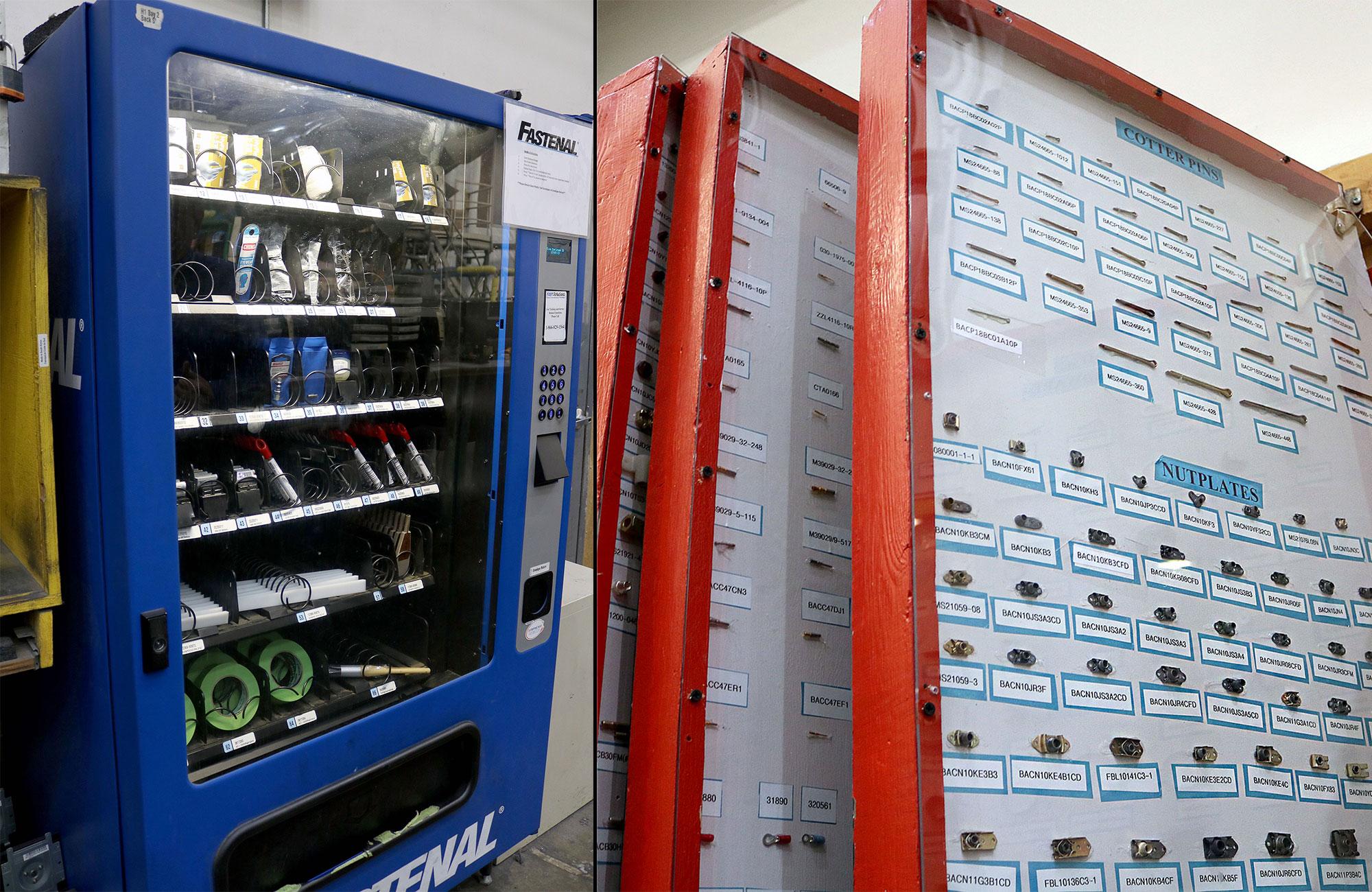
Left: A number of Fastenal vending machines are located throughout the hangar so technicians can easily and conveniently grab small parts.
Right: These standards boards are used as “Cliffs Notes” so technicians can visually identify small parts without needing to search through manuals.
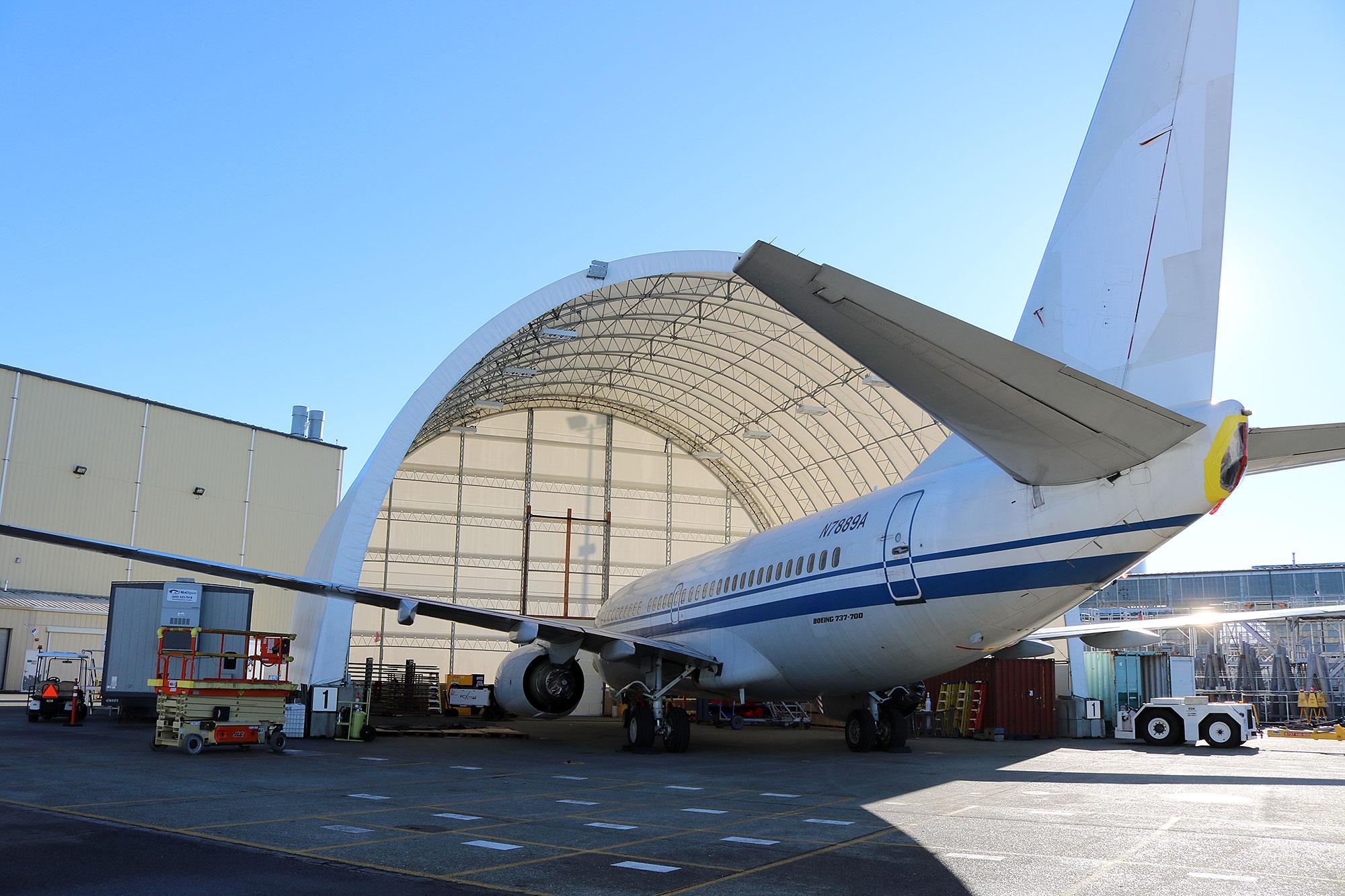
ATS maximizes space by also doing work outside of the hangar. There are six white “nose docks” located just outside the hangar, which widebody aircraft can be nosed into.
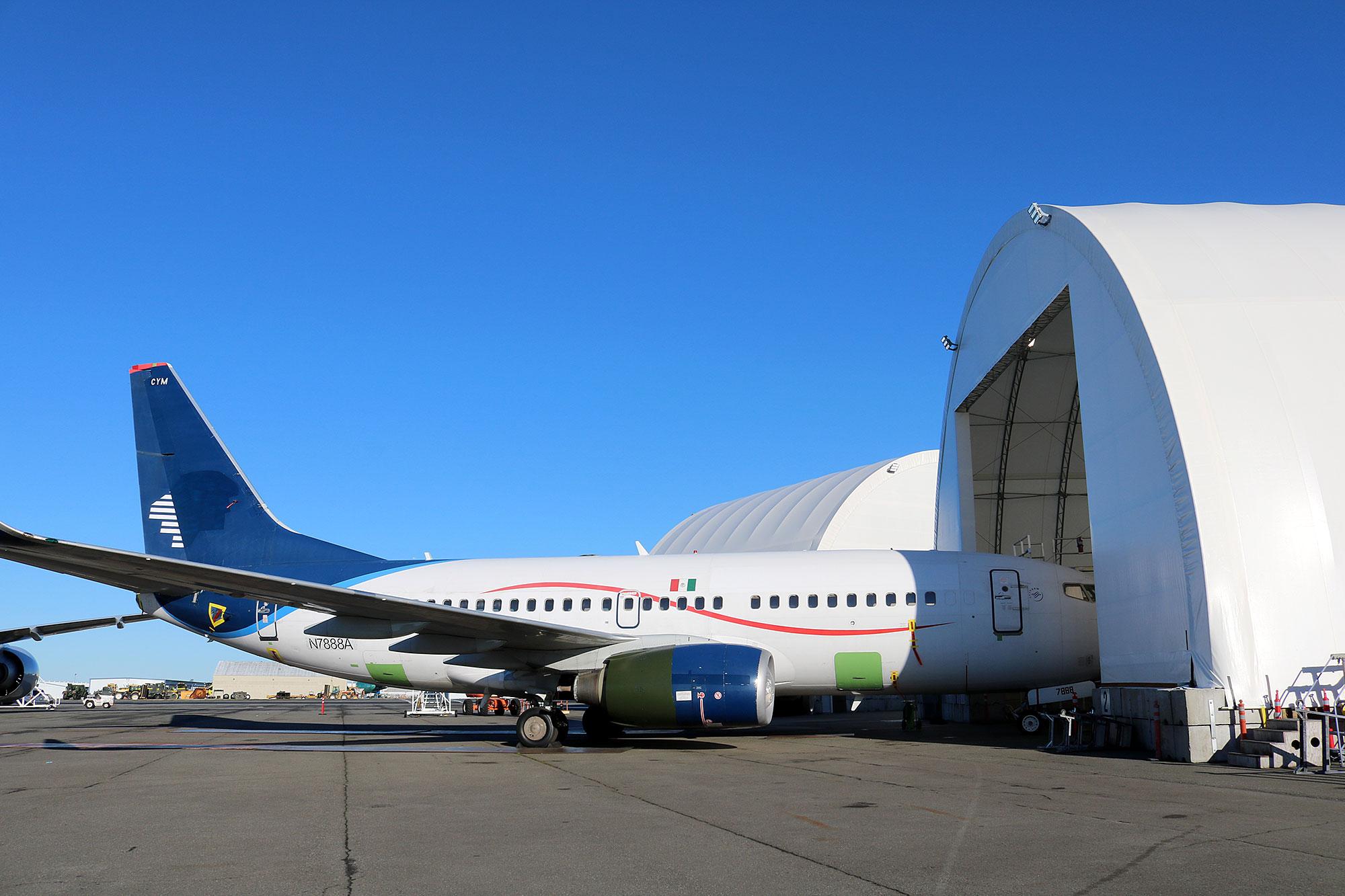
The work performed inside the nose docks focuses on modifications and interior repairs. Heavy maintenance checks are all performed inside the hangar.
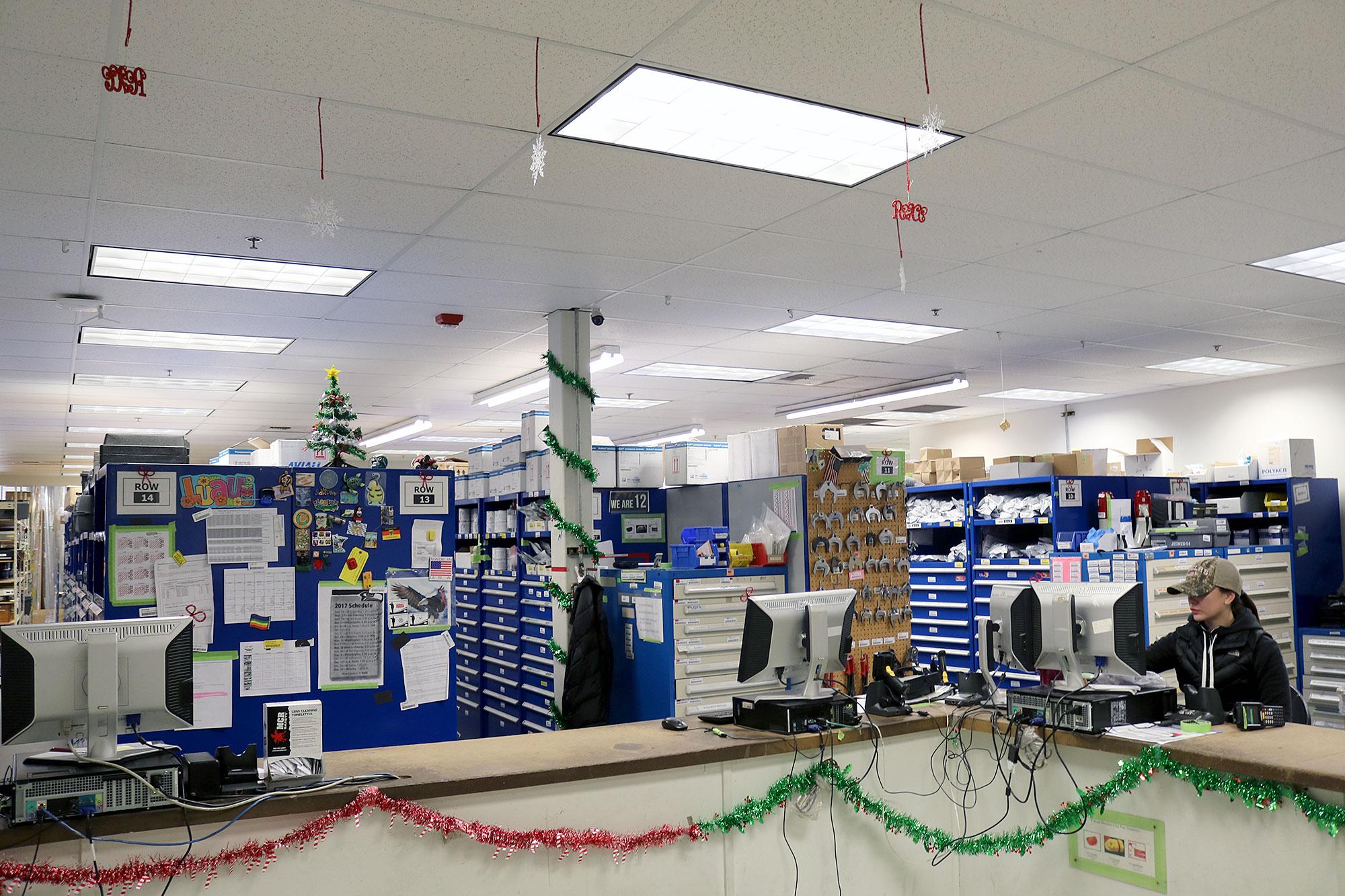
This parts room is where thousands of parts are kept on hand based on what ATS uses on a weekly basis. Workers scan a technician’s badge and the requested part to keep track of what was taken. In addition to this room, there is a larger store room located in Hangar 1.
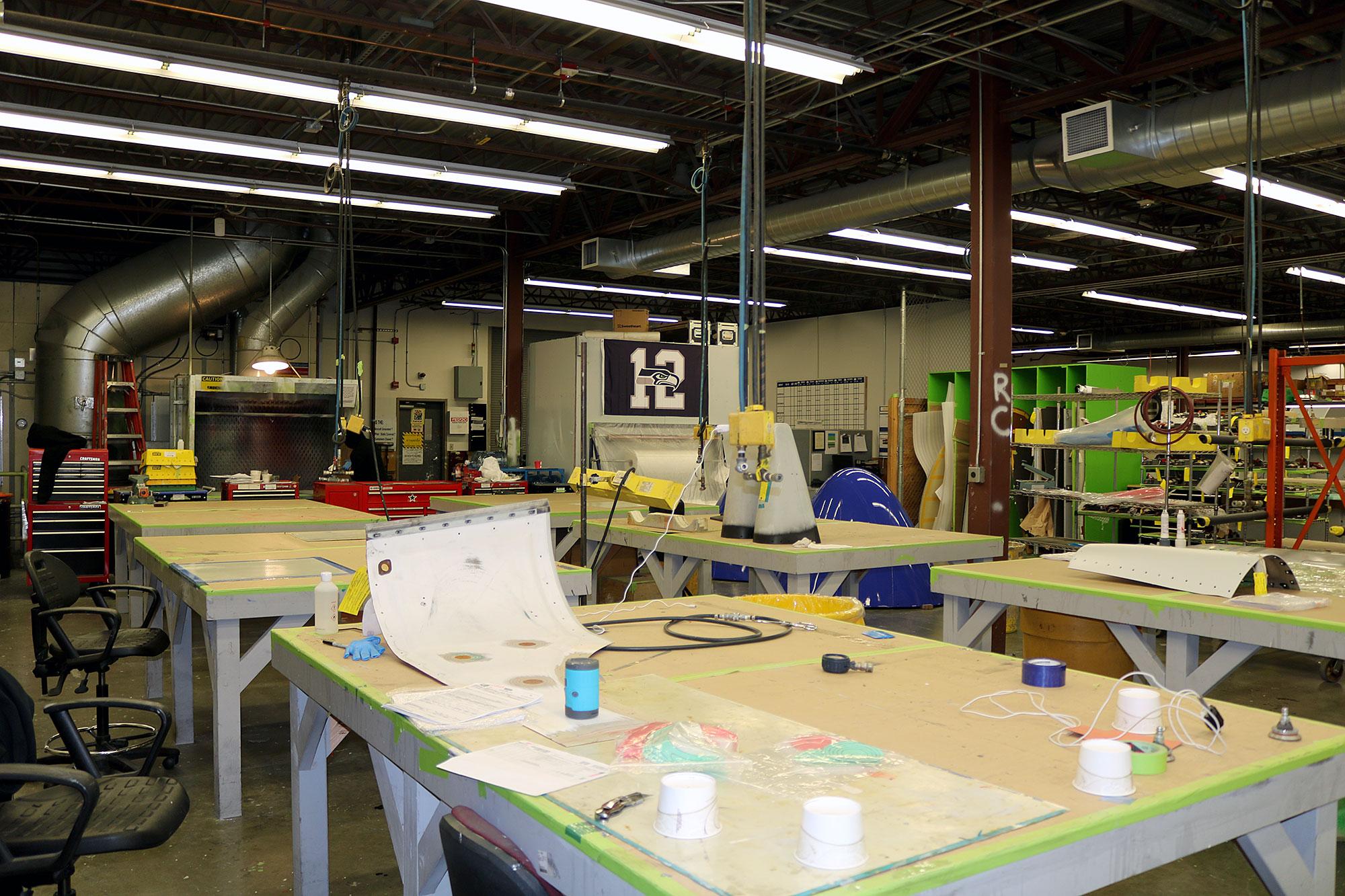
The back shop is where a variety of structure, paint and test work is performed.
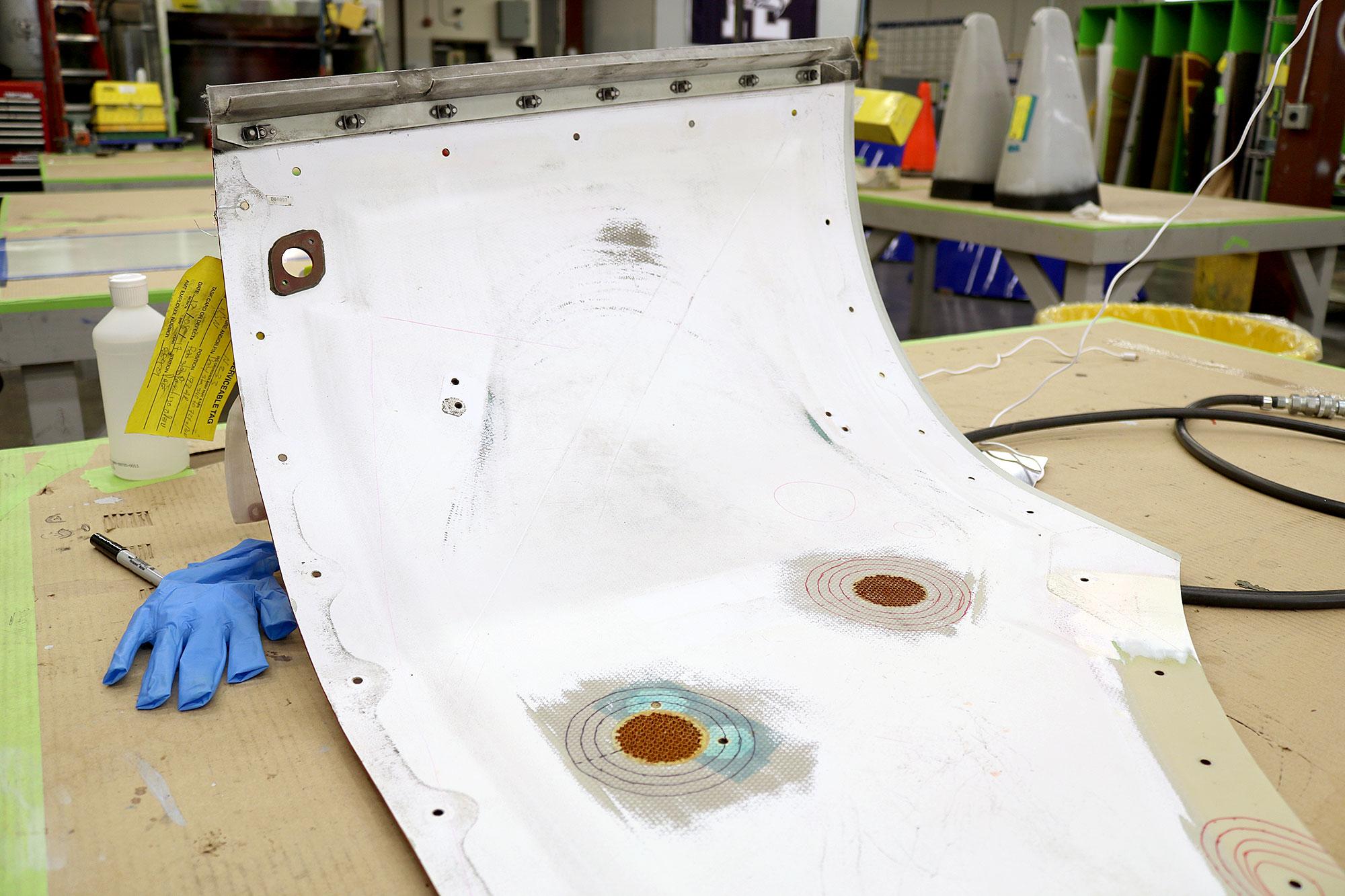
Pictured here is a fairing panel, which is undergoing composite work.
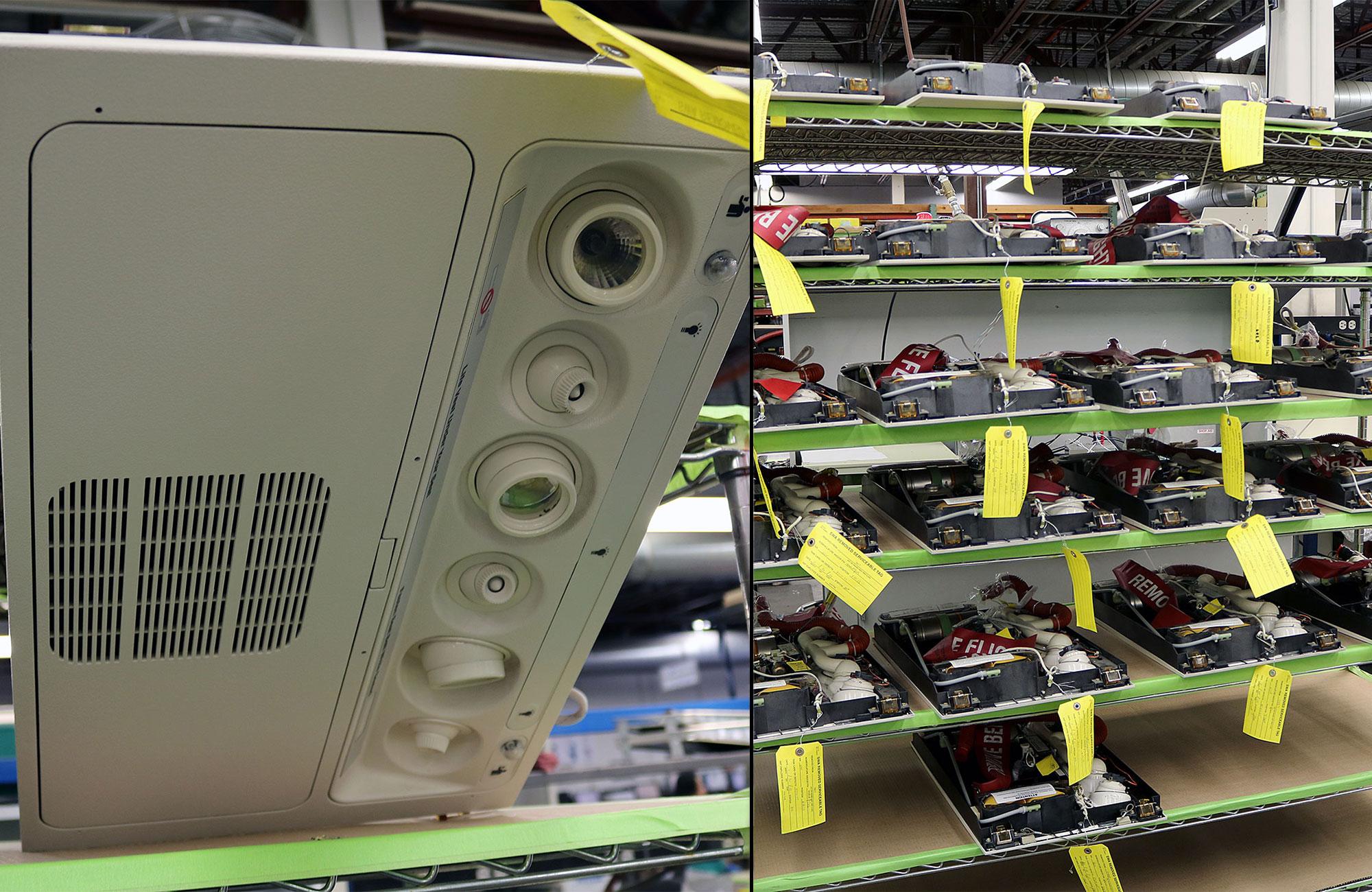
These oxygen systems are being worked on as part of the reconfiguration of a 737-700.
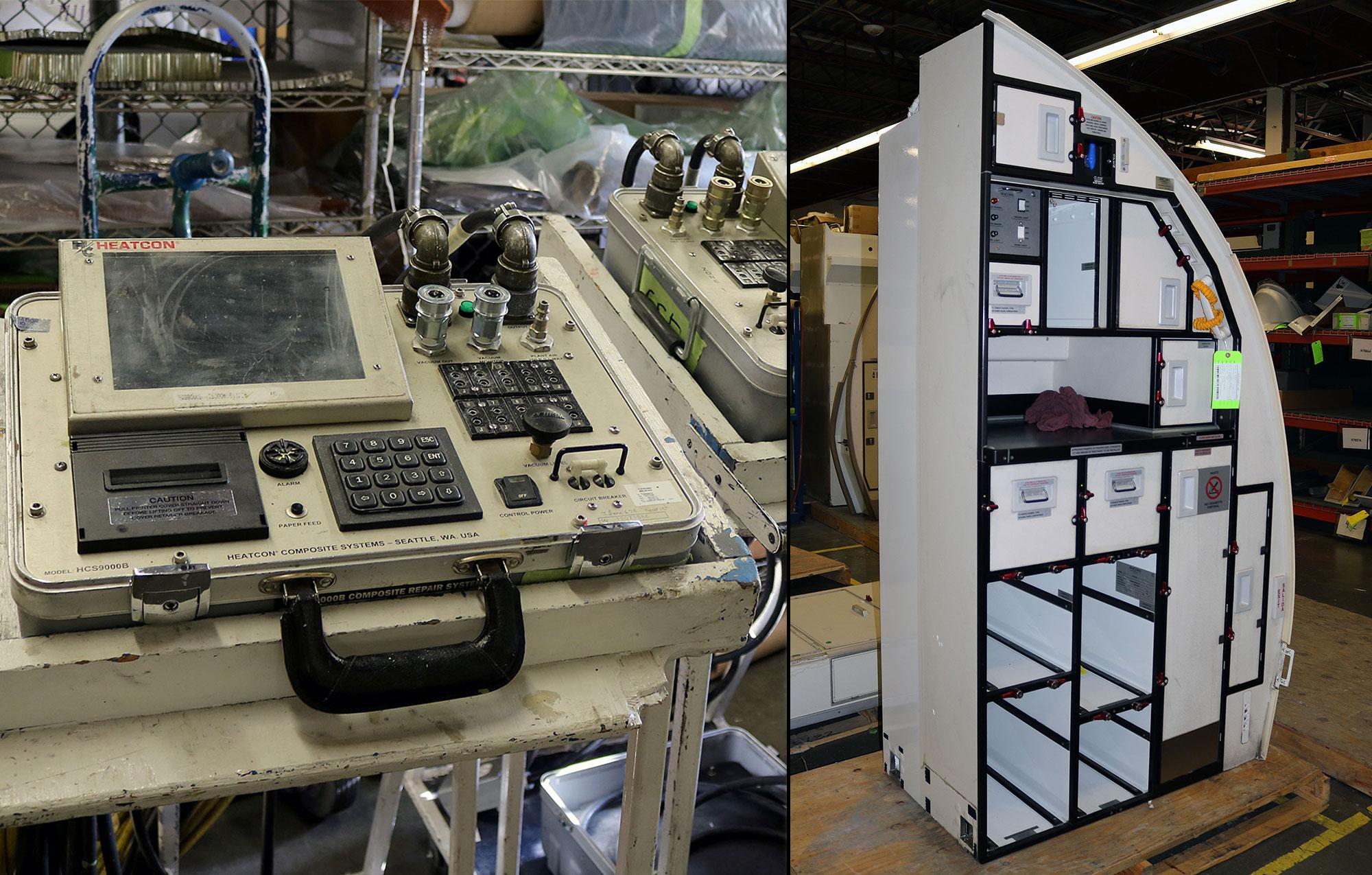
Left: Test equipment.
Right: Interior galley
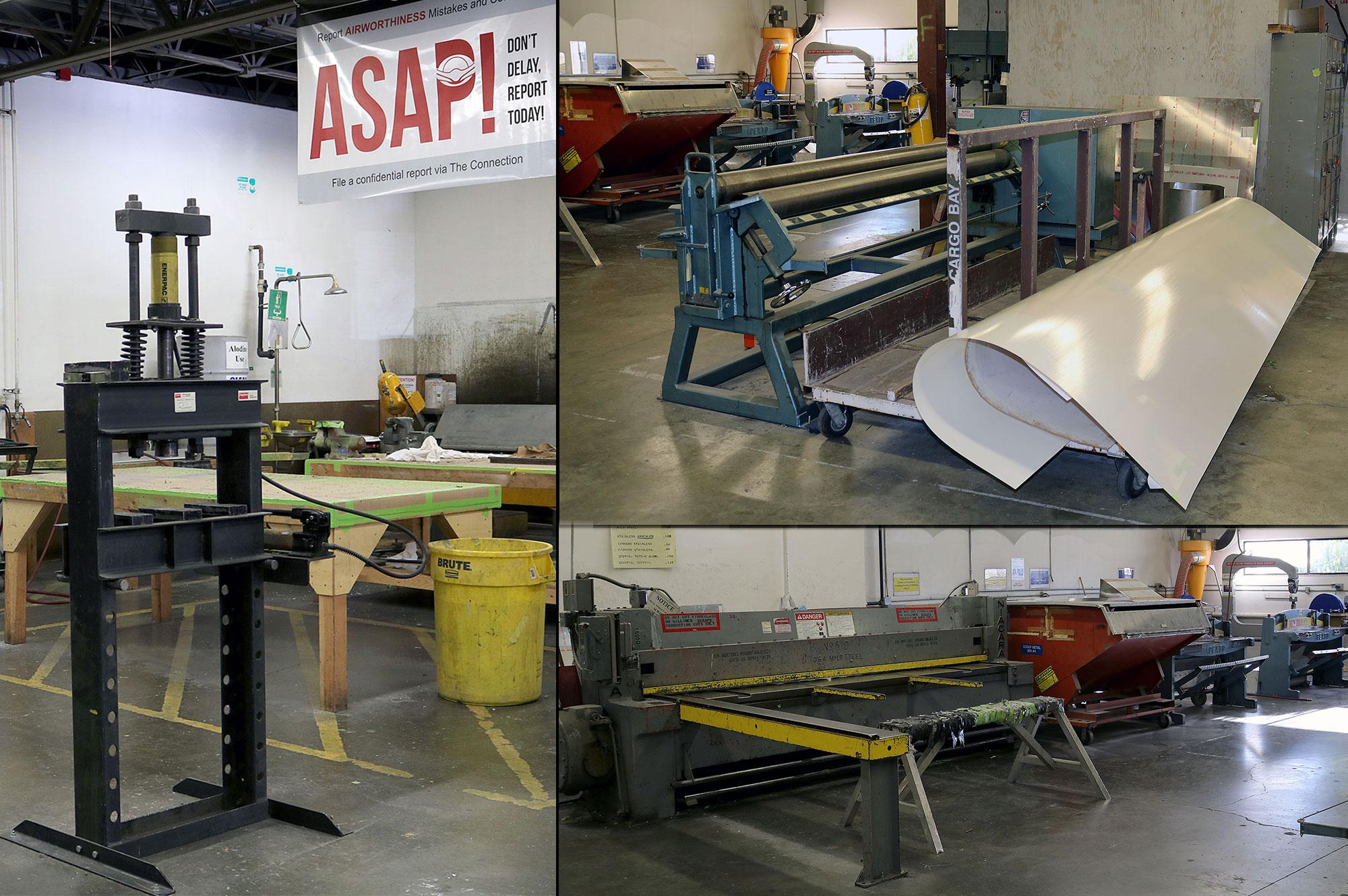
The back shop contains a small machine shop for sheet metal work, which contains rollers, shears, grinders and other machinery.
Aviation Technical Services (ATS) was named Aviation Week’s 2016 Leading Independent MRO for its turnkey fleet integration service. The service, called Skyline, has helped ATS develop a reputation in the industry for its efficient and cost-effective aircraft transitions. Aviation Week had the chance to visit ATS’ flagship location in Everett, WA to see the Skyline program in action and learn more about what the MRO has in store for the future.