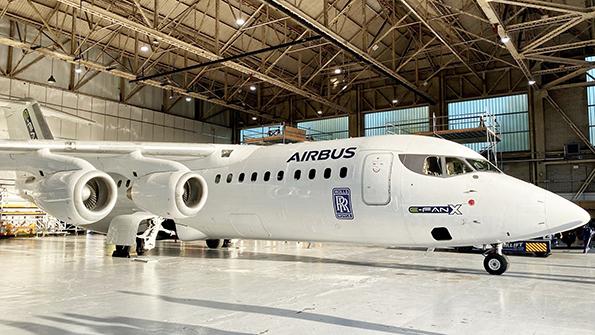
Engine-makers are laying out tentative development strategies for a new generation of advanced lower-emissions powerplants that embrace everything from more-electric and hybrid-electric technology to distributed propulsion architectures, hydrogen fuel cells and carbon neutral-fuels.
But what does this mean to the established multibillion-dollar engine aftermarket industry that has flourished for so long on maintaining, repairing and overhauling the conventional gas turbine? Is the game about to change, and will the traditional service providers be increasingly left out in the cold as the industry moves toward a brave new, sustainable world?
While the shift to new technologies will inevitably be more radical than anything the aftermarket has seen since the start of the jet age, there are currently more questions than answers when it comes to what directions the engine OEMs will take and when. The only certainty is that changes are on the way as airframe and engine-makers work toward reducing CO2 emissions to 50% of 2005 levels by 2050.
A short-term change with almost no known implications for engine MRO will be the broader adoption of sustainable aviation fuels. But beyond this, the picture is murkier. Although development of all-electric propulsion systems is underway, the limited energy density of batteries means the concept will necessarily be limited to applications such as unmanned cargo drones, urban air mobility and other electric vertical- takeoff-and-landing vehicles.
However, this doesn’t mean engine MROs can ignore the electric revolution. Engine-makers are already planning to make turbofans more electric—both to feed future airliner power needs as well as to potentially gain fuel savings by using electric power to optimize engine operation.
Pratt & Whitney is studying a next-generation PW1100G geared turbofan that could be a parallel turboelectric hybrid engine, which could be up to 5% more efficient than current engines and be available for the next generation of single-aisle airliners.
Rolls-Royce, which is building the first demonstrator of its new UltraFan geared turbofan for tests starting in 2021, is already pondering “micro-hybrid” electric versions with embedded starter-generators.
Paving the way for a more electric future, in August the U.S. Energy Department awarded $33 million in contracts to develop all-electric powertrain and fuel-to-electric power-conversion technologies to reduce emissions of future single-aisle airliners.
Covering everything from high-performance energy storage and power generation subsystems for electric aircraft—including fuel-to-electric power conversion—to developing ultra-efficient all-electric powertrains with advanced thermal management systems, the programs make a statement that the U.S. does not intend to fall behind in the more-electric race.
The clear message is that electric power, in various forms and levels of hybridization, is coming, and MRO providers should think about how not only to adapt but also to take advantage of the potential market opportunities. As well as more electric features on future single-aisles, a new generation of all-electric small commuter and hybrid-electric regional aircraft is on the horizon and, because of their promised low operating costs, they could be in service in far greater numbers than today’s generation.
Beyond electric power lies a growing interest in hydrogen. Although discounted as a viable option for aircraft until very recently, hydrogen is now viewed as a way to deeply decarbonize aviation—particularly in Europe. Airbus sees the fuel as one way to meet its stated commitment to bring an aircraft with net-zero carbon emissions to market by 2035.
While earlier efforts to bring hydrogen to aviation have failed because of the high cost of the infrastructure required for production and distribution, the climate-change imperative and the “flight-shaming” movement in Europe have forced a reconsideration.
So what could the adoption of a hydrogen ecosystem mean for the MRO industry? Almost certainly it would present significant new support opportunities, as hydrogen can be used in fuel cells powering electrified propulsion systems or directly combusted in gas turbine engines. Hydrogen, renewable electricity and captured CO2 can also be used to produce carbon-neutral synthetic fuels.
Against this backdrop of dramatic change, there is one great certainty to warm the heart of all engine MRO operators: The gas turbine is not going away—at least not for the next few decades. Alan Newby, director of aerospace technology and future programs at Rolls-Royce, echoes his competitors when he says gas turbines have plenty of runway left ahead. “From our point of view, whether or not it is fueled by sustainable aviation fuel or even ultimately hydrogen in the long-term future, you’re still going to need a highly efficient gas turbine,” he says.