Improved Aviation Coatings Promise Greater Protection, Sustainability
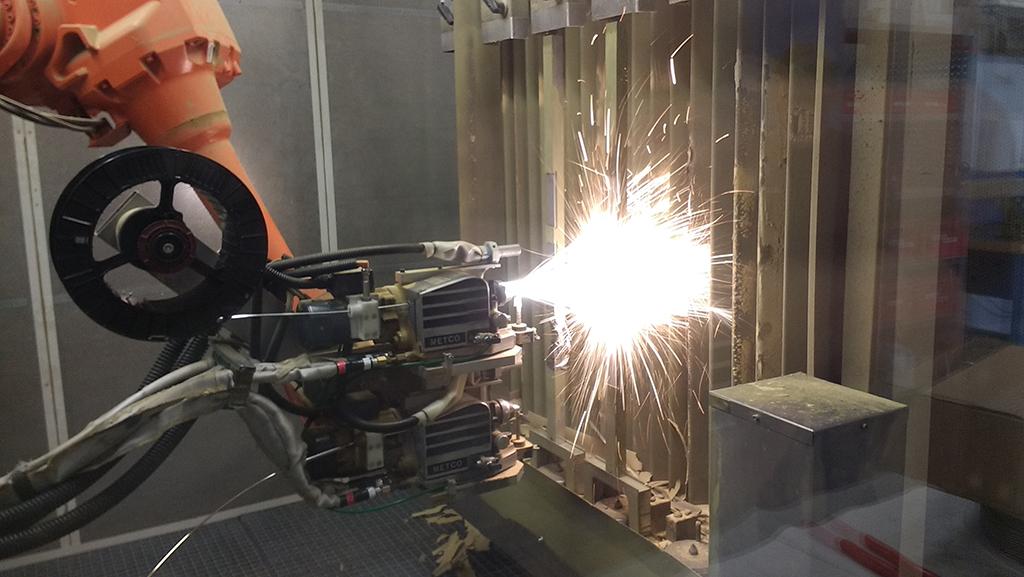
Airbus is replacing hexavalent chromate compounds, which help inhibit erosion in surface treatments.
Credit: Airbus
Coatings and surface treatments are integral to the functionality, reliability and longevity of airframe components. Recent advances in coatings technology are providing greater protection and sustainability alike. Dominic Shore, a specialist in surface technology at Airbus, explains that reducing...
Improved Aviation Coatings Promise Greater Protection, Sustainability is part of our Aviation Week & Space Technology - Inside MRO and AWIN subscriptions.
Subscribe now to read this content, plus receive full coverage of what's next in technology from the experts trusted by the commercial aircraft MRO community.
Already a subscriber to AWST or an AWIN customer? Log in with your existing email and password.