
Andy Best, chief technical officer at Iberia Maintenance, discusses how the airline’s MRO business is looking to adapt over the long term and in which areas it plans to invest.
As an airline-affiliated MRO, the past 18 months must have been difficult for Iberia. What position was its maintenance business in at the end of 2021?
Over the past 18 months, the maintenance division took a hit and saw drop-offs of around 40% at the height of the crisis, but in different areas considering that we cover airframes, engines and components. We saw less of a drop-off in airframe maintenance. This was because we had a super-flexible workforce, and staff were able to move around. As engines dropped off somewhat, we introduced a new parking and storage service for airframes. At Madrid, there are now aircraft from British Airways, Scandinavian Airlines and EasyJet parked there, and staff have had the flexibility to work on these aircraft.
At the height of the COVID-19 crisis, how many aircraft did Iberia Maintenance have in storage?
These aircraft were not just from International Airlines Group (IAG), but there were a total of 78 aircraft at Madrid, where on our own land we don’t incur the cost of leaving them airside. This fact was very attractive to customers. We stored aircraft for IAG, first to look after the aircraft and second to reduce costs. For our non-IAG customers, we provided parking and storage linked to base maintenance and engine services. Aircraft that were due for a C check were brought in and would be parked and looked after by us, before entering the hangar for the check. Likewise, the engine would come off wing and be taken into the shop. So all aircraft parking was provided for free.
How have you been conducting cargo maintenance activities during the pandemic? For Iberia itself, we took several Airbus A330 aircraft and did some form of cargo conversion, albeit not a fully fledged one. This work included taking the seats out of the aircraft and undertaking a modification program to install netting in place of seats before flying various routes. Some of these routes included shipping the COVID-19 vaccine, as well as basic cargo to the Americas and Asia. These aircraft are still in operation, but over the next quarter will be returned to passenger service as long-haul routes start opening up.
How is Iberia dealing with capacity challenges? Are there any concerns about when MRO demand starts to gradually pick up?
I don’t see the industry getting overexcited and throwing large volumes of capacity at MRO operations. The recovery will see green shoots and grow along with it. From an airline perspective, we will take those opportunities as they come along, while from a maintenance point of view we’ll make sure that the cargo aircraft are returned to passenger operations and make sure that the base maintenance activity supports the return for next summer of both short-haul and medium-haul flights. A key market for us is South America, and once that opens a bit more, those routes will also follow. The idea is that by summer 2022, we will need all the aircraft available to fly those routes.
Line maintenance will likely pick up faster than areas such as engines, with airlines burning through green time at present. Airlines need to be conscious of the fact that there is only so much engine shop capacity available. There won’t necessarily be a massive bow wave, but there are a bunch of engines out there that will need shop visits. This brings about two risks: first, the actual availability of the shop visit itself, and second, can the OEMs and vendors ramp up to support those visits? Some of the supply chain vendor support allocated through the OEMs is at risk and has affected some of our engine turnaround times. The longer turnaround times mean reduced shop-visit capability and fewer engines on the market.
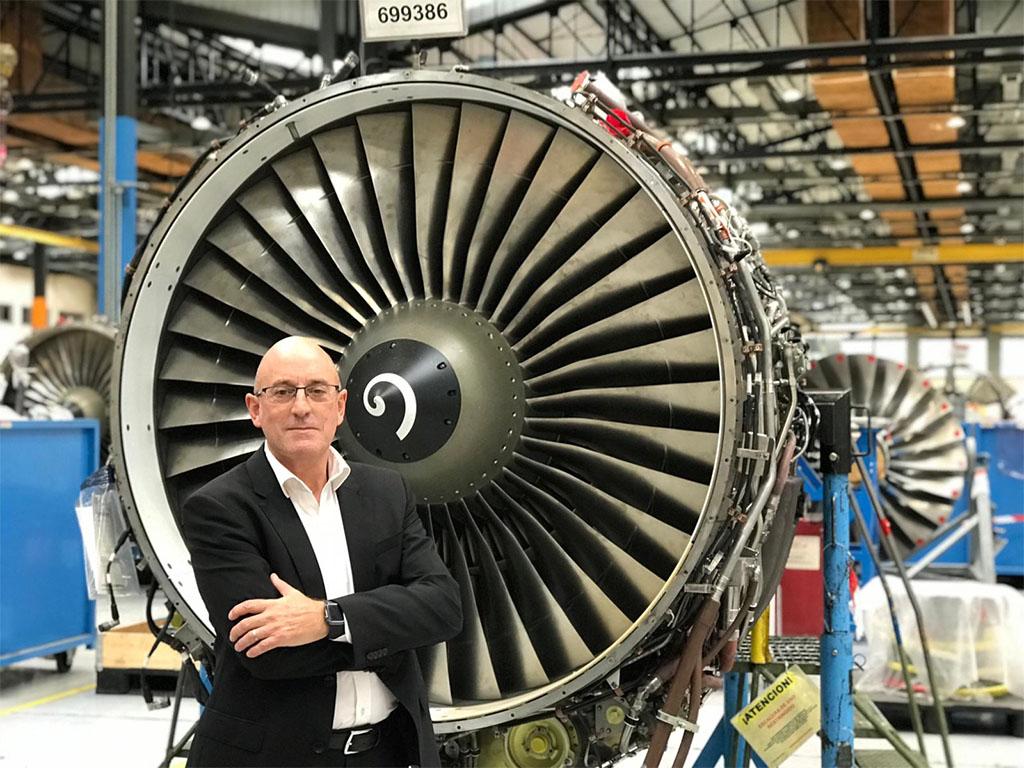
As an MRO provider with engine capabilities, how do you see that segment of the commercial aftermarket recovering in 2022?
We’ve seen a few players in the market who’ve swept up a lot of the used serviceable material, along with some of the life-limited parts and engines. They will then try and leverage that market from a capacity and availability angle. From our perspective, we will still be 20%-25% down on capacity by the end of this year. As we go into 2022, we’ll try and recover that.
The V2500 aftermarket remains strong, but CFM56 engines less so, although they will inevitably come back. There will be issues with the availability of capacity for shop visits. Another factor will be having enough staff—a lot have left the industry because of the crisis. That’s not just mechanics, but engineers and middle management also. We have to retain the people we already have while giving a confident outlook in order to attract workers back to the company.
How is Iberia approaching the next-generation CFM Leap and Pratt & Whitney geared turbofan (GTF) engine programs?
We have Leap and GTF capability. The GTF program investments have been approved by the airline group and those are starting now. The test cell has already been upgraded for GTF purposes but calibration testing still needs to take place. Tooling demands and purchase orders have also been placed. We’ve recently received a high-speed grinder, which cost around €7 million ($7.90 million), and all-new cleaning areas are being put in place for this. The aim is to go live in the fourth quarter of [2022], but that may drift a little bit based on some of the availability of tooling from the OEMs. We have 50 GTF engines in the group and the idea is that these will account for the first inductions.
This will start with smaller checks and the capability will eventually grow to full overhauls. The Leap will follow; we took a very clear view that we didn’t want to do this engine at the same time as the GTF because of capacity considerations. Sign-off for the Leap investments will likely begin over the next six months and we’ll start building this up afterward.
How is the staff situation in the Iberia Maintenance business? Did the crisis hit workforce numbers?
From the very first day, a lot of the hands-on staff were still working, including the health and safety teams working with local authorities to get our COVID-19 processes in place. The processes introduced allowed us to maintain some level of workload, with base and line maintenance activities remaining ongoing. The flexibility of staff will likely be here to stay, with people moving around depending on which division the workload is affecting most. This flexibility is positive because staff would rather work than be on furlough not just from a financial perspective, but also a mental one. We did use the Spanish ERTE furlough scheme to some degree, but as of now, our workforce of 2,700 only has around 100 on the ERTE scheme, and most of them volunteered for it.
Some airline MROs have used the crisis to invest in technology rollouts. In December 2020, Iberia partnered with Ramco for rollout of its enterprise resource planning (ERP) software. What influenced this choice, and how has the program played out?
Over the past five years, we’ve been changing and streamlining product lines, and one of those next steps was to get the ERP to support us going forward, with it being instrumental for the next 15-20 years. After looking at options we selected Ramco as the tool we would use. There are now around 20 of their team working with the Iberia team in Madrid. The Ramco system will interface with AMOS for line maintenance, while some of our financial software tools will link into it. That’s a significant investment but also a sign from IAG and Iberia that they are investing in the right things for the MRO and are backing its future.
The ERP system will go live in mid-2022 after a trial process, which is presently ongoing. This will make a big difference because in areas such as base maintenance and the engine shop, everything will be paperless and done either via mobile device or tablet. The speed of documentation capture and being able to more easily provide the necessary data to airlines and customers for things such as lease hand-backs will also be important. It’s also a big leap forward for our sustainability initiatives, which have included us recently fitting solar panels onto the top of our Madrid engine shop, which will attempt to provide enough power to support all of our MRO requirements. Over the next year, we plan to feed some of this power back into the grid as well.
IBERIA FACT FILE
History: The airline was founded in 1927 in Madrid. Since 2010, it has been part of International Airlines Group (IAG), formed out of its merger with British Airways. The group also includes Spanish low-cost carrier Vueling and Ireland’s Aer Lingus.
Fleet: Iberia operates an all-Airbus fleet of more than 60 aircraft. These include several variants of the A320 family, including newer A320neo and A321XLR aircraft. Its widebodies include A330 variants and A350 aircraft; the airline received its first A350 in 2018.
MRO: Around 35% of Iberia Maintenance’s work is generated from IAG airlines, with the remaining 65% coming from outside of the group. Its main hangars are located in Madrid and Barcelona, where it carries out base maintenance. Its engine division, Iberia Maintenance, undertakes full overhauls on the V2500, CFM56 and to a lesser extent Rolls-Royce’s RB-211 in Madrid, where it operates a test cell with 90,000 lb. of thrust. Iberia’s line maintenance consists of stations in Spain and South America. The current strategy is for this sort of work to be undertaken directly by the airline rather than by the specialist MRO unit. In Barcelona, IAG carrier Vueling has in-sourced line maintenance, with Iberia performing base maintenance at that location.