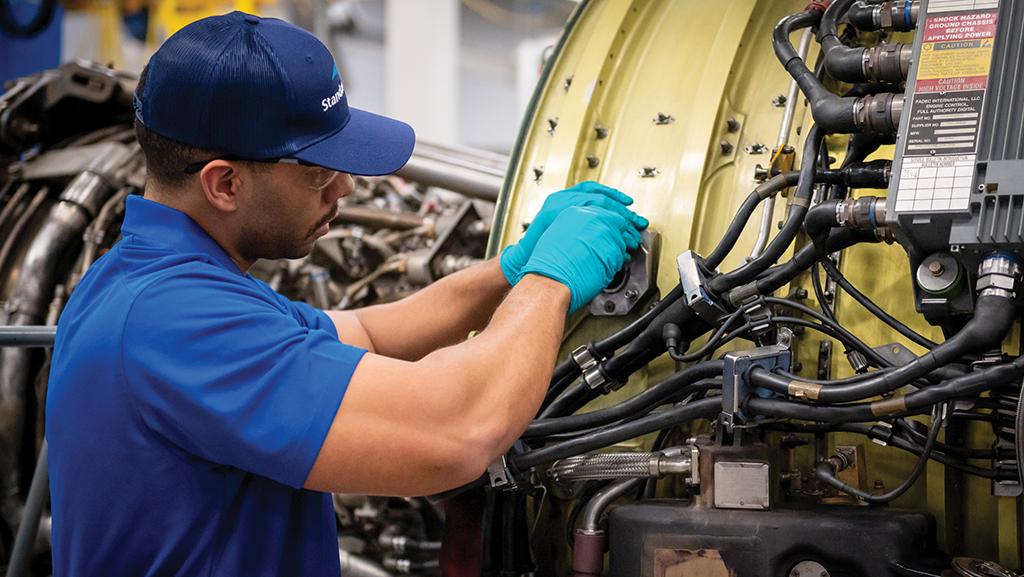
StandardAero added CFM56-7B MRO capacity at Dallas-Fort Worth International Airport and Leap 1A and 1B capacity in San Antonio.
Credit: StandardAero
The health of the aerospace engine maintenance market comes down to perspective: OEMs and independent MRO providers are enjoying a glut of business as older engines run longer, but airlines are suffering from extended turnaround times as maintenance capacity and material supply struggle to keep pace...
Engine Market Strains To Boost Capacity Amid Long Turnaround Times is part of our Aviation Week & Space Technology - Inside MRO and AWIN subscriptions.
Subscribe now to read this content, plus receive full coverage of what's next in technology from the experts trusted by the commercial aircraft MRO community.
Already a subscriber to AWST or an AWIN customer? Log in with your existing email and password.