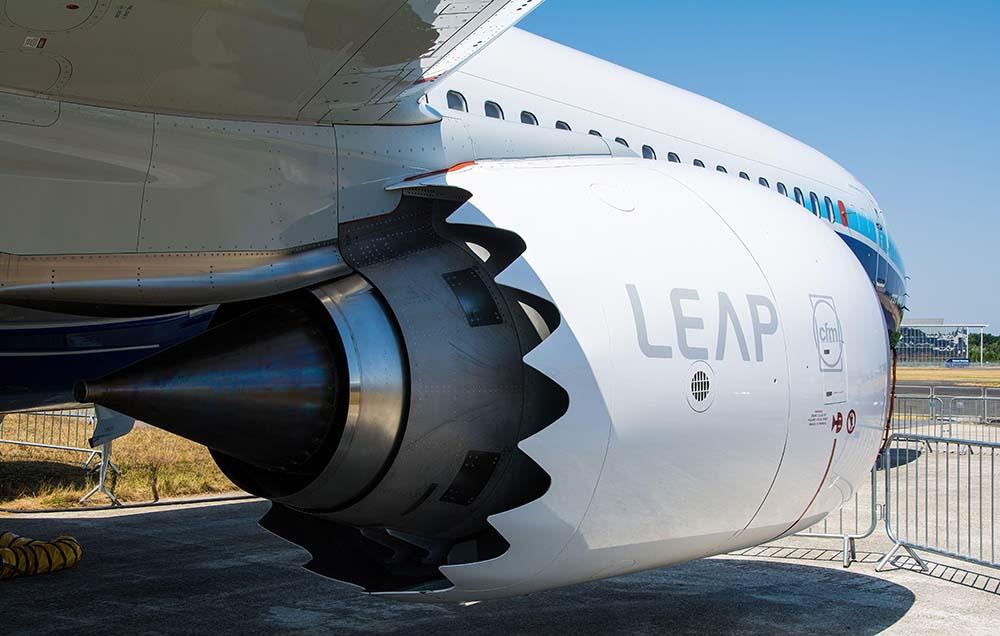
Dag Johnsen, Aero Norway’s recently appointed chief operating officer, spoke exclusively with Aviation Week about industry turnaround times for material repairs on CFM56 engines, spare part pricing trends and the integration plan for CFM International Leap 1A and 1B engines.
Appointed as COO in February, Johnsen’s new role comes at a challenging time for the aviation aftermarket, with long turnaround times (TAT) for material repairs and suppliers continuously striving toward improvements.
“Aero Norway is facing the same material shortages as the rest of the industry, but we are starting to see improvements across various suppliers,” says Johnsen. He feels the key to achieving the desired TAT is early identification of parts and material with long lead-times, and to place these orders and parts into the repair cycle as soon as practical. “Late discoveries and unforeseen part requirements have a negative impact on the overall TAT. In some cases, we make sure we keep key components in stock, anticipating future needs. We are doing quite well overall on the TAT, but we can always do better.”
Johnsen thinks the critical issue for MROs is reoccurring inventory and parts supply chain issues. “I think most MROs are facing the same challenges, but for us it is to identify the critical parts that are needed early on in the repair process.”
Johnsen acknowledges that subcontractors are also struggling with their own turn times. For example, with component repairs, the piece part repair providers need to get the critical parts into the repair cycle to get the component back in time for the engine build.
“We work very closely with all our customers to look at alternate parts or parts substitutes if we can't get the part back in time,” says Johnsen. “Having all the parts when you get into the build process is important to make the TAT work. That is a big focus and I think we're doing okay.”
Johnsen believes coordination with OEMs is also crucial—in this case, with CFM. “We advise them of any impending parts shortages with serial numbers, and the customers that will be affected by delayed turn times. They [CFM] have been very good at working with us when we identify engine serial numbers, customers, target dates or partial delivery for parts in critical needs.”
In terms of spare part price differences between CFM56-3, -5 and -7 variants, Johnsen observes that part supplies for the CFM56-3C engine are becoming more challenging, so Aero Norway relies heavily on spare parts from disassembled engines. “New part pricing for the CFM56-5B and -7B has remained unchanged other than the normal annual price escalation. However, at Aero Norway we do see increases in the used serviceable material market, especially with life-limited parts,” he says.
Going forward, Aero Norway’s plan is to integrate Leap 1A and 1B engines. Johnsen says the company has now obtained the first set of 1A and 1B licenses to start inspecting these engine models. “Our next step is to talk to customers to fully understand their diverse needs and start gearing up for the next level of repairs,” he says, noting that initial activities will start with basic inspection work. “We are looking at the basic tooling to accomplish some of these inspections, such as pedestals, lift beams and things like that. We don't need to go all out until we understand the customer need.”