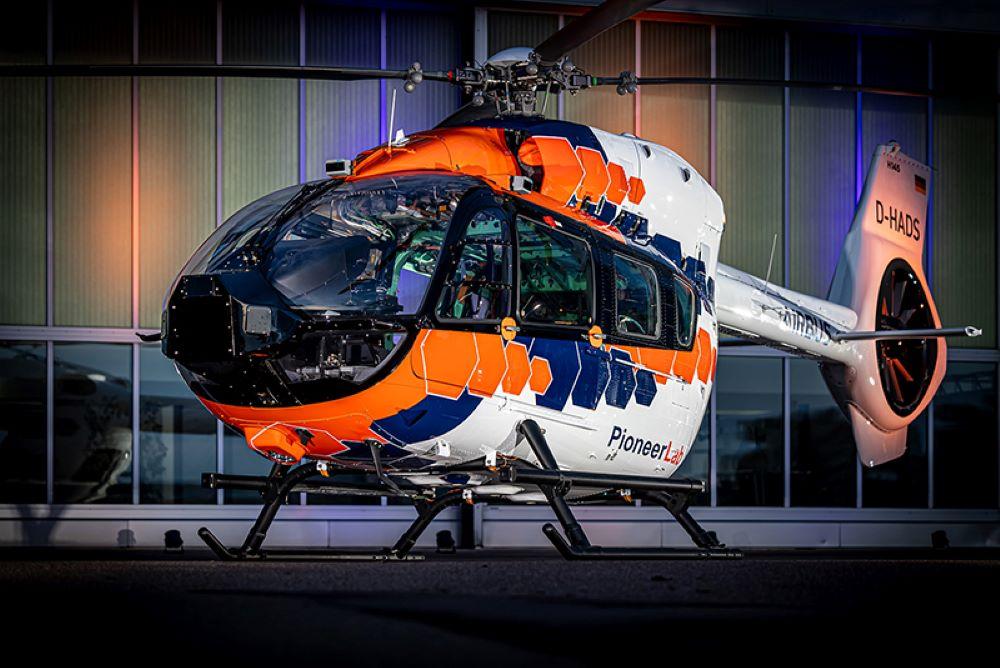
Credit: Airbus Helicopters
DONAUWORTH, Germany–Airbus Helicopters is planning to begin flight tests of a hybrid-electric propulsion system on its PioneerLab H145 helicopter demonstrator in 2027. The project will replace the aircraft’s existing pair of 667-shp Safran Arriel 2E turboshafts with a single 1,000 shp Pratt &...
Subscription Required
Airbus Helicopters To Flight Test Hybrid-Electric Propulsion System is published in Aerospace Daily & Defense Report, an Aviation Week Intelligence Network (AWIN) Market Briefing and is included with your AWIN membership.
Already a member of AWIN or subscribe to Aerospace Daily & Defense Report through your company? Login with your existing email and password.
Not a member? Learn how you can access the market intelligence and data you need to stay abreast of what's happening in the aerospace and defense community.