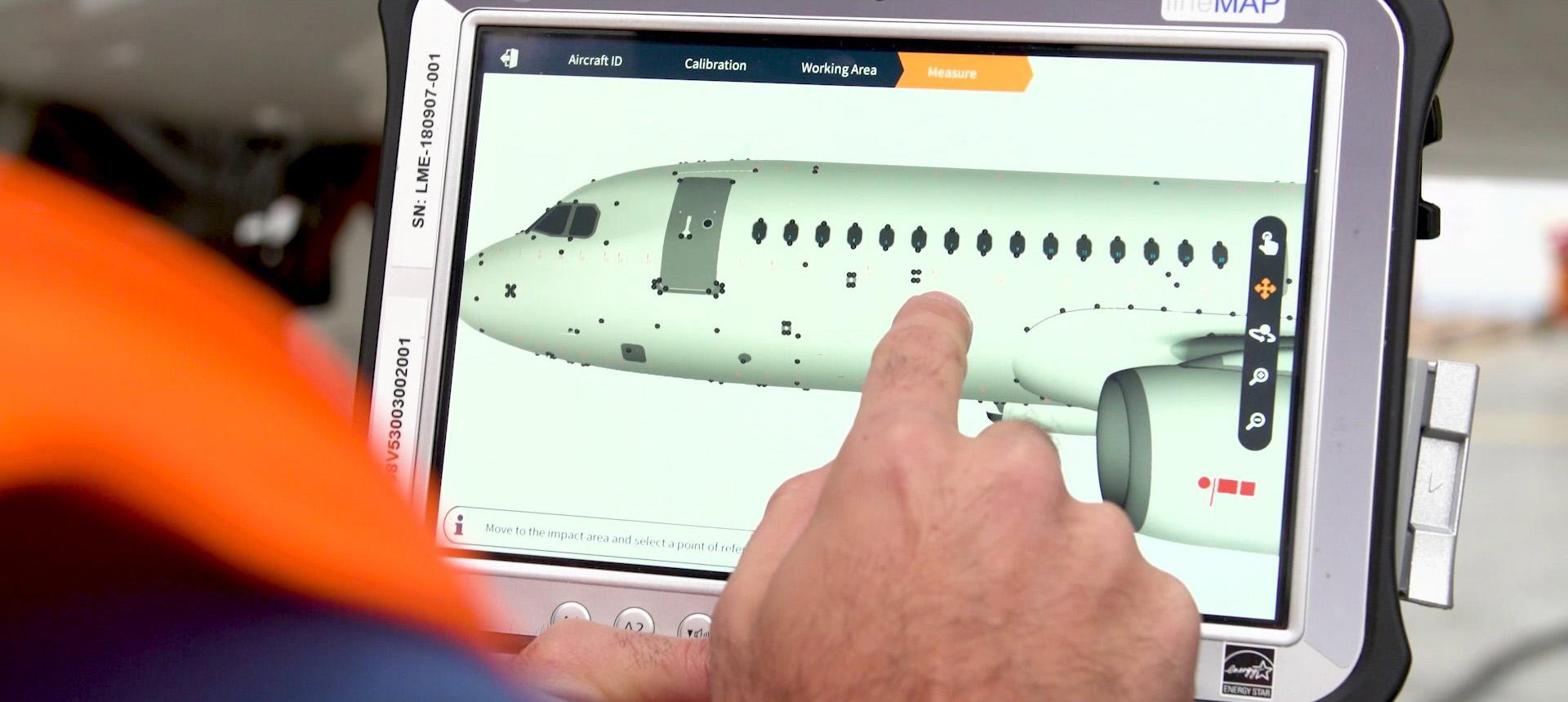
LYON, France—Airbus has begun using an “e-Delivery” remote process for aircraft handovers as a way to ensure health and safety amidst the COVID-19 pandemic.
The method could become a permanent cost-saving option for the customer.
With e-Delivery, Airbus aims at ensuring social distancing standards are met. Pegasus Airlines was one of the first customers to adopt the end-to-end remote process. From April 9, it received three new A320neo family aircraft from the Hamburg final assembly line (FAL).
Since mid-March, half of an unspecified number of deliveries took place utilizing the same procedure. At least one carrier has followed Pegasus this month, according to Alain Villanove, Airbus VP for contracts delivery.
E-Delivery starts with the so-called technical acceptance completion (TAC). It includes a ground check, an acceptance flight and minor cosmetic rework, if needed. The customer is offered to delegate these actions to Airbus or a local third party.
How can the customer be guaranteed Airbus will not just defend its interests? According to Villanove, the customer already gives the airframer the ultimate proof of trust when it accepts an Airbus-employed FAL customer manager (FCM) ratification of airworthiness. The FCM is part of the team that owns the Production Organization Approval awarded by EASA.
The FCM-conducted certification process is independent from TAC. The latter is purely commercial and does not relate to safety or liability, Villanove points out. Delegating TAC is seen as less important than relying on Airbus for airworthiness, which customers have done for a long time.
In practice, Airbus suggests the customer take 2-3 days, after landing the new aircraft at its home base, to perform more inspections and raise potential issues. If the request is “reasonable,” an issue will be corrected for free, Villanove promises. In the worst-case scenario, the customer may resort to usual contractual guarantees.
If the owner elects to entrust a third party in Toulouse or Hamburg, it may tap a person it knows already. Or the customer may choose from a list of companies Airbus can supply and which will provide a qualified person to be the eyes of the owner, says Villanove. The owner then signs a delegation letter.
After TAC, the second stage in e-Delivery is the electronic transfer of title. A new collaborative platform, “e-SalesContract,” enables negotiations to be finalized. It offers secure virtual signature and the wire payment can take place in parallel.
The final stage is the ferry flight, for which the owner can send its pilots, ask Airbus to provide some or resort to a specialist company.
Recently, Airbus pilots ferried an aircraft to the home base of an unnamed customer in Asia and they were flown back on a business jet, which they boarded immediately after having disembarked from the Airbus.
If the customer sends a crew, they can spend one night on site. Airbus has its own hotel in Toulouse and secures the pilots’ entire environment, including ground vehicles, says Villanove.
Turkey-based Pegasus sent two pilots to the Hamburg factory. An exemption was obtained and allowed them to spend three hours on German soil. They landed at Airbus’ Finkenwerder site.
Could the e-Delivery process become the norm even after the COVID-19 crisis? At least, Airbus would like to grow adoption, says an Airbus spokesperson. The current period requires extra precaution—such as duplication of Airbus’ work shifts—that slows down the e-Delivery process, the spokesperson notes.
But nominal conditions would let e-Delivery’s benefits appear clearly. For the airframer, the fewer representatives of the owner are on site, the faster the delivery. Under normal circumstances, the size of the team can vary between 1-50 customer employees, according to Villanove.
The customer can see value, too. “The members of an acceptance team play a daily role in the company—while in Toulouse or Hamburg, they are away from their office,” Villanove says. Moreover, savings from hotels and airfares can be significant.
Well before the crisis, e-Delivery was devised with streamlining in mind. Airbus’ digitalization effort inspired two members of Villanove’s team and the creation of the remote method started two years ago, he says.