Physics-Based AI Promises To Accelerate Aerospace Design Optimization
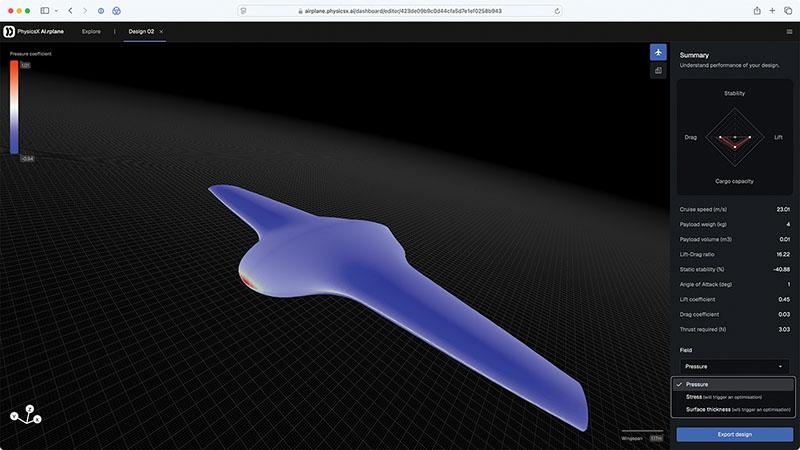
PhysicsX’s LGM-Aero AI-based analysis tool predicts performance of new shapes.
Numerical simulation has become an essential part of aircraft design, from aerodynamics and structures to aeroacoustics and thermal analysis. But the escalating use of modeling and simulation comes with a cost—the tens of millions of computational core hours required to develop an aircraft.
Automated and ultrafast numerical simulation via cloud access to thousands of general processing units instead of hundreds of on-premises central processing units is one solution. Physics-based artificial intelligence (AI) is offering another approach.
- AI model is pretrained on computational engineering data
- Users will tune model using their own simulation results
London-based startup PhysicsX has launched a large geometry model, LGM-Aero, pretrained on tens of thousands of computational fluid dynamics (CFD) and finite element analysis (FEA) simulations of generic shapes, generated using tools from Siemens Digital Industries Software.
Rather than performing calculations to solve the mathematical equations governing fluid flow or simulate how a structure will behave under loads, LGM-Aero infers the results using a machine-learning model trained on that CFD and FEA data.
“What we’re setting up to do with PhysicsX is change the way that engineering is practiced, starting with how physics simulation is carried out,” co-founder and CEO Jacomo Corbo says. “The backbone of all of engineering is assessing different designs. And that involves physics simulation of some description.
“All of that involves solving partial differential equations explicitly, at some resolution on some mesh, and a lot of engineering is bottlenecked by these physics simulations,” Corbo continues. “They’re compute-intensive, and that stands in the way of optimization and end-to-end automation.”
Numerical simulation entails the laborious process of generating a mesh of thousands or millions of simple cells that capture a complex geometry, simplify the calculations and allow computational power to be focused on high-resolution areas of interest to produce high-fidelity results.
“We’re trying to change the form factor of that compute by moving to AI models that are very fast,” Corbo says. “All the physics simulation now is a prediction step. It’s happening by inference. That means speed-ups of 104-106, so up to a million times.
“What that allows us to do, in turn, is to optimize things differently to how they’re currently done,” he adds. “So more algorithmically driven optimization, more end-to-end automation and, ultimately, greater creativity imbued in the whole engineering process.”
Work on aeroelastic applications began in 2022. “There’s no explicit calculation of the physics. They’re not about solving the equations of physics,” Corbo says. Instead, LGM-Aero infers aerodynamic performance, flight stability and structural stresses for a large class of flying shapes. It can operate as a zero-shot model, producing results out of the box without being trained on specific examples, PhysicsX says, but the model only needs tuning to capture the fine features required for a specific application like exterior aerodynamics.
The model comes pretrained, but customers can use their own data to further train it and produce a version “that’s in the loop of an optimization process,” Corbo says. “So we can search a large space much more effectively than if we have numerical simulation in the loop every step of the way.”
LGM-Aero can be used in detail design but also, because of its speed, from conceptual design to process control. “[In detail design], we can unlock a lot of value by enabling much better optimization,” he says. “We can also go upstream to concept design, where we are evaluating big architectural choices.”
Computer-aided engineering (CAE) typically is not applied to concept design because of the complexity of building meshes. “We think we can get to CAE levels of accuracy but bring it into concept engineering because we’ve divorced physics simulation from the complexities of the mesh,” Corbo notes.
“We can also go downstream of detailed design,” he adds. “CAE is just too slow at the fidelity required to be in the loop of a control process. Now we can bring it there, and one of the things we’re unlocking is an ability to bring a high-quality physics simulation to the entire product development life cycle.”
PhysicsX is working with OEMs and Tier 1s to integrate physics AI into their tool chains. “We are building a new software stack for complex engineering and manufacturing—a platform and developer tools for our customers to build workflows based on this kind of physics simulation and these kinds of AI models and do optimization they otherwise are not able to,” Corbo says.